郭 超
(秦皇岛威卡威汽车零部件有限公司,河北 秦皇岛 066000)
摘 要:【目的】提高汽车行李架加工效率,设计一种机器人自动上下料装置。【方法】通过研究机器人自动上下料工艺流程,对机器人自动上下料装置进行了整体设计。【结果】机器人自动上下料装置利用储料式传送带集中供料,对零件进行传送、分离、检测后,机器人抓取和搬运,完成上料操作,将成品有序地放在下料车中,完成码垛操作。【结论】采用工业机器人替代工人进行上下料操作,车间生产状态从一人操作一台设备变成一人操作多台设备,可降低人力成本,提高企业生产效率。
关键词:工业机器人;自动上下料;汽车行李架;RobotStudio仿真;一键复位
汽车行李架是安装在汽车车顶上的支架,用于携带大件物品,如自行车、大件行李、帐篷等,增加了爱车的承载空间,成为越来越多的车主喜欢选装的部件[1]。行李架的材质多为铝合金材料,有着较高的强度和硬度,在机加工成型的工序中,需要工人不断重复单一的上下料操作进行生产,劳动强度大,消耗大量的人力成本,生产效率低。汽车行李架图如图 1所示。
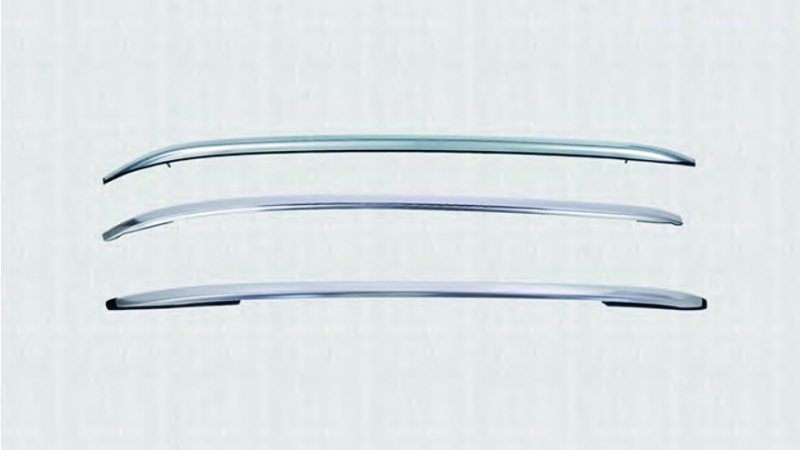
图1 汽车行李架图
机器人技术是机械、电子、自动控制、人工智能等多学科领域知识交叉和融合的一门新兴交叉学科[2]。近年来,工业机器人的技术水平持续提升,其凭借操作灵活、占地面积小、精度高和成本低等优势,被广泛应用在汽车制造、电子工业等领域[3]。汽车行李架机加工工序采用 PLC+HMI 架构设计,进行程序逻辑控制,采集传感器的输入,控制伺服、气缸等执行机构的输出,通过工业机器人模拟工人的上下料动作,可实现行李架的自动抓取、搬运、下料码垛操作,将员工从重复和单一的工作中解放出来,有效降低了员工的劳动强度,改善了员工的作业环境,可提高企业生产效率,为促进工厂的智能化和自动化发挥了重要作用[4]。
1 机器人自动上下料工艺流程
工艺流程图如图2所示。1)将待加工的零件集中放在上料传送带的隔断内,伺服系统通过以太网连接PLC,按照人机界面上预先设定的参数配方,以位置控制模式带动传送带向机器人方向转动。2)当传送带终端的红外测距传感器检测到零件时,尼龙材质的符形块托起零件,利用零件本身的重力作用,在垂直方向对零件进行位置校正,安装弹簧缓冲机构的气缸侧推工作,在水平方向对零件进行二次定位校正,3D激光传感器对零件侧面进行轮廓扫描,判断零件是否上错、放反,保证上料位置一致性,提高机器人自动上下料装置的稳定性。3)PLC通过射频识别技术读取机器人夹具上面的电子标签,采集工装产品信息,转换成数字产品代码后,通过网络将代码发送给机器人,用来自动调用机器人的运动轨迹任务,当传感器检测零件合格时,上料单元启动机器人。4)机器人将待加工的零件放置在加工设备的上料位置,取走已加工完成的零件,同时启动设备工作,按照码垛程序的控制算法,将零件有序地放入下料小车对应位置。5)MES系统对PLC进行数据采集和信号连接,利用智能算法进行生产、设备、质量数据分析,并自动生成表格和图形,以便进行可视化管理[5]。
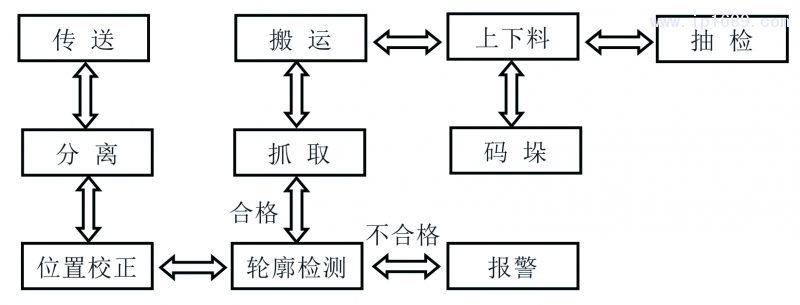
图2 工艺流程图
