李建军,唐伟,李东
金发科技股份有限公司,广东广州 510663
摘要:对集中吸料系统原有的固定分组控制进行节能分析,通过对固定分组控制建立数学模型,确定了影响系统能耗的关键要点。在固定分组控制算法基础上,提出了一种基于机台联网的动态分组与匹配优化的智能方法,介绍了其优点和关键技术,建立数学模型,实现智能控制的主要算法,分析结果表明该方法可稳定的完成智能控制功能,降低了系统能耗。
关键词:塑料数字化工厂;集中吸料;智能算法;动态分组;匹配优化
集中吸料系统的工作原理是通过集中真空系统的罗茨风机进行恒压控制[1],并通过管道连接到生产机台,实现成品的吸料控制,如图1所示。在改性塑料行业,生产车间内有多条生产线,要求集中真空系统恒压PH(单位MPa)能满足总的运行机台的负压要求。集中真空系统的PH通过罗茨风机进行恒压控制产生,生产机台所需负压与产量,产品特性等有关,为了减少设备投资及系统运行能耗,在设计时,集中真空系统的最小恒压值满足大多数机台同时运行所需负压即可。在生产运行时,在集中真空系统中,根据生产需求设定合适的恒压值PH,在传统设计中,采用固定分组法进行吸料,实现生产车间机台成品吸料控制。
固定分组法通过对机台进行分组控制,集中真空系统的负压值只需要满足分组内的机台吸料需求,减少了系统设计冗余量。但是在实际应用中,存在以下问题:
1)分组提前设定,生产机台的运行/停机状况变化,很难进行分组变化。
2)生产线的设置参数不合理,机台信息缺少与集中吸料系统的交互,导致吸料参数设置不合理。
3)系统能耗较大,主要在于负压空损耗[2]导致的能耗浪费。
本文提出了新的智能算法,包括动态分组 [3-4],机台联网及机台匹配优化三个部分内容,可降低集中吸料系统能耗,实现以下控制目标:
1)进行动态分组之后,负压控制能满足生产机台运行/停机的变化。
2)通过生产机台的联网,自动优化相关设置参数,实现智能降低能耗。
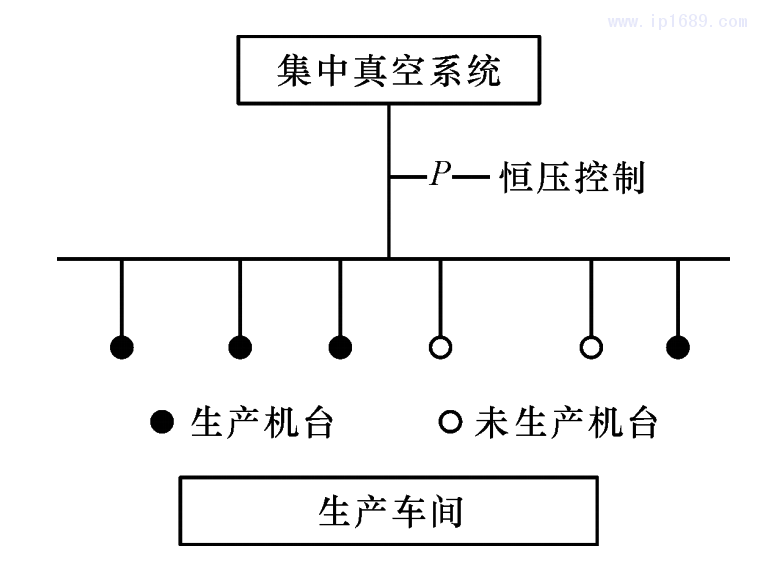
01 集中吸料系统原理与节能分析
1.1集中吸料系统结构及负压需求
集中吸料系统使用固定分组法进行成品吸料控制,存在能耗浪费问题,本文对吸料系统原理及实际的负压需求进行分析,确定节能要点。集中吸料系统的单个机台成品吸料系统如图2所示,成品斗内物料通过负压吸料到缓存罐,然后放至在线混色罐,成品吸料速度与负压值成负相关。机台所需负压Pi与实际产量为负相关,当产量较大时,负压Pi值更小,才能保证生产成品及时送至在线混色罐中。
