张维合,冯婧,赵利平,胥永林,闫丽静,费强,陶永杰,陈卓航
(广东科技学院,广东东莞523000)
摘要:针对汽车左前门板的尺寸大小、结构特点和工艺要求,设计了一副大型薄壁顺序阀控制的热流道注塑模具。模具喇叭网孔成型零件采用粉末冶金透气钢,有效消除了喇叭网孔中填充不良和熔接痕等成型缺陷。模具采用倾斜式导滑槽,有效解决了倾斜式内侧倒扣脱模难题。模具采用由顺序阀智能技术控制的热流道浇注系统,有效解决了汽车左前门板尺寸大壁厚小熔体填充难题。模具采用快速且均衡温度控制系统,注射周期缩短了约8%,尺寸精度达到了MT3(GB/T14486—2008)。
关键词:汽车左前门板;大型注塑模具;顺序阀热流道;侧向抽芯机构
前言
汽车门板是汽车内饰件的重要组成部分,位于汽车车门的内侧。为因应轻量化、美观化和安全性要求,汽车门板都采用塑料,由注塑模具注射成型。汽车门板批量大,尺寸大,结构复杂,汽车门板注塑模具是典型的大型、薄壁、精密、复杂且长寿命注塑模具,设计难度大,设计周期长。本文介绍了某款新能源汽车左前门板注塑模具的先进结构及其创新技术。
1 塑件结构及成型工艺要求
图1所示为某款新能源汽车左前门板零件图,材料为PP/EPDM,收缩率取1.1%[1],其中EPDM乙烯、丙烯和少量的非共轭二烯烃的共聚物,是乙丙橡胶的一种,能够提高门板的抗冲击弹性[2]。塑件结构特点和成型工艺要求如下:(1)塑件尺寸为:804.8mm×721.3mm×102.4mm,平均壁厚2.6mm,流长比约为200,为典型的大型薄壁塑件,成型困难。(2)塑件外形复杂,塑件内、外侧面共有S1~S6共6个与脱模方向不一致的倒扣,脱模困难。(3)塑件外观面(俗称A面)蚀皮纹,脱模斜度均大于或等于5°(4)基于车门的位置,成型塑件外观面不允许有飞边、收缩凹陷、熔接痕等缺陷,也不允许有黑斑和点浇口痕迹。
