董嫔1,董瑞佳2,张晓妍1
(1.河南工业职业技术学院机械工程学院,河南 南阳473000;
2.唐山工业职业技术学院自动化工程系,河北 唐山063299)
摘要:汽车大型塑件生产中,塑件的脱模设计是模具设计成败的关键因素,浇口的自动切除是影响塑件生产效率的另一关键因素。在分析成型对象塑件结构形状及成型方案的基础上,提出了一种斜导柱增强复合斜顶机构及浇口模内自动热切除机构设计。所设计的模具为一模两腔两板式家族模具结构,模具采用2个斜导柱增强复合斜顶机构、2个斜导柱滑块机构、14个滑动座圆杆斜顶机构、36根顶针和4个推管实施脱模;采用2个模内热切机构来对冷浇口进行模内自动热切除。生产实践证明,该模具设计巧妙,结构新颖,成型的塑件获得了良好的注塑效果,大幅提升了模具生产效率,极具设计参考价值。
关键词:内饰板;斜顶机构;浇口热切机构;模具设计;热流道
汽车门板上的支撑性内饰件一般为大型塑件,且都是左右成组设计,即外形尺寸和形状基本相同,但局部区域的结构设计特征不相同,因为左右门的功能安装件要求不一样。该类塑件的注塑成型模具生产一般采用家族模布局方式进行模具设计与制造,当流道较长的时候,一般采用单点或者多点热流道嘴对注塑机的喷嘴进行延伸后,再通过冷流道及冷浇口进行浇注,以保证熔融料流在模腔内的充填流动充足性。冷浇口的切除一般采用人工剪除的方式,这是一个严重降低生产效率和增加制造成本的技术缺陷。本文拟针对某内饰板的注塑生产提供一种热流道两板式家族模模具结构设计案例,该模具内设置有一种特殊的斜顶机构及模内冷浇口自动热切除机构,生产效率高,具有极大的设计实践参考价值。
1左、右内饰板塑件结构
图1a为某新款汽车左、右前门上的开门拉钩的支撑内饰板的形状图。塑件材料采用PP(宁波大川DCPM1017),该塑料添加20%的玻璃纤维。塑件分为左、右两件,在车门内壁上安装,分别用于左右车门开门拉钩座的安装支撑。两塑件的正面形状基本相似,但内表面上分布特征稍有不同。