张维合1,邓成林2,闫丽静1,胥永林1,冯婧1
(1.广东科技学院,广东,东莞523000;2.东莞市模人科技有限公司,广东,东莞523000)
摘要:根据汽车后大灯镜壳的结构特点,设计了一副大型薄壁精密注塑模具。模具采用定模成型内表面、动模成型外表面及动模侧向抽芯机构,有效地解决了成型塑件脱模困难问题;模具采用三级定位机构,显著提高了模具刚度和寿命;模具采用随形水路温度控制系统,成型周期降低了10%,成型塑件最大变形量下降了20%,成型塑件的尺寸精度达到了设计要求的MT3;模具采用推杆先复位机构,有效地消除了滑块和推杆汽相撞的风险,保证了侧向抽芯机构安全可靠。模具投产后运行平稳,成型塑件尺寸稳定。
关键词:汽车后大灯镜壳;大型薄壁精密注塑模具;三级定位机构;随形水路;侧向抽芯机构;先复位机构
汽车车灯的主要作用是照明。因此,汽车车灯外观要求较高,从而对模具设计与制造要求也较高。组成汽车前后车灯的主要零件均为塑料零件,包括左右透镜、左右装饰框、左右镜壳和左右反射镜等。其中,镜壳结构复杂,精度较高,为解决模具和塑件在注射成型过程中存在的问题,文章结合同类型车型后大灯镜壳注塑模具进行优化设计。
1塑件外观要求与结构
图1为广州本田某款SUV汽车右后大灯镜壳零件图,除了灯头孔以外,左后大灯镜壳与其对称。镜壳材料为PP+TD20,其中,聚丙烯PP为镜壳的基体,TD为添加剂滑石粉,TD20表示滑石粉添加量为20%,滑石粉能提高镜壳的刚度[1-2]。塑件的最大外形尺寸为475.3 mm×355.6 mm×291.4 mm、平均壁厚为2 mm,灯头孔和后盖孔装配精度较高,尺寸精度为MT3(GB/T 14486—2008),属于大型薄壁精密塑件;镜壳外形和内形均较复杂,当分型面选择不合适时,成型塑件有粘定模的风险;镜壳外侧面有6处倒扣,侧向抽芯结构复杂;塑件外观面不允许有斑点、收缩凹陷、熔接痕和飞边等成型缺陷。

图1汽车右后大灯镜壳零件图(单位:mm)
(a)主视图(b)侧视图(c)立体图
S1~S6-侧向抽芯机构
2模具结构设计
2.1成型零件设计
根据镜壳的结构特点,为保证塑件开模后留在动模中,采用定模成型内表面,动模成型外表面。模具采用一体式结构,模具的定模A板为定模成型零件,动模B板为动模成型零件。该设置具有结构紧凑、刚度较好、模具体积较小的特点,同时减少了开框、配框和制造斜楔等复杂的工序。
汽车后大灯镜壳内外侧均较为复杂,为解决塑件容易粘定模或拖伤的问题,采用定模成型内表面,动模成型外表面;定模型腔的脱模斜度设置为3°,动模型腔的脱模斜度设置为1°[3];在塑件不允许大脱模斜度内侧面对应的外侧面设计倒扣纹,倒扣纹深度在0.5~1 mm范围内,倒扣纹设计在靠近塑件的圆角处[4]。
灯头孔的尺寸精度较高,灯头孔的拔模斜度须在0.5°以内,否则影响灯座与灯头孔的装配精度。后大灯镜壳塑件加强筋及模具镶件较多,为有利于装拆,所有镶件均采用冬菇头定位,螺钉全部从正面旋入,在影响成型面处采用黄铜堵头。