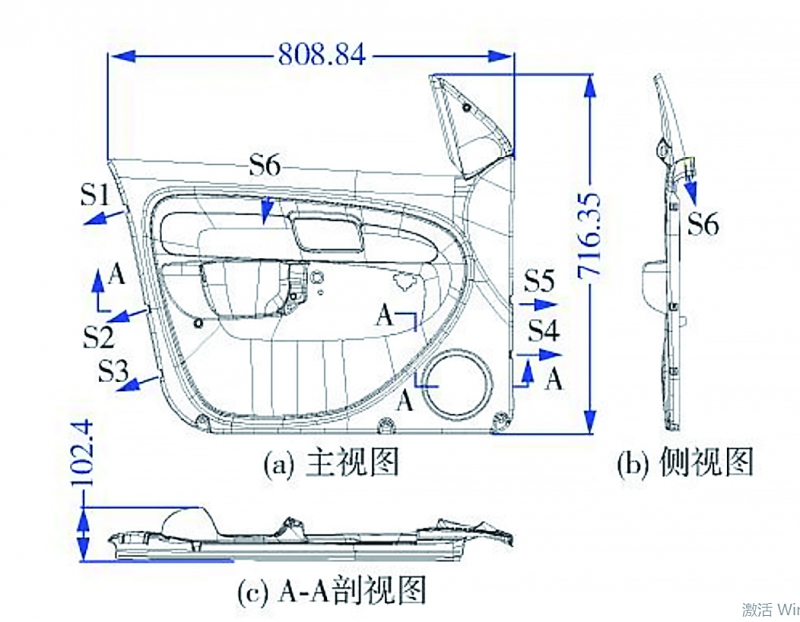
图1 汽车左前门板零件图
2 模具结构设计
由于汽车左前门板属于大型平板类零件,为改善熔体填充,模具采用热流道浇注系统,但由于塑件表面不允许有浇口痕迹,塑料熔体最后由扇形浇口从侧面进入模具型腔。塑件内外侧面共有6个倒扣,其中S6为内侧,倒扣面积大,倒扣深度10mm,模具中采用“斜顶+斜推杆”的内侧向抽芯机构;S1、S2、S3、S4、S5为外侧倒扣,模具采用“滑块十斜导柱”抽芯结构。模具详细结构见图2。
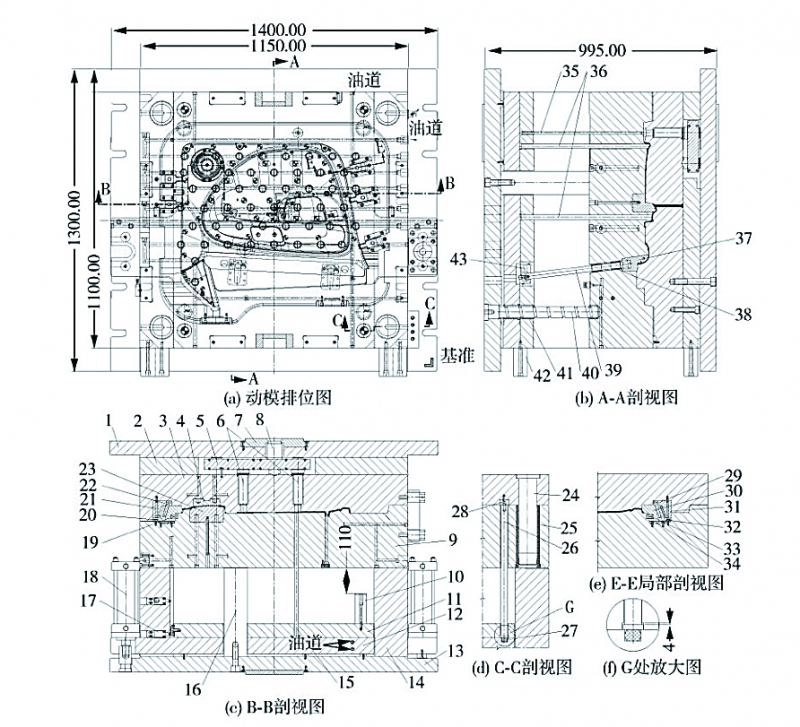
1—定模固定板2—框板3—定模A板4—定模镶件5—热流道板6—二级热射嘴
7一定位圈8—一级热射嘴9—动模B板10—限位柱11—推件固定板12—推件底板
13—动模固定板14—方铁15—推杆16—撑柱17—行程开关18—顶出油缸19—滑块
20—挡块21—锁紧块22—斜导柱23—动模镶件24—导柱25—滚珠导套26—复位杆
27一弹力胶28—耐压硬块29—斜导柱30—滑块31—锁紧块32—挡销33—弹簧
34—耐磨块35—流道拉杆36—塑件推杆37一斜顶38一斜推杆导套39—斜推杆
40—推件板导柱41—导套42—支撑柱43—斜推杆底座
图2 汽车左前门板注塑模具结构图
本模具外形尺寸为:1400mm×13000mm×995mm,总质量约10t,属于超大型注塑模具[3]。
2.1 模具成型零件设计
为提高模具刚度,减小模具的外形尺寸,模具定、动模成型零件与模板采用一体式结构,即型腔直接开在定模A板和动模B板上,定模A板选用P20模具钢,动模B板选用718模具钢[4]。模具定模A板和动模B板采用四面围边的锥面定位结构,详见图3模具立体图。
