田玉晶1,2,董浩2,孙晓宇1,2
(1.哈尔滨理工大学威海研究院,山东荣成264300;2.哈尔滨理工大学荣成学院,山东荣成264300)
摘要:分析热敏打印机底壳的结构特点,利用UG及Moldfow软件进行建模并模拟注塑成型过程。结果表明:浇口位置由底部中心改为螺纹装配孔处能够有效避免试模时产生的熔接痕,填充效果良好。根据模流分析结果得出,最佳熔体温度为200℃,最佳模具温度为80℃,最佳注射时间为0.1s。冷却方式采取带有隔水板的冷却系统,模拟结果显示成型质量符合要求。模具结构采用一模两腔布局,功能动作为一次开模,一次顶出,四向一次抽芯。
模具结构整体布局合理,利用该模具生产的注塑制件表面质量及精度均满足设计要求。
关键词:注塑成型;热敏打印机底壳;Moldflow;UG;模具设计
塑料因具有质轻、价格低、抗化学腐蚀性好、绝缘性能优良等特点,在机械加工、电气设备、新能源、航空航天等领域被广泛应用[1-3]。注塑模具作为成型工具,在制件投入生产中起到至关重要的作用[4-6]。随着我国科学技术的进步,传统的模具生产加工技术已不能满足市场发展的需求,运用新工艺和新技术提高生产率、减少生产成本、避免资源浪费是模具产业发展的必经之路[7-9]。利用CAD/CAE/CAM技术能够预测塑件成型过程缺陷,改善成型工艺性,设计合理的模具结构,极大地提高模具生产效率,缩短模具制造时间[10-12]。周俊杰等[13]利用Moldflow对塑料排水泵过滤网进行注塑成型过程模拟,采用正交试验结合方差分析优化成型工艺参数,使最大翘曲变形量降低10.37%,并通过UG设计模具结构。黄继战等[14]采用UG