汽车后大灯镜壳注塑模具分型面形状复杂,分型面必须平顺光滑,不能有尖角锐边等薄弱易损结构。这样的分型面既有利于加工,又能有效地提高模具寿命。汽车后大灯镜壳注塑模具分型面封胶宽度为40 mm,分型面以外的区域避空1 mm。在大面积的避空处设计了8块承压块,保证模具受力均匀,避免了模具长期生产后变形。
模具定模成型零件采用P20模具钢,动模成型零件采用718模具钢,这是由于,不同的模具钢在摩擦时不易由于高温产生粘连烧结[5-6]。
2.2浇注系统设计
成型塑件尺寸较大,结构复杂,熔体填充阻力较大,为保证成型质量,浇注系统采用两点开放式热流道,进胶点直接设计在塑件内表面,可以使料流速度较快,注塑周期较短,保证成型质量较好。由于镜壳为非外观件,表面的进胶痕迹不影响外观。模具的热流道浇注系统由接线盒、一级热射嘴、二级热射嘴和热流道板组成,如图2所示。为解决针对同类型车型镜壳成型过程中易出现热嘴流延、拉丝及浇口残留过高的问题,在热嘴区域及热嘴正对面的动模区域单独设计了1条冷却水道,以上问题均得到了解决[8]。

图2模具热流道浇注系统
2.3侧向抽芯机构设计
一模成型后,大灯左右2个镜壳塑件,每个塑件均有6个倒扣,6个倒扣均在塑件外侧,模具均采用了“动模滑块+斜导柱+定位夹”的侧向抽芯机构,该结构加工方便,抽芯动作安全稳定,定位可靠[9-10]。后大灯右镜壳的6个侧向抽芯机构分别为S1、S2、S3、S4、S5和S6,后大灯左镜壳的6个侧向抽芯机构分别为S1″、S2″、S3″、S4″、S5″和S6″。每个侧向抽芯机构均由成型零件滑块、驱动零件斜导柱、定位零件定位夹、限位块及辅助零件斜导柱固定块和耐磨块组成,如图3所示。
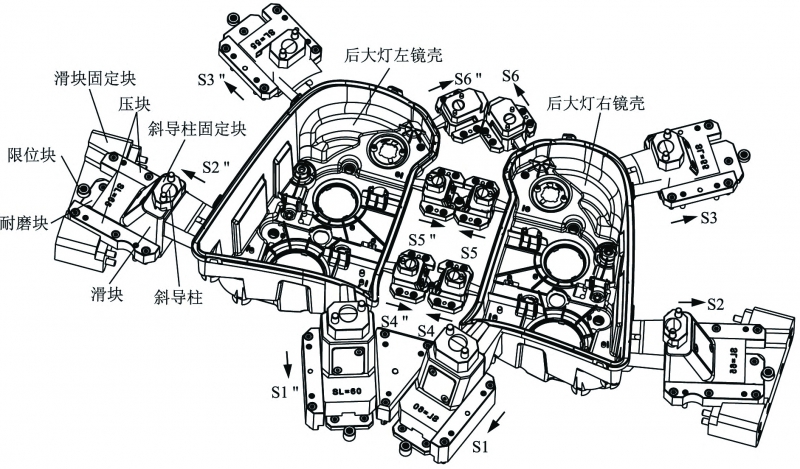
图3汽车后大灯镜壳模具侧向抽芯机构立体图
S1~S6-右镜壳侧向抽芯机构S1″~S6″-左镜壳侧向抽芯机构
2.4温度控制系统设计
镜壳外形落差较大,模具采用了“垂直式水管+倾斜式水管+隔片式水井”随形水路的组合式温度控制系统,如图4所示。定模设计了4组循环水路,动模设计了5组循环水路,冷却水道距离型腔面必须基本相等,约为水道直径的4~5倍(50~60 mm)。2个热射嘴附近温度较高,模具均单独设计了1组冷却水路,有利于散热[11]。定、动模冷却回路形成了互相交叉网状结构,冷却面积约为塑件面积的60%。水路设计均匀合理,模具型腔冷却快速均衡,显著提高了模具的生产效率和塑件的成型精度,成功将注塑周期控制在40 s之内,与同类型镜壳注塑模具相比,缩短了约10%,成型塑件最大变形量下降了20%,尺寸精度达到了MT3。
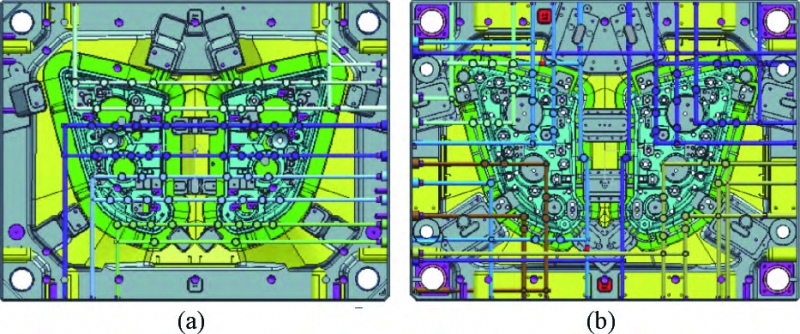
图4注塑模具温度控制系统
(a)定模冷却系统(b)动模冷却系统
