李志龙,左干清,张鹏程
(中国南方电网有限责任公司超高压输电公司广州局,广东 广州 510663)
摘 要:以某智能巡检机器人的监视装置基座为实例,以模具表面温度、熔体温度和充填压力为分析变量,塑件的体积收缩率为响应指标,设计了响应面试验,构建了响应面分析模型。利用Design Expert进行了方差与响应面分析,并利用Moldflow软件验证优化分析的可靠性。结果表明:相比初始工艺参数,体积收缩率降低14.76%,有效避免了塑件体积收缩率过大的问题,提升了监视器基座成型的质量。
关键词:响应面模型;注塑成型;巡检机器人;优化分析
智能巡检机器人用于替代工作中遇到的急、险、难和重复性工作,是基于多传感器融合技术而搭建的智能移动平台,广泛应用于电力、油井、安防和防爆灯行业,为现场工作人员和设备安全运转提供更多保障[1]。监视摄像机是 智能巡检机器人重要的组成部分[2-3]。监视摄像机一般通过底座固定在智能巡检机器人的躯体上[4],由于监视摄像机的底座与机器人的躯体存在配合要求,并且为了提高美观性,对监视摄像机的底座加工质量要求较高。监视摄像机的底座一般通过注塑加工成型而成,Moldflow是注塑加工行业中常用的模流分析软件,能够准确模拟塑件的成型情况[5-6]。本实验以某型号智能巡检机器人监视摄像机底座为实例,基于响应面模型,对其注塑加工工艺进行优化,得到了较为良好的加工工艺参数。
1 成型工艺分析
图1为利用三维建模软件Pro/E建立的某型号智能巡检机器人监视装置底座的模型。
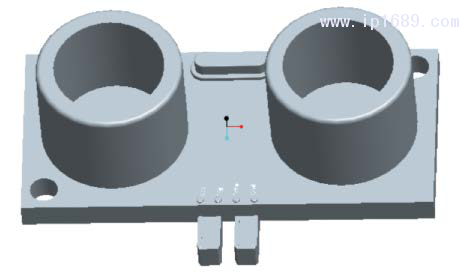
图1 监视装置底座
监视装置底座含有的结构类型较多,包括安装孔、固定块、摄像头基座等。外形总尺寸为45 mm×13.64 mm×25.8 mm,平均壁厚3.2 mm,主要部分的厚度基本保持一致。监视装置的底座材料选择为Generic Default制造商,牌号为Generic PP的聚丙烯(PP)塑料[7],该塑料的熔体密度为0.737 54 g/cm3,固体密度为 0.894 17 g/cm3,表1为推荐工艺参数。
表 1 加工工艺参数
模具表面温度/℃ 熔体温度/℃ 模具温度/℃ 顶出温度/℃ 最大剪切力/MPa 最大剪切速率/s-
50 220 20~80 124 0.25 100000
2 响应面试验设计法
图2为网格划分的结果。网格单元总数为10 368个, 表面积45.81 cm2,纵横比最大为39.8,最小为1.16,平均为2.27,相互百分比91.2%,匹配百分比92.8%。
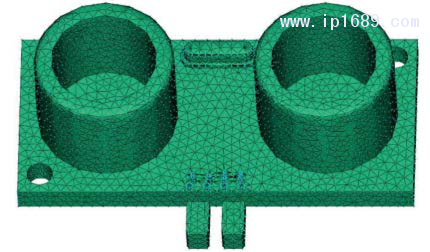
图2 网格划分结果
在Moldflow中创建监视装置底座的冷却系统和浇注系统,图3为所得的有限元分析模型。为使塑件表面各处温度保持一致,冷水管道设计为对称布置,介质选为25 ℃的普通水。综合考虑塑件的外形尺寸及结合最佳浇口位置分析结果,设计为单浇口的形式。