NX12.0设计一套三板式的四面抽芯单腔模具,简化了模具结构。刘青宜等[15]以响应面法对电机外壳成型工艺进行优化,降低了制件翘曲变形量。王平洲等[16]基于Moldflow及UG注塑模向导模块优化了杯托产品的模具结构,缩短制造周期。王君等[17]通过对抽芯机构的创新设计对讲机外壳的四面抽芯及内侧抽芯模具机构。
本文以某热敏打印机底壳为研究对象,针对试模后塑件出现的熔接痕问题,分析产生质量问题的原因,利用CAE软件对其注塑过程进行工艺分析,优化制定合理工艺方案,并运用UG12.0注塑模向导模块设计合理注塑模具,解决实际生产中的问题。
1.塑件工艺性分析
图1为热敏打印机底壳结构。整体外形为方形壳体,最大外形尺寸为140mm×114mm×54mm,平均壁厚为2.5mm,最小壁厚为0.4mm,体积为78.6cm³。制件两侧面设计有平行分布的工艺凹槽,右侧面有散热孔,后面设计装配孔,成型较复杂,需要设计合理的四向侧抽芯机构。制件材料为丙烯腈-丁二烯-苯乙烯共聚物(ABS),该材料耐磨性能好、尺寸稳定性优异。结合实际生产需求,所选注射压力机型号为XS-ZY250/180型塑料注塑成型机,注射量为250cm³,锁模力1800kN。
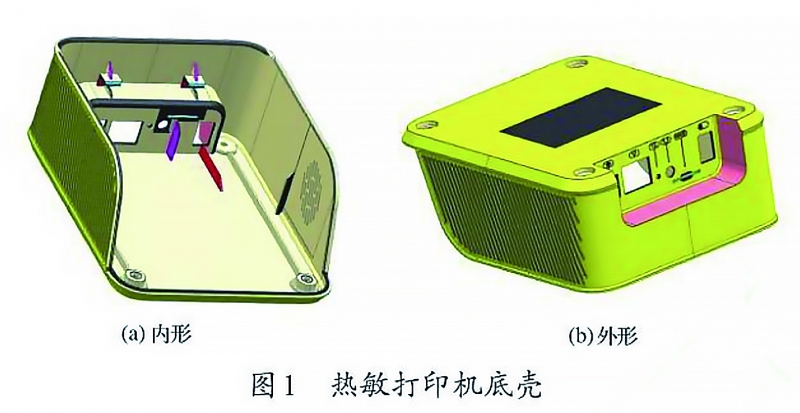
图2为塑件内表面和熔接痕位置。为保证制品整体装配及美观性,初期浇口位置设计在底部凹槽中心处,浇口留痕后期以商标遮盖。经实际试模发现在后侧中心处产生熔接痕,导致产品质量不合格,如图2b所示。原因可能是制件后面多为空洞及流速不连贯区域,两股熔体在后面中心部位汇合时前沿温度下降较快产生应力,导致物料不能完全融合。为解决热敏打印机底壳质量缺陷,优化加工工艺,利用Moldflow模拟软件对塑件进行CAE分析。
