章文飞
国家知识产权局专利局专利审查协作江苏中心,江苏苏州 215011
摘要:中空吹塑成型(Blow Molding)是一种中空成型制品的方法,是制造塑料制品最重要的成型方法之一,可以获得各种形状与大小的中空塑料制品。吹塑能较好地保证制品的外部形状和尺寸,能成型用注塑等其他方法无法成型的中空制品。吹塑成型是将处于熔融状态的塑料型坯置于模具型腔中,借助压缩空气将其吹胀,使之紧贴于型腔壁上,经冷却定型得到中空塑料制品的成型方法。吹塑成型在工业中应用十分广泛,几乎所有的热塑性塑料都可以用于吹塑成型。本文主要对中空吹塑成型吹气机构技术进行综述。
关键词:中空吹塑成型;吹气型芯;吹气针
01 吹气机构技术演进
目前,中空吹塑成型的吹气方式可分为针管吹气和型芯吹气。针管吹气是利用中空针管刺破型坯壁,压缩空气通过针管中的流道进入型坯从而吹胀型坯;而型芯吹气是型芯直接进入开口的型坯内并确定颈部内径,型芯内部设置有气体通道和出气孔,不需要刺破型坯壁。因此,根据是否需要刺破型坯壁这一特征,可以将中空吹塑成型的吹气机构分为吹气针和吹气型芯两类。
02 吹气型芯的发展史及结构技术
吹气型芯又称为吹气芯棒、吹气芯轴,还有的称之为吹气管或吹气嘴。
早期的吹塑成型技术借鉴了玻璃容器吹制工艺。玻璃容器吹制工艺主要是采用管对玻璃液进行吹制,因此,早期的吹塑成型技术的吹气机构就是简单的吹管。
吹管是一种比较原始的吹气机构,其应用十分有限,只能成型简单的吹塑成型制品。例如GB568090A、DIX-ON PLASTICS LTD和FRANCIS HAROLD TONSLEY在1941年3月17日申请的mprovements in or Relating to the Manufacture of Hollow Articles from Thermo-plastic Materi-al。该文献描述了一种吹塑成型技术,其中,吹气机构采用吹气管,吹气管和热塑性材料型坯的一端被夹持在一个塞头中,且吹气管设置在型坯的端头内,压缩气体通过吹管吹入热塑性材料型坯中,成型制品。
当吹气型芯完成对塑料型坯材料的吹塑成型后,需要将吹气型芯旋转退出。然而,由于熔融状态的塑料型坯材料温度比较高,吹气型芯在退离塑料中空容器时会出现与塑料中空容器的口部粘连的现象,影响塑料中空容器的质量。为了解决上述技术问题,美国菲利普斯石油公司(PhillipsPetroleum Company)在1971年1月4日申请的专利US3717429A公开了一种具有冷却结构的吹气型芯,吹气型芯中间具有吹气通道,两侧具有气体回收通道,由此对与模具接触部的吹气型芯周侧进行冷却,以使吹针头与塑料中空容器之间形成显著的温差,从而防止粘连现象[1]。