为提高设备利用率,机器人自动上下料装置设计三个功能。1)抽检不停机功能。由于下料车被安全护网围在内部,质检员在护网外部接触不到零件,若进入护网内部取件,需要设备停机,以保护人员安全,但会降低设备生产效率。抽检功能只需要员工触发抽检按钮,机器人自动将加工完成的零件放在下料传送带上,传出防护网外。2)换车不停机功能。当下料车码垛装满时,蜂鸣器报警,设备继续进行生产,机器人自动切换下料轨迹,将零件放在下料传送带上,换车完成后,员工触发启动按钮,机器人自动切换到下料车码垛轨迹。3)机器人一键复位功能。当设备出现故障停机时,若机器人没有停在待机起始位置,以往需要员工手动操作示教器来复位机器人,步骤繁琐,对员工技能要求高,一键复位功能可以通过按住复位按钮,机器人自动调用复位程序,判断停止位置,规划复位轨迹,回到待机位置,操作简单方便。
2 整体系统设计
机器人自动上下料装置分为主体设备和产品工装两部分,通过更换产品工装,主体设备可以实现对不同规格零件的加工,以此适应市场上产品多样化和个性化的需求。主体设备由工业机器人、上料单元、下料单元、电控系统四部分组成,设备实际效果图如图3所示。
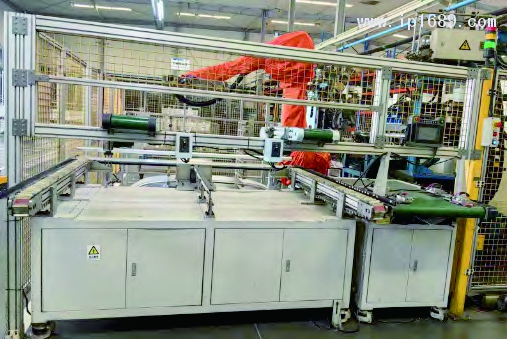
图3 设备实际效果图
2.1 工业机器人选型
工业机器人在自动上下料装置中的主要应用为搬运和码垛操作,选型的依据和重点是动作范围、有效负载和重复定位精度。IRB 4600-40/2.55 是 ABB公司开发的高效通用型机器人,装配性能优异的IRBP变位机和IRBT轨迹运动系统,增强了机器人对目标应用的适应能力,纤巧的机身使其在避绕障碍物时,可以保持最高加速度,循环周期时间短。IRB 4600的规格参数如表1所示。
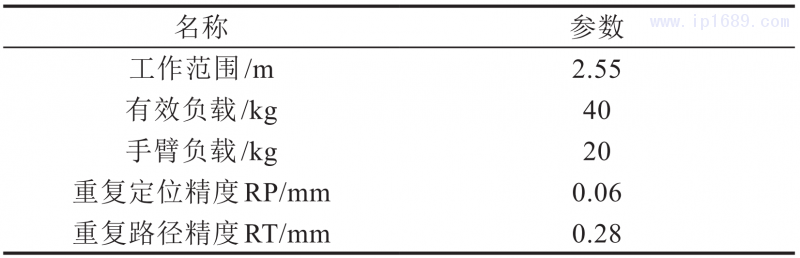
表1 IRB 4600的规格参数
2.2上料单元设计
上料单元设计采用储料式传送带的形式,集中供料,可以满足50件待加工零件的同时摆放,皮带上的横条用于隔断相邻的两个零件,便于零件的分离操作,皮带支架固定在花轴上,通过轴承在花轴上的移动,调节两侧支架的间隔,使上料单元可以兼容长度在1.8 m~2.8 m范围内的零件,利用传送带两侧的导向板,对移动的零件进行左右方向校正,降低人工零件摆放的位置精度要求。下料传送带固定在上料单元的上方,用于抽检和换车下料,上下料在一侧的设计,可以有效减少员工的频繁走动,下料传送带的皮带电机为220 V调速电机,通过旋转调速旋钮可以控制皮带转速,防止速度过快,导致成品件堆放,造成零件表面磕碰划伤。
2.3 下料单元设计
下料单元由下料小车和小车固定机构两部分组成,由于不同型号的汽车行李架形状相似,所以下料小车设计成通用形式,即不同型号的行李架共用一种下料车,可以降低产品的生产成本。小车的车身结构是方钢焊接成型,结构简单,牢固耐用,使用耐磨的布料包裹车身,防止小车运输零件时产生划伤。小车固定机构具有导向、定位和锁死功能,利用电容式传感器检测下料小车的摆放位置,保证每次换车操作后,下料车位置的一致性。
2.4 电控系统设计