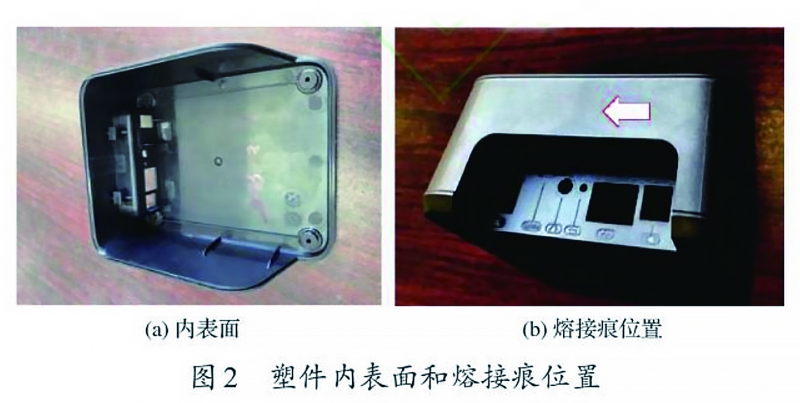
2.塑件CAE分析
2.1网格划分
利用UGNX12.0软件进行三维建模,在模型导入Moldflow软件分析之前需要通过Caddoctor软件对制件结构进行简化处理[18-20]。热敏打印机底壳属于薄壁零件,为保证网格质量及分析精度选用双层面网格,取全局边长为1mm。图3为网格划分后的模型,网格数量为239292,最大纵横比为19.17,最小纵横比为1.16,平均纵横比2.06,网格匹配率为86.1%。该模型可以通过模流仿真得到准确的分析结果。
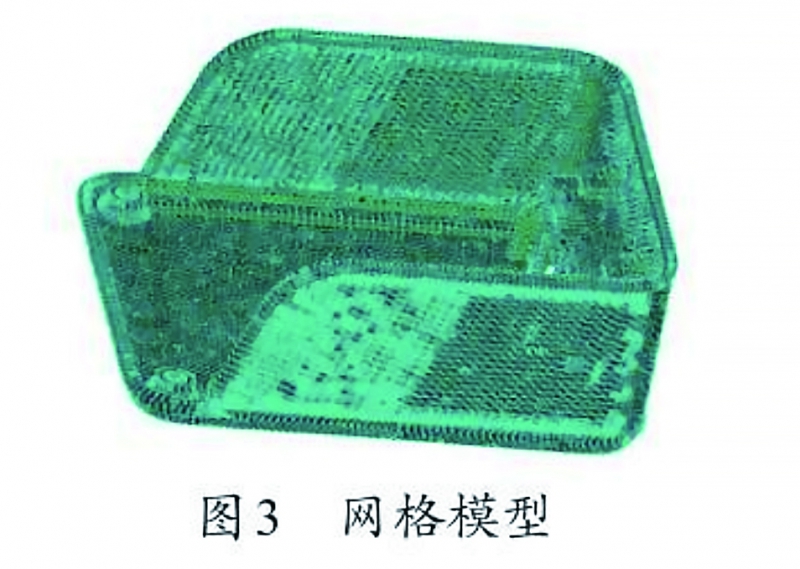
2.2浇口位置分析
浇口位置的正确选择使填充过程更加均匀,避免产生空洞、填充不均、熔接痕等缺陷,保证塑件的质量[21-23]。图4为浇口位置。从图4a可以看出,浇口匹配性模拟结果显示,红色区域浇口匹配性最差,蓝色区域为最优浇口区域。从图4c、4d可以看出,优化后采取点浇口,设置在底面螺纹装配孔处。该制件属于小型件,底壳与打印机身装配由其他3个螺纹孔配合,不影响整体装配性。该浇口位置在避免浇口痕迹、保证制件表面质量的同时,浇口匹配性较好。
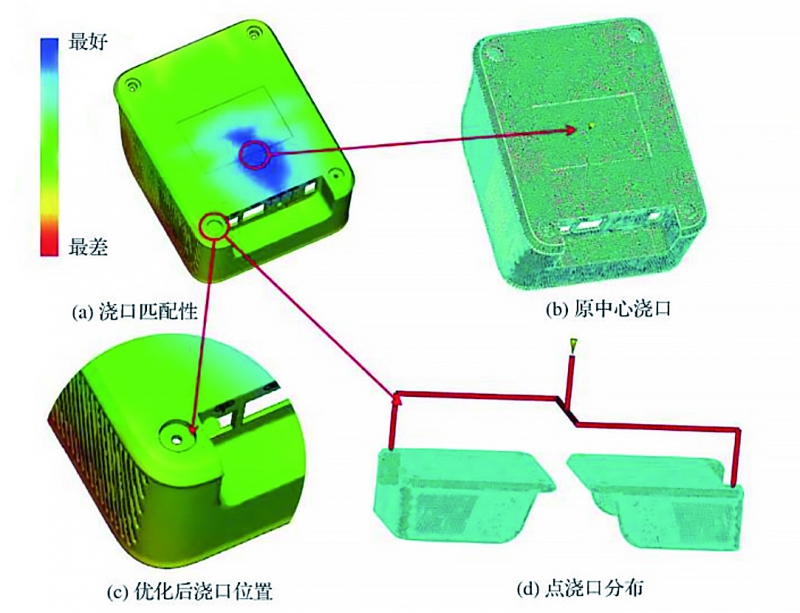
通过Moldflow验证该浇口位置合理性,图5为可成型性分析。从图5可以看出,熔接痕只少量分布于两侧面平行凹槽且填充效果好,浇口位置选择合理。