左、右塑件内表面上所分布的脱模困难特征如图1b所示。在左饰板内壁上,分布有H1~H8共8个倒扣特征,且倒扣的形式不尽相同,外壁上,前端位置有1个圆柱型侧孔H0特征,H0特征向内壁延伸后,形成倒扣特征H1;Z1、Z2为内壁上的两个螺丝柱。同样,右饰板的内壁上分布有K1~K8共8个倒扣特征,其外壁的前端有一个K0孔,该孔向内延伸后形成倒扣特征K1。Z3、Z4为内壁上的两个螺丝柱。左右两塑件的浇注分别在G1、G2两个位置开设扇形侧浇口进行浇注。
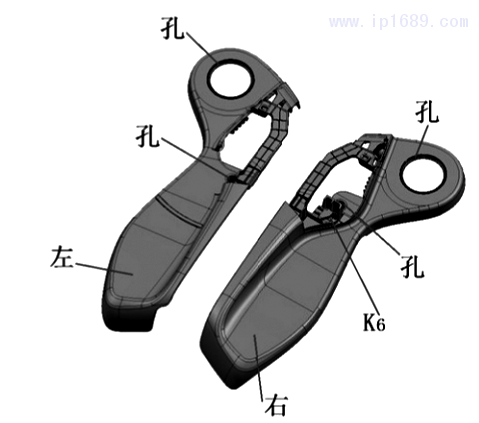
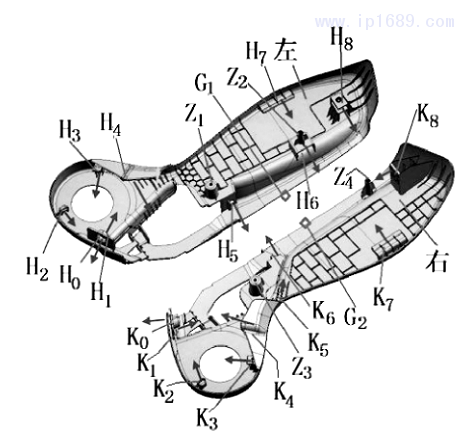
2脱模结构设计
2.1机构布置
左、右内饰板在模具中的布局如图2所示,针对塑件内、外壁难脱模的结构特征分别设置脱模机构实施脱模。针对左饰板塑件,其外壁的侧孔H0特征采用斜导柱滑块侧抽芯机构M1实施侧抽芯脱模,H1~H8特征采用X1~X8共8个斜顶机构进行顶出式侧抽芯脱模。针对右饰板,K0孔特征采用滑块侧抽芯机构M2实施侧抽芯脱模,K1~K8特征采用Y1~Y8共8个斜顶机构来实施顶出式侧抽芯脱模。两个塑件的斜顶机构中,斜顶X4、斜顶Y4机构的结构相似,其结构设计如图2b所示,采用一种斜导柱增强复合斜顶机构;斜顶X1~X3、斜顶X5~X8、斜顶Y1~Y3、斜顶Y5~Y8机构相似,都采用动座圆杆斜顶机构,只是斜顶杆的顶出方向不同。
2.2斜导柱增强复合斜顶机构
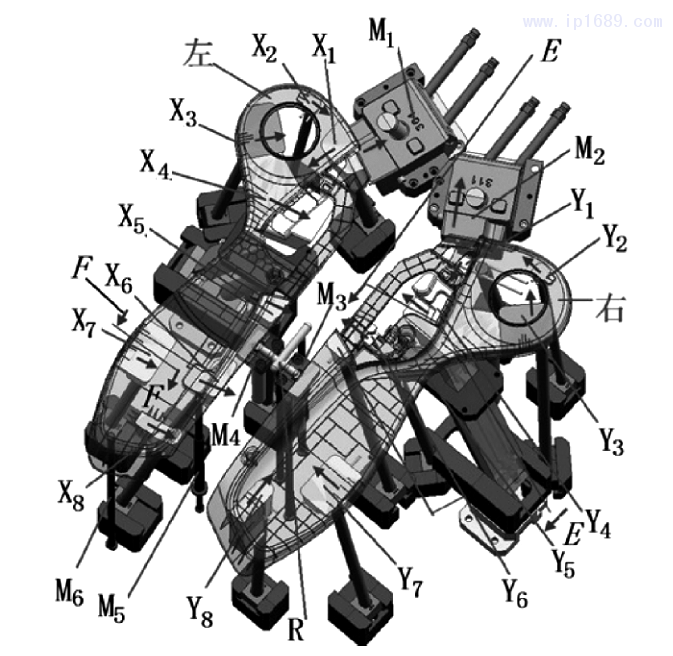
斜导柱增强复合斜顶机构X4、Y4的作用是针对塑件内壁倒扣需要大角度、长距离侧抽芯时设计的,如图3所示,机构斜顶杆6的底端安装于支撑块11上,支撑块11两侧通过转动销14安装有两个导向块12、13,导向块12、13可在斜顶座10所开设的滑动槽内沿Kh向滑动,同时,斜顶杆6和支撑块11组合在一起后可绕转动销14按T1方向转动。