邓小珍1 ,肖兵1 ,任重2
(1. 南昌工程学院 江西省精密驱动与控制重点实验室,江西 南昌 330099;2. 江 西科技师范大学 江西省光电子与通信重点实验室,江西 南昌 330038)
摘要: 挤出成型是聚合物加工领域出现得较早且应用最广泛的技术之一,聚合物传统挤出成型过程中存在的挤出胀大、扭曲变形等问题严重阻碍了该技术的进一步发展及其推广应用。聚合物气辅挤出是本世纪初发展起来的一种新型成型工艺,通过在口模内壁与熔体表面间形成稳定的气垫膜层,使熔体以完全滑移非粘着方式挤出成型,改善了口模内熔体的流场分布,从而有效减小甚至消除了传统挤出过程中存在的影响制品质量的固有问题。该技术因具有节能、环保、改善制品质量等优良特性,自问世以来即受到聚合物加工领域诸多学者的广泛关注,相关研究成果对丰富和发展聚合物成型理论及其加工技术的进一步推广应用均具有重要的科学意义和工程价值。本文综述了聚合物气辅挤出成型问世以来国内外研究进展,主要介绍了该技术的成型机理和成型装置,气体辅助单层挤出、双层共挤、微管挤出及气垫膜层等方面的研究方法与研究成果,并在综述现有的研究基础上展望了气辅挤出成型的研究趋势。
关键词: 聚合物;气体辅助技术;挤出胀大;气垫膜层
挤出成型是聚合物加工中出现较早的一门技术,经过一个多世纪的发展,因其生产效率高、适应性强、用途广泛,已成为聚合物加工领域中生产品种最多、产量最大、变化最多的加工方法之一,然而,传统挤出成型产生的挤出胀大[1]、“鲨鱼皮”现象[2]、扭曲变形[3]、黏性包围[4] 、界面不稳定[5]等问题严重影响了制品质量,制约了该项技术的进一步发展。为解决上述难题,提高聚合物挤出产品质量,行内研究者将气体作为辅助介质引入挤出成型,形成全新的聚合物气体辅助挤出成型技术(简称气辅挤出)。气辅挤出因在口模内壁与聚合物熔体表面间形成了稳定气垫膜层,对熔体流动起到润滑作用,使得口模内熔体的速度场趋于均匀一致,剪切速率和应力值趋于零,熔体呈柱塞状挤出。因具有节能、环保和改善制品质量等优势,气辅挤出自问世以来备受相关领域研究者的关注,成为聚合物加工领域的研究热点,研究者们开展了大量的研究工作,取得了丰硕研究成果。现有公开发表文献表明,与传统挤出相比,气辅挤出能有效消除挤出胀大和翘曲或偏转变形,减少黏性包围和界面不稳定等固有问题,还能明显节能减耗,提高聚合物制品生产效率[6, 7]。
1 气体辅助挤出成型机理
传统挤出时,黏弹熔体在口模内作剪切流动时,挤出胀大现象随着法向应力差和剪切速率的增大而增大,且剪切速率在熔体破裂前达到最大值[8],而气辅挤出是基于完全滑移非粘着挤出成型机理,由气体辅助装置将气体以低速注入熔体与口模壁面之间,形成稳定气垫膜层,使熔体在口模内的流动为完全滑移流动,从而使得口模内熔体速度场趋于均匀一致,口模出口处的剪切速率趋于零值,熔体呈柱塞状挤出,如 Fig. 1 所示。
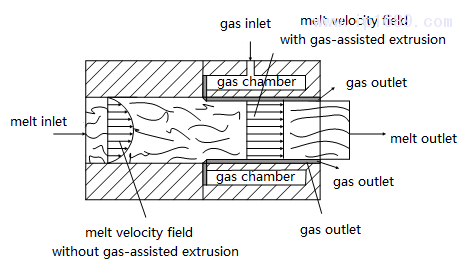
2 气体辅助挤出口模结构
气辅挤出口模结构对形成稳定的气垫膜层至关重要,将气体引入口模的方式主要有2种:一是多孔金属管进气法;二是缝隙进气法。多孔金属管进气口模如 Fig.2 所示,图中A段为进料段,B段为气辅挤出段,其中B段包含1个孔径0.5μm的粉末冶金套管,气体能经过多孔粉末冶金套管进入到口模壁面与熔体表面之间,形成稳定的气垫膜层。多孔金属管进气时,熔体容易将金属管的微小进气孔隙堵塞,且堵塞孔隙的熔体很难清理,影响后续气垫膜层的有效形成。此外,多孔金属管进气口模内气体压力在气体入口与出口区域内是相等的,而口模内熔体内应力在气体入口与出口区域内是逐渐减小的,口模内气体压力与熔体内应力的不平衡将影响挤出制品表面质量,因此,此种进气方法目前研究较少。
