张宗飞,王锦玉,谢鸿洲,汤连英,卢文新
(中国五环工程有限公司,湖北 武汉 430223)
摘 要:概述了可降解塑料的几种典型产品及其市场情况。介绍了聚乳酸(PLA)、聚(对苯二甲酸/己二酸丁二醇酯)(PBAT)等可降解塑料的生产工艺和技术进展,并对其综合性能进行了对比 。 此外,还介绍 了PLA 和 PBAT的市场现状,并对我国可降解塑料未来的市场需求进行了预测。
关键词:可降解塑料;生产工艺;市场分析
doi:10.3969/j.issn.1004-8901.2021.06.002
中图分类号:TQ320.7 文献标识码:A 文章编号:1004-8901(2021)06-0010-04
塑料自20世纪50年代问世以来,给人们的生活带来了极大的便利,曾被誉为20 世纪最伟大的发明之一。然而,当前广泛使用的塑料,如聚乙烯、聚丙烯、聚氯乙烯等,均需数百年才能降解,且废塑料通常采取填埋和焚烧的方式进行处理,由此带来的环境污染问题日益严峻。据数据统计,1950 年至今合计产生约 83 亿t塑料,其中回收利用率仅9%。目前,全球每年塑料产量约3.7 亿t,预计到2050年将增加2倍。
可降解塑料被认为是解决塑料污染问题的有效途径之一,全球多个国家和地区相继出台了限制或禁止使用一次性不可降解塑料制品的相关政策 或规定,以推动可降解塑料的发展。我 国在2020年初出台了被业界称为“最严限塑令”的《关于进一步加强塑料污染治理的意见》,提出了可降解塑料推广应用的时间表[1,2]。随着国内各地禁塑政策的逐步制定和执行,我国可降解塑料迎来了空前的发展机遇,未来市场使用率有望和欧美发达国家平齐。
1 可降解塑料产品介绍
可降解塑料是指各项性 能可满足使用要求,在保存期内性能不变,而使用后在自然环境条件下能降解成对环境无害的物质的塑料[3]。 按原料来源主要分为石油基、生物基和煤基三大类,石油基可降解塑料包括聚对苯二甲酸/己二酸丁二醇酯(PBAT)和聚丁二酸丁二 醇酯(PBS)、聚己内酯(PCL)等,生物基可降解塑料包括淀粉基、纤维素、聚乳酸(PLA)、聚羟基脂肪酸酯(PHA)等,煤基可降解塑料有聚乙醇酸(PGA)。另外,在“双碳”背景下,CO2基可降解塑料PPC具有一定的工业化价值,现已初具规模。2020年全球可降解塑料产能达 到122.7万t,欧洲 生 物塑料协会统计的产能分布见图 1,淀粉基 、PLA 、PBAT为主流产品,产能占比分别为32%、32%、23%,三者合计占比87%。其中,部分淀粉基塑料存在争议,目前,仅淀粉基完全生物降解塑料被广泛认可,因此,本文不再对其作详细介绍,仅介绍几种主流的可降解塑料。
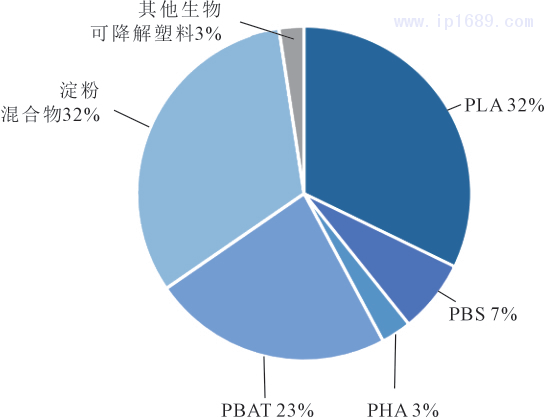
图1 2020年全球可降解塑料产能分布
1.1主流可降解塑料
1.1.1 PLA
聚乳酸又称为聚丙交酯,由乳酸聚合而成,其聚合单体乳酸以可再生的植物资源(主要是玉 米)所提取的淀粉为原料,经糖化得到葡萄糖,再经菌种发酵而成。乳酸聚合制备PLA有乳酸直接缩聚法(一步法)和丙交酯开环聚合法(二步法)两种不同的生产工艺,工艺路线见图2。
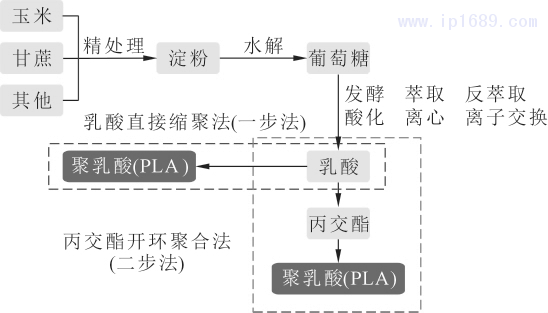
图2 PLA 的生产工艺路线