之后的吹气型芯,在冷却结构上大体上遵从上述设计方式,只是根据应用的不同稍有调整。例如,1973年的US3937610A、1976年的US3955908A等。吹气介质早期多采用空气,为了提高冷却效率,也可以采用冷冻的二氧化碳、氮气用于吹塑。但上述冷却结构,均是对吹气介质回收后再对吹气型芯进行冷却,但由于吹气介质对型坯吹气后温度会升高,再对升高后的温度回收用于对吹气型芯进行冷却,其冷却效果并不太理想,于是设计了一种吹气介质与型芯冷却分开的吹气型芯,如1975年的DE2519137A1公开了一种具有单独冷却通道的吹气型芯,吹气型芯具有独立的水冷却循环系统,该设计使型芯冷却很快,提高了生产效率。
除了采用单独的水冷却系统外,也有采用冷却气体代替水对吹气型芯进行冷却的,如我国于2012年申请的专利CN102848559A,型芯冷却循环系统中的冷却介质为冷却气体。
由于水冷效果比气冷效果好,采用水冷却系统对吹气型芯进行冷却是主流方式。然而,当吹气型芯从包覆的型坯中旋出时,气针主要做周向和轴向运动,这给水路的循环带来了难题。李卫民等的《大型中空吹塑设备气针的结构设计和优化》公开了一种吹气型芯,通过在吹气型芯外套的周向,上下各开8个通孔,上8孔为气针的入水口,下8孔为气针的出水口;在支座的一侧上下各有1个孔,水从支座的上孔流入,进入上环槽,通过上8孔流入气针进行冷却,冷却水通过下8孔流入下环槽,再由支座下孔排出,这样吹气型芯可以在周向运动的同时进行流水循环。同时,上下环槽用格来圈隔开,吹气型芯的轴向行程不能超过环槽的轴向尺寸,即始终保持上、下8孔分别与上、下环槽相通,这样就实现了吹气型芯在轴向运动时也可以流水循环,而且这种设计避免了传统设计的冷却水局部死循环的不足。
随着技术的发展,塑料的应用广泛,塑料原料可以制造许多产品,例如,桶、燃油箱、双壁箱、双臂座椅等,吹气型芯也根据成型产品的需要不断进行改进,吹气型芯的样式也越来越丰富。但无论吹气型芯的结构和样式如何变化,最根本的结构没有变化,吹气型芯既要有气体通道以便对型坯进行吹气,还要具有定径的作用。
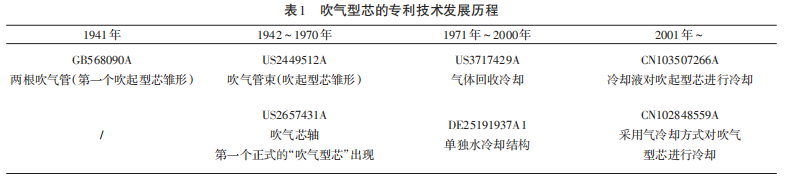
吹气型芯的专利技术发展历程如表1所示。
03 吹气针的发展史及结构技术
1942年7月15日,SUN RUBBER CO在1942年7月15日申请的Method for Producing Hollow Rubber Articles,公开号为US-2346634A,介绍了一种用于制造玩具娃娃的吹塑成型方法。该方法公开了一种具有锥形尖头的吹气针,锥形尖头上有气孔。锥形尖头刺破型坯壁后,气体从针体内的通道吹出进入型坯,使型坯膨胀成型。采用该方法制造的产品外观美观,后期处理少。
早期的吹气针结构均是针头呈锥形,吹气通道从针尾延伸至锥形针尖,或者是在锥形针尖的圆周面设置出气孔,譬如,1949年10月3日申请的US2515093A、1950年9月1日申请的ES194433A1、1965年10月25日申请的US3492106A、1963年3月27日申请的BE -630207A等,压缩空气均是从锥形针尖处流出。
吹气通道从针尾延伸至锥形针尖的方式和在锥形针尖的圆周面设置出气孔的方式一直被沿用至今。前者用于对产品质量要求不高的制品;而后者的出气孔设计得更巧妙,可以避免堵塞针尖顶气孔,因而广受欢迎,在更多吹气针上被采用。