图6为成型效果图。从图6a可以看出,填充时间为1.15s,填充区域分布均匀。从图6b可以看出,流动前沿温度的温差约为6.4℃,符合设计原则[24]。从图6c和6d分析得出,制件成型均匀,收缩量小,成型质量优异。
2.3冷却系统设计
根据塑件在型腔内部的分布,构建合理的冷却水道能够提高系统总换热率,确保塑件成型质量,提高生产效率[25-27]。热敏打印机底壳为盒形件,普通冷却水道一般为直通式X型、Y型或者环形排布,无法对该制件进行充分冷却,图7为两种不同排布形式的冷却水道方案。从图7a可以看出,隔水板系统能够使冷却液在冷却水道弯道处形成湍流,增强冷却效果。从图7b可以看出,随形冷却方式水管道利用3D打印成型,能够更好地贴近制件表面进行冷却。对两种方案进行填充+保压+翘曲分析序列模拟,得出最优冷却方案。
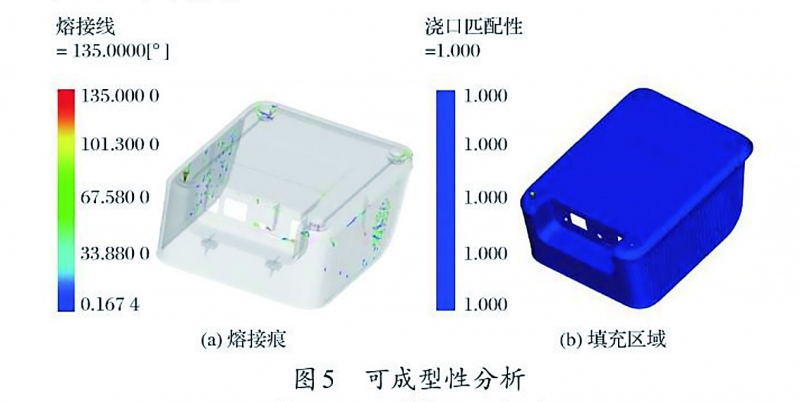
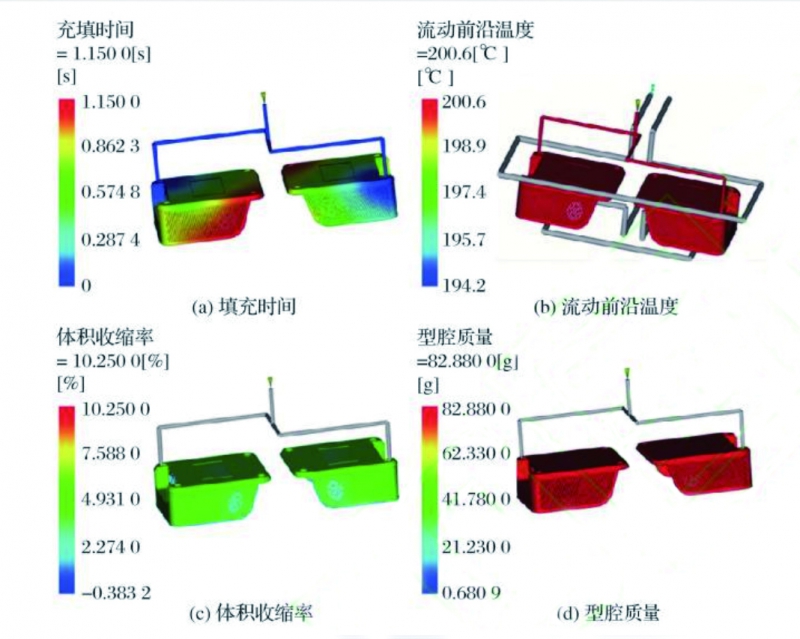
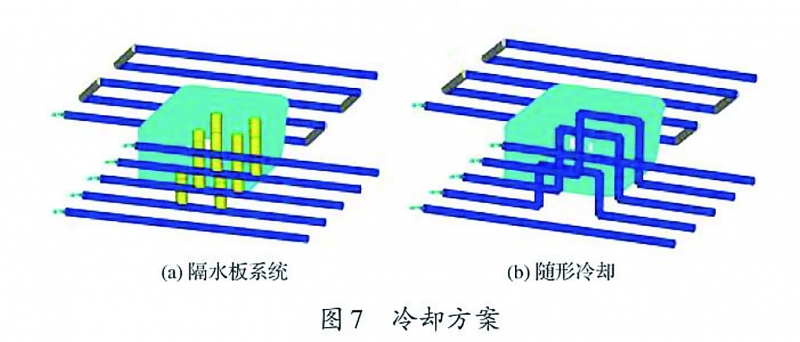
3.塑件成型参数分析
3.1最佳工艺参数
为比较两种冷却方式对成型质量的影响,依据成型窗口分析制定最优注塑工艺参数[28-29]。图8为基于Moldflow软件分析所得的最优注塑参数。根据图8结果,结合ABS材料注塑工艺参数范围,最优工艺参数为熔体温度200℃、注射时间0.1s、模具温度80℃。
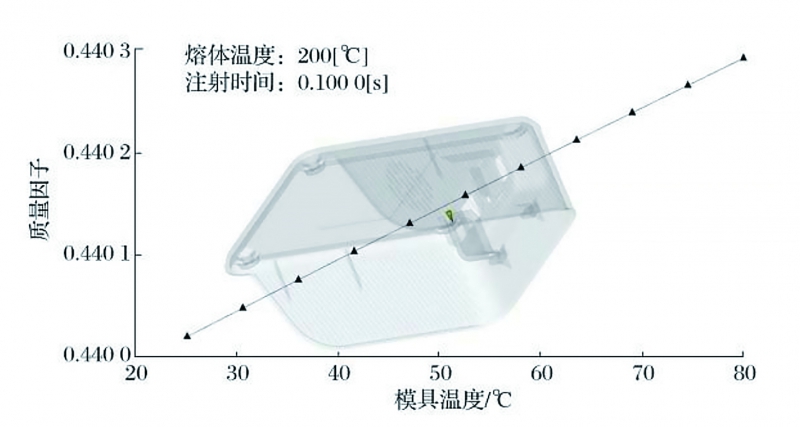
3.2 冷却系统分析