一步法即乳酸在催化剂作用下脱水缩聚成聚乳酸,该工艺的优点包括流程短和成本低等,缺点主要在于缩聚副产物(水)难以从高黏度体系中脱除,难以获得高分子量的PLA产品。 受此限制,该工艺工业应用程度低,国内目前仅上海同杰良公司采用同济大学的一步法工艺技术制备PLA 。
两步法先是乳酸经过缩聚和解聚步骤得到中间单体丙交酯,再经开环聚合制备PLA。该工艺虽存在生产工艺流程长、生产成本高 、丙交酯难以精制等缺陷,但制备的PLA产品分子量较高,可满足高端领域的应用需求,因而两步法成为主流的PLA生产工艺。国内PLA聚合技术商包括中科院长春应化所 、南京大学、常州大学、成都有机化学研究所、武汉大学等[1]。丙交酯的合成和纯化是PLA产业链的技术难点,国内多数企业不具备丙交酯生产能力,均外购NatureWorks 和 Corbion生产 的丙 交酯生产PLA。目前,我国金丹科技、浙江海正和 安徽丰原具备高分析纯、化学纯丙交酯的生产能力,其中,安徽丰原已具备规模化生产能力。此外,国内中粮科技计划建立“玉米-乳 酸-丙交酯 -聚乳酸”的全产业链生产基地。
1.1.2 PBAT
PBAT为脂肪族-芳香族共聚酯。聚二元酸二元醇酯工业化制备方法有扩链法和酯化-缩聚法,其中,扩链法由于需要用到具有毒性的异氰酸酯类扩链剂,所制备的产品在用于食品包装领域时存在安全隐患。
PBAT以1,4-丁二醇(BDO)、己二酸(AA)、对苯二甲酸(PTA)为原料,经酯化-缩聚反应而制得。 其生产工艺根据聚合单体参加反应顺序的不同,可分为共酯化法(直接酯化)、分酯化法和串联酯化法[4],具体见图3。共酯化法为三种聚合单体经过酯化和缩聚反应合成PBAT,该工艺具有工艺流程短、原料利用率高、反应时间短、生产效率高等优点,成为我国PBAT主流生产工艺 。分酯化和串联酯化工艺通过聚合单体分开进行反应的方式合成PBAT,优点有产品分子量分布窄、设备简单、反应体系中间物质较少等,缺点是各批次产品质量可能存在差异。
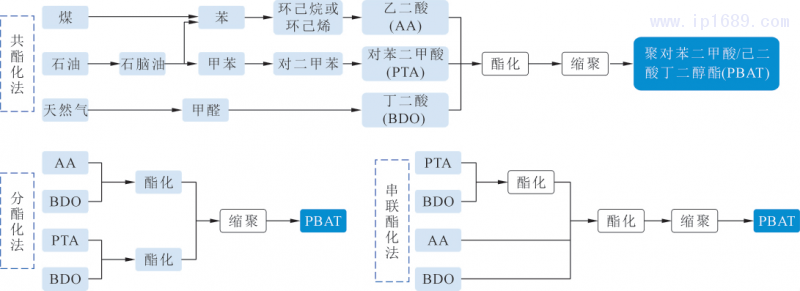
图3 PBAT 的生产工艺路线
PBAT生产工艺最初由德国巴斯夫开发,国内技术商包括上海聚友、北京芯友、蓝山屯河公司、金发科技等。中国五环工程有限公司(以下简称中国五环)在PBAT和PBS的产品上拥有丰富的设计建设和总承包经验,先后承接了望京龙、旭科、宇新等多个项目的设计工作。此外,为降低PBAT的成本,提高市场接受度,中国五环开发了低成本 PBAT产品,其综合性能与市面上通用PBAT相当,甚至更优,且原料成本比商品化PBAT低20%左右 。
1.2其他可降解塑料
1.2.1 PGA
PGA又称聚乙交酯,以乙醇酸或其前驱体乙醇酸甲酯为原料聚合而成。乙醇酸制备PGA有乙醇酸直接缩聚法(一步法)和乙交酯开环聚合法(二步法)两种生产工艺[5]。当前PGA的生产以两步法为主,技术商包括日本吴宇化学、上海浦景化工、江苏金聚、惠生工程和中国五环等。
PGA聚合原料乙醇酸可由煤制乙二醇装置联产制备,通过更换DMO的加氢催化剂,可以在乙二醇装置上侧线生产乙醇酸甲酯,以及经水解结晶进一步生产乙醇酸。中国五环联合其他技术方开发了合成气制聚合级乙二醇技术,并采用该技术以EPC模式建设了内蒙古荣信化工乙二醇 、新疆广汇荒煤气制乙二醇等多个大型项目,具有深厚的技术积累和丰富的工程经验。基于此,中国五环正进行合成气制高分子量PGA的全流程技术开发,目前已掌握关键单体—高纯乙交酯的合成技术和乙交酯聚合小试技术,所得乙交酯产品纯度和收率均较高,而且生产成本较低,具有技术和经济双重优势。