本模具成型零件设计的难点是门板喇叭网孔成型结构的设计。由于喇叭网孔数量多,模具设计图中若全部画出会严重影响电脑运行速度,因此门板喇叭网孔设计时,不要在3D上面把每一个喇叭网孔都设计出来,只需要设计少部分的参考喇叭网孔,再在零件上面设计上不同颜色的喇叭网孔分布线,以2D线条来表示喇叭网孔的分布,见图4。
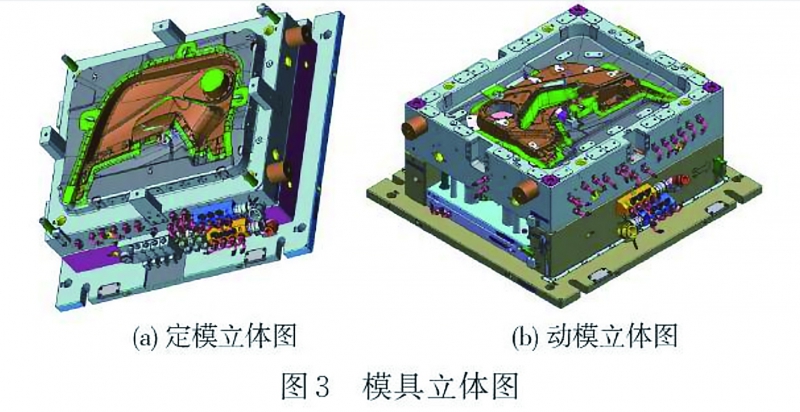
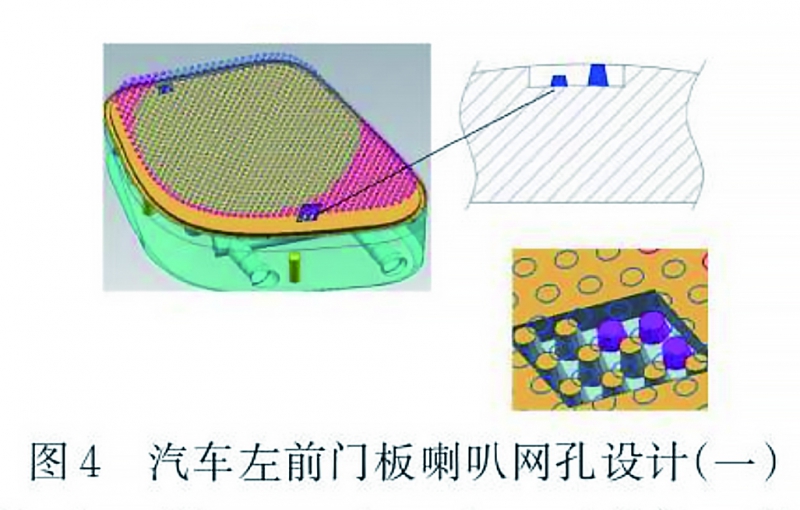
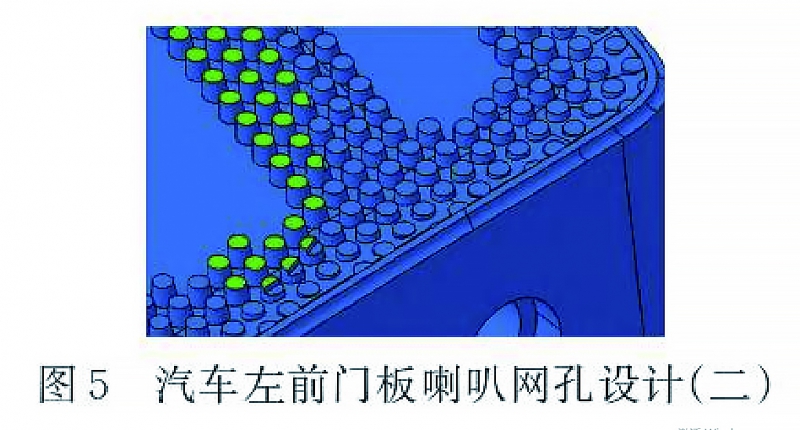
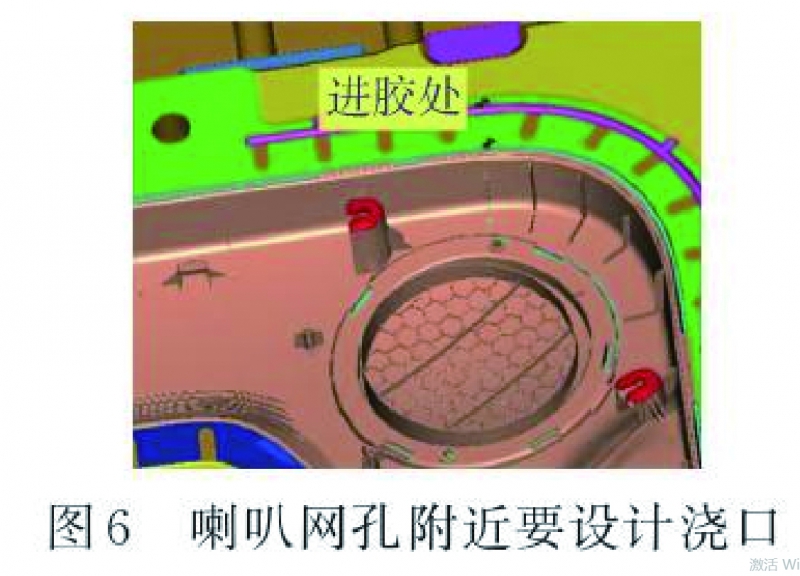
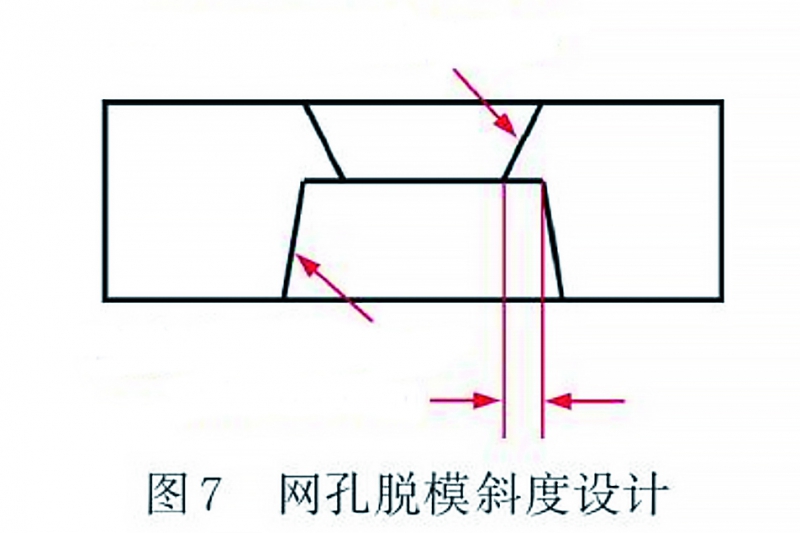
本例以碰穿网孔的高度为基准,长钢料封胶,在局部切出几个喇叭网孔作为网孔尺寸基准进行设计。如果碰穿网孔或者不碰穿网孔都不等高,那么我们需对所有不同高度的网孔都进行3D真实建模。这种设计方法只针对圆形网孔,其他形状网孔需3D真实建模。碰穿与不碰穿的网孔在3D设计时要有区分,用颜色区分最好,见图5。由于碰穿孔对塑料熔体阻力大,喇叭网孔附近要设计浇口,以改善熔体填充,提高保压效果,消除熔接痕,见图6。汽车门板喇叭网孔定模型腔脱模斜度应尽量大,定、动模对碰处要设计0.1~0.15mm台阶(见图7),动模对应位置应设计加强筋骨防止黏定模。
为避免困气,喇叭网孔镶件采用粉末冶金透气钢。透气钢虽然贵,但排气效果好。如果采用P20模具钢,需要在网孔镶件上设计排气针或者镶针,网孔镶件底部还要设计排气槽,但这种排气槽很容易被胶粉和油污堵塞,导致排气不畅而影响熔体填充,由此造成的损失会生产成本更高[5]。
2.2 模具导向定位系统设计