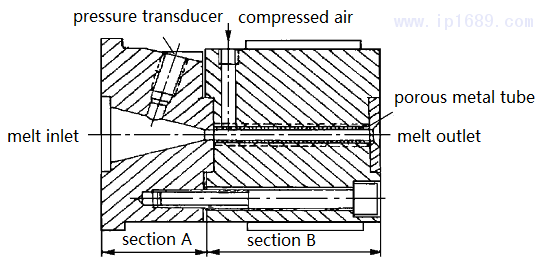
缝隙进气法口模由上、下两部分组成,上部分为传统挤出段,下部分为气辅挤出段,如 Fig.3 所示,上、下两部分之间有δ=0.1mm的环形缝隙,下部分有一气室,气体先进入气室再由环形缝隙进入口模,在口模壁面与熔体表面之间形成稳定的气垫膜层。缝隙进气时,熔体不容易堵塞进气缝隙,即使堵塞,也容易清理缝隙中的熔体,此外,气体压力与熔体内应力都是从气辅挤出入口处到出口处逐渐减小的,两者容易达到平衡,使得挤出物表面质量良好,因此,目前气辅挤出相关研究中大多使用缝隙进气法。
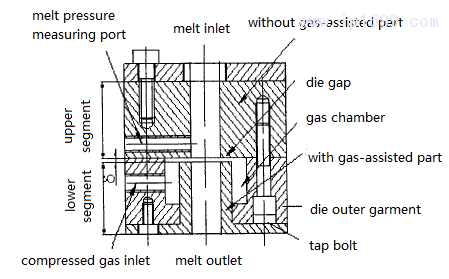
3 圆形棒材气辅挤出
1987年,Brzoskowski等[10]为减小橡胶挤出成型过程中口模内橡胶熔体的流动阻力,首次将压缩空气作为辅助介质引入橡胶挤出成型,他们采用多孔金属管把压缩空气引入口模内壁与橡胶熔体表面之间,形成稳定的气垫膜层。稳定气垫膜层的形成对熔体流动起到润滑作用,大大减小了口模内橡胶熔体的流动阻力,降低了口模压降,减小了橡胶的挤出胀大率,同时能有效提高橡胶挤出生产效率和产品质量。随后,钱百年等[12]采用多孔金属 管进气法将压缩空气引入口模,对短纤维增强胶管挤出进行了数值模拟和实验研究,结果表明,气体辅助技术不仅能明显降低机头阻力,提高挤出产量,降低挤出膨胀程度,还能成功消除物料出口后产生的扭转变形。
2001年,Liang等[13]首次采用缝隙进气法将氮气引入高密度聚乙烯(HDPE) 圆形棒材和狭缝形片材的挤出成型,实验研究结果表明,不论是圆形还是狭缝形口模,气体辅助技术均能有效减小口模压降和挤出胀大率,提高产品产量。为验证口模内气垫膜层使熔体产生完全滑移流动的假设,他们将气垫膜层简化成完全滑移边界条件,采用Polyflow软件对圆形棒材和狭缝形片材进行了二维等温数值模拟研究,数值模拟与实验研究结果一致。此后,黄兴元[11] 以过滤后的压缩空气为辅助介质,采用缝隙进气法对 HDPE圆形棒材气辅挤出进行了系统的实验和理论研究,研究结果表明,与传统挤出相比,气辅挤出基本可以消除挤出胀大行为,大幅降低口模压降。肖建华[14]以HDPE,PP和ABS的圆形棒材气辅挤出为对象,研究了气辅挤出缩小现象及口模入口几何构型和滑移段长度(即气辅段长度) 对气辅挤出胀大的影响,研究结果表明,提高气体温度至熔体温度,可在根本上消除半固态熔膜引起的挤出缩小现象,而适当降低熔体挤出温度和采用淋浴设施相结合的方法则可消除熔垂现象引起的挤出缩小问题;流线型口模比非流线型口模在挤出压力、流动速度和应力集中等方面均有明显优势;延长滑移段长度可减小挤出胀大,获得精确的外形尺寸,此外,还能降低挤出压力,减小应力集中,提高挤出制品表观质量。
4 异型材气辅挤出