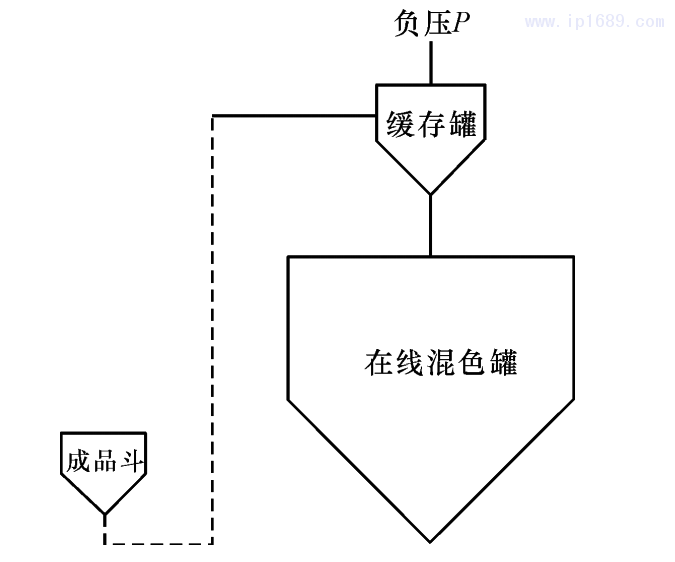
在机台成品吸料系统中,负压值Pi应该与产量相匹配,成品斗内物料堆积到一定的料位,通过负压吸料至缓存罐,等待料位堆积一定料位时再次吸料,等待过程中机台对负压值大小无要求。如图3,机台负压需求曲线描述了与产量相匹配的负压值的变化情况,P1为产量较大时的需求负压,P0为较小产量时的需求负压,曲线P为与成品斗料位相关的负压需求。
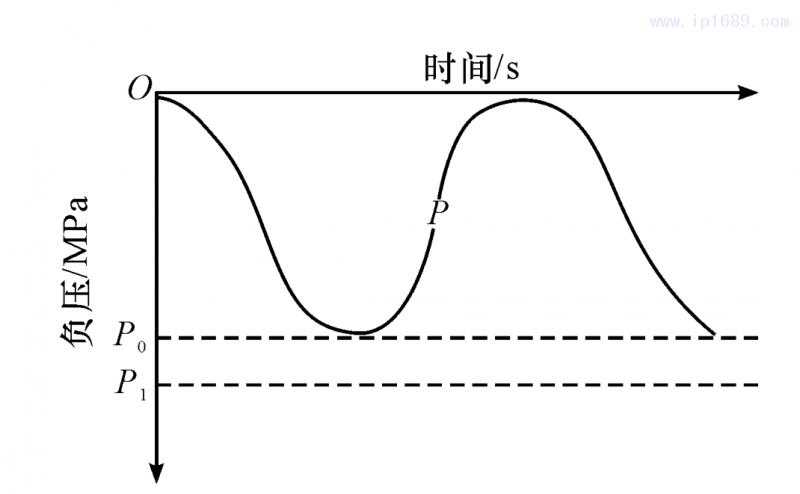
1. 2 固定分组法的节能分析
上文分析了单个机台的实际负压需求,集中吸料系统使用固定分组法对生产车间机台进行分组时,组内机台总的负压需求仅进行了简单计算,如式 (1) 。其中N为组内的机台数量,机台所需最小负压值为Pi,保证了组内所有机台同时运行时仍能够实现成品吸料功能。

在实际控制系统中,组内机台是否运行是由生产订单确定的,分组内的机台不运行时,负压需求为零,运行机台的负压需求曲线Pi与图3相似,则分组内的机台实际负压总需求PZ计算,如式(2) ,其中n为运行机台数量,Pi为机台i的实际负压需求。

生产线的进行固定式分组时,通过对式(1)、(2)进行细化分析,将分组内的实际负压总需求与恒定负压值进行比较,其关系如图4所示。从图中可以看出PZ是根据机台运行情况变化的曲线,而PH为集中真空系统设定的恒压控制值,当出现机台开机数量较小或成品吸料完成后的等待过程时,两者之间存在明显的差值(图4中的阴影部分) ,维持此部分负压所需要的能耗(图4中阴影部分面积并不表示具体能耗数值) ,即为负压损耗值。
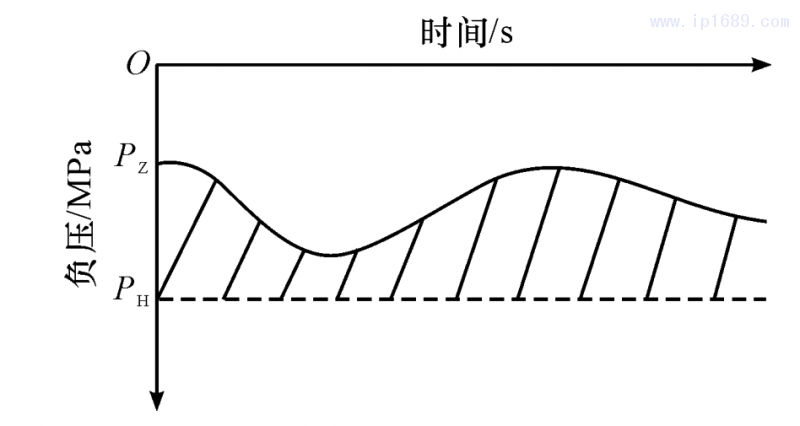
如何降低集中吸料系统的负压损耗值,如图4所示,可以从PH和PZ两个方面来进行梳理:
1) PH由集中真空系统进行恒压控制,与分组内的运行机台数量n有关,调整频次较低,调整PH可以明显降低系统能耗,但PH与n的关系还要进一步研究确定。
2) 负压总需求PZ实质上是运行机台的负压需求值Pi进行综合计算后的曲线,前文可知,负压需求值Pi与生产过程相关,其变化较快,通过固定式分组法很难调整PZ曲线,需要使用更加智能的算法来对PZ进行调整,降低系统能耗。
02 集中吸料系统节能数学模型
2. 1 节能组合模型