支撑块11内开设有一个斜向导柱孔,该斜向导柱孔与斜导向柱8滑动配合。斜导向柱8上端通过导向耐磨板7固定在模具的动模板下端面上,下端通过固定座16和压板17用4个无头螺丝紧固固定在模具底板上。机构的工作原理为:当注塑机按Km反向打开时,注塑机顶出板推动斜顶座10按Km方向顶出,支撑块11在斜导向柱8的驱动下,沿着Kh方向在斜顶座10的槽内滑动,导向块12、13与支撑块11之间可以相互转动(T1方向),斜顶杆6被支撑块11推动按S向顶出,从而实现其水平分向S1向的侧抽芯脱模。
2.3滑动座圆杆斜顶机构
滑动座圆杆斜顶机构的结构如图4所示。机构的底座安装于模具顶出板上,其上通过23、24、25、22、21安装第二斜顶杆20,左活动滑块24、右活动块25在斜顶座26的滑动槽为斜向槽,用于增大斜顶杆20的斜向顶出角度,同样,第二斜顶杆20和导滑块22通过螺钉21锁紧组合在一起后,与滑块23、24之间可以绕转动销23的中心做T2向的旋转转动。两个斜顶机构中,斜顶头1、斜顶头18采用独立滑块头形式,便于加工和安装。
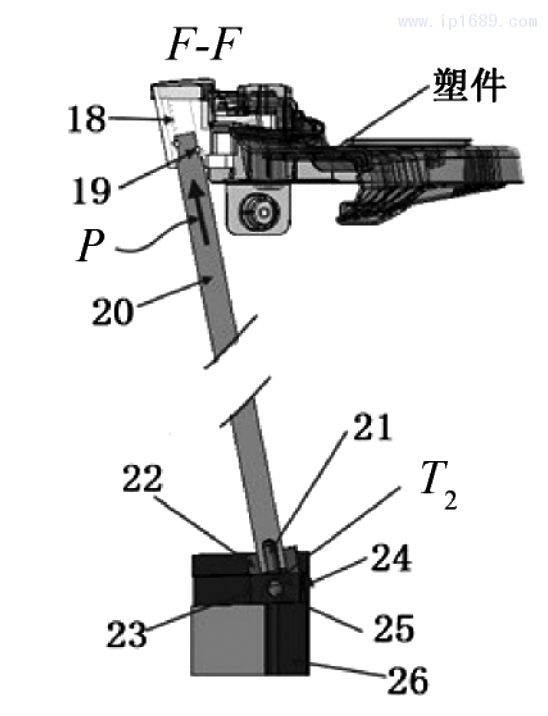
2.4斜导柱滑块机构
滑块机构M1、M2的结构及安装形式相同,M1的结构组成如图5所示,机构斜导柱27驱动滑块体32按S4方向抽芯抽出,实现侧孔型芯34与塑件的分离。
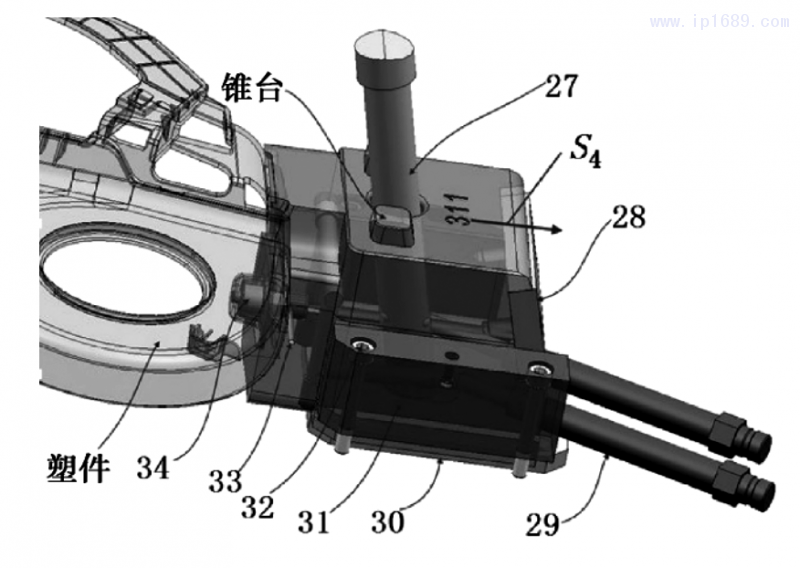
2. 5 模内浇口热切除机构
为实现流道废料与塑件的自动分离,模具中设置模内浇口热切除机构M3、M4,两个机构的结构形式相同,以M3机构为例,该机构在模具内的安装如图6a所示,其结构件组成如图6b所示。机构主要功能件切刀机构安装在模腔型芯镶件上浇口位置处,机构控制则安装在动模板38内。