在圆形棒材成功实现气辅挤出的研究基础上,卢臣[15]基于Phan-Thien-Tanner (PTT) 本构方程运用Polyflow软件对T形异型材气辅挤出实现了三维等温数值模拟,并选用LDPE材料进行了实验验证,研究结果表明,对于T形异型材,气体辅助技术仍能有效减小挤出胀大和口模压降,说明气辅挤出具有广泛的适应性,对于不同物性的材料和口模构型均能成功实现气辅挤出。李萍[16]对“工”形和钢骨架塑料复合管气辅挤出进行了数值模拟研究,周国发等[17]对马鞍形异型材气辅挤出进行了数值模拟研究, Ren 等[7, 18]对中空方形管材和 L 形管材气辅挤出进行数值模拟研究,他们的研究结果一致表明,由于气垫层的减黏降阻作用,异型材气辅挤出过程中,各偏应力分量、切剪速率、第一和第二法向应力差及口模压降均远小于传统挤出,故气辅挤出能明显消除异型材的挤出胀大和翘曲变形,还能起到节能减耗的作用,说明气辅挤出不仅可实现异型材挤出制品尺寸的精确自动控制,还能有效解决异型材挤出口模难于设计的技术难题,这对气辅挤出的推广应用具有重要意义。
尹洪娜等[19]基于PTT黏弹本构方程运用Polyflow构建了描述线缆包覆挤出流动的数值模型,对线缆包覆传统挤出和气辅挤出进行了数值模拟研究,研究结果表明,与棒材和各种截面形状异型材的气辅挤出不同,线缆包覆气辅挤出不能消除传统挤出过程中的挤出胀大,但气辅技术仍然成功运用于线缆包覆挤出,且能有效降低口模压降,减小能耗,还能有效降低口模出口处的剪切应力,提高线缆包覆表面质量。
5 气体辅助共挤出成型
为解决聚合物传统共挤产生的挤出胀大、黏性包围和层间界面不稳定等问题,推动共挤技术的进一步发展,南昌大学柳和生课题组在多年单层气辅挤出数值模拟与实验研究基础上,将气体辅助技术应用于聚合物共挤成型,并进行了深入系统的研究。黄益宾[9]以30mm×20mm 矩形叠层共挤为对象,研制了气辅共挤成型实验系统,研究了矩形叠层气辅共挤过程中,稳定气垫膜层形成条件和影响因素以及各工艺参数对挤出胀大、黏性包围及界 面稳定性的影响。邓小珍[20]设计了L形截面异型材叠层和包覆气辅共挤口模,基于PTT黏弹本构模型建立了“气-液-液”多相流L形异型材共挤成型机理模型,并对L形异型材叠层和包覆共挤成型进行了深入系统的理论和实验研究。陈璐璐[21]对Y形截面异型材包覆 气辅共挤进行了数值模拟和实验研究。研究结果表明,气辅共挤能有效减小甚至消除传统共挤产生的挤出胀大和口模外的扭转或偏转变形,能改善黏性包围和界面不稳定现象,且与物料特性无关,即气体辅助技术能较好适应各种聚合物物料的共挤出成型;能有效降低口模压降,在相同能耗下,气辅共挤产量比传统共挤大,产量的增幅与物料黏度有关,黏度越大增幅越大。
此外,邓小珍等[22]还对曲线型异型材包覆气辅共挤进行了三维数值研究,相对传统共挤,气辅共挤制品的挤出胀大、偏转(扭转)变形现象以及口模内熔体速度场、压力场、剪切速率和应力场等的分布均与芯壳熔体的物性无关,能实现制品截面与口模截面保持一致,即气辅共挤能实现聚合物复合制品的精密自动成型。
6 气体辅助微挤出成型
近年来,随着微/纳米科学技术的蓬勃发展,产品逐渐向小型化、微型化、精密化方面发展,聚合物气辅挤出成型研究也逐渐趋于微量化,目前,公开发表文献关于气辅微挤出的研究主要集中于塑料微管的挤出成型,旨在解决传统塑料微管挤出过程中产生的离模膨胀、熔体破裂和挤出变形等固有问题。