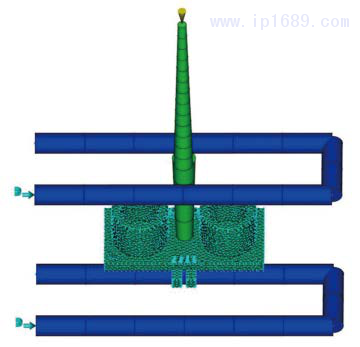
图3 有限元分析模型
3 响应面模型构建与分析
3.1 分析模型建立
选取模具表面温度(A)、熔体温度(B)和充填压力(C)为设计变量,将塑件的体积收缩率(S)作为响应指标变量,基于BBD试验分析法进行响应面分析。表2为响应面的因素水平设计表。表3为响应面的实验结果。
表2 BBD试验因素水平设计
水平 因素
模具表面温度A)/℃ 熔体温度(B)/℃ 充填压力(C)/MPa
-1 30 200 64
0 50 220 80
1 70 240 96
表3 BBD试验方案和结果
方案编号 因素 S/%
A B C
1 1 0 1 12.80
2 -1 0 1 10.74
3 0 0 0 11.52
4 0 -1 -1 10.38
5 1 1 0 12.99
6 1 0 -1 12.11
7 1 -1 0 10.99
8 0 1 1 12.18
9 0 1 -1 12.21
10 0 0 0 11.52
11 0 0 0 11.52
12 0 0 0 11.52
13 -1 -1 0 9.84
14 -1 0 -1 10.85
15 0 -1 1 10.31
16 0 0 0 11.52
17 -1 1 0 11.61
在Design Expert中进行回归分析计算,所得的各个参数与体积收缩率间的响应面模型为:
Y=11.34+0.73A+0.933 5B+0.06C+0.058AB+0.2AC+0.01BC+0.186 5A2-1 685 B2+ 0.098 5C2
3.2 方差与响应面分析
表4为方差分析结果。从表4可以看出,塑件体积收缩率的二阶响应面模型P值小于0.000 1,同时失拟项的P值为0.238 1,表示所建立的响应面模型显著和可靠,可以比较真实有效地反映工艺参数与塑件的体积收缩率的关系。
图4为因素A(模具表面温度)、因素B(熔体温度)、因素C(充填压力)相互作用下的3D响应面图。从图4a可以看出,在较低的模具表面温度和熔体温度的情况下,塑件的体积收缩率最小。从图4b可以看出,较低的模具表面温度和较高的充填压力时,塑件的体积收缩率较小。从图4c 可以看出,较低的熔体温度和较高的充填压力时,塑件的体积收缩率较小。因此,在实际生产时可以考虑降低模具表面温度和熔体温度,并适当提高充填压力的方法来降低塑件的体积收缩率,以提高注塑成型的质量。
表4 方差分析结果
类型 SS DF MS F值 P值 显著性
模型 11.750 9 1.3100 41.15 <0.0001 显著
A-A 4.2700 1 4.2700 134.75 <0.0001 显著
B-B 6.9700 1 6.9700 219.75 <0.0001 显著
C-C 0.0288 1 0.0288 0.0978 0.2641
AB 0.0135 1 0.0135 0.4242 0.5357
