王新蒙
(唐山工业职业技术学院,河北 唐山,063299)
摘要:针对汽车内饰功能件模内装饰(IMD)成型的需要,设计了该功能件的IMD成型工艺方案,完成了两副关键设备的结构设计。IMD成型工艺包含膜片文创图案丝印、膜片预成型、膜片冲裁、膜片模内注塑等环节。针对膜片预成型工序设计了一种膜片高压预成型模具;针对模内注射成型工序,设计了一种两板两腔单次分型侧浇口注塑模具。实践证明,该成型工艺工序设计合理,成型模具装置结构简单、实用,能为同类内饰件的成型设计提供借鉴。
关键词:模内装饰 高压成型 汽车内饰 工艺设计 模具设计
对于集艺术性、时代性为一体的具有文创图案标识的功能性内饰件,如空调调控面板、中控挡位操控面板等,需运用特殊的注射成型工艺,保证塑件外表面上文创标识的耐磨性能及其清晰度[1-3],此工艺被称为模内装饰(IMD)。该技术是将印有图案的薄膜放入注塑模内进行注塑的一种新技术,其在汽车内饰件生产中有着广泛应用,并被广大消费者喜爱[4-6]。下面结合某乘用车行车模式功能键触摸盖内饰件的IMD成型进行该工艺技术介绍,以供工艺制作及模具设计参考。
1行车模式功能键触摸盖塑件形状
采用IMD成型的功能键触摸盖塑件如图1(a)所示,塑件外围尺寸为 45mmx11mm。塑件由三部分构成,如图1(b)所示,最外层为聚对苯二甲酸乙二醇酯(PET)保护膜耐磨层(厚度为0.125~ 0.250mm),中间层为丝印油墨(厚度为0.125~0.250mm),最内层为丙烯腈-丁二烯-苯乙烯共聚物(ABS)硬胶塑胶层(厚度为2mm)。该塑件在文案位置处实际上有三层,而在非文案处则为两层
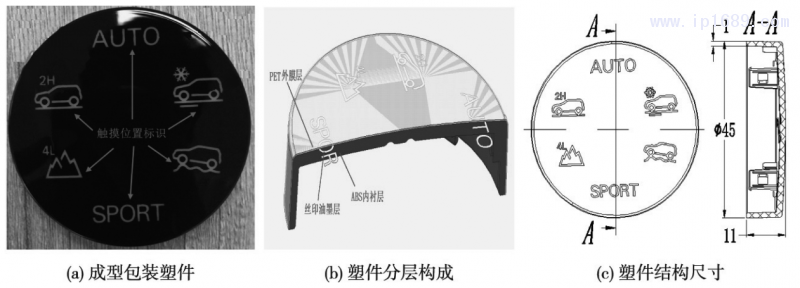
2塑件IMD成型工艺
1)PET硬质膜定制。膜材料选用深圳市森锐泰科技有限公司的PET膜,该膜特点:防变形能力较好,耐高温、耐水、耐化学性,熔点260℃以上,透明性非常优越,透光率90%,不同厚度透光率几乎不变,适用于高端面板印刷。膜的定制采用单面加硬膜,厚度为200μm,该厚度的薄膜应用于该产品特点:抗刮伤性好,耐腐蚀性好,单面可印刷,紫外光胶(UV)/PET油墨附着力强,透明度可达90%以上,可单面/双面油墨增强附着力处理,印刷附着力强。本次成型选用的膜片为单面加硬膜片,加硬膜面涂装硬度级数为2H。PET膜片为卷料。