黄楚晔[23]基于Bird-Carreau纯黏本构模型运用Polyflow 软件对单腔微管气辅挤出过程进行了有限元研究,并与传统微管挤出进行了对比分析,任重等[24-26]设计了塑料单腔微管气辅挤出口模,基于Bird-Carreau纯黏本构方程和PTT 黏弹本构方程建立了“气-液-气”多相分层流动单腔微管气辅挤出成型机理模型,并对单腔微管传统挤出和气辅挤出进行了系统深入的理论分析和实验研究,研究结果表明,气体辅助技术可不受挤出物料特性和各工艺参数的影响,有效消除口模内壁、芯棒外壁及口模出口处塑料熔体的剪切应力和第一法向应力,从而克服传统微管挤出中由剪切应力和第一法向应力引起的挤出胀大、熔体破裂和扭曲变形等缺陷,有效提高微管表面光洁度和透明度。Ren[27]对内外半径分别为1.5mm 和1.8mm的四腔微管气辅挤出进行了数值模拟,结果表明,气辅挤出中熔体的径向速度、口模压降、剪切速率和第一法向应力差趋于零值,而熔体轴向速度均匀一致,这有利于消除挤出胀大,实现四腔微管精密挤出成型。
李福成[28]研究了医用双腔和五腔导管挤出流动行为,研究结果表明,气体辅助技术可使多腔导管挤出过程中的剪切变形速率和第二法向应力差趋于零值,从而消除径向二次流动,达到调控医用多腔导管挤出胀大和椭圆度误差的目的,实现多腔导管的精密挤出成型。陈思维[29]选用医用级TPU为挤出材料,氮气为辅助介质,进行了直径为1mm的细丝气辅挤出实验研究和CAE理论分析,研究结果表明,在适宜的工艺条件范围内,医用级TPU细丝气辅挤出能有效降低挤出口模内的压力降和第一法向应力差,能有效消除细丝传统挤出产生的挤出胀大,减小挤出过程的功耗,还能有效改善挤出物表观质量。周友明[30]研制了直径1 mm的细丝气辅挤出机头和内外直径分别为1.4 mm和2.0mm的单腔微管挤出机头,选用热塑性弹性体TPE为挤出材料,氮气为辅助介质,进行了系统的实验研究,结果表明,细丝挤出过程中,气体辅助能有效减小挤出胀大率,对制品表面粗糙度也有较大的改善作用,但对制品拉伸强度没有明显改善;单腔微管挤出过程中,采用内外双层气辅比采用内层(单层)气辅挤出效果要好,在合理的工艺条件下,采用内外双层气辅挤出可实现TPE单腔微管的精密挤出成型。王嫘等[31, 32]在对纵向单通道和三通道矩形微管挤出研究中发现,引入气体辅助技术可有效抑制矩形微管宽度方向的离模膨胀,同时减小中央通道的长宽比,使注气压差较大时的通道均匀性高于传统挤出。
7 气垫膜层研究
不论是单层挤出还是多层共挤,稳定气垫膜层的形成是成功实现气辅挤出的关键,因此,研究气辅挤出离不开对气垫膜层的研究。实验研究表明,气体压力、气体温度和气垫层厚度对挤出成型过程和挤出物表面质量均有较大影响,如Fig.4和Fig.5所示(熔体压力为0.1 MPa,熔体温度为190℃),在其他工艺条件相同时,当气体压力和温度与熔体压力和温度接近时,较容易形成稳定的气垫膜层,此条件下挤出的产品表面质量最佳,在其他气体压力和温度范围内也能形成气垫膜层,但所形成的气垫膜层容易受外界因素影响而遭破坏,且挤出产品表面质量欠佳。
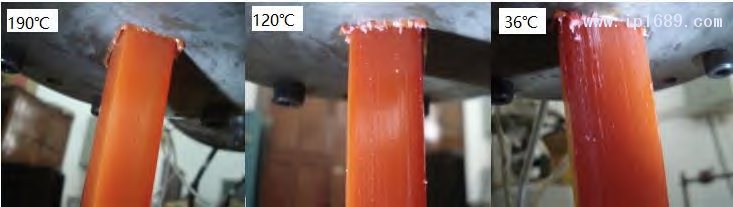
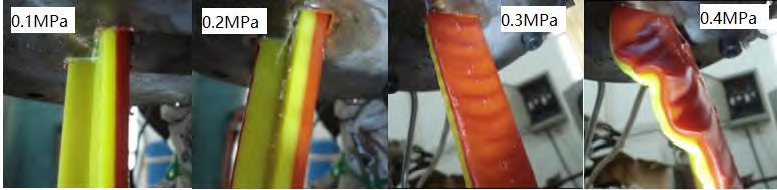