采取控制变量法,将优化后工艺参数导入模拟软件,通过对比回路冷却液温度、平均温度以及翘曲程度确定模具的冷却系统方案。图9~图11分别为冷却液温度、平均温度和翘曲变形效应云图。从图9~11可以看出,随形冷却方式的冷却液温度及零件平均温度分别低于隔水板冷却0.12℃和5.4℃,零件翘曲程度高于隔水板系统0.1595mm。两种冷却方案对该制件的冷却效果差异不大,因随形冷却需要3D打印技术支持,其加工成本以及加工时间远高于隔水板冷却,结合实际选用隔水板冷却方案。
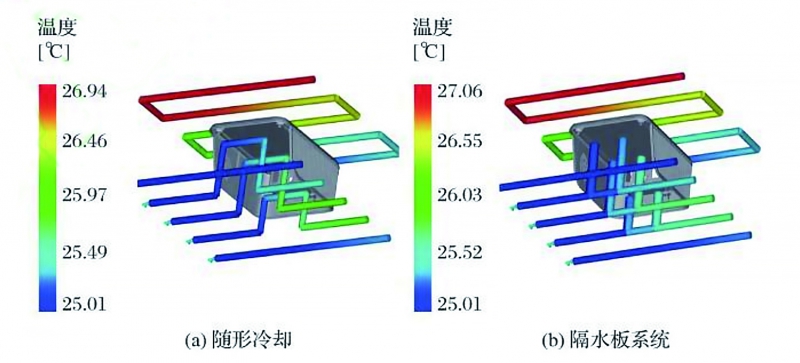
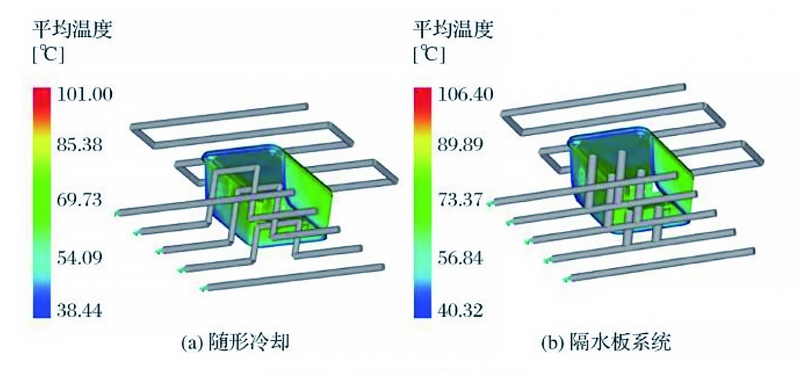
3.3 成型质量分析
图12为隔水板冷却系统水管道排布及制件成型质量结果。针对制件结构及型芯的分布,外侧为环形冷却水路,内侧为隔水板冷却水路,水路直径8mm。从图8可以看出,冷却液出入口温度变化为3.75℃,回路管壁温差为6.96℃,制件温度均匀,翘曲量小,冷却液流动状态为层流,冷却效率高,冷却水路设计合理。
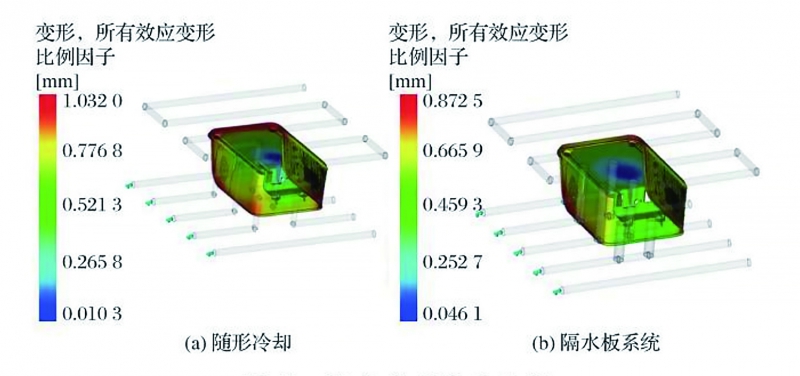
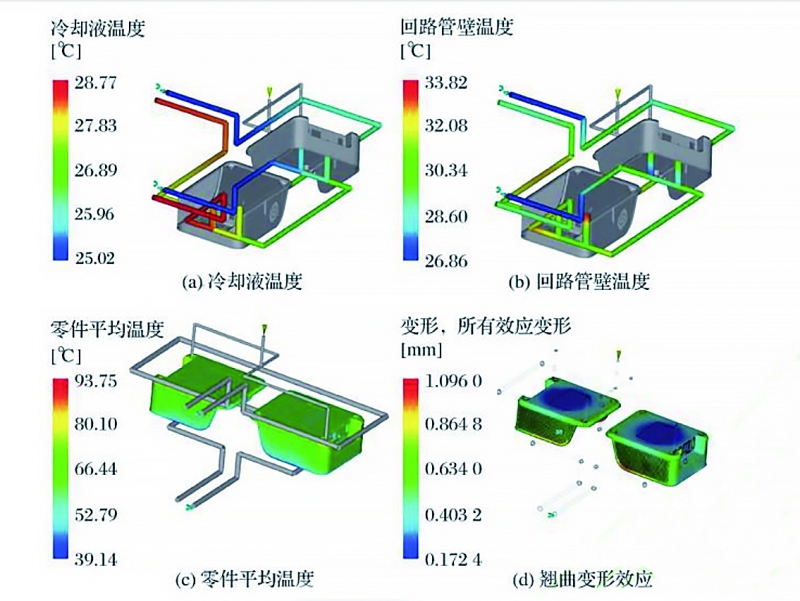
4.基于UG的模具结构设计
4.1主要零部件设计
为提高生产效率,降低生产成本,模具设计为一模两 腔,图13为主要零部件设计。
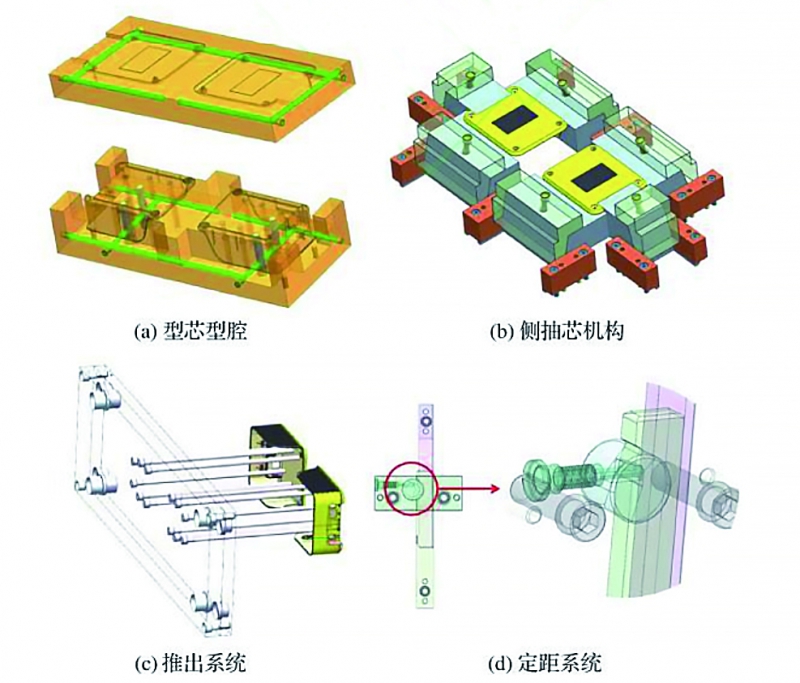