2)油墨丝印。将图1(a)所示的文字及图案经预变形尺寸分析后,通过丝网印刷的方式,印制于非加硬膜面一侧,如图2(a)所示。
3)定位孔冲裁。油墨烘干后需要进行定位孔设置,为下一步的膜片高压成型做准备,定位孔冲裁如图2(b)所示。
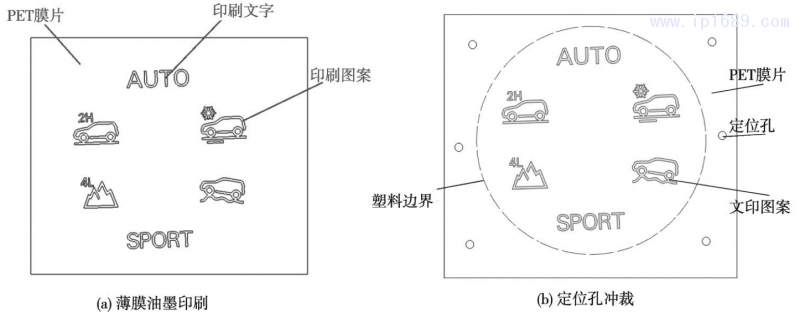
4)将图2(b)中获得的膜片置入高压成型机内,进行膜片的预成型,该步骤需要设计专用膜片高压预成型模具,成型好后的膜片再进行下一步的修边冲裁。
5)将成型后PET膜片放置于专用IMD注塑机内进行注塑,需要设计相应的模内成型注塑模具,该注塑环节不同于普通注塑,对环境温度控制要求较高,需要设置特殊的注塑机及专用注塑机工以保证塑件在一定湿度和温度条件下进行注塑。注塑机环境采用如图3所示的工棚进行控制。
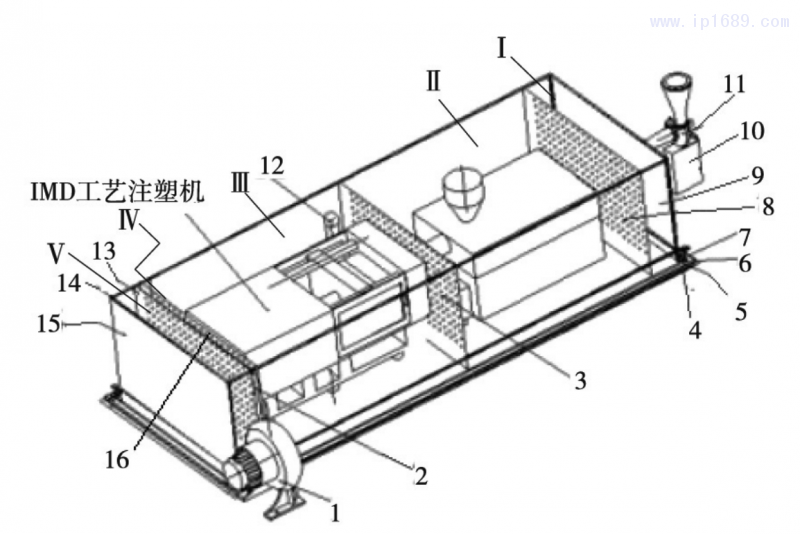
工棚主要是保证制作IMD塑件注塑机为恒温、恒湿、去静电的使用环境。各零件作用:件6,9,15薄膜围成注塑机所需要的独立工作空间,其内设置有件14,3,8,这3个隔热小孔通风板形成Ⅰ~Ⅴ共5个空间,其中Ⅳ空间为灰尘过滤空间。其中件13,16,3,8设置有小圆孔,起到通风的作用。件5,6起到与外界空气隔绝的作用,件4用于调节件5的压紧程度。其工作原理是:件1送等离子风至第Ⅴ室,经件2过滤后进第Ⅲ室、Ⅱ室、Ⅰ室,随后由件11抽送至外部环境中,以防止Ⅱ室内加热空气倒流进Ⅲ室,而影响Ⅲ室内的温度,从而引起IMD制品的翘曲变形。件12为开启注塑机舱门时,保证操作者身上无静电释放。件1所送进的风为等离子空气。Ⅰ、Ⅱ、Ⅲ、Ⅳ室内皆设置有温度、湿度控制传感器,以保证件1在空气输送期间随时依据工况变化而做湿度调整,保证Ⅱ、Ⅲ室内的恒温、恒湿环境。
3膜片高压预成型模具设计
3.1模具结构
膜片高压预成型模具的结构如图4所示。
3.1模具结构