理论研究方面,早期的研究在构建描述气辅挤出流动行为的机理模型时,均将口模壁面与熔体表面间的气垫膜层简化成完全滑移边界条[13, 33],这无法从理论上揭示气垫膜层对聚合物挤出成型的影响机理。为从理论上分析气垫膜层对挤出成型的影响,邓小珍等[34, 35]将气体简化为广义牛顿流体作为独立流动层构建了L形截面异型材“气-液-液”共挤成型 三维黏弹机理模型,进行了较为全面的理论研究,并与将气体层简化为完全滑移边界条件 的理论研究结果进行了对比分析,结果表明,口模内气体入口设在两熔体汇合后3~5mm处可有效解决复合制品界面结合处容易产生气槽的问题;在形成稳定气垫膜层的气压范围内,较薄的气垫层厚、较小的气体压力和较大的熔体流率有利于保证复合制品尺寸精度和产品质量;将气垫层作为独立流动层和简化为完全滑移边界条件两种不同情况,其速度、压力、应力和温度等流场分布基本一致,但口模出口端面熔体边界形貌略有不同,结合实验验证结果,将气垫层作为独立流动层适合于气体工艺参数对挤出成型流场分布影响的研究,而研究气体辅助技术对熔体边界和层间界面形貌影响时,可将气体层简化成完全滑移边界条件构建机理模型。
任重等[36]基于气体的可压缩性,建立了方形截面型材“气-液”两相流模型,进行了非等温黏弹有限元分析,结果表明,气体压力对聚合物熔体挤出具有较大影响,气体压力越大,熔体的速度、压力、法向应力差和形貌收缩程度等均显著增大,因此,若为提高挤出产量,可适当增大气体压力,但为保证产品形貌和尺寸精度,在成功实现气辅挤出前提 下,应尽量降低气体压力。刘同科等[37-39]建立了内外双层气垫作用的“气-液-气”微管挤出机理模型,进行了有限元数值模拟和实验研究,研究结果表明,在口模出口处,由于外气垫层气体进入大气,瞬间减压,此时微管内层气压大于外层气压,因内气垫层气体对微管的挤压作用而产生的第一法向应力差使得微管壁厚变薄,管径增大,他们采用将内气垫 层压力先由小调大,再由大调小的方法快速形成微管内外双层稳定气垫膜,继而实现塑料微管尺寸的精确控制,罗成等[40]则采用在芯棒上开设排气孔的方法来解决微管离开口模后产生壁厚变薄和管径增大的问题。
江诗雨等[41, 42]运用理论和实验方法研究了4 mm×15mm片材水平方向气辅挤出过程中上下气垫膜层厚度对成型的影响,研究结果表明,片材上下层气垫膜采用不同的厚度(上层0.25 mm、下层0.75 mm)可改善口模出处口熔体容易下垂的现象,且当气体入口压力为0.1 MPa时,挤出质量最佳,片材扁平透明,此外,将气垫层作为独立流动层构建的“气-液”片材机理模型可很好的研究气垫层各工艺参数对熔体流场分布情况和挤出物轮廓的影响规律。
8 结束语
聚合物气辅挤出成型是21世纪初发展起来的一种新型加工方法,因其广泛的适应性、独特的加工优势和良好的发展前景,该技术受到聚合物加工领域研究者的广泛关注。国内外研究者对气辅挤出开展了大量的研究工作,取得了丰硕的究成果,前期研究工作主要集中在宏观尺寸的气辅单层挤出和双层共挤成型,近年来,随着微纳米科学技术的迅速发展,气辅挤出研究工作也逐渐向微挤出方向发展,现阶段的气辅挤出研究工作主要聚焦于医用微管的精密挤出成型及气垫膜层对挤出成型的影响机理,研究内容侧重于气体辅助技术对制品外观形貌和表面质量的影响,尚未涉及对制品微观结构和力学性能及光学性能的影响,这有望成为未来的研究趋势。
参考文献
[1] Anand J S, Bhardwaj I S. Die swell behaviour of polypropylene-an experimental investigation[J]. RheologicaActa, 1980,19: 614-622.
