褚建忠 台州科技职业学院,浙江 台州 318020
摘要:根据目前汽车密封件在结构和装配方面的要求,介绍了PP+TPE一体大型旋转注塑模具的设计难点,详细分析了模具在运动定位、顶出平衡、复位平衡等方面存在的问题,对重复定位系统、双浇注系统、顶出与复位自动调整机构分别进行了创新设计。该项技术不但实现了PP+TPE一体产品自动生产,而且提升了产品的质量稳定性。该项技术也可推广到其他双料一体的注塑模具的开发上。
关键词: 重复定位系统; 双浇注系统; 顶出与复位自动调整机构
01 国内外研究情况
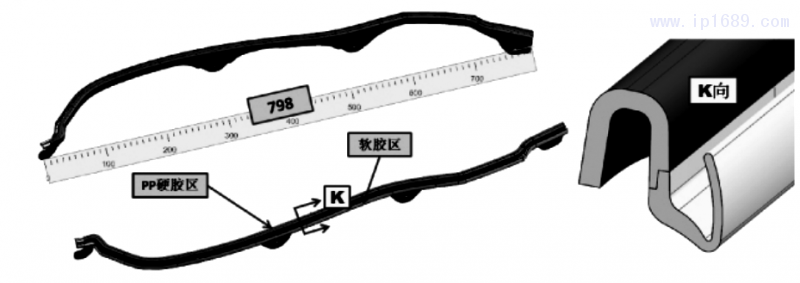
由于汽车外饰件通常需要与内部的各种加强骨架或钣金件配合,经常需要兼顾安装强度与密封的功能,如车前后门密封条、天窗骨架等。要实现这些应用功能,传统的做法是先将硬质塑件安装后再装软质塑件,或者是将独立的硬质塑件与软质塑件装配好后再一起装配到汽车上,但无论哪一种都存在较大的装配误差,达不到与日俱进的应用需求,影响汽车的整体质量[1-3]。
相比之下,PP(聚丙烯)+TPE(热塑性弹性体)双料一体产品既具有硬胶的装配刚性,又具有软胶的密封性能,能满足实际应用的各种需求,但需对产品模塑化的设计方案与工艺进行改造。根据产品结构的特点,要求硬胶在不脱离模腔的情况下实现二次注塑,这就需要模具采用旋转式二次合模的成型方案,也就要求模具具有高精度的二次合模定位精度、低压力注塑软胶的工艺保障以及多型腔单侧顶出平衡的有效控制等。目前 PP+TPE一体产品所用的大型旋转高精密双料一体密封件注塑模具方面,由于其技术含量比较高,到目前为止中国市场上凡高端车型的双料一体模具均从国外进口,赶超国外仍是国内模具行业相当长时期内的主要目标[4-6]。
02 PP+PTE双料一体大型旋转高精密封件注塑模具开发
经过本项目的开发后,该大型旋转高精密双料一体密封件注塑模具在模具寿命、产品精度等方面接近或部分达到国外同类产品先进水平,主要指标及成本比较如表1所示:
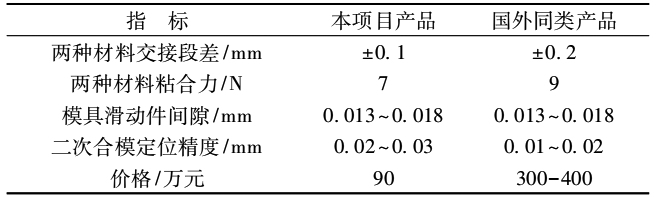
主要技术指标体现在以下六点:
( 1) 型腔表面粗糙度Ra达到0. 8μm标准要求,两种材料交接处段差不超过0. 1mm,黏合力不低于7N。
( 2) 产品无飞边、毛刺,浇注熔接痕控制在非可视区内,表面光感均匀。
( 3) 产品安装孔位尺寸误差不超过0.1mm,成品装车的密封性满足国家的相关法律法规的要求。
