虽然同向旋转双螺杆设备的几个基本概念在二十世纪早期就被Wuensche [1]和Easton [2, 3]申请专利,但同向旋转设计是基于Erdmenger元件剖面自清洁几何学原理的,此设计是目前市场上使用的所有双螺杆挤出系统的理论基础。
自清洁剖面元件的初步设计和开发可见于德国专利862,668,此专利于1952年被W. Meskat和R.Erdmenger申请,优先期到1944年(没有美国的专利)。那个时候此设计的目的是混合高粘度的液体,如聚合后反应产物。
上述专利以及相关的一系列专利(属于Erdmenger或他在Bayer的某个同事),确定了基础设计参数,并最后于1950年由Werner和Pfleiderer开发和商业运用ZSK双螺杆挤出机,以及之后50多年出现了很多复制机型。此设计的关键特征在于其两根螺杆的自清洁性能。它能消除物料在挤出机工艺段行进时的停滞和可能导致的降解。
自清洁几何学螺杆发明的价值在于这对于同向旋转双螺杆挤出系统来说是一个基础专利,而此双螺杆系统目前被广泛应用于塑料、食品和化学领域。(关于最近的发展,请见由Andersen发表的ANTEC 2009论文[4]和White于1991年发表的Twin Screw Extrusion [5]。)
自从同向旋转双螺杆挤出机基础理论被提出后,有了一系列技术上重大的持续改进。包括Bierdel发明的一系列新的螺杆元件[6],有更高自由容积的双头剖面元件(最初在Erdmenger专利上使用的是自由容积较低的三头元件),输送能量更高效的新的螺杆芯轴,以及最新的工艺应用技术[7]。而其中最重要的一个步伐是高转速/高扭矩配混技术基本面的识别[8]。这是由Heidemeyer于2000年3月28日申请的美国专利6,042,260的基础。
高扭矩,高转速双螺杆配混技术
自从第一代高扭矩、高转速ZSK MegaCompounder (Mc)于90年代中期被推出市场以来,新的能量传输技术(传动箱、芯轴和材质)允许在Mc比扭矩11.3的基础上,额外增加50%升级到比扭矩为18的Mc18(PVF: Md/a3[Md = 扭矩,a = 中心距])。
提高能量传输能力的影响在于配混行业产能(生产率)的显著提高,更高的效率和系统适应度。
此项技术成功的关键在于提高螺杆转速的同时,提高能量(扭矩)传输能力。在高速运转下的一个系统在某些点会产生足够额外的能量,导致所加工物料的降解。图1阐明了此点。它表明对于任何Do/Di(外径和内径之比)的螺杆,平均剪切率(能量输入)会随着螺杆转速的提高而线性提高。所以所加工物料的温度也会相应的提高。但是,由于双螺杆挤出机首先是运行在一个饥饿吃料模式之下,更高的能量传输能力可使物料在挤出机中能有更高的填充度,所以在同样转速下有更高的产能。(例如图1比较了低填充度高点和高填充度低点的情况。)反过来,填充度的提高对降低熔温也有积极效果。
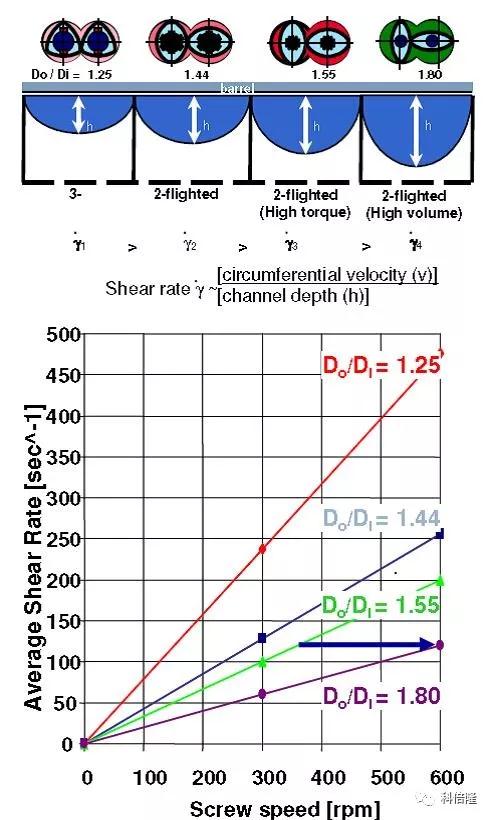
图1:Do/Di和RPM对剪切率的影响
如图2中螺槽所示,更多的物料进入螺槽的中部,此处螺槽较深(相比于低产能)。它转而使所有物料的平均剪切率下降,结果导致每公斤物料的能量输入(如总温度)降低。所以工艺人员有足够的弹性来使挤出机运行在更高的转速之下,同时熔温不会超过物料的限定温度。例如,图3显示了30%玻纤增强PA6,使用3代ZSK45挤出机ZSK Mc(比扭矩为11.3),ZSK Mc Plus(比扭矩为13.6)和ZSK Mc18(比扭矩为18)的比较。