无论是吹气通道从针尾延伸至锥形针尖,还是在锥形针尖的圆周面设置出气孔,上述设计结构都存在一个缺点,即当吹气针刺破比较厚的型坯壁时,刺破时会产生碎屑,碎屑难免会进入出气孔,从而对出气口造成堵塞,影响出气质量。而且,刺破时会有型坯壁的碎屑掉落在型坯内部,对型坯质量造成影响。
为了避免型坯碎屑堵塞出气口,保证制品质量,1991年4月30日,FORD MOTOR CO在美国申请了一项专利, 即US5078948A。该项专利记载了一种具有切割刀片的吹气针头,其在锥形的针尖部分设置多个刀片,而出气孔设置的位置与针尖有一段距离。通过这样的设置,吹气针工作时,切割掉的坯料碎屑既不会堵塞出气孔,也不会掉入型坯内[2]。
该项专利在锥形针头上设置了多个刀片,利用刀片对型坯壁进行切割,避免了刺破时产生碎屑,而出气孔设置在距锥形头有一段距离的针杆体上,而不是设置在锥形针尖的圆周面上,即使产生碎屑,碎屑也不会进入出气孔,避免了堵塞。
后期很多专利中的吹气针都采用了这样的设置,该设计方式对之后吹气针结构影响深远。例如,1995年12月28日 (KYKO) KYORAKU CO LTD在日本申请的JPH09183150A就采用了这种出气口在针杆侧面的设计, 而2008年09月29日申请的US2010078842A1采用锥形针头上设置多个刀片、出气口在针杆侧面的设计。
人们对吹气针只能实现吹气并不满足,开始对吹气针的结构和功能进行改进,希望赋予吹气针更多的作用和功能。
现在,人们在制造中空塑料制品时经常采用的是吹气型芯,吹气针已经逐渐出了人类的视线,但吹气针在塑料吹塑历史上起到过很重要的作用,而且在制作精细的吹塑制品时,仍会采用吹气针。吹气针的专利技术发展历程如表2所示。
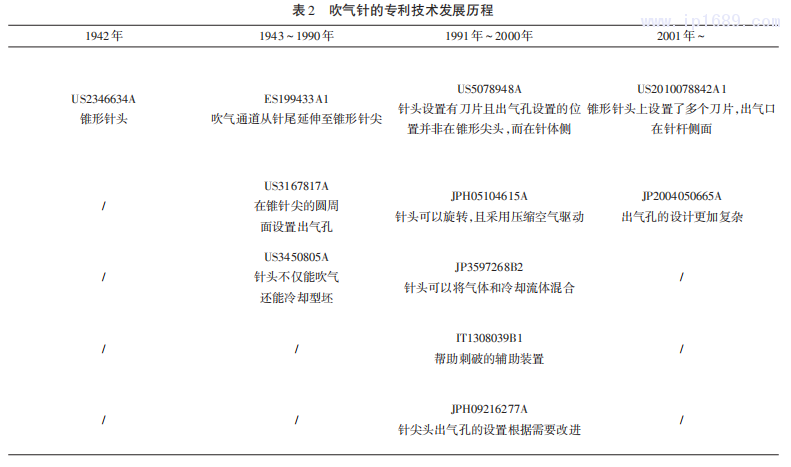
4 结语
中空吹塑成型吹气机构在国外已相当成熟并实现了大规模的工业化应用。目前,日本在吹气机构上的专利是最多的,而我国吹气机构的专利近十年来才开始起步,自有技术不多。但随着吹塑技术的发展和进一步完善、提高,吹气机构又是吹塑成型必不可少的部件,我国吹气机构技术会得到进一步发展。目前,三维吹塑成型工艺已经兴起,相信吹气机构随着吹塑技术的推广和应用,其结构改造也会越来越好,希望我国技术人员能发挥创造性,对吹气机构进行更加优化和完善的改进,从而对促进模具工业本身的改革和发展产生积极作用。
和进一步完善、提高,吹气机构又是吹塑成型必不可少的部件,我国吹气机构技术会得到进一步发展。目前,三维吹塑成型工艺已经兴起,相信吹气机构随着吹塑技术的推广和应用,其结构改造也会越来越好,希望我国技术人员能发挥创造性,对吹气机构进行更加优化和完善的改进,从而对促进模具工业本身的改革和发展产生积极作用。
参考文献:
[1]魏刚,彭必友,廖永衡.塑料成型理论与技术基础[M]. 成都:西南交通大学出版社,2013.
[2]李卫民,李铭.大型中空吹塑设备气针的结构设计和优化[J].机械设计与制造,2013(8):233-236.