( 4) 模具滑块的滑配间隙保持在0.013~0.018mm,二次合模的定位精度达到0.02~0.03mm。
( 5) 模具主材料硬度保持在HRC28~32。
( 6) 模具各处冷却温差在10℃范围内。
为了实现以上技术指标,本项目开发从三个方面进行创新设计,分别是精密导向与定位系统、独立的双浇注系统可控注塑、顶出与复位平衡自动调整的新方法。
2. 1层级式精密导向与定位系统
大型高精密旋转双料一体注塑模具最大的技术难点之一就是模具的重复定位技术。
大型旋转模具在工作过程中,需要考虑的负面影响的主要因素有:开模过程中,定模侧的抽芯滑块与开模过程同步误差过大; 大而重的模具在旋转过程所产生的离心力会可能导致模具中心的偏移; 导向系统的加工误差影响产品的二次定位,导致硬胶产品在二次合模过程中拉伤。
根据对以上负面因素的分析,所采用解决方案及相关模具开发目标如下:
(1)开模过程中,定模侧的抽芯滑块与开模过程同步误差过大
要保证定模侧的滑块抽芯与开模同步,必须使滑块有良好的导向系统、稳定的动力系统、运动过程中的摩擦损耗保护等。一块大型滑块长度约940mm,质量约300kg,通过对滑块运动平衡与机床加工精度保障的分析,对每一块大型滑块均设计了独立的导向,其配合面均设计了高耐磨的配件予以保护; 滑块工作时,在动模侧设计了启动拉钩,保证了开模的一 瞬间注塑设备的开模力直接作用于滑块,而不会因为摩擦力而滞后,同时在滑块的底部设计了氮气弹簧,保证了滑块在运动方向上持续平衡受力,顺利滑动。如下图2所示。
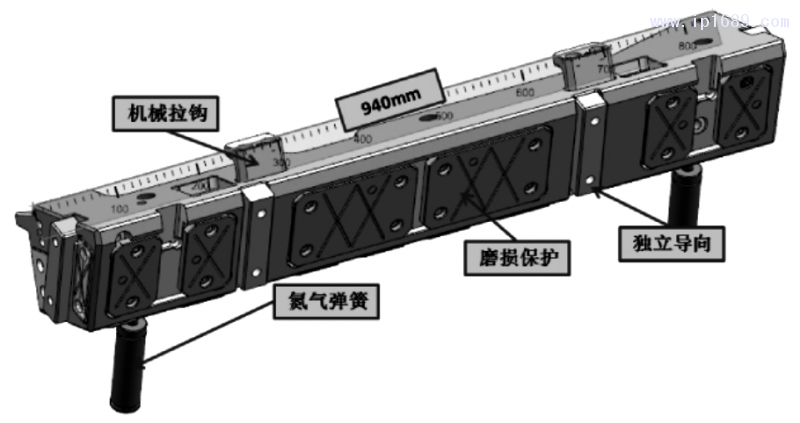
(2)大而重的模具在旋转过程所产生的离心力会可能导致模具中心的偏移在进行模具设计开发时,所有易产生偏移、松动的活动件以及相对质量较大的零部件(如方导柱、热流道系统)等均保留在定模侧,有效降低了动模部分的质量,大大降低了动模侧在旋转的过程中所产生的离心力与惯性,保证了动模侧在旋转时的位置误差不超过0.05mm,满足了双色设备二次合模时所需的误差要求 (如图3所示) 。
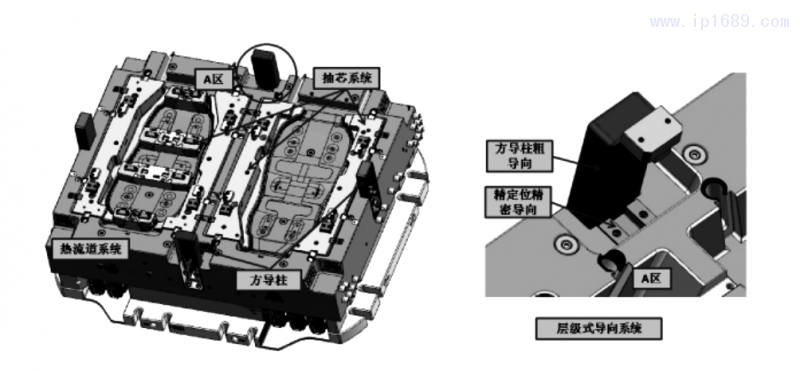
(3)导向系统的加工误差影响产品的二次定位,导致硬胶产品在二次合模过程中拉伤大型模具在制造加工、研配、使用过程中均存在误差,特别是在实际量产过程中,由于模具处于高频工作状态,细小的误差都会逐渐加重零部件的磨损,最终导致失效。因此在模具设计开发过程中,结合了方导柱与精定位的导向特点,在导向系统上双重应用,使模具在合模的过程中导向先粗后精,具有自动调节的功能,有效保护了合模的同向性精度要求,开模则与这个过程相反。通过层级式的精密导向与定位系统,有效保证了模具工作的持续稳定性与生产精度,提高了产品的生产质量(如图3所示)。