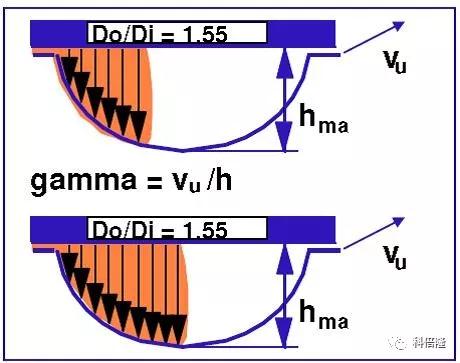
图2:填充度对平均剪切率的影响
在图3的上部,显示了3代ZSK的产能和转速关系。更高比扭矩(ZSK Mc 18)有最高的产能。而且,如图的下部显示,它同样有着最低的比能耗。从两个结果(更高的产能和更低的SEI)的结合来看,这个数据显示了使用最高比扭矩的设备,有着双倍的经济效益。第一,从这几代机型来看,因为更低的SEI(比能耗 – 同样也写作Sme:比机械能),更高比扭矩PVF系统有更高的产能,此更高的产能高于比扭矩的提高而导致的线性提高。(在这个具体例子上,PVF只提高了略高于50%,但产能提升率则在70-80%。)产能提升的一般指导在于:现在的产能 = 旧的产能 × (PVF高扭矩/PVF低扭矩) × (SEI低扭矩/SEI高扭矩)。第二,这里还存在一个额外的每公斤比能耗的节约。
另外需要额外强调一个关于高扭矩高转速配混挤出机的要点。这些机器不须一定要运行在最高转速之下,即使这个转速为设计下的转速。如图3所示,产能提高和能耗节约处于任何一个转速之下。但是,这里有另外一个能耗/转速的协同作用,有着第二个产能的非线性提高因素,即生产经济学。
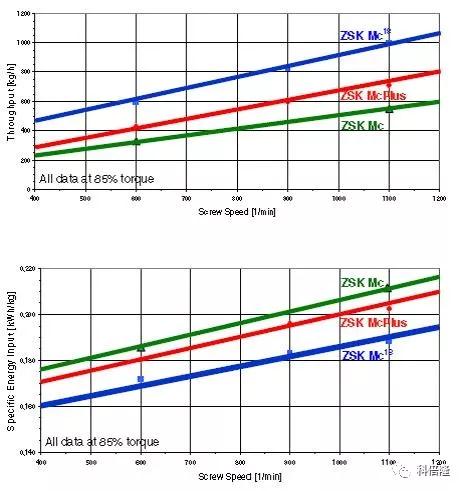
图3:30%玻纤增强PA6在不同转速下,使用3代ZSK45挤出机产能和SEI的比较
这种关系[8]的一个例子可在图4中发现。图4中显示3种比扭矩机型产能对于螺杆转速的曲线关系。SEI同样作为参数因子。此数据来源于在ZSK 58 Mc (Do/Di = 1.55, torque= 1250 N-m/shaft, PVF = 11.3)上加工ABS 接枝共聚物(Acrylonitrile-Butadiene-Styrene)。69%和90%的2个曲线比较了在90%扭矩运行下在低扭矩机型ZSK 58 SuperCompounder (Sc) (Do/Di = 1.55, 960 Nm/ shaft, PVF 8.7)和在Mc (1250 N-m/shaft)上的情况。此2款机型有着30%的扭矩差距。对于此例,选择了一个恒定的转速700rpm。在69%扭矩曲线上(在960 Nm芯轴挤出机上90%扭矩运行),产能在660kg/h,SEI在0.19kw-h/kg,熔温为290°C。提高产能到90%扭矩曲线,可发现SEI从0.19降低到0.177kw-h/kg。产能有40%的提高,到930kg/hr,不仅仅是预计的30%的提高。同时熔温也降低了15°C到275°C。这尤其有利于热和剪切敏感物料。它们可以运行在高产能之下,同时有着较低的熔温。
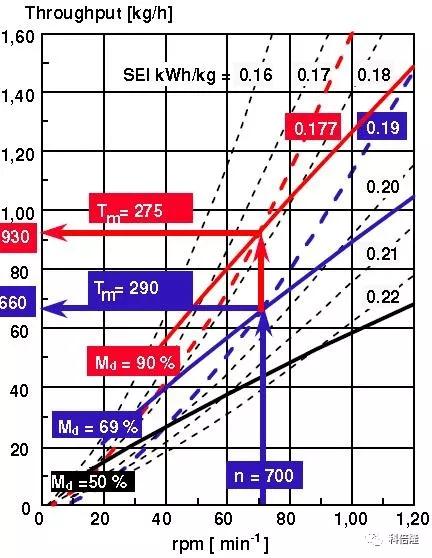
图4:高扭矩的利用率
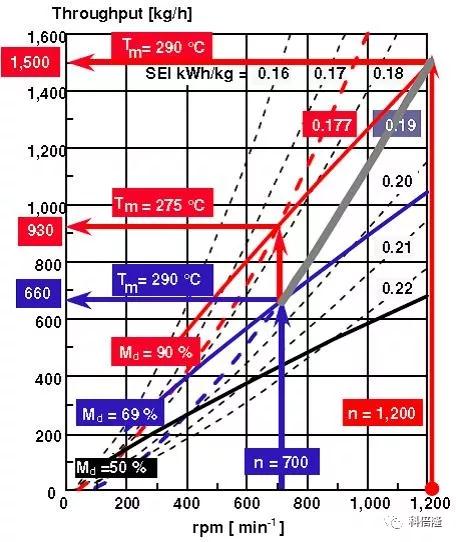
图5:高扭矩和高转速的利用率
所以,如果290°C的初始温度是安全的,那么从图5可看出高扭矩和高转速结合的显著影响。转速提升到1200rpm时,产量可达1500kg/hr,此时出口温度为290°C,这个温度与低扭矩操作系统相同。但产能则从原来的660kg/hr提升了150%多。