模具导向定位系统攸关大型、精密和长寿命注塑模具设计的成败。汽车左前门板注塑模具设计了4支圆导柱和4支方导柱,其中圆导柱布置在模具的4个角上,尺寸为φ80mm×300mm。方导柱布置在模具4个边的中间位置,尺寸为50mm×150mm×300mm。方导柱既起导向作用又起定位作用,详见图2和图3。4支圆导柱和四支方导柱都装配在定模A板上,这种结构既方便成型塑件取出,又方便模具制造,在配模时4支导柱还可作为支撑脚用[6]。
在五组“滑块+斜导柱”的侧向抽芯机构中,每个滑块都由锁紧块推回复位,为减小锁紧面之间的磨损,导柱24必须在各锁紧面接触之前20mm就插入滚珠导套25内。
2.3 模具浇注系统设计
针对左前门板为大型、复杂、薄壁平板类塑件,且喇叭网通孔多的特点,模具采用“3点热射嘴+热流道板”的浇注系统。3点进料势必产生多条熔接痕,熔接痕不但影响美观,也会减小门板的强度。为了消除熔接痕或把熔接痕赶到非外观面,3个热射嘴的射胶时间和顺序采用顺序阀控制,顺序阀由油缸的驱动,其开闭顺序和时间由模具智能化系统控制,以得到最优的成型质量。由于门板表面不能有浇口痕迹,故只能采用“热流道+冷流道”组合式浇注系统,熔体经热流道、冷流道,最后由3个扇形浇口从侧面进入型腔[1-2,7]。浇口位置见图8,图中G1、G2和G3为热射嘴位置。热射嘴至塑件边缘的流道长度不宜超过50mm,过长的冷流道会导致热量及压力损失过大。
2.4 模具侧向抽芯机构设计
侧向分型与抽芯机构是本模具最复杂的结构之一。成型塑件存在6个与开模方向不一致的倒扣,其中倒扣S1~S5在塑件外侧,模具采用了“滑块+斜导柱+弹簧挡销”的侧向抽芯机构,S6为内侧倒扣,倒扣深度10mm,面积较大,模具采用了“斜顶+斜推杆”的内侧抽芯机构[8]。模具侧向抽芯机构详见图2(b)、(c)、(e)。S6倒扣抽芯距离较大,为避免成型塑件在侧向抽芯时黏斜顶,导致塑件变形甚至断裂,侧向加强筋的脱模斜度不得小于2°。另外,由于S6倒扣方向不是和脱模方向垂直,属于倾斜式内侧抽芯,故斜推杆的底座中滑动导轨的方向必须与内侧抽芯的倾斜角度一致,即采用倾斜式导滑槽,否则,内侧抽芯时加强筋会断裂,见图9。