选用罗克韦尔1769-L30ERM型号的CPU作为电控系统的PLC,进行程序控制、信号采集、数据处理和故障诊断;选用罗克韦尔2711P-T6C21D8S型号的触摸屏作为人机界面,用于设定伺服参数、手动操作HMI上的虚拟按钮、显示设备报警[6];选用易福门AC1421型号的以太网IP网关配置AS-i从站,控制分布式I/O,与行李架加工设备进行通信,采集传感器输入,控制电机和气缸等执行器机构输出;选用罗克韦尔Kinetix350型号的单轴驱动器控制伺服电机工作,驱动器与电机间用两根电机线相连接,红色的电机线提供电源,绿色的电机线传递电机编码器信号,PLC执行MAM控制命令,使伺服电机按设定的绝对位置转动,每当上料传送带旋转一周时,伺服电机的位置值自动归零,防止出现累计误差;选用易福门ANT513型号的RFID读写头,识别机器人夹具上的E80371型号的RFID标签,标签里写有当前工装的ID信息,PLC将其与切换工装时选择的产品信息做比较,以验证当前工装是否配方选择错误,同时将产品代码传送给机器人,机器人利用TEST语法结构来选择当前产品对应的上下料程序[7];利用MES系统对PLC进行设备产量、运行时间、异常报警等数据采集,通过智能算法的逻辑计算,转换成可视的图形和报表,进行监控和管理[8]。开通ABB机器人EtherNet/IP通信协议,将机器人的EDS文件通过Studio5000软件导入PLC中,使PLC与机器人建立硬件组态,实现32个字节长度的以太网通信;开通ABB机器人DeviceNet协议,使用DSQC652型号信号板连接机器人夹具I/O信号,控制真空吸盘和气缸夹爪动作。硬件网络图如图4所示。
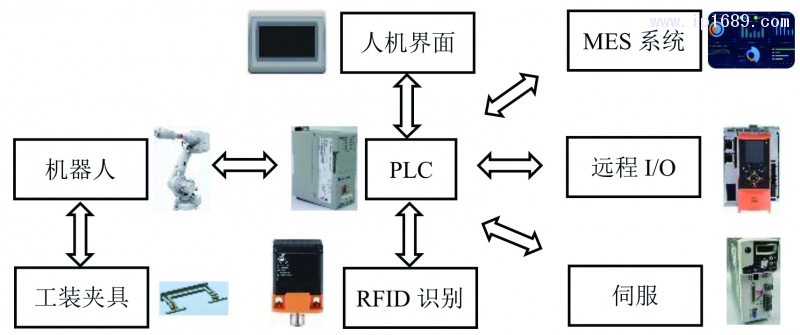
图4 硬件网络图
2.5工装夹具设计
通用型工装夹具可靠性低,夹持精度不高,影响行李架上料稳定性,所以将上料传送带的定位机构和机器人夹具设计成专用型工装,不同型号的行李架需要开发对应形状和尺寸的工装[9]。定位机构有零件分离、位置校正、轮廓检测功能,是通过水平和垂直方向的气缸运动,以及3D激光轮廓传感器检测来实现的。机器人夹具结构简单,使用定位销和螺丝与机器人六轴法兰相连接,降低工装硬件成本,夹具的执行机构由真空吸盘和气爪组成,利用真空发生器产生真空压力,将行李架吸附在夹具上,利用气爪运动,锁紧行李架位置[10]。
3机器人程序开发
3.1机器人轨迹仿真
机器人仿真图如图 5 所示。机器人程序开发有手动示教和离线仿真两种方式,手动示教是在现场环境,手持示教器操作机器人移动,记录轨迹位置、编写逻辑;离线仿真是在软件里建模,模拟机器人工作,编写动作程序。机器人自动上下料装置利用ABB公司开发的RobotStudio软件对其进行离线仿真[11]。1)创建一个空的工作站,在模型库中选择IRB 4600-40/2.55机器人模型,并将其导入工作站中。2)选择“从布局”方式创建机器人系统,设置机器人的RobotWare的版本,配置系统参数,如添加840-1 EtherNet/IP Anybus Adapter、608-1 World Zones、617-1 FlexPendant Interface等功能。3)将SolidWorks软件设计的上下料主体设备和产品数模,以stp格式几何体导入系统中,按照设计布局,摆放各装置的位置。4)定义工具数据,将机器人夹具的质量和重心位置等参数保存在tooldata中,定义负荷数据,将行李架质量和重心保存在loaddata中,分别在上料传送带、加工设备和下料小车三个位置定义工件坐标,保存在wobjdata中。5)将机器人运动曲线生成轨迹指令,配置轴参数,仿真运行机器人的上下料操作,检测机器人是否发生碰撞[12]。