通过产能提高150%多,得到的生产率和经济提升的影响是显著的。但是,对寻求安装新生产线的厂家来说,这里也有另外一个潜在选项。如果您不需要1500kg/hr的产能,只需运行在原来的660kg/hr,那么您可以选择一款更小的机型。比如,新的ZSK 45 Mc18,与ZSK 50 Mc相比有着高于10%的功率,与ZSK 50Mc+相比有着略微低的功率,如图6所示。但是,正如图7中显示的,与更大的机型相比,它其实可以满足相同的或更高的产能要求。
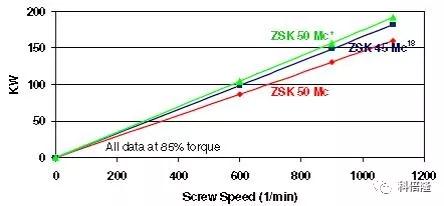
图6:ZSK 45 Mc 18和之前几代更大外径的ZSK 50挤出机有效功率的比较
如图3中显示,在加工30%玻纤增强PA6的时候,ZSK 45 Mc18可以满足600kg/hr @ 600 rpm以及970kg/hr @ 1100 rpm的产能。假定在ZSK 45 Mc Plus上运行,SEI为0.18kwh/kg @ 600 rpm以及0.202kwh/kg @ 1100rpm,那么在更大的机型ZSK 50 Mc Plus上,产能约为580kg/hr @ 600rpm,此产能ZSK 45 Mc18就能满足。若在ZSK 50 Mc Plus上产能约为950kg/hr,那么在ZSK 45 Mc18上就能达到同样的或略低的产能(如图7)。
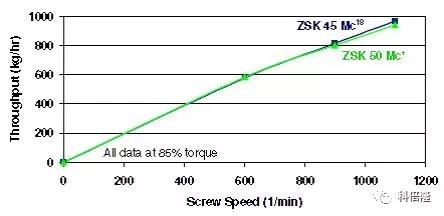
图7:不同转速下ZSK 45 Mc 18和更大机型ZSK 50 Mc+产能的比较(30%玻纤增强PA6)
喂料增强技术(FET)
高扭矩挤出工艺只是一种经济实用的技术,目的是充分利用所有的功率,达到工艺的优越性。不过,很多配混加工包含了低堆积密度的材料,比如非压缩的亚微粒滑石粉。如果不去除这类原料内部的大量空气,则很难将其喂入挤出机。而且,堆积密度越小,原料越容易流态化,导致密度进一步降低,加剧喂料问题。处理易流态化原料的常见操作步骤是:从储存容器运送到喂料机,从喂料机喂入双螺杆挤出机,进入挤出机的喂料输送段。一些方法可以降低流态化的倾向,比如从储料到喂料使用浓相输送,挤出机喂料口高度的最小化,料斗增加排气口,增加挤出机喂料段输送区的长度。但这些方法最终都会因为体积受限,远远无法达到最经济的产量。
FET喂料增强技术在ANTEC2011[9]上已经做了详尽的介绍,在EUROTEC2011上我们再次为大家展示。先来简单描述一下其原理。
FET的目标是针对难喂料的原料,增加喂料段的进料能力。方法就是通过增加物料和筒壁的协同摩擦系数,减少或消除筒壁的打滑,改进输送效率。
为提高协同摩擦系数,增强输送效率,我们对喂料段特殊设计的多孔透气筒壁施加真空(而不是对原料抽真空),让部分筒壁上附着一层原料。因此这段多孔筒壁上的孔径与原料粉末粒子的直径之间的关系非常重要。此外,最佳的真空度取决于粒子的直径和形状。如果粒子能够穿透筒壁上的孔,那么喂料效率就会降低。不过,穿透孔洞的粉末粒子也能够被真空管线的压力再次吹回。相比于穿孔粉末带来的麻烦,聚合物熔体或者其他液体则更加的关键。这些物料可能覆盖多孔表面,甚至穿过孔洞,堵塞多孔结构。