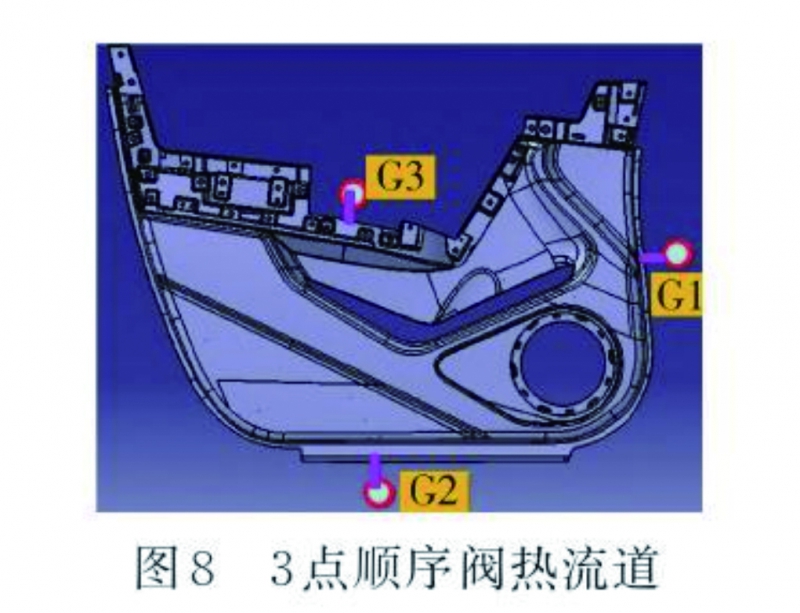
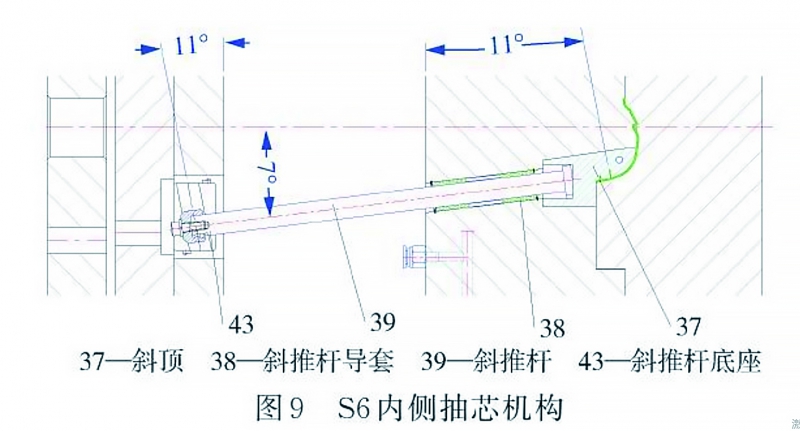
由于成型塑件对斜顶包紧力较大,在汽车左前门板模具斜顶的设计中,要防止侧向抽芯时塑件对斜顶的粘连,避免斜顶将塑件拉裂。
2.5 模具温度控制系统设计
成型塑件的冷却时间占成型周期的80%左右,成型塑件的填充不良和翘曲变形通常都是模具型腔各处的温度不合理造成的。对于汽车左前门板这种汽车最重要的大型内饰件,温度控制系统设计原则是使模具能够均衡冷却和快速冷却,为此冷却水道之间的距离必须合理,冷却水道距离型腔面应大致相等。
根据以上原则,汽车左前门板模具温度控制系统动模采用8组冷却水路,定模采用10组冷却水路,每条冷却水路都由直通式水管和隔片式冷却水井组成,详见图10,图中不同的颜色表示不同的冷却水路。模具冷却水路沿型腔等距离布置,纵横交错,呈网格状。冷却水流动方向与料流方向大致相同,进出水路长度大致相等,水道之间的间距保证在50~60mm之间,冷却水道距型腔面在20~25mm之间,冷却水道与推杆、推块等推件孔保持了至少8mm的距离[9]。本模具定动模设计了网孔镶件,动、定模网孔镶件和斜顶都单独设计一组冷却水冷却。快速且均衡的冷却系统大大提高了成型质量和模具的劳动生产率。成型塑件尺寸精度提高了一级,达到了MT3(GB/T14486—2008),注射周期缩短了约8%。
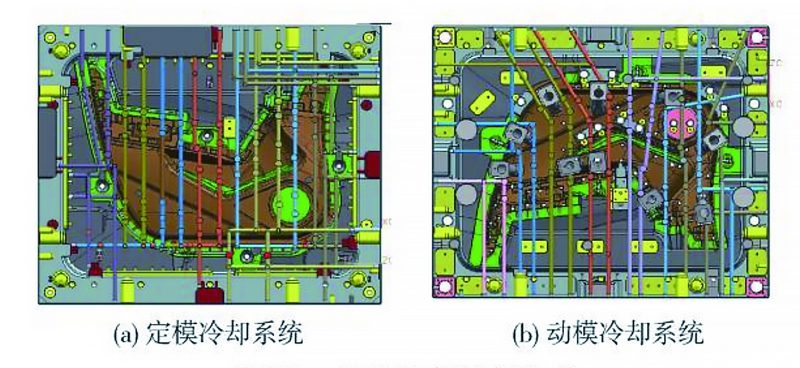
2.6 脱模系统设计