2.5脱模系统及先复位机构设计
汽车后大灯镜壳模具脱模机构采用“推杆+推管”结构形式,模具在定、动模开模与侧向机构抽芯后,依靠模具推出系统推出塑件,推件固定板由注塑机通过KO孔机械推动和在4支复位杆的作用下复位[12]。汽车后大灯镜壳注塑模具脱模系统如图5所示。
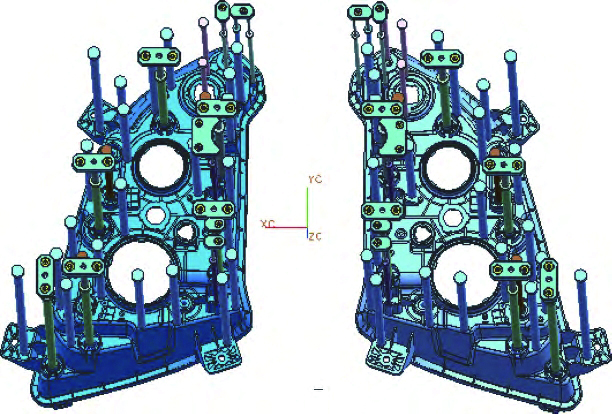
图5汽车后大灯镜壳注塑模具脱模系统
由图2e中C-C剖视图可知,模具S2和S2″的滑块35下为推杆40,为防止合模时推杆40由于复位较差,导致滑块和推杆相撞,模具设计了4个推杆先复位机构:在4根复位杆固定端的下方各设计1块20 mm×20 mm的弹力胶,如图6所示。复位杆固定板的大头孔比复位杆固定端深3 mm,开模后,由于弹力胶作用复位杆比推件向前多推出3 mm,可以缩短合模时复位杆和定模A板接触时间,将推件固定板和推件提前推回复位,达到推出零件先复位的目的。
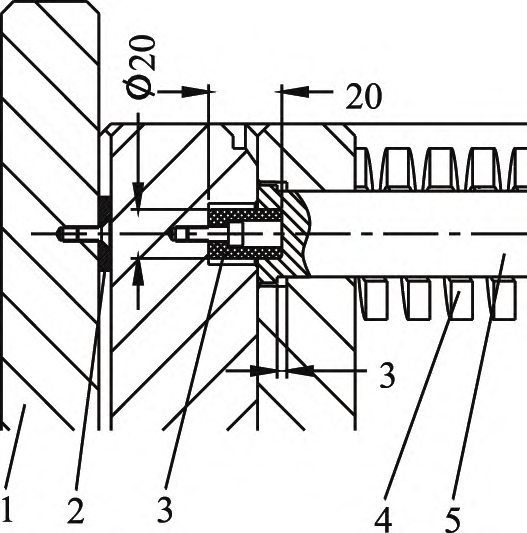
图6模具先复位机构(单位:mm)
1-动模固定板2-垃圾钉3-先复位弹力胶4-复位弹簧5-复位杆
复位弹簧虽然具有先复位功能,但是,容易疲劳失效,在推杆必须先复位的情况下,仅依靠复位弹簧不可靠[13]。另外,塑件灯头孔与左右转向灯头装配时需要增加密封圈,而且密封效果要求较高,因此,该区域不能设计推杆,避免影响密封性。
2.6模具排气系统设计
汽车后大灯镜壳尺寸较大、结构复杂,客户反映其他类型汽车后大灯镜壳注塑模具常出现填充不满、困气、脱模不顺利等注塑缺陷,严重时产品分型面处还会出现烧焦痕迹,这些均为排气系统设计不合理造成的[14]。因此,对排气系统进行了充分分析,在一级排气槽位置和数量设计方面进行了改善,将排气槽主要开设在动模分型面上,并且采用数控铣床加工,如图7所示。

图7模具排气系统
2.7导向定位系统设计
模具在4个角上各设计了1支60 mm×450 mm圆导柱,导柱安装在定模侧,如图8所示。由于塑件开模后留在动模侧,导柱不影响塑件取出,同时避免了塑件图粘到导柱上的油污。定模导柱在翻模时还可作为支撑脚使用,便于制造。导柱的长度必须在斜导柱插入滑块前20 mm时插入导套,保证侧向抽芯机构顺利复位。另外,导柱最大长度不宜超过其直径的10倍[15]。
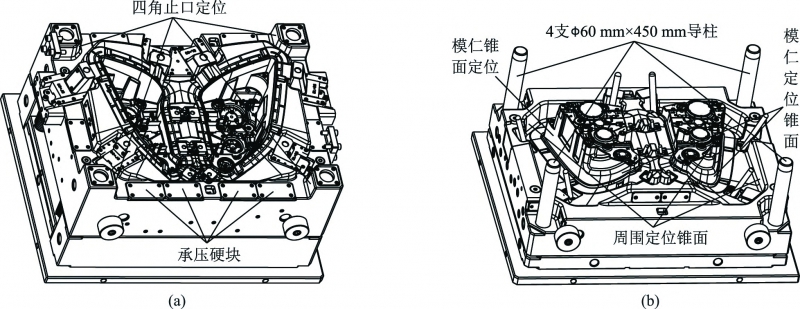
图8汽车后大灯镜壳注塑模具立体图
(a)动模立体图(b)定模立体图