1.2.2 PCL
PCL是由ε-己内酯开环聚合制备的一类线性脂肪族聚酯,其生产难点在于原料ε-CL的生产,由于ε-CL生产时需要使用过氧酸作为氧化剂,储运过程中安全风险较高[1],其生产技术长期被德国Perstorp 公 司和日本大赛璐公司垄断。 我国ε-CL长期依赖进口,近年来湖南聚仁打破限制,现已具备生产能力并对外供货。
1.2.3 PPC
PPC是由二氧化碳和环氧丙烷共聚而成的脂肪族聚酯,其中二氧化碳含量约40%[6]。PPC聚合的关键技术在于催化剂以及工艺控制技术,当前,国内技术主要掌握在科研机构及高校手中,中科院长春应化所研发的稀土三元催化剂、中山大学研发的负载型催化剂以及中科院广州化学所研发的双金属催化剂体系均已工业化,此外,兰州大学和浙江大学也均有自主研发的催化剂体系,但尚未工业化应用。目前,我国PPC已实现工业化,江苏中科金龙化工、浙江台州邦丰塑料、河南天冠集团、吉林博大东方等采用相关技术拟建/建成PPC工业化装置,但由于目前催化剂和工艺控制技术不够成熟,以及下游应用不明确,PPC尚未实现大规模生产和应用。
1.2.4 PHA
PHA 是一类 由3-羟基脂肪酸组成的高分子线性聚酯的统称,在细菌体内合成,细菌的种类和摄入的原料决定了PHA 的分子结构[6],不同PHA 的区别主要在于C-3位上侧链基团不同,现发现的PHA有150余种,以侧链为甲基的聚3-羟基甲-酸(PHB)最为常见。目前掌握PHA生产技术的技术商主要有日本 Kaneka 、P&G、国韵生物和蓝晶微生物等,但PHB技术门槛高且生产成本较高 、产品质量难以控制,目前市场规模较小。近年来,蓝晶微生物的PHA技术进展迅速,已成功融资数亿元,有望在未来几年实现万吨级工业化生产。
1.3可降解塑料综合性能对比
市场上可降解塑料产品种类繁多,从性能角度来看各有优缺点,将典型的可降解塑料的综合性能进行对比,结果见表1[3]。具体来看,PLA 拉伸强度和杨氏模量较高,但延伸率最低、韧性差,通常采用合金共混的方式来改善PLA 的脆性,提高其柔韧性和抗冲击强度。PBAT力学强度低,但延伸率是PLA 的数百倍,韧性好。PBS的综合性 能优异,但由于亲水性过强,存在储存稳定性差的问题,而且目前受制于其原料丁二酸供应短缺,尚未实现规模化应用。PGA 力学强度最佳,气体阻隔性好,降解速率快,但是韧性差、加工困难[7]。PCL耐热性较差,力学性能一般,降解速率慢。PHA综合性能优异,且可海水降解,但当 前价格太高,难以普及应用。PPC 的韧性较好,但为无定形聚合物,而且耐热性较差,因此难以单独使用,一般作为改性组分进行共混应用。
2 可降解塑料市场分析
2.1 主流可降解塑料市场分析
当前,PBS 、PGA 、PCL 、PPC和PHA的市场容量较小,本文主要介绍市场份额较高的PBAT和PLA的市场情况。
2.1.1 PLA 市场分析
据华安证券统计,全球PLA 主要生产企业及产能情况见表2 。 全球PLA 产能约48.65 万t/a,其中国外产能约25.15万t/a,国内产能约23.5万t/a。国外产能集中在西欧和美国,美国的Nature-works是全球最大的PLA 生产企业,产能达15万t/a,占据了全球30% 以上的PLA产能。近年来,国内一些玉米深加工企业和生物化工企业开始投资进入PLA产业,但受制于乳酸来源 、丙交酯生产技术等方面的 原因,我国PLA产业仍处于起步阶段,产能分散度较高,单家公司的产能都较小,但随着安徽丰原及其他生产厂商逐步突破丙交酯生产技术,PLA 放量在即。