对于集中吸料系统来说,降低系统能耗的重点在于降低系统负压损耗值,从前文可知,集中真空系统和集中吸料系统的控制均可以降低系统能耗,但本文主要把集中系统吸料作为控制目标。图4中,对于分组内的N条生产线,T为PH调度周期[5](假定为分组内的运行机台数量n变化为一个调度周期) ,由于系统负压损耗S与负压总需求PZ和恒压值PH的偏差有关,系统负压损耗S最小的目标函数数学模型为:

式中,假定调度时间T内PH值不变; kn-系统恒压值PH的损耗计算系数; kn-运行机台数n有关。
本文中集中真空系统进行变频恒压控制,两者关系如图5所示: 1) kn为损耗负压计算系数,吸料使用负压设为1,kn值大于1; 2)当机台运行数较少时,系统负压损耗较高; 3)当运行机台数量增加时,集中真空系统负压损耗系数降低。4)在机台数量不变化时,负压损耗系数基本不变化,为方便进行节能分析,假定调度周期T内,kn值为恒值。
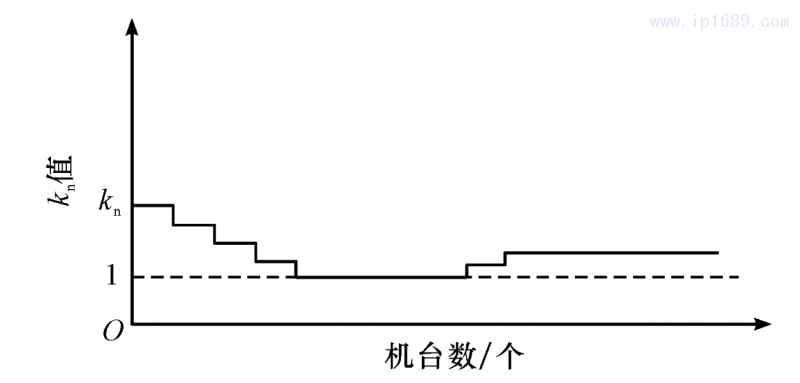
由式(2)中,对PZ进行替换,可得出新的数学模型,见式(4),前式(3)中,运行机台数量必属于分组内的机台,使用μi作为机台运行状态,见式(5)

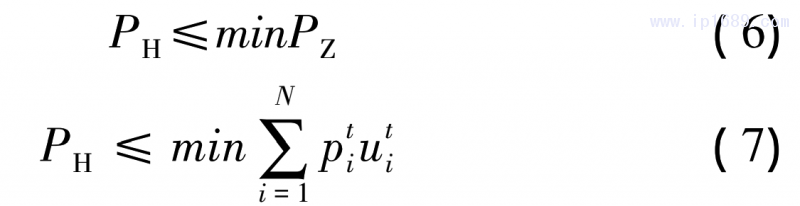
前文已经叙述了降低系统能耗的两个方面,除了降低系统负压损耗S外,若能够降低系统恒压值PH,从图4可知,PH需要满足运行机台的吸料负压需求,联合式(2) ,建立数学模型,见式(6)、(7) 。
2. 2 节能模型智能算法
集中分料系统控制车间所有机台的成品吸料,假设车间机台总数量为M,分组内的机台数量为N,一般情况下,分为2组进行成品吸料控制,图6为车间机台进行固定分组时的负压需求图,未运行机台负压需求为零。本节详细介绍智能算法的实际运用。
2. 2. 1 动态分组算法
图6中,分组1和分组2中各有3个机台,其中P6机台未运行,其负压需求值为0。依据式(4)的数学模型,分组2中负压损耗值更大,若PH未进行调试,则依据式(7) ,系统能耗也更高。本文提出了通过动态分组算法,对分组进行调整,确保组内的机台全部为运行机台,建立如下数学模型:
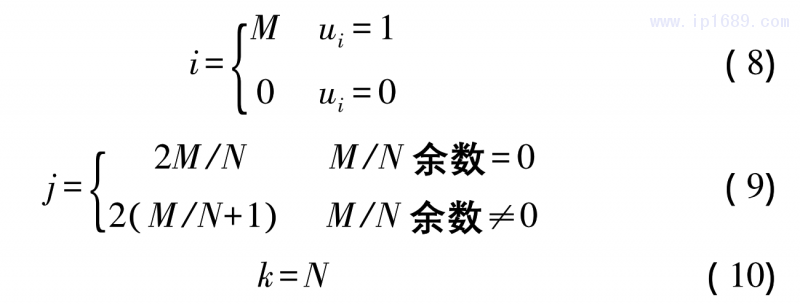
式中,i-运行机台编号; j-分组编号; k-组内编号; M-机台总数量; N-分组内机台数量。
2. 2. 2 机台联网