结合汽车后大灯镜壳在生产中外观面存在拖伤现象,模具设计采用三级定位机构,其中,导柱导套为一级定位机构,由于导柱导套之间采用间隙配合H7/f6,在合模时具有初步定位作用,其主要具有导向作用。模具二级定位机构为模具动模板和定模板的锥面止口,包括4个角上的8个锥面定位面及四面围边式的定动模互锁定位,二级定位主要为模架的定位,定位精度远高于导柱导套的定位,对于精密模具与汽车模具而言,二级定位是模具的主要定位结构。三级定位机构是模仁分型面上的精准锥面止口,主要保护模具插穿面,同时也承受侧向注射压力。二级定位面和三级定位面锥度一般取值在3°~8°范围内,止口高度设计与模仁最高面相比,高出了5~10 mm。止口定位面需设为面对面,实现互锁,避免模具向一侧倾斜打滑。模具三级定位机构保证了动定模精准定位,显著提高了成型塑件的精度、模具的刚度和生产寿命。
3模具工作过程
模具最大外形尺寸为1 200 mm×950 mm×820mm,总重量约为8 t,属于大型注塑模具。模具平面结构如图9所示。
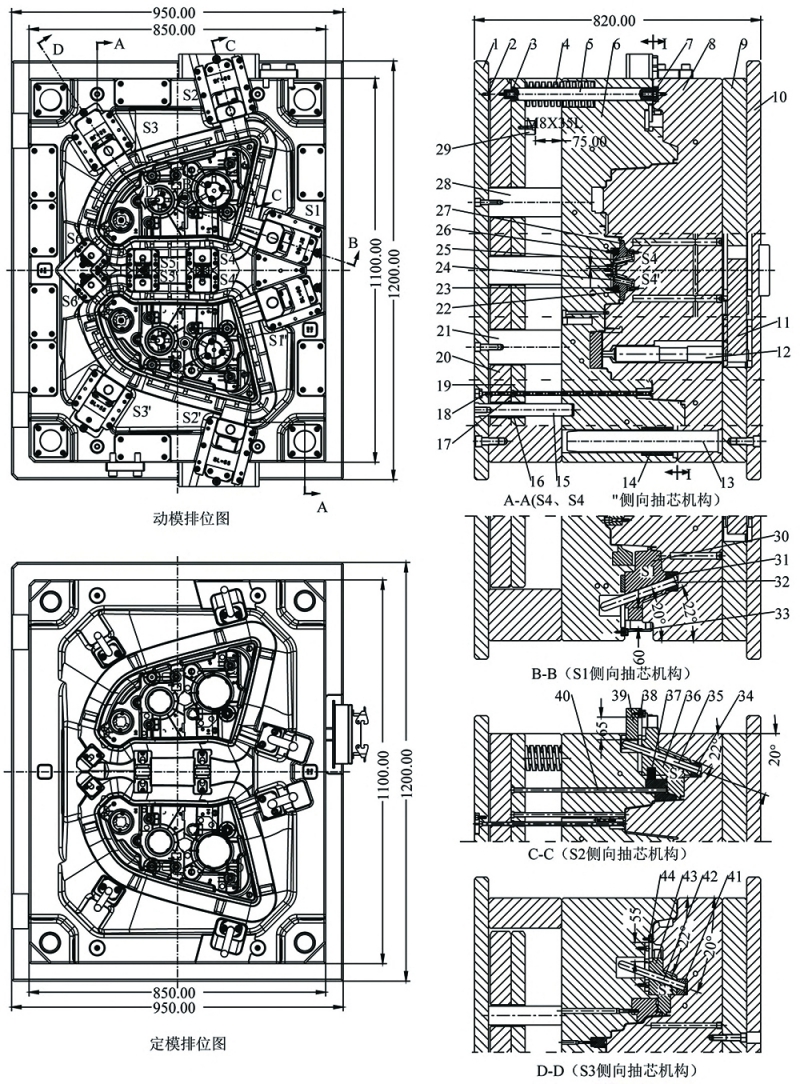
图9汽车后大灯镜壳注塑模具结构图(单位:mm)
1-动模固定板2-垃圾钉3-先复位弹力胶4-复位弹簧5-复位杆6-动模板7-硬块8-定模板9-框板10-定模固定板11-热流道板12-热射嘴13-导柱14-导套15-推件板导柱16-推件板导套17-推管18-芯型19-推件固定板20-推件底板21-撑柱22-滑块23-弹簧24-斜导柱25-斜导柱26-弹簧27-滑块28-撑柱29-限位柱30-滑块31-斜导柱固定块32-斜导柱33-斜导柱固定块34-斜导柱35-滑块36-弹簧37-滑块限位柱38-导向块39-滑块限位柱40-推杆41-斜导柱固定块42-斜导柱43-滑块44-滑块限位柱
PP+TD20熔体经热流道浇注系统进入模具型腔,熔体充满型腔后,经保压、冷却及固化至足够刚性后,注塑机拉动模具的动模固定板1,模具从分型面Ⅰ处开模,动、定模开模距离500 mm,由注塑机控制。在开模过程中,12个滑块在12支斜导柱的驱动下进行侧向抽芯,S1和S1″的抽芯距离为60 mm,S2和S2″的抽芯距离为65 mm,S3和S3″的抽芯距离为55 mm,S4、S5、S6、S4″、S5″和S6″的抽芯距离为6 mm。抽芯距离由挡销和定位夹控制。完成开模行程后,注塑机顶棍推动推件底板20、推件固定板19以及所有推杆、推管,将成型塑件推离动模。塑件顶出75 mm后,由限位柱29控制。成型塑件由机械手取出后,注塑机推动动模合模,在复位弹簧4和弹力胶3作用下,推件及其固定板提前复位,模具进行下一次注射成型。
4结论
(1)模具采用定模成型内表面、动模成型外表面及动模侧向抽芯机构,不但有效地解决了成型塑件脱模困难的问题,而且显著简化了模具的侧向抽芯机构。
(2)模具采用三级定位机构,显著提高了模具刚度和寿命,模具采用随形水路温度控制系统,成型周期降低了10%,成型塑件最大变形量下降了20%,成型塑件的尺寸精度达到了设计要求的MT3。
(3)模具采用弹力胶推杆先复位机构,消除了滑块和推杆相撞的风险,保证了侧向抽芯机构安全可靠。模具第一次试模成功,投产后运行平稳,成型塑件尺寸稳定。该车型装车效果较好,该款车型车灯在车展中得到了广泛认可与好评,为客户创造了较好的经济效益。