图5 机器人仿真图
3.2机器人一键复位程序开发
现场异常触发机器人故障停机,需要设备具有一键复位功能,快速恢复正常生产。创建初始化程序rinit(),并添加在主程序main()中,删除中断连接,将中断字符int_Home和中断程序Return_to_home相关联,将输入信号Home_Button与中断字符int_Home相关联,当按住Home_Button按钮时,触发中断程序执行。机器人停止移动,获取机器人当前位置,并保存到变量P_Home中,清除真空吸盘工作指令,清除气爪工作指令,机器人放下夹具中的零件,在x方向以直线运动指令移动-100距离,在y方向和z方向保持不变,用于安全避让,然后回到Home位置,机器人停止。机器人自动复位程序图如图6所示。
4结语
利用上料单元对加工零件进行存储、传送、分离、定位、检测,IRB4600工业机器人抓取和搬运零件进行上下料操作,在下料单元进行有序的码垛操作,完成成品存储,设计出一种用于汽车行李架加工的机器人自动上下料装置。通过RobotStudio软件对机器人动作进行虚拟仿真,简化开发和设计流程,通过机器人一键复位功能,降低设备操作复杂度。采用工业机器人替代工人进行上下料操作,车间生产状态从一人操作一台设备变成一人操作多台设备,可降低人力成本,提高生产效率,为增强企业竞争力提供了可靠支持。
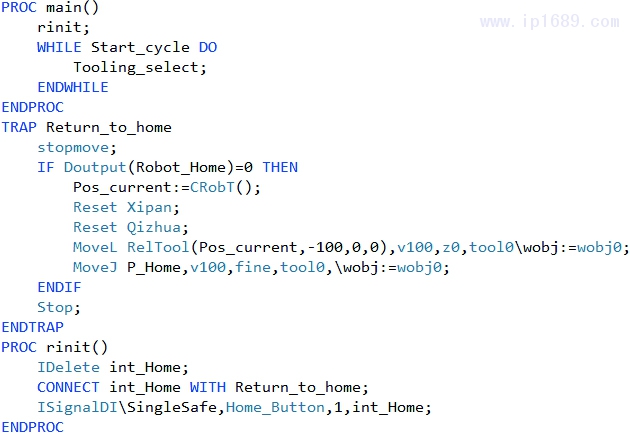
图6 机器人自动复位程序图
参考文献:
[1] 王亚运,杨杰.用于汽车行李架的一体式嵌件螺母[J].汽车与配件,2021(17):67-69.
[2] 胡艳琳.基于PLC控制的物料检测分类放置工业机器人系统研究与设计[D].河北:河北科技大学,2020:1-7.
[3] 郭文豪. 基于等离子堆焊机器人工艺过程的动力学研究[D].辽宁:沈阳工业大学,2022:43-44.
[4] 王晓燕.基于PLC的液晶玻璃基板自动上料控制系统 [J].兵器装备工程学报,2020,41(9):176-181.
[5] 廖能解,马平,欧建国,等.上下料桁架机器人控制系统设计[J].机械设计与制造,2020(12):171-175.
[6] 刘恒超.基于AB PLC和工业机器人的汽车天窗自动排序上料系统设计[J].制造业自动化,2022,44(12):102-106.
[7] 杨亚,范琳琳.RFID 技术在 PLC自动化系统中的集成应用[J].工业控制计算机,2022,35(11):10-12.
[8] 张明月,贺福强,李思佳,等.基于MES系统的印刷工艺能耗管控研究[J].制造业自动化.2023,45(5):36-39.
[9] 鲁霞,吴卓明.一种工业机器人多功能夹具[J].机床与液压,2020,48(1):113-115.
[10] 杨昆,王艳春,郭湖东,等.面向3C自动化生产线的装配工业机器人多功能组合夹具设计[J].科学技术创新,2019(29):105-106.
[11] 樊琛,朱致远,颜远远.基于RobotStudio的分类码垛工作站仿真研究[J].制造业自动化,2023,45(7):61-66.
[12] 赵伟博,李琳杰,齐锴亮. 基于RobotStudio的机器人上下料工作站设计与仿真 [J].计算技术与自动化,2021,40(4):21-25.