2. 2 设计了独立式双浇注系统
由于所注塑的两种材料特性不同,如: 收缩率差异、注塑温度悬殊、注塑压力需求、分子结构、黏度等,因此要求通过流变分析和工艺流程的数值的模拟来解决这些差异对产品精度的影响以及两种材料结合处强度的需求,即在PP完成浇注后,橡胶浇注能适时与其粘接,达到所需的黏度; 同时橡胶浇注的时间损耗不影响PP的成型收缩效果,保证产品的尺寸精度。除此之外,两种材料注塑时对模具排气的需求也因其流动性不同而需采用不同的设计方案。为解决这些关键技术问题,保证产品质量和提高生产效率,这就要求浇注系统能完全按照CAE的分析方案实施,各冷却回路需经过分析确认各部位的温度在标准要求的范围内才能应用,同时要求在浇注的末端按CAE分析的结果设计排气,以辅助浇注系统顺利完成浇注。其具体控制方案如下:
模具在注塑机上工作时,其一个循环周期内按如下步骤进行: 模具处于合模状态,启动GA系统浇注硬胶,在注塑设备的控制下,使各浇口同时开启浇注,并直至硬胶浇注完成,如图4所示。
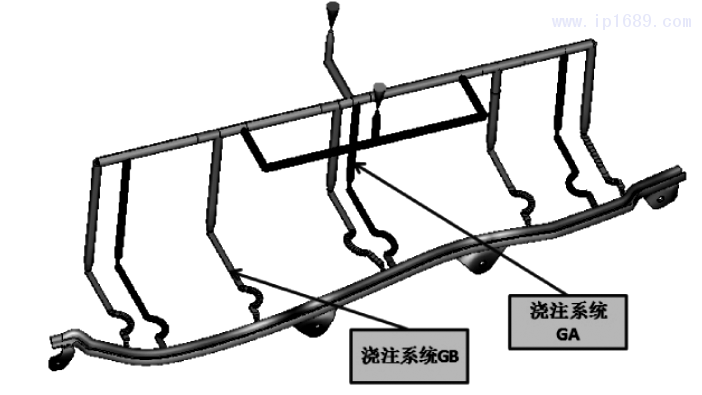
硬胶浇注完成后,关闭硬胶注塑系统GA,开模,启动注塑设备旋转动模侧部分180°,随即完成二次合模;合模完成后启动GB系统浇注软胶,使G1~G5同时开启浇注,直至硬胶浇注完成,如图5所示。
结束浇注后,对模具进行通水冷却,启动开模程序,打开动定模至需求位置,使产品处于能自由顶出的状态; 启动顶出系统,在直顶块、斜顶块等顶出功能件的作用下将产品顶出,最后取件,完成后进入下一个工作循环。
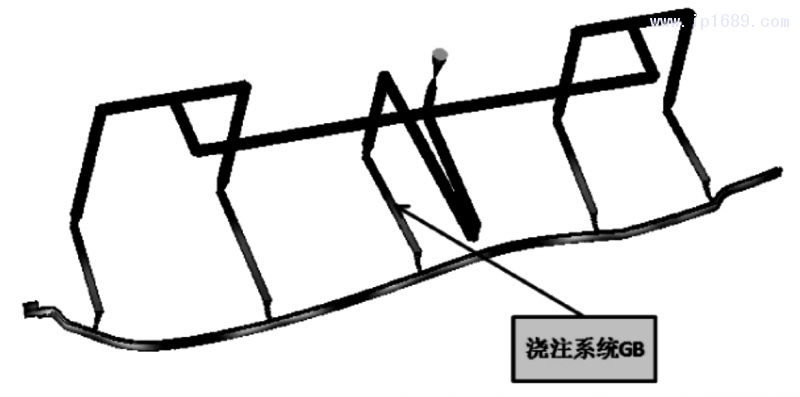
2. 3顶出与复位平衡自动调整设计
狭长型产品的平衡顶出是要求顶出系统顶出产品时,产品能按设计的要求,同步脱离型芯,各顶出单元的同步误差不超过±0.03 mm。
在此技术要求下,首先通过对大型不同牌号的钢材性能研究的基础上,通过有限元分析和工艺过程的优化,保证了顶针板、复板以及动模板的变形误差在可控范围内; 其次,鉴于狭长型产品的顶出受力点是依据产品特征来分布的,而型芯的工作温度高于顶针板的工作温度,因此顶块在型芯上的轴心位置与顶针板的轴心位置受热膨胀的影响会发生偏移,于是在顶块结构的设计上采用浮动式结构,使顶块在工作时能随温度的变化作随机调整,同时设计了直顶块定位产品,解决了产品在顶出时所产生的不定向位移的问题; 