从图13a可以看出,型芯型腔分模位置处于制件最大截面处,模仁采用虎口精定位,整体嵌入结构。从图13b可以看出,侧抽芯机构利用斜导柱加斜滑块四向侧向分型,斜导柱倾斜角75°,抽芯距为16mm。从图13c可以看出,分模后制件通过12根圆推杆推出,推出过程平稳。从图13d可以看出,模具分型定距系统采取定距扣机机构,能保证首次分型距离,使模具顺利分型。
4.2模具工作原理
基于CAE分析结果,结合实际生产需求,图14为模具结构及三维装配图。
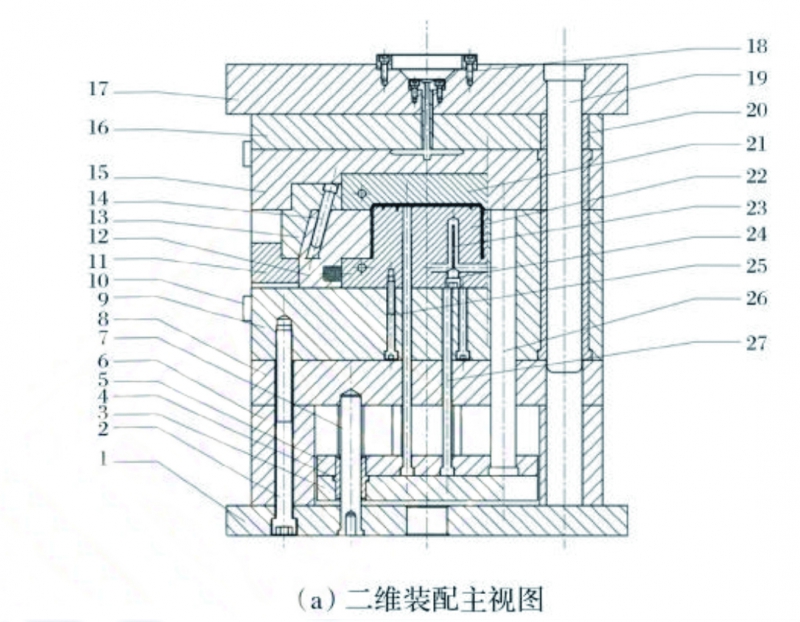
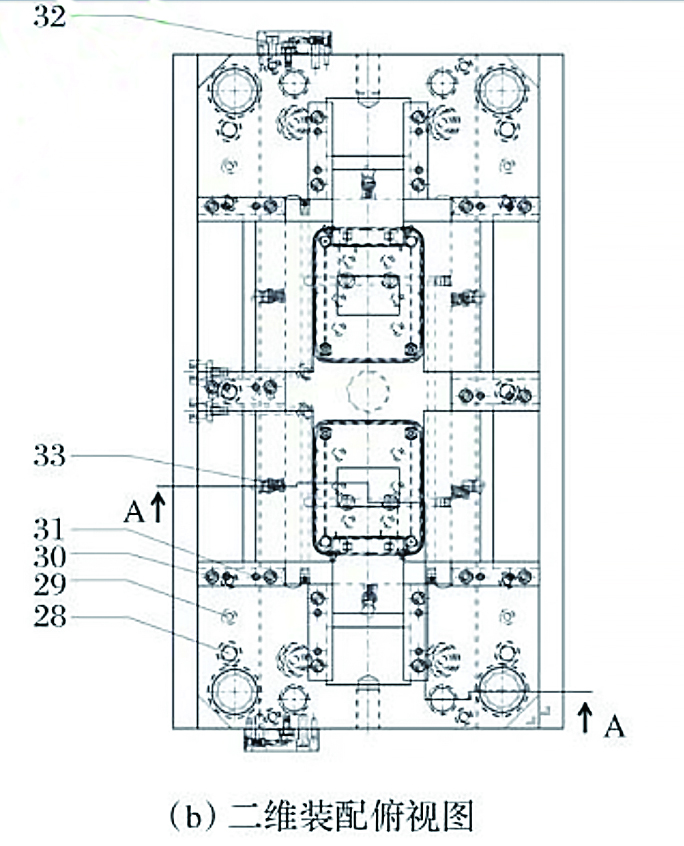
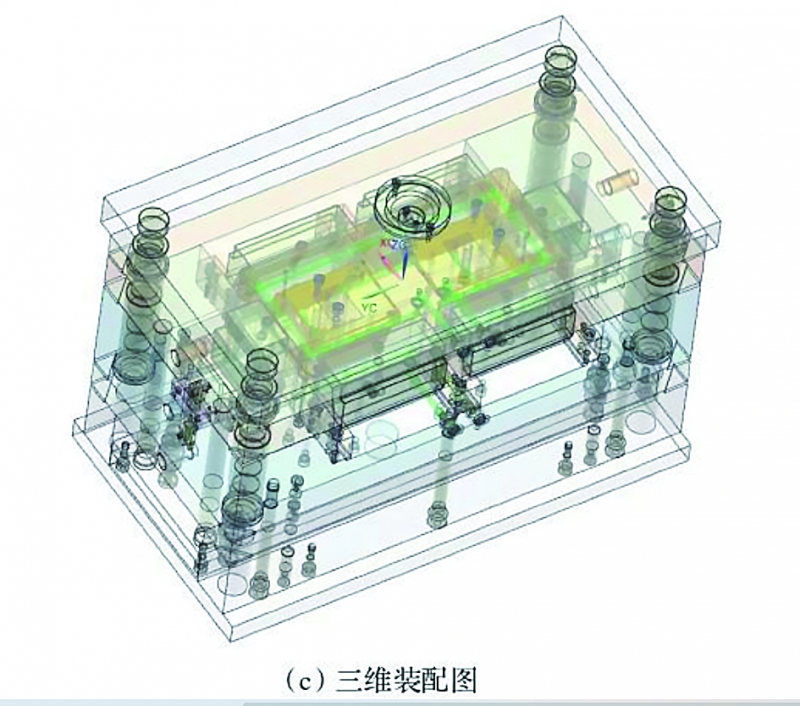
注:1-动模座板;2,18,28,30-内六角螺钉;3-推板;4-推板导套;5-推杆固定板;
6-垫块;7-推板导套;8-动模垫板;9-动模套板;10-入/出水阀门;11-压块;
12-滑块;13-楔紧块;14-斜导柱;15-定模套板;16-脱胶板;17-定模座板;
19-导柱;20-导套;21-型腔镶块;22-型芯镶块;23-隔水板;24-止水塞;
25-圆头螺钉;26-复位杆;27-推杆;29-销钉;31-定位销;
32-定距扣机;33-弹簧。
模具的工作过程如下:开模时,定模套板15与动模套板9在定距扣机32的作用下向开模方向运动,脱胶板16与定模套板15分离,凝料被一起从主流道中拉出。随着开模运动的继续,当达到定距扣机32的固定距离后扣机两部分分离,第一次分型结束,定模套板15与脱胶板16分型,凝料与制件分离并脱落。接着动模部分继续开模运动,定模套板15停止运动,定模套板15与动模套板9分型。压块11将滑块12与动模套板9连接,使滑块12可沿垂直于开模方向运动。在分型过程中,动模套板滑块12在弹簧33及斜导柱14的作用下跟随动模部分一起向开模方向运动。