AC 0.1600 1 0.1600 8.1900 0.0243 显著
BC 0.0004 1 0.0004 0.0126 0.9137
A² 0.1528 1 0.1528 7.4900 0.0290 显著
B² 0.1139 1 0.1195 6.1200 0.0426 显著
C² 0.0442 1 0.0442 1.3900 0.2762
残差 0.2221 7 0.0317
失拟项 0.1368 3 0.0456 2.1400 0.2381 不显著
纯误差 0.0043 4 0.0013
总和 11.970 16
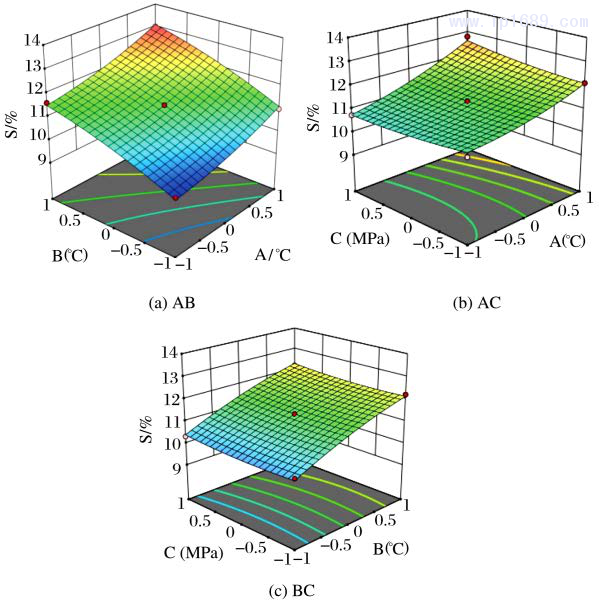
图4 响应面3D 图
4 工艺优化分析
图5为优化后的体积收缩率。
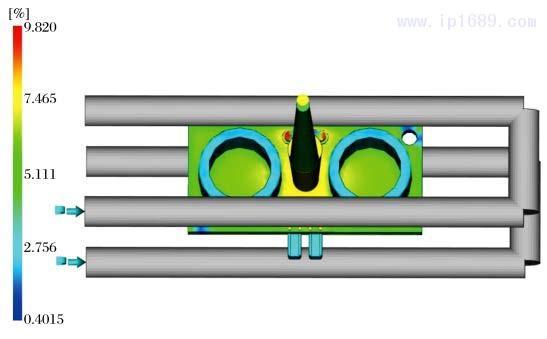
图5 优化后的体积收缩率
与响应面预测值 9.84% 相比,Moldflow 验证结果为 9.82%,仅相差0.02%,说明构建的响应面分析模型具有较高的可靠性和准确性。相比初始工艺参数(A为50 ℃ ,B为220 ℃ ,C为80 MPa)的注塑条件,与推荐工艺参数下的体积收缩率 11.52% 降低了14.76%,有效避免了塑件体积收缩率过大的问题,提升了监视器基座成型的质量。将上述注塑工艺参数进行试模验证,图6为试模样品。从图6可以看出,试模样品外观质量较高,能够满足使用要求。
5 结论
以某智能巡检机器人的监视器塑料基座为实例,分析了其结构外形,选取了合适的材料与加工工艺参数,并建立了响应面模型对影响其体积收缩率的因素进行了优化分析,基于Moldflow软件验证了优化分析的可靠性。结 果表明:相比初始体积收缩率降低了14.76% 与推荐工艺参数相比,有效避免了塑件体积收缩率过大的问题,提升了监视器基座成型的质量。根据优化所得的参数进行试模,效果良好,能够满足要求。
参考文献
[1] 徐波, 陈欢, 田定胜,等.基于Dijkstra的智能巡检机器人避障算法[J].供用电, 2020, 37(12): 74-80.
[2] 王少成, 吕荣鑫, 于福超,等.智能巡检机器人设计[J]. 中国科技信息,2020(23): 80-81, 83.
[3] 金涛.智能轨道式巡检机器人在海洋石油平台首次应用研究[J]. 化工设计通讯, 2020, 46(11): 24-25, 36.
[4] 王学民,徐海奇,刘小寨,等.变电站智能巡检机器人塔杆倾斜识别深度研究[J]. 自动化与仪器仪表, 2020(11): 73-76.
[5] 叶立清.基于UG/MFI 的 LED 灯内壳注塑模具设计[J].塑料科技,2020,48(11):98-102.
[6] 宋云雪,杨天亮.基于响应面模型的防护箱箱体注塑成型优化[J].塑料科技,2020,48(10):8-12.
[7] 李付.基于计算机辅助技术的POE 交换机注塑模具优化分析[J]. 塑料科技, 2020, 48(11): 76-79.