参考文献:
[1]张维合.注射模具设计实用手册[M].北京:化学工业出版社,2011.
[2]张维合.汽车注塑模具设计要点与实例[M].北京:化学工业出版社,2016.
[3]张维合.基于顺序阀热流道技术汽车导流板注射模设计[J].塑料科技,2018,46(12):100-105.
[4]万鹏程.汽车保险杠注射模浇注系统设计与成型参数优化[M].昆明:昆明理工大学出版社,2011.
[5]沈忠良,郑子军,肖国华,等.汽车中控面板IMD成组模具设计[J].工程塑料应用,2017,45(1):70-75.
[6]张维合.汽车中央装饰件顺序阀热流道二次顶出注塑模设计[J].工程塑料应用,2018,46(7):87-91.
[7]吴梦陵.Moldflow模具分析实用教程[M].2版.北京:电子工业出版社,2018.
[8]刘彦国.塑料成型工艺与模具设计[M].4版.北京:人民邮电出版社,2018.
[9]周纪委,王明伟,吴迪,等.汽车尾门左右窗框饰板气辅注塑模具设计[J].中国塑料,2023,37(11):141-148.
[10]张云,熊建武,夏凯,等.汽车通风管接头注塑模具设计[J].塑料,2023,52(5):74-78.
[11]刘祥建,周佳睿,姜劲.基于Moldflow的按钮开关帽注塑模具设计[J].工程塑料应用,2023(6):1-6.
[12]REN J W,WU C,LIU H H,et al.A collaboration navigation system for concurente mold design[J].The International Journal of Advanced Manufacturing Technology,2009,40(3/4):215-225.
[13]TSAI C C,LU C H.Multivariable self-tuning temperature control for plastic injection molding process[J].Industry Applications IEEE Transactions on,1998,34(2):310-318.
[14]LI C G,WU Y.Evolutionary optimization of plastic injection mould cooling system layout design[C]//International conference on intelligent system design&engineering application.IEEE Computer Society,2010.
[15]张维合.汽车后背门护板热流道大型注塑模设计[J].中国塑料,2019,33(5):102-108.