[2] Inn Y W, Fischer R J, Shaw M T. Visual observation of development of sharkskin melt fracture inpolybutadiene extrusion[J]. Rheologica Acta, 1998, 37: 537-582.
[3] Collyer A A, France G H. Extrudate distortion studies of polystyrene using an extrusion rheometer[J]. Journal of Materials Science, 1980, 15: 2945-2949.
[4] Takase M, Kihara S, Funatsu K. Three-dimensional viscoelastic numerical analysis of the encapsulation phenomena in coextruaion[J]. Rheologica Acta, 1998, 37: 624-634.
[5] Tzoganakis C, Perdikoulias J. Interfacial instabilities in coextrusion flows of low-density polyethylenes: experimental studies[J]. Polymer Engineering and Science, 2000, 40: 1056- 1064.
[6] Liu H S, Deng X Z, Huang Y B, et al. Three-dimensional viscoelastic simulation of the effect of wall slip on encapsulation in the coextrusion process[J]. Journal of Polymer Engineering, 2013, 33: 625-632.
[7] Ren Z, Huang X Y. 3D Numerical simulation of the hollow square-typed polymer based on gas-assisted extrusion method[J]. Materials Science Forum, 2016, 861: 189- 194.
[8] Graessley W W, Glasscock S D, Crawley R L. Die swell in molten polymers[J]. Journal of Rheology, 1970, 14: 519-526.
[9] 黄益宾. 聚合物气体辅助共挤成型的理论和实验研究[D].南昌: 南昌大学,2011.
[10] Brzoskowskit R, White J L, Szydlowski W, et al. Air-lubricated die for extrusion of rubber compounds[J].Rubber Chemistry and Technology, 1987, 60: 945-956.
[11] 黄兴元. 聚合物气体辅助口模挤出成型的理论及实验研究[D]. 南昌:南昌大学, 2006.
[12] 钱百年, 童玉清, 汪传生, 等. 气膜润滑剪切机头及其在短纤维增强胶管中的应用[J]. 橡胶工业, 1997,44(6): 323-326.
[13] Liang R F, Mackley M R. The gas-assisted extrusion of molten polyethylene[J]. Journal of Rheology, 2001,45: 211-226.
[14] 肖建华. 用于精密挤出成型的气辅挤出口模设计数值模拟和实验研究[D]. 南昌:南昌大学, 2008.
[15] 卢臣. 塑料异型材气辅挤出口模流动的理论与实验研究[D]. 南昌:南昌大学, 2007.
[16] 李萍. 聚合物气体辅助挤出成型工艺及数值模拟[D]. 哈尔滨: 哈尔滨理工大学,2010.
[17] 周国发, 周文彦, 胡晨章. 三维粘弹性异型材气辅挤出成型过程的数值模拟研究[J]. 塑性工程学报,2008, 15(5): 198-203.
[18] Ren Z, Huang X Y, Liu H S. 3D Numerical study on the hollow profile polymer extrusion forming based on the gas-assisted technique[C]//IOP Conference Series: Materials Science and Engineering.Hangzhou: IOP Publishing, 2016, 137: 012007.
[19] Yin H N, Huang X Y, Liu T K, et al. Effects of gas-assisted extrusion on slip in the cable coating process[J].Journal of Polymer Engineering, 2021, 41: 329-337.