机构的工作原理为:模具闭合注塑完毕,待模腔内的塑件冷却到一定程度,模具打开时,注塑机外部的高压油经进油管口39、高压油管40而进入油道板41内,经油道板41的管道分流控制后,进入微型油缸42内,微型油缸42驱动推杆43顶出,推动切刀座47及其上的切刀50克服刀座弹簧48的阻力将浇口51切开,实现流道52与塑件的分离。切除完毕,高压油经出口油管44排出,切刀座47及推杆43被刀座弹簧48推回复位,等待下一次切除动作。
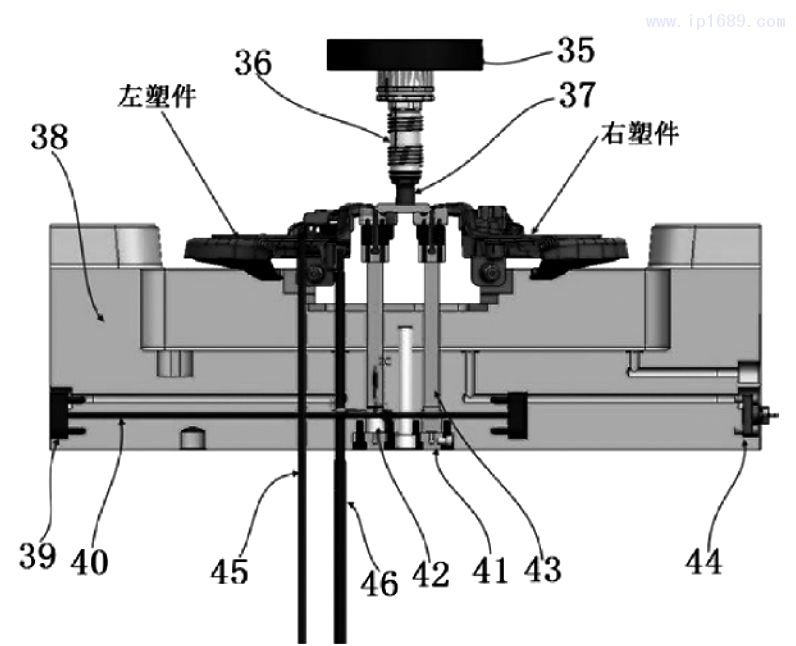
3模具结构及实际生产验证
3.1模具3D结构设计
模具3D结构如图7所示,模具采用两板式热流道结构,通过一个共用的热流道嘴对两个模腔进行熔融塑料输送。模腔的成型件采用型腔镶件78、型芯镶件76组成,鉴于该两成型件尺寸较大,难以控制其精度的需要,该两镶件安装时采用锥度块58靠单边进行锁紧安装,以保证模具闭合时两者的闭合位置精度。塑件采用顶出板上安装斜顶机构、顶针、推管等机构顶出件进行顶出,因为顶出板上安装有16个斜顶机构,36根顶针,4个推管,顶出元件较多,顶出板67、板68的顶出复位位置必须准确可靠,板67、板68的边角上安装有行程开关73,以准确控制此两板的复位。
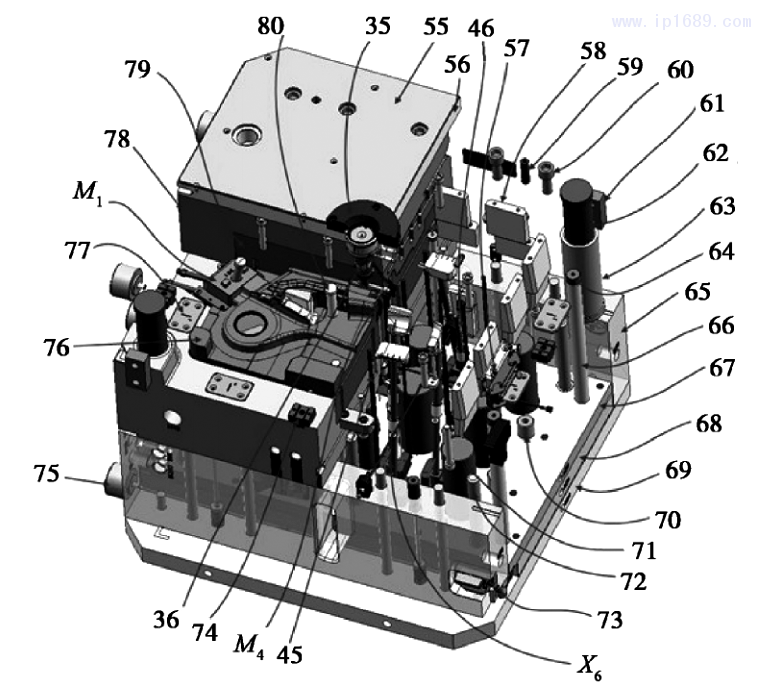
3.2模具加工实物验证
模具零部件经加工完成装配后,组装后的定模如图8a所示,动模如图8b所示。成型件加工完成时,定模模腔内壁的表面粗糙度须抛光至Ra=0.4μm,动模型芯面的经数控铣削加工后表面粗糙度Ra=0.8μm。
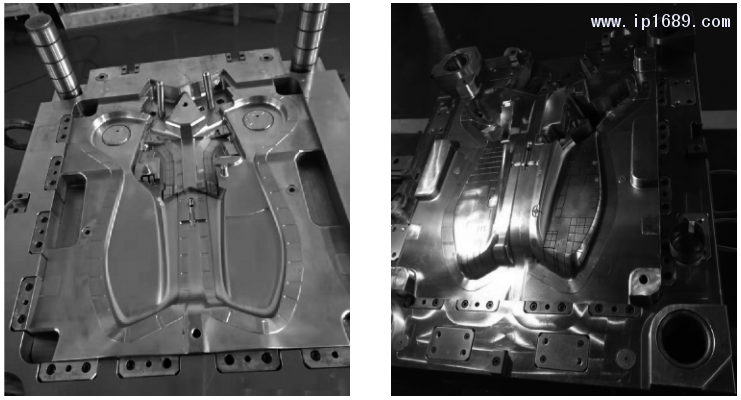
3.3试模塑件实物验证
模具经装配、调试后装于注塑机上进行试模,试模第三次时,左产品上角存在充填不足问题。经模流分析验证后,此处充填压力不足,改善方式有增强排气及扩大浇口两种办法,模腔内注塑PP料时,排气需要增强,故在型腔镶件78上,模腔分型面上等距开设了6条散射状排气槽,其深度为0.02mm,宽度为6mm,对应的引气槽深度0.5mm,并在上端大孔中心位置增设了排气孔。经后续多次试模后,充填不足问题得到解决,塑料成型质量良好,如图9所示。