膜片高压预成型模具的结构如图4所示。
模具结构类似于板料冲压模具,由上、下两部分构成。其作用是:模具在高压成型机内放置好后,模具打开,将图2(b)中进行定位制成后的PET印刷膜片放在图4(a)所示的由定位针17与膜片上相应的定位孔定好的位置,高压成型机内的加热装置对膜片进行加热,再将高压成型机上部的冲头将模柄18下压,将上模与下模闭合,对膜片进行成型,成型的膜片如图4(b)所示。
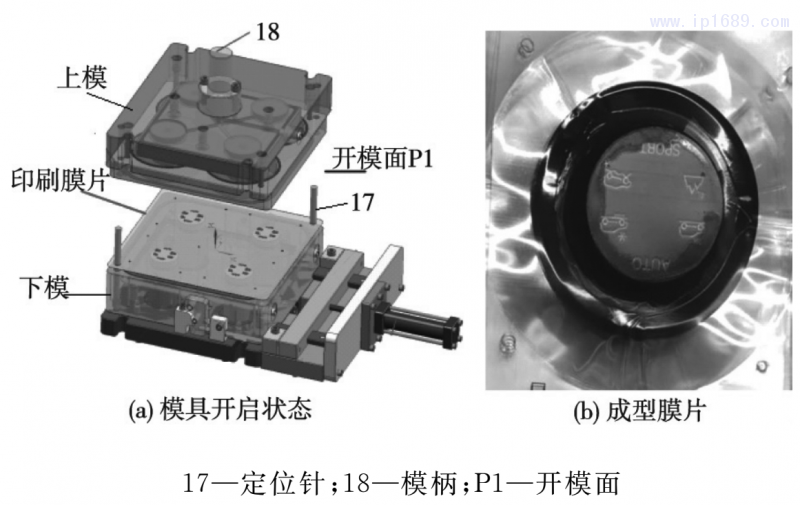
3.2工作原理
具工作原理如图5所示。将PET膜片放入模具中,依靠定位针17定位加热好后,模具闭合,高压成型机将高压气体注入膜片上部的腔体中,从而将软化后的膜片通过高压气体往下压,紧贴住下方的下型芯19,同时膜片下方腔体中的气体由抽气机抽走,保证膜片能无间隙紧贴下型芯19的表面并将其包紧,形成图4(b)所示的成型膜片。成型后膜片的脱模由型腔板20推出和气体辅助顶出2种方式相结合来从型芯19上顶出。
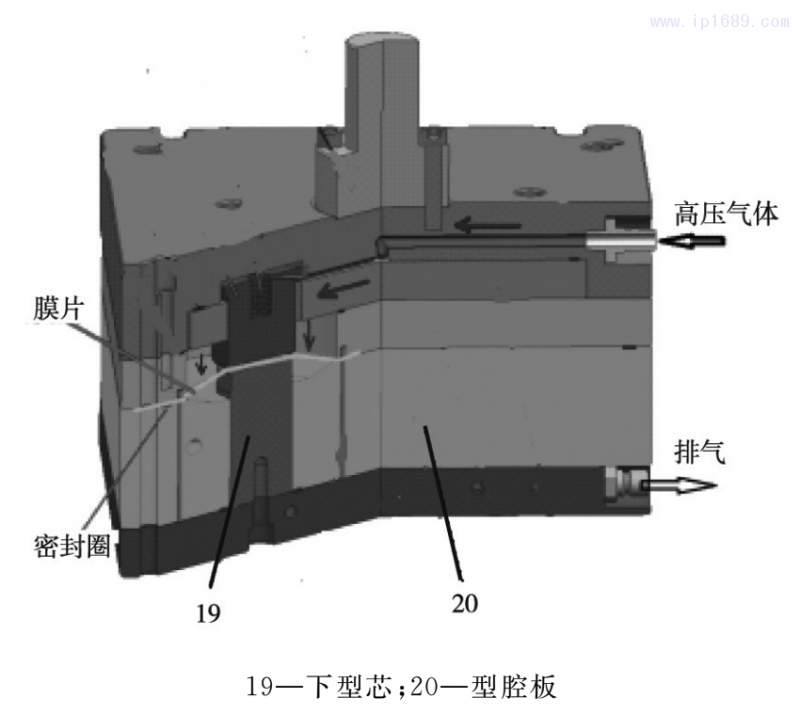
4模内成型注塑模具设计
4.1模具结构
将图4(b)所示预成型膜片进行冲裁修边后,再将该膜片放入图6所示的IMD注塑模具中,对膜片的内表面进行注塑增强加固。使用两板两腔单次开模冷流道侧浇口结构的注塑模具,单腔中,浇口采用开设于脱模推板27上的流道浇口34进行浇注,模腔内的排气则依赖于型芯26与脱模推板27之间的安装间隙来进行,其安装间隙不大于0.02mm。
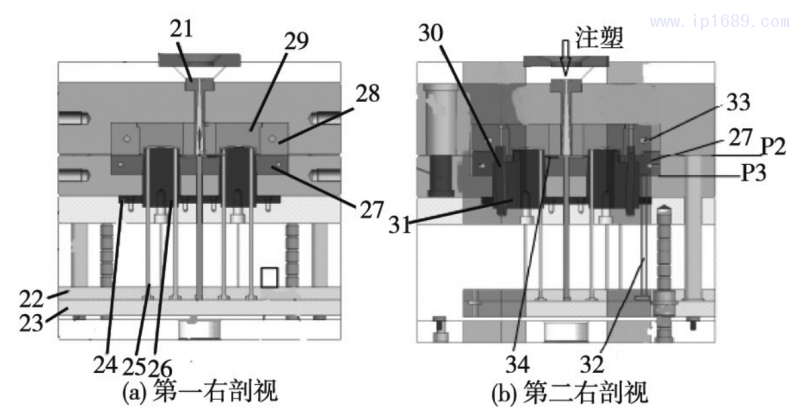
单腔型腔的成型件主要由型腔中央镶件29和型芯26构成。采用8mm水道33进行冷却,型芯26、脱模推板27、型腔镶件28都需要冷却。成型后的塑件脱模依靠3种机构实现:一是依靠推杆32和脱模推板27组合在一起的外沿推板机构实施外边沿的推出脱模;二是内壁上设置顶针25的顶出脱模;三是塑件内壁上4个倒扣的弯销内收抽芯脱模机构,机构由弯销30驱动安装于型芯压板24以下的内滑块31实施内收抽芯,实现塑件内壁上4个倒扣的脱模。