汽车左前门板模具脱模系统包括了推杆、推管、推块等所有的常规推出零件,各推件的位置详见图11,图中粉红色为推管(即司筒),绿色区域为推块,红色的为圆顶针位置。这些推出零件固定在推件固定板11上,推件固定板11由4个顶出油缸18驱动,其作用是将脱模零件推出并拉回复位,复位的准确度由行程开关17控制。因为是特大型模具,推件固定板须设计了6支导柱和导套,推件底板下方设计了6个限位钉。定模A板与复位杆接触的区域都设计了一块比复位杆大10mm的回复硬块,回复硬块选用油钢DF2(冷作工具钢),并经淬火热处理。模具设计了平衡布置的6支限位柱,顶出距离控制在110mm。推杆排布在包紧力大的位置,最大直径φ20mm。
由于斜顶37须依靠定模A板3推回复位,为了防止二者反复撞击使定模A板3产生凹陷,从而影响斜顶37复位精度,模具设计了复位杆先复位机构,即在复位杆的大端下方设计一块弹力胶27,见图2(f)。开模后,弹力胶27将复位杆26向前推出4mm,合模时,定模A板3提前4mm接触到复位杆26,从而提前将斜顶37推回复位,大大减小了斜顶37和定模A板3的撞击力度。
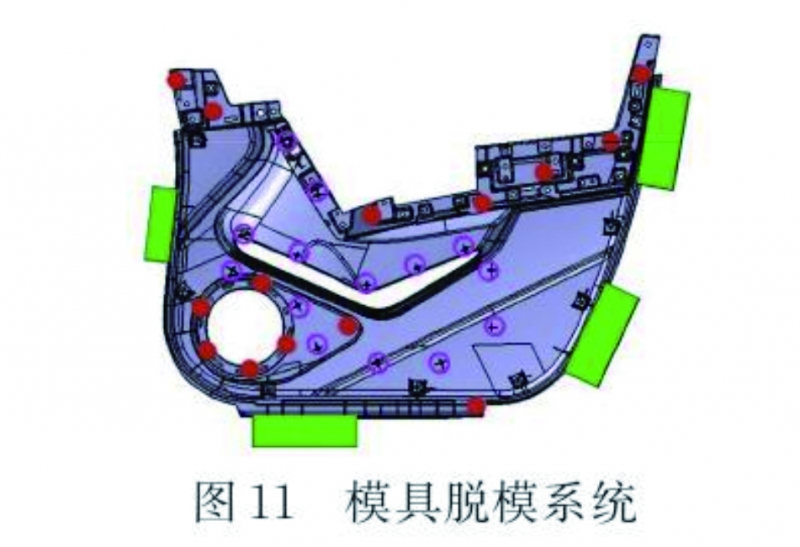
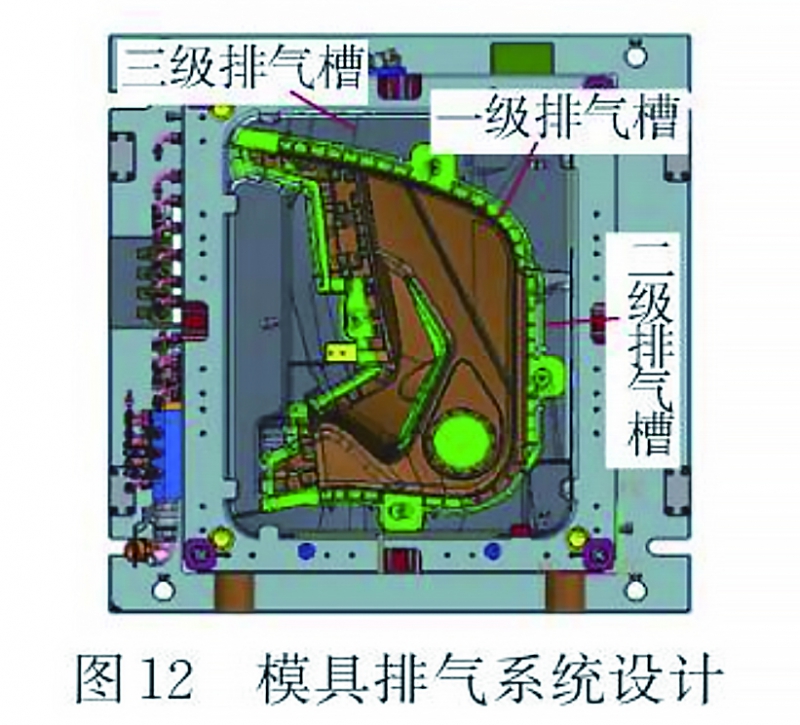
3 模具排气系统设计
汽车左前门板体积大,模具在注射成型过程中型腔内有大量气体需要及时排出,若排气不良,会严重影响成型塑件的质量,出现填充不良、困气甚至会烧焦塑件等成型缺陷。另外,成型塑件和型腔接触面积大,开模时外部气体必须及时进入型腔,否则就会形成真空,造成黏定模型腔或脱模困难。汽车左前门板注塑模具属于平板类零件,模具主要通过分型面排气,分型面上的排气槽沿型腔布置,由一级排气槽、二级排气槽和三级排气槽组成,排气槽开设在定模侧的分型面上,详见图12。一级排气槽深度0.04mm,二级排气槽深度0.5mm,三级排气槽深度1mm,排气槽宽度均为10mm。分型面上的排气槽加工方便,易清理,排气效果好。
4 模具工作过程