2.1.2 PBAT 市场分析
据德邦证券统计,全球 PBAT主要生产企业及产能见表3。 当前,全球 PBAT 产能共约50万t/a, 其中国外约17.4 万t/a,国内约32.6万 t/a。 全球PBAT产能最大的两家企业是意大利 Novamont(10万t/a)和德国 BASF(7.4万t/a),国内生产规模较大的为蓝山屯河(12.8万t/a)、金发科技(6万 t/a)和康辉石化(3.3万t/a)等。自2020年1月禁塑令出台以来,国内掀起可降解塑料扩产潮,其中PBAT规划新增远超其他可降解塑料,远期产能规划超800 万t/a,但能否如期开建,取决于PBAT的推广应用程度。
2.2 国内可降解塑料市场需求预测
华安证券研究所根据国内各省市禁塑政策执行时间和执行力度,以及海外可降解塑料的发展现状,对国内可降解塑料市场需求进行预测,今后5年预测数据见表4。
假设我国废弃塑料总量维持在4200万t/a不变,预计可降解塑料替代率将呈逐年递增的变化趋势,从2021年的2.34%增长至2025年的4.92%。包装和农用地膜是可降解塑料最主要的两个下游市场,2021年两者合计占比约90%以上。2021年,国内可降解塑料的下游需求约为107.5 万t/a,随着限塑禁塑政策的出台和“双碳”理念的普及,可降解塑料的需求快速增长,预计2025年国内消费量将达到 225.3 万t,累加净出口量将达到 238.5万t。如果按均价2万元/t计算,2025年我国可降解塑料市场规模将达到477亿元。总体来看,我国可降解塑料需求总体呈现减缓上升的趋势,未来市场空间巨大。
3 结语
根据上文中的分析,可得出如下结论:①在环保和政策的双驱动下,可降解塑料产业具有极大的发展空间,预计可降解塑料市场将会加速扩张。PLA和PBAT是当前主流的可降解 塑料产品,占据较大的市场份额。中国五环从技术和工程两端发力,在PBAT和 PGA 等产品领域有坚实的技术沉淀和丰富的工程经验,同时开发了低成本PBAT产品,极大地迎合了市场对于低成本可降解塑料的强烈需求。
参考文献
[1]陈韶辉,李涛.生物降解塑料的产业现状及其发展前景[J].现代塑料加工应用,2020,32(2):50-54.
[2]林世东,杜 国强,顾君,等.我国生物基及可降解塑料发展研究 [J].塑料工业,2021,49(3),10-13.
[3] 谢鸿洲,卢文新,商宽祥.几种可生物降解塑料的性能与应用比较研究[J].化肥设计,2020,58(4):4-6.
[4] 欧阳春平,卢昌利,郭志龙,等.聚对苯二甲酸-己二酸丁二醇酯 (PBAT)合成工艺技术研究进展与应用展望[J].广 东 化 工, 2021,48(6):47-48.
[5] 王淑敏,商宽祥,谢鸿洲,王锦玉.聚乙醇酸产业现状和发展前景 [J].化肥设计,2021,59(4):1-4.
[6] 白聪艳.生物可降解塑料的研究现状分析[J].当代化工研究, 2021(7):4-5.
[7] 陶怡,柯彦,李俊彪,等.我国生物可降解塑料市场现状[J].化工管理,2020,33(2):118-119.
[8] 陈岳.聚碳酸亚丙酯及 其 复合材料的性能研究[D].湘 潭: 湘潭大学,2013.