从上文可以看出,动态分组算法主要是对分组内的机台进行调整,从图6中可以看出,机台的负压需求曲线均不相同,负压需求主要与产品产量,物料特性等有关,使用kpi表示机台i的负压吸料系数,当产量较高时,kpi值也更高。
在式(11)中,kmin为最小产量机台系数(通常默认为1) ,ki为机台i与最小产量机台产量比值 (≥1) 。
2. 2. 3 机台匹配优化
通过对图6的机台负压需求曲线进行简化计算,当吸料时负压值Pi为恒值,当等待吸料时,负压值Pi为0,当负压满足吸料要求后,可根据负压吸料系数Kpi对机台吸料时间与等待时间进行匹配优化[3],可以降低系统恒压值PH。
03 智能算法求解与分析
智能算法求解过程如下:
1) 根据机台总数量M,分组内的机台数量为N,根据式8,计算分组数量j。
2) 通过系统联网,确定运行机台数量n,并按照式8,式9,进行动态分组编号。
3) 通过各机台产量信息,确定机台的吸料负压系数kpi,对机台的吸料与等待时间进行优化。
04 结论
本文通过对集中吸料系统进行分析,提出了新的智能算法,降低集中吸料系统的能耗,需要从PZ和PH两个方面进行处理,解决了固定分组法存在的能耗损失问题。本文提出的智能算法通过对机台实际负压需求曲线进行分析,使用动态分组方法确保分组内的机台数量为最大允许值,可以减少系统的负压损耗值,在通过机台联网的情况下,根据机台实际产能情况,合理的匹配分组内不同机台的吸料时间和等待时间,降低系统的恒压值,减少了系统的能耗。
通过本文介绍的控制算法,只需要设置根据机台运行情况,机台产量信息,实现智能的集中吸料系统控制,是一种比传统的固定分组法控制更行之有效的节能方法,应用范围更加广阔,符合数字化工厂的建设需求。
参考文献
[1]罗秋芳.PLC在负压恒压自动控制系统中的应用[J].中
国科技信息,2006 ( 3) : 42.
[2]马玉秋,张业辉,耿久红.降低变压器空载损耗的新方法[J]
.变压器,2007,44 ( 5) : 30-33.
[3]李会,张天丽,陶佰睿,等.动态分组方案的自适应人工鱼算法[J]
.计算机工程与应用,2013,49 ( 8) :58-62.
[4]李树山,李刚,程春田.动态机组组合与等微增率法相结合的
火电机组节能负荷分配方法[J].中国电机工程学报,2011,31 (7) ,41-47.
[5]尚金成.基于时间尺度的节能发电优化调度协调模型及算法[J]
.电网技术,2008,32 (15) : 55-61.