(1)注射充模:熔体依次经过一级热射嘴8、热流道板5、二级热射嘴6进入分型面之间的冷流道,最后由扇形浇口进入模具型腔。它分3个阶段:流动充模、保压补料、防止倒流。(2)冷却定型:在温度控制系统作用下,熔体冷却和固化。(3)开模及外侧抽芯:成型塑件固化至足够刚性后,注塑机驱动动模开模。在开模过程中,5支斜导柱拨动5个滑块对成型塑件进行外侧抽芯。开模距离500mm,由注塑机控制。(4)脱模及内侧抽芯:注塑机顶出油缸18推动推件固定板11,一边推动推杆、推管和推块将成型塑件推离动模,一边推动斜推杆39及斜顶37进行内侧抽芯。(5)合模复位:塑件由机械手取出后,顶出油缸18拉动推件固定板11复位,推出零件及斜推杆最后在复位杆26作用下准确复位,行程开关17打开,注塑机推动动模合模,模具开始下一次注射成型。
5 结论
(1)汽车左前门板喇叭网孔成型零件采用粉末冶金透气钢,提高了排气效果,改善了熔体流动,成功消除了喇叭网孔填充不良和熔接痕等成型缺陷。模具采用倾斜式导滑槽,有效解决了倾斜式内侧倒扣脱模难题。
(2)模具3个针阀式热射嘴采用顺序阀热流道智能控制技术(简称SVG),精确控制喷嘴的流量和压力,成功解决了大型薄壁塑件熔体填充难题,大大提高了成型质量。
(3)动、定模共18组水路呈网格状,纵横交错,有效达到了模具型腔各处的温度平衡,这种温度控制系统应用效果明显,注射周期缩短了约8%,尺寸精度达到了MT3(GB/T14486-2008)设计要求。
模具设计思路正确,结构先进合理,对大型、薄壁、精密、长寿命注塑模具设计具有较强的参考价值。模具顺利投产,运行安全,各项指标均达到设计要求。
参考文献 :
[1]张维合.注射模具设计实用手册[M].北京:化学工业出版社, 2011:112-177.
[2]张维合.汽车注塑模具设计要点与实例[M].北京:化学工业出版 社,2016:23-45.