开模工作完成后,推出机构推动推板3以及推杆27沿着推板导套7向合模方向运动,将制件从模具中推出。
制件推出后,在拉杆作用下动模部分向合模方向运动,复位杆26先触碰到定模套板15停止运动,带动推出系统各零件复位。当定模套板15与动模套板9接触后,定距扣机32两部分自动复位,动模部分与定模套板15继续运动,直至定模套板15与脱胶板16接触后完成合模工作。
注塑模具各零部件利用传统加工方法成型[30]。图15为利用模具实际加工的产品。从图15可以看出,塑件熔接痕问题得到解决,整体结构、质量及精度均满足设计要求。
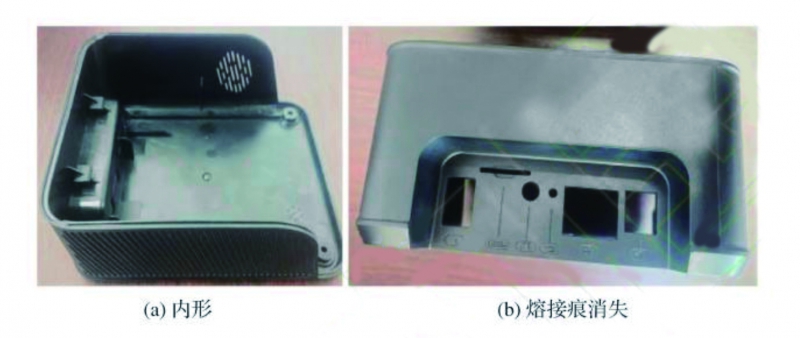
5.结论
利用Moldflow对热敏打印机底壳进行模拟仿真分析,综合制件结构及浇口匹配性,将浇口位置由底部凹槽中心部位改为装配工艺孔处,解决了实际试模出现的熔接痕问题。模具冷却方式为带隔水板的冷却系统。质量分析结果显示,最佳熔体温度为200℃,模具温度为80℃,注射时间为0.1s。基于UG注塑模向导模块设计注塑模整体结构,确定模具结构为一模两腔,两次分型,四向抽芯,制件由12根推杆推出,模具整体结构布局合理。利用CAD/CAE辅助技术设计模具能够提高一次性试模成功率,有效缩短模具设计周期,提高企业核心竞争力。塑件精度及表面质量均满足设计及使用要求。
参考文献
[1]刘朝艳.2022—2023年世界塑料工业进展(II): 工程塑料和特种工程 塑料[J]. 塑料工业,2024,52(4):1-26.