第三,模具顶出系统的动力方面,由于模具有多达40余件的顶块,受热膨胀的影响各异,并且旋转型双料一体模具是单侧顶出,因此根据液压系统具有可自动调节平衡的特点为,设计以液压动力源代替了机械顶动力源,并辅以油路分配器,保证了顶出误差在±0.03mm,如图6所示。顶出系统运动平衡稳定,产品在此机构的作用下安全脱出动模,达到预期的设计效果。
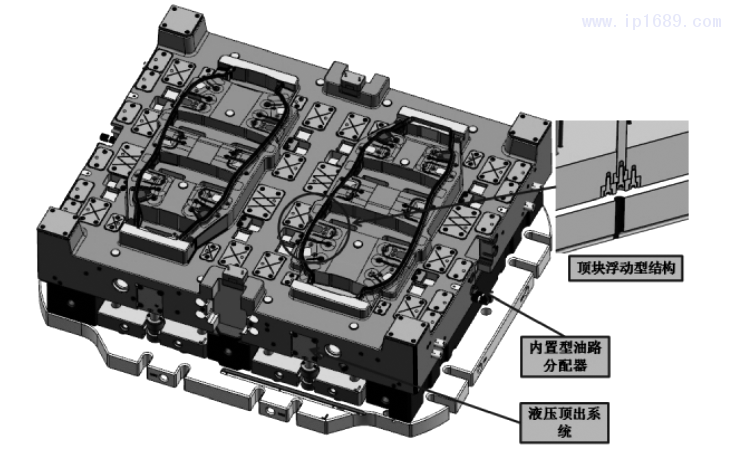
03 结论
综上所述,本项目主要创新点为:
采用层级的精密导向与定位系统,辅以机械拉钩与氮气弹簧,使首次注塑后定模侧大型抽芯块与开模同步的误差保持在±0.05mm,动定模的二次合模误差控制在±0.03mm,有效达到了利用大型旋转双料一体注塑模具所生产的产品其两种材料的黏合处段差不超过0.1mm的应用要求。
在对PP/TPE材料相关工艺参数研究基础上,通过流变分析和工艺过程的数值模拟,采用独立的双浇注系统分别对硬软胶部分进行可控浇注,既解决了两种不同收缩率材料注塑对产品精度的影响,达到了两种材料结合处强度的需求,又在大型旋转双料一体模具内完成PP/TPE材料塑化成型工艺过程的新工艺。
在对大型不同牌号的钢材性能研究的基础上,通过有限元分析和工艺过程的优化,液压顶出与复位系统上辅以油路分配器,使作用于狭长产品的各顶块均具备自动调整顶出与复位平衡的功能,同步顶出误差在±0.03mm,实现了狭长型产品在弹性型变的的情况下能定向顶出,且不降低产品的质量。
参考文献
[1]曾文瑜.汽车保险杠冷流道结合注塑成型工艺CAE优化分析[J].塑料工业,2016,44 (3) : 83-88.
[2]洪建明.汽车格栅双色注射模具热流道系统的CAE分析与优化[J].塑料,2016,45 ( 2) : 117-120.
[3]吴松琪,刘斌,朱训民,等. 汽车前保险杠注塑模具热流道热平衡分析及其优化设计[J].塑料工业,2015,43 (12) : 54-59.
[4]苏金林,黄飞,于正云,等. 汽车主动进气格栅叶片安装支架双料注射模设计[J].模具制造,2019 (4) : 39-44.
[5]刘鑫,郭恒亚,黄明.汽车挡风玻璃装饰条对射式双色注塑模具设计[J].中国塑料,2019,33 (10) : 100-104.
[6]徐超辉,王涛. 汽车阀体零件热流道双色注塑模具设计[J],中国塑料,2019,33 (3) : 93-96.