[3]万鹏程.汽车保险杠注射模浇注系统设计与成型参数优化[M].昆明理工大学出版社,2011,58-75.
[4]沈忠良,郑子军,肖国华,等.汽车中控面板IMD 成组模具设计 [J]. 工程塑料应用,2017,45(1):70-75.
[5]吴梦陵,Moldfow 模具分析实用教程[M].2 版.北京:电子工业出版社.2018.
[6]张维合.基于顺序阀热流道技术汽车导流板注射模设计[J].塑料 科技,2018,46(12):100-105.
刘彦国.塑料成型工艺与模具设计(第4版)[M]. 北京:人民邮电出版社,2018.
[7]周纪委,王明伟.汽车尾门左右窗框饰板气辅注塑模具设计[J]. 中国塑料,2023,37(11):141-148.
[8]CGLi,Yuguang Wu.Evolutionary optimization of plastic injection mould cooling system layout design[J].IEEE 2010:693-696.
[9]张云.汽车通风管接头注塑模具设计[J].塑料,2023,52(05): 74-78.
[10]刘祥建,周佳睿,姜劲.基于Moldflow的按钮开关帽注塑模具设计[J]. 工程塑料应用,2023(06):97-102.
[11]Ren Jong,W Wu,Ch Liu,et al.A Collaboration NavigationSys- tem for Concurente Mold Design[J].The International Journal of AdvancedManufacturing Technology,2009,40(3/4):215-225.
[12]赵利平,张维合,彭新华,汽车座椅侧护板注塑模具创新设计 [J]. 中国塑料,2023,37(10):139-143.