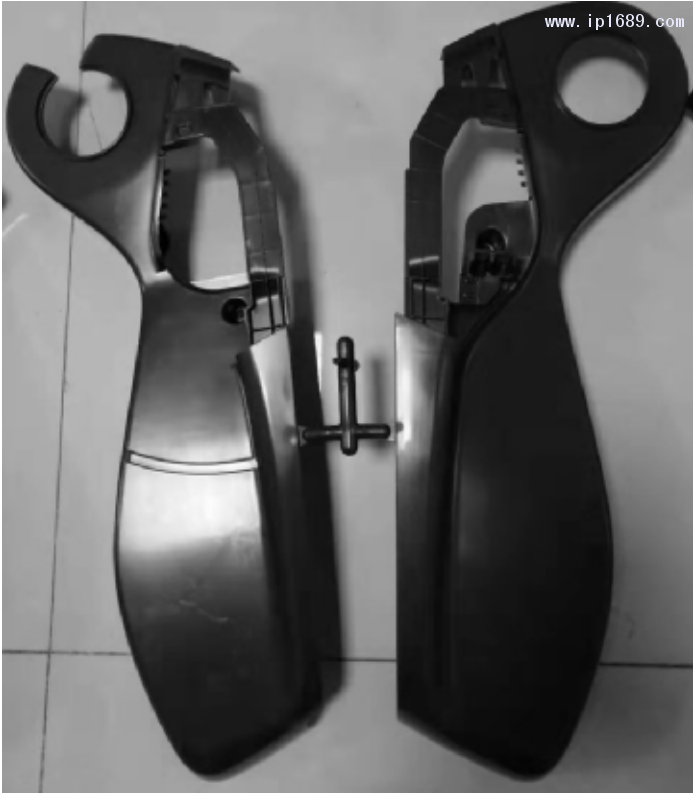
4 结论
1) 针对脱模困难的问题,分别设计了一种斜导柱增强复合斜顶机构,机构针对塑件内壁倒扣需要大角度、长距离侧抽芯而设计,解决普通单斜顶杆大角度、长侧抽芯距离顶出时强度和刚度不足,容易折弯、卡死的问题。2) 针对浇口自动化剪切问题,设计了一种模内浇口热切除机构。机构通过从外部引入高压,推动微型油缸驱动切刀完成浇口在模具上的自
动切除,极大地提高了模具的生产效率,节省了塑件的单件生产成本。
生产实践证明: 基于该模具结构的创新设计,为塑件的成型降低了潜在的技术风险,获得了良好的注塑效果,能为同类塑件的注塑模设计提供良好的参考价值。
参考文献
[1]刘红燕,卞平.基于CAE分析的汽车刹车油盒家族模注塑模具设计[J]. 塑料,2019,48 ( 3) : 70-73.
[2]邵良臣,王悦,张鹏玉,等.基于Moldflow的汽车控制面板旋钮开关注塑模具设计[J].塑料工业,2019,47 ( 5) : 67-71.
[3]孙肖霞,张俊. 基于CAE的汽车拉手外壳注塑工艺参数优化[J].塑料工业,2019,47 ( 9) : 70-73.
[4]洪慎章.汽车车门把手臂注塑工艺及模具设计[J].橡塑技术与装备,2019,45 ( 8) : 38-40.
[5]张维合,成永涛,许淑娟,等.汽车后背门护板热流道大型注塑模设计[J].中国塑料,2019,33 ( 5) : 102-107.
[6]洪慎章.汽车散热器注塑工艺及模具设计[J].橡塑技术与装备,2019,45 ( 4) : 28-30.
[7]洪慎章.汽车仪表外壳注塑工艺及模具设计J].橡塑技术与装备,2019,45 ( 12) : 14-16.
[8]洪慎章.汽车前灯罩注塑工艺及模具设计[J].橡塑技术与装备,2019,45 ( 23) : 25-27.