[20] 邓小珍. 塑料异型材气体辅助共挤出成型的实验和理论研究[D]. 南昌:南昌大学,2014.
[21]陈璐璐. Y 型截面塑料异型材气辅共挤成型的数值模拟和实验研究[D]. 南昌:南昌大学, 2016.
[22] 邓小珍, 柳和生, 黄兴元, 等. 气体辅助工艺对曲线型异型材共挤成型的影响[J]. 高分子材料科学与工 程, 2015, 31(11): 119- 123.
[23]黄楚晔. 气辅微管挤出数值模拟与模具设计[D]. 南昌:南昌大学, 2016.
[24] Ren Z, Huang X Y, Xiong Z H. Experimental and numerical studies for the gas-assisted extrusion forming of polypropylene micro-tube[J]. International Journal of Material Forming, 2020, 13: 235-256.
[25] 任重, 黄兴元, 柳和生. 塑料微管气辅挤出成型实验与机理分析[J]. 材料导报, 2020, 34(10): 20193-20198.
[26]任重. 塑料微管气辅挤出成型理论及实验研究[D]. 南昌:南昌大学, 2017.
[27] Ren Z. Numerical simulation of gas-assisted extrusion of four-lumen micro-catheter based on fem method[C]//Journal of Physics: Conference Series. IOP Publishing, 2020, 1622: 012050.
[28]李福成. 异型医用多腔导管挤出离模膨胀变形机理与调控[D]. 南昌:南昌大学, 2020.
[29]陈思维. 医用级 TPU 的气辅微挤出成型过程研究[D]. 南昌:南昌航空大学, 2017.
[30]周友明. 医用导管的气辅微挤出成型工艺研究[D]. 南昌:南昌航空大学,2017.
[31] Wang L, Huang X, Zhao J X, et al. Production of high-aspect-ratio rectangular-lumen microtube by gas-assisted microextrusion[J]. Journal ofApplied Polymer Science, 2020, 137: 49352.
[32]王嫘. 聚合物矩形通道微管挤出成型及加工工艺研究[D]. 杭州:浙江大学,2020.
[33] Arda D R, Mackley M R. Sharkskin instabilities and the effect of slip from gas-assisted extrusion[J].Rheologica Acta, 2005, 44: 352-359.
[34] 邓小珍, 柳和生, 黄益宾, 等. 气辅共挤精密成型中 2 种方法处理气体层的比较[J]. 中南大学学报(自 然科学版) , 2016, 47(7): 2227-2234.
[35] Deng X Z, Liu H S. Three-dimensional viscoelastic numerical analysis of the effects of gas flow on L- profiled polymers[J]. Journal of Polymer Engineering, 2018, 38: 503-512.
[36] Ren Z, Huang X Y, Liu H S, et al. Numerical and experimental studies for gas assisted extrusion forming of molten polypropylene[J]. Journal of Applied Polymer Science, 2015, 132: 42682.
[37] Liu T K, Huang X Y, Luo C, et al. The formation mechanism of the double gas layer in gas-assisted extrusion and its influence on plastic micro-tube formation[J]. Polymers, 2020, 12: 1- 17.
[38] 刘同科, 黄兴元, 柳和生, 等. 塑料微管气辅挤出中内气垫层气体的影响[J]. 高分子材料科学与工程,2020, 36(4): 75-86.
[39] Liu T K, Huang X Y, Ren Z, et al. Analysis of superimposed influence of double layer gas flow on gas-assisted extrusion of plastic micro-tube[J]. International. Polymer Processing, 2020, 2: 158- 168.
[40] Luo C, Huang X Y, Liu T K, et al. Research on inner gas inflation improvements in double-layer gas-assisted extrusion of micro-tubes[J]. Polymers, 2020, 12: 1- 17.
[41] Jiang S Y, Liu H S, Huang X Y, et al. Numerical and experimental studies on the effect of thicknessdifference between up and down gas layers on sheet polymer gas-assisted extrusion forming[J]. PolymerEngineering and Science, 2020, 60: 2470-2486.
[42] Jiang S Y, Liu H S, Huang X Y, et al. Improved die assembly for gas-assisted sheet extrusin using different up and down gas layer thicknesses[J]. Polymer Engineering and Science, 2021, 61: 1546- 1558.