陈如香,雷乔治,何铭,张国轩,胡一博,刘改霞
(哈尔滨工业大学(深圳)实验与创新实践教育中心,广东深圳518055)
摘要:本文应用Moldflow模流分析技术对即将开发的注塑件的成型方案进行仿真分析,首先,根据产品的结构特征确定最佳浇口位置,设计成型方案并进行动态模流分析,预测注塑件可能存在的质量问题。结果表明,初始方案的注塑件熔接线和气穴位于注塑件正上方位置,影响产品的强度、外观和使用寿命,同时翘曲变形量较大;为了提高产品的质量,分别从材料和浇注系统两方面进行优化,设计了优化方案一和优化方案二,分析结果表明,选用20%填充物的材料并选用2点进浇的浇注系统方案,优化了产品的质量,将熔接线和气穴转移到不影响产品质量和外观的位置,同时减少了充填时间,将翘曲变形量降低了64.4%。优化方案可为注塑件的开发提供参考,提高注塑件质量,缩短产品开发周期,降低模具开发成本。
关键词:注塑成型;模流分析;翘曲变形;优化
1前言
随着塑料工业的飞速发展,人们对塑料制品提出了更高的要求,而模具行业是一个高新技术密集型,依靠人工经验来设计模具已经不能满足需要。与传统的模具设计相比,计算机辅助工程(CAE)技术无论是在提高生产效率、保证产品质量方面,还是在降低成本、减轻劳动强度方面,都具有极大的效用。
Moldflow是一款用于塑料产品、模具的设计与制造的行业软件。Moldflow为企业产品的设计及制造的优化提供了整体的解决方案,帮助工程人员轻松地完成整个流程中各个关键点的优化工作。
Moldflow可以模拟整个注射过程及这一过程对注射成型产品的影响。Moldflow工具融合了一整套设计原理,可以评价和优化组合整个过程,可以在模具制造以前对塑料产品的设计、生产和质量进行优化。
某单位正在开发一款注塑件,如图1所示。注塑件结构、材料物性、模具结构以及成型工艺条件是否合理都会影响注塑件的成型质量,应用模流分析软件对当前注塑件进行注塑成型仿真分析,预测注塑件成型质量缺陷,并提出优化方案,推荐最佳的材料、流道系统,缩短注塑件成型周期,减少注塑件翘曲变形,提高产品质量,提高注塑件的生产效率和合格率,缩短产品开发周期,降低模具开发成本。