4.2模具工作过程
模具工作过程按照如下步骤。
1)模具安装于注塑机上后,在图6(b)的P2面处打开,依靠机械手,将图4(b)中冲裁好的膜面放入型腔中央镶件29内,并通过背面中空吸住贴紧镶件29的腔壁。
2)模具在P2面处闭合,注塑机喷嘴通过浇口衬套21将塑件注塑到模腔内,熔融塑料通过流道浇口34进入模腔,采用低压注塑方式进行注塑。经保压、冷却等过程后,等待开模。
3)模具在P2面处打开,打开时,弯销30将驱动内滑块31完成塑件内壁4个倒扣内收抽芯脱模。
4)注塑机顶杆推动盖板22、推板23顶出,从而推动推杆32及其连接的脱模推板27、顶针25等联合将塑件从型芯26上顶出,实现塑件的完全脱模。
5)复位时,第4步中的顶出机构必须先复位,而后模具再次从第1步往复循环进行。
05 膜片注射成型工艺
通过塑件IMD成型工艺过程可以看出,膜片热氛围高压吸塑成型、模内IMD注射成型是关键的成型环节,该工序中用到的模具设计关键技术要点和创新点如表1所示。
6结论
a)针对某汽车内饰件艺术图案装饰成型需要,设计了IMD成型工艺方案。
b)针对膜片预成型工序设计了一种膜片高压预成型模具;针对模内注射成型工序,设计了一种两板两腔单次分型侧浇口注塑模具。最终生产出的内饰件文创图案美观清晰、色泽鲜明。
参考文献
参考文献
[1]李天添,赵丹华,赵江洪.基于视觉认知的汽车内饰造型效果图评价体系构建[J].包装工程,2018,39(6):165-169.
[2]赵利平.基于多腔交错排布的操作按钮注塑模具设计[J].现代塑料加工应用,2018,30(4):48-51.
[3]赵丹华,顾方舟.汽车内饰的造型设计与设计研究[J].包装工程,2019,40(16):43-61.
[4]王薇莉,胡在京,陈利民.采用模内装饰技术的手机面板注塑模具设计[J].塑料,2009,38(2):101-103.
[5]李桂芹.汽车仪表罩壳IMF斜曲面膜热定型成型模具设计[J].塑料工业,2016,44(8):44-48.
[6]沈忠良,郑子军,肖国华,等.汽车中控面板IMD成组模具设计[J].工程塑料应用,2017,45(1):70-75.