[2]林朗,工程塑料在电气设备方面的应用[J]. 塑料工业,2024,52(2):187.
[3]席晓晖.工程塑料的研究综述[J].山东化工,2024,53(3):84-86.
[4]刘世革,袁长勇.注塑模具制造产业的发展现状及未来趋势研究[J]. 内燃机与配件,2019(15):200-201.
[5]任天娟 .基于CAD/CAE/CAM 一体化技术的注塑模具设计制造研究 [D]. 陕西:长安大学,2017.
[6]杨磊.模具工业发展现状及注塑模具新工艺和新技术[J]. 南方农机, 2021,52(14):135-137,143.
[7]张铁.基于整体结构标准化的注塑模具设计系统开发[D]. 武汉:华中 科技大学,2022.
[8]赵春元 .基于Moldflow 的烟丝水分仪注塑模具浇口位置优化分析 [J].塑料科技,2021,49(4):75-78.
[9]王谦,陈晓勇. 国内注塑模具设计研究现状的可视化分析[J].工程塑 料应用,2019,47(5):159-164.
[10]龚世海.注塑模具先进制造技术发展趋势综述[J].现代制造技术与装 备,2019(9):208-209.
[11]郭晓鑫.注塑模CAD/CAE/CAM 技术的发展和应用[J].现代制造技 术与装备,2020(6):161-162.
[12]张晓光,程志超,孟枭,等.无人机灭火弹饰盖模流分析及注塑模具设 计[J]. 塑料科技,2024,52(4):121-126.
[13]周俊杰,陈秋凡,冯文,等.基于Moldflow 的排水泵过滤网注塑工艺优 化与模具设计[J]. 工程塑料应用,2024,52(1):109-115.
[14]黄继战,范玉,肖根先.温控器面壳注塑模具设计[J].工程塑料应用, 2023,51(10):118-124.
[15]刘青宜,郭谭娜,王宁.基于Moldflow 电机外壳注塑成型质量分析[J]. 塑料科技,2023,51(11):80-84.
[16]王平洲,钟丽霞,郑志军,等.基于Moldflow 和 UG 的杯托注塑模设计 [J]. 工程塑料应用,2022,50(7):99-103.
[17]王君,司成俊.基于四面侧向抽芯机构和内侧抽芯机构的对讲机外壳 注塑模具设计[J].塑料科技,2024,52(2):116-118.
[18]叶立清.基于UG/MFI 的 LED 灯内壳注塑模具设计[J]. 塑料科技, 2020,48(11):98-102.
[19]杨双华.轿车雾灯座注塑工艺CAE 与成对模具设计[J]. 塑料工业, 2018,46(3):61-66.
[20]周纪委,王明伟,张文超,等.基于灰色关联分析的汽车雾灯灯罩注塑 成型工艺优化[J]. 塑料科技,2022,50(12):74-79.
[21]郭旭,邢飞,王慧儒,等.基于Moldflow 的分离罐浇口位置方案分析[J]. 塑料科技,2023,51(12):70-75.
[22]朱红萍,王星星.基于田口实验的水盒盖注塑工艺参数优化与模具设 计[J]. 塑料科技,2022,50(12):80-84.
[23]李波,林荣川,王云超,等.电视USB 支架的模流分析及模具设计[J].机 械设计与制造,2021(5):176-179.
[24]黄华辉,戚春晓,王灿宇,等.基于Moldflow 的投影仪上盖倒装热流道 注塑模设计[J]. 轻工科技,2024,40(3):183-186.
[25]丁同梅,周正武.基于CAD/CAE 的笔记本底座注塑模具设计[J].塑料 科技,2019,47(4):82-87.
[26]梅益,那天灿,王莉莉,等.基于UG 和Moldow 的电器壳盖注塑模优化 设计[J]. 塑料科技,2019,47(11):122-127.
[27]黄清民,周玉辉.淋浴器花洒夹座注塑件浇注系统的CAE 分析[J].塑 料,2021,50(4):76-80.
[28]孙世臣,韩旭,胡辰,等.帆船绳钩注塑模具设计与工艺优化[J].工程塑 料应用,2020,48(6):83-87.
[29]赵美云,基于CAE 技术的电器面壳零件注塑成型工艺研究[D]. 合肥: 合肥工业大学,2022.
[30]张荣清,模具制造工艺[M].北京:高等教育出版社,2016.