2注塑件模流分析
2.1模型建模及前处理
注塑件三维模型如图1所示,外形尺寸为:130mm×85mm×10mm,壁厚为1.5mm,采用3D实体网格模型,进行有限元网格划分,创建注塑件的网格模型,总共有4328个网格单元,诊断并修复网格模型,如图2所示。
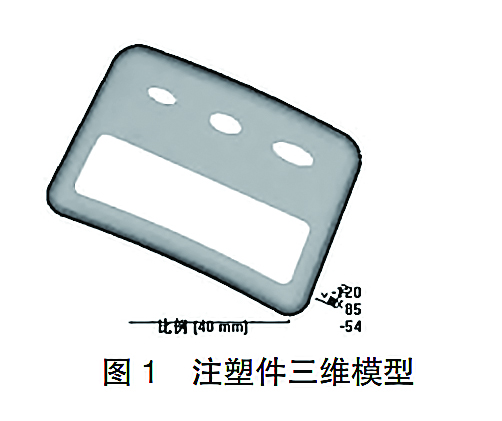
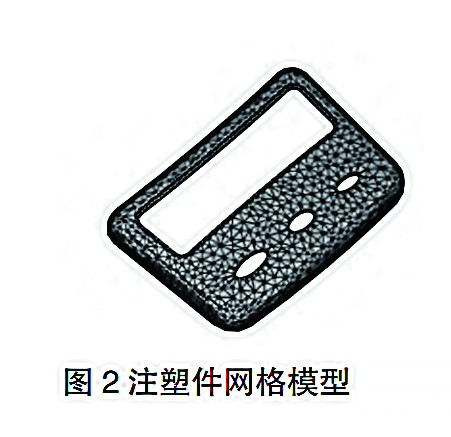
2.2初始方案模流分析
2.2.1浇口位置分析及材料
浇口位置的设定直接关系到熔体在模具型腔内的流动,从而影响聚合物分子的取向和产品成型后的翘曲,因此,选择合理的浇口在模具产品的设计中是十分重要的。
初始方案可以应用Moldflow的浇口位置分析功能,综合考虑塑件尺寸、结构、孹厚等特征、流动阻力和流动平衡,给出最佳的浇口位置。Moldflow中的浇口位置分析模块,可以用来为设计分析过程找到一个初步的最佳的浇口位置,对设计会有很好的参考价值。
模流分析类型选择“浇口位置”。
注塑件选择默认的材料PP,制造商为LGChemical,牌号为LupoySC-1004A。
工艺设置选择默认值即可,进行分析计算。
浇口位置分析结果如图3和图4所示,包括浇口匹配性和流动阻力指示器,可以看到,注塑件的上表面中心位置是最佳浇口位置。
根据浇口位置分析结果,将注塑件的上表面中心节点作为进浇口,如图5所示。
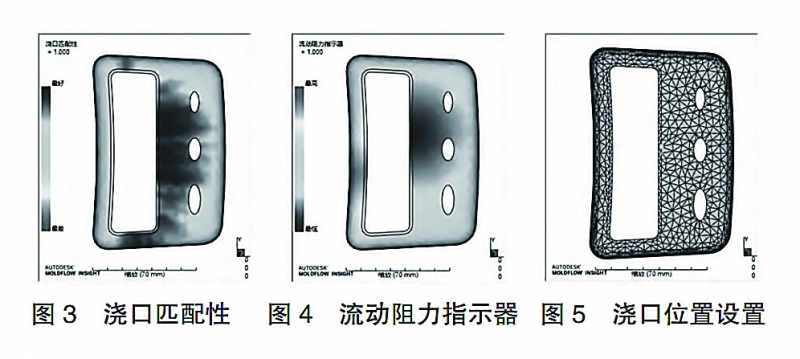
2.2.2模流分析
注塑件初始方案模流分析类型选择填充+保压+翘曲,分析注塑件注塑成型过程中的熔体流动行为,工艺参数直接选用系统推荐的默认值即可。
注塑件模型前处理及分析参数设置完成,选择分析,开始进行分析计算。
注塑件初始方案模流分析结果如图6所示,填充时间为1.086s,总的翘曲变形量达到0.6551mm,注塑件的熔接线位于最后填充位置,如图6所示(图片为产品逆时针旋转90度效果,以下相同),位于注塑件正上方最薄弱的中间位置,同样,气穴也位于注塑件薄弱的正上方位置。
该注塑件为外观件,首先,熔接线和气穴位于外观件正上方,会影响产品的外观质量;另外,熔接线和气穴位于注塑件最薄弱的位置,会影响注塑件的强度及产品的使用寿命,因此,初始方案存在致命的成型缺陷,需要对模具设计方案进行优化。

3注塑件优化分析
根据注塑件结构的特殊性以及模流分析的结果可知,该注塑件使用单浇口进浇会导致注塑件熔接处存在严重的熔接痕和气穴,由于注塑件正上方无支撑,容易产生变形,加上熔接痕和气穴正好位于正上方中间,影响注塑件的强度和使用寿命。
针对初始方案存在的以上问题,优化方案一选用填充物增强材料,优化方案二修改浇注系统方案,由1点进浇改为2点进浇,改变熔接痕和气穴位置,尝试提高注塑件的强度和使用寿命。
3.1优化方案1模流分析
优化方案一,选用PC+10%玻纤+10%碳纤材料,制造商为LGChemical,牌号为LuconCP-4208F,其它同初始方案,通过Moldflow优化分析,分析结果如图7所示。选用含20%填充物的PC材料比选用PC料,充填时间由1.086降低至0.816s,总的翘曲变形量由0.6551减小为0.279mm。
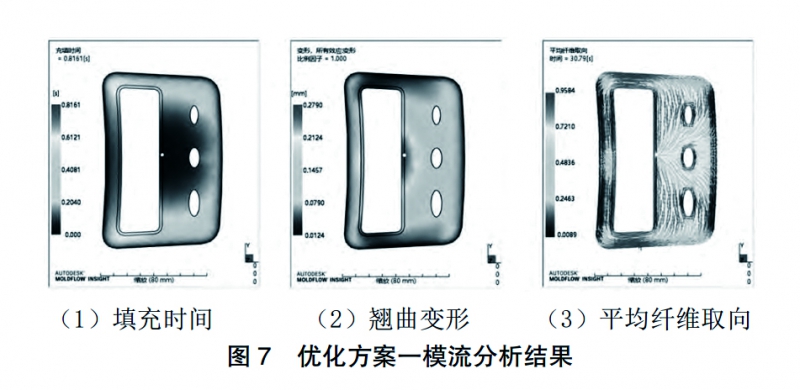
3.2优化方案2模流分析
优化方案2在优化方案1的基础上优化浇注系统设计,由单浇口改为双浇口进浇,浇注系统方案如图8所示。
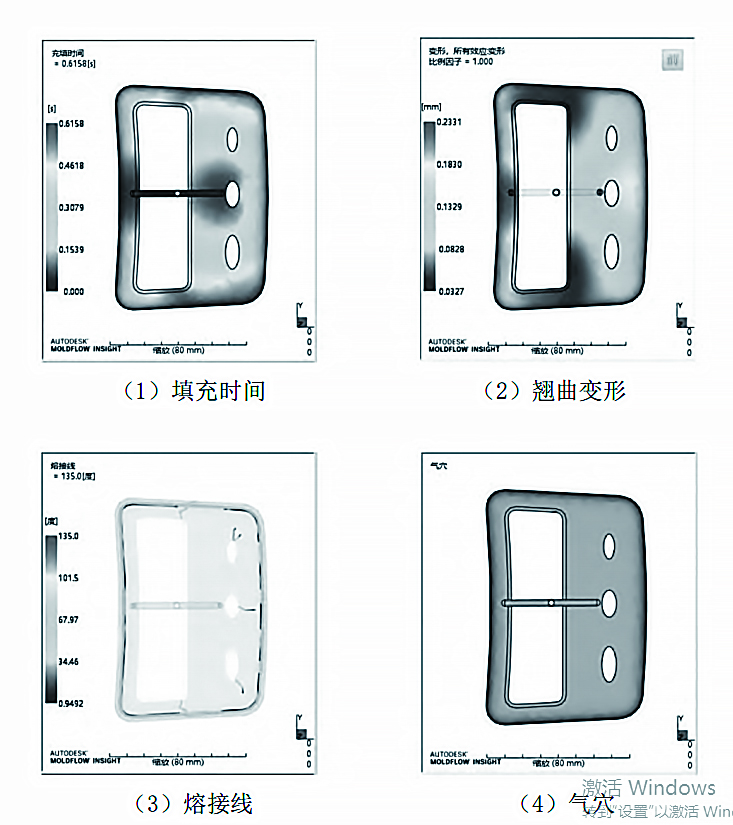
优化方案二模流分析结果如图8所示,由于设计双浇口同时进浇,注塑件的充填时间降低到0.6158s,总的翘曲变形量减小到0.2331mm,关键是注塑件的熔接线转移到注塑件的两侧边缘,气穴基本已经转移到注塑件的外表面,注塑件的强度和外观质量都显著提高。
4设计方案对比
初始方案由于注塑件质量不能满足使用要求,所以从材料和浇注系统方案两方面进行优化设计,三个方案及模流分析结果见表1所示,充填时间分别从1.086a分别降低至0.8161s和0.6158s,翘曲变形量分别从0.6551减小到0.2790s和0.2331s,总的翘曲变形量降低了64.4%,放大比例因子,三个方案的翘曲变形如9所示,注塑件的翘曲变形明显减少,显著提高了注塑件的质量;最重要的是注塑件的熔接线和气穴基本已经不影响注塑件质量,注塑件的强度和外观质量都显著提高,优化的效果还是比较明显的。
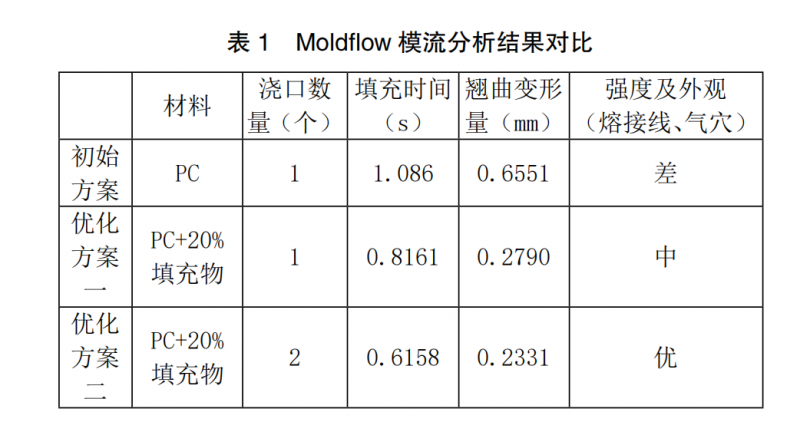
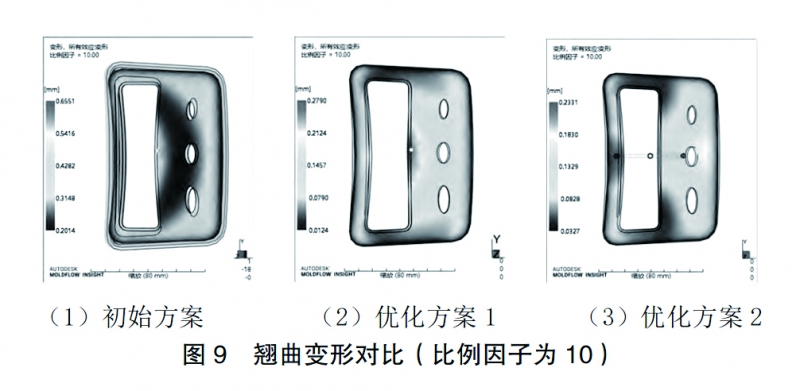
5结语
针对新开发的注塑件应用CAE软件进行辅助设计,预测模具初始方案可能存在的质量问题并进行优化设计和分析,本文提出了2个优化方案,分别从材料和浇注系统两个方面进行优化。结果表明,通过Moldflow模流分析技术,注塑件的填充时间从1.086s减少到0.6158s,翘曲变形量由0.6551mm减小到0.2331mm,同时,将影响注塑件强度和外观的熔接线和气穴等缺陷转移到其他位置,提高了产品的强度、外观、质量及使用寿命,为注塑件的开发提供参考,从而避免单纯靠经验评估可能出现的失误,避免模具反复试模修模而增加的开发成本和开发周期,同时可明显改善产品成型质量。
参考文献:
[1] 陈如香 , 刘改霞 , 戴坤添等 . 基于 Moldflow 的注塑件模流分析 与优化 [J]. 科技创新与应用 ,2022:12(29):80-83.
[2] 王蓓 , 王刚 .Moldflow 模具分析应用实例 [M]. 北京 : 清华大学 出版社 ,2004.
[3] 陈如香 , 戴坤添 , 刘能锋 . Moldflow 2021 模流分析从入门到精 通 [M]. 北京 : 电子工业出版社 ,2010.
[4] 陈如香 , 彭响方 , 刘斌 . 塑料配重块收缩率的计算模拟 [J]. 塑 料 ,2010:39(30):107-109.
[5] 王新继 , 杜群贵 , 刘雄 , 谢叶青 . 典型注塑模成型过程模拟与模 具变形分析 [J]. 机械设计与制造 ,2015, (01):243-246+250.
[6] 何建林 , 白志鹏 . 基于 Moldflow 的汽车配件 CAE 优化分析 [J]. 机械设计与制造工程 ,2019,48(2):16-20.
[7] 陈如香,彭响方 . 基于 Moldflow 的注塑件熔接痕缺陷验证与优 化 [J]. 塑料,2010:39(5):85-88.