图8描绘了FET的工作原理。通过多孔材料来施加真空,在聚合物或者填料经过FET筒壁段的嵌件时,周围的空气被抽走。因为空气被抽向嵌件,连带着粒子也向嵌件表面运动。空气能通过孔隙,但粒子不能,于是覆盖在多孔材料表面。这层粒子,或者称之为浓缩聚合物粉末形成的滤饼,能增加筒壁和物料之间的摩擦系数。旋转的螺杆不断更新因真空而粘附在筒壁上的物料。而且,粉末的密度在通过嵌件之后也增加了。这两种效应的共同作用,带来了更高的输送效率。
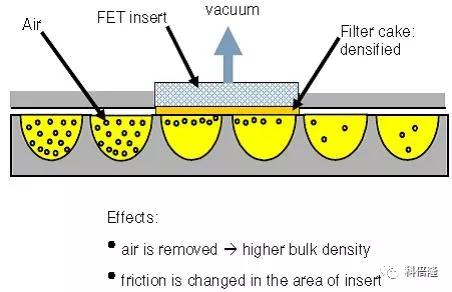
图8:FET操作原理
通过FET可以增加总体产量[9],但并不止于此。与之前详述的高扭矩配混机型可以提供的优势类似,FET能增加高填充聚合物配混线的产能,而其它条件不变,其结果就是生产单位产品的能耗下降。更低的单位能耗又能降低产品的温度,减少降解,减少稳定剂的消耗。
图9描绘了这一点。这是用科倍隆最新一代Mc18 ZSK45挤出机加工40%滑石粉(Luzenac1445)填充PP的数据。如果没有FET技术,挤出机的高扭矩就无法发挥。而应用了FET技术之后,系统运行时充分利用了85%的扭矩,产量增加超过50%,出料温度显著下降。
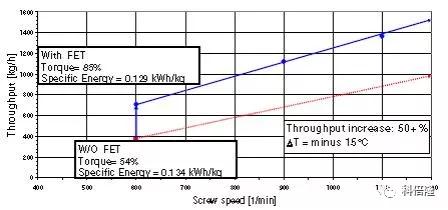
图9:改进喂料量的影响和物料温度
总结
在物料能运行在高转速下时,可以达到很高的产能。但是对绝大多数系统来说,对现有机器简单的提升转速不能达到期望的目的。在产能提升时,产品性能可能下降到及格线以下。但是,在高扭矩下提高转速,聚合物加工工艺经济能显著提升,而不损失产品性能。另外,当处理低堆积密度原料遇到困难时,FET可以给予帮助,以充分利用双螺杆挤出机的最大能力。(文章来源于网络)
作者
Paul G. Andersen,Coperion Corporation, Ramsey, NJ
Frank Lechner, Coperion GmbH, Stuttgart, Germany
参考文献
1. A.Wunsche, German Patent 131,392 (1901)
2. R. W.Easton, British Patent 109,663 (1916)
3. R. W.Easton, U.S. Patent 1,468,379 (1923)
4. P.G.Andersen, Chi-Kai Shih, Mark A. Spalding, Mark Wetzel, Tim Womer, SPE-ANTECTech. Papers, 55, (2009)
5. J. L.White, Twin Screw Extrusion: Technology and Principles (1991)
6. M.Bierdel, Co-Rotating Twin-screw Extruders: Fundamentals, Technology, andApplications (2007) K. Kohlgrueber & W. Wiedmann Editors
7. P.G.Andersen, Plastics Compounding, D.B. Todd ed., 71-124 (1998)
8. P.G.Andersen, E. Haering, K. Kapfer, SPE-ANTEC Tech. Papers, 43, (1997)
P.G. Andersen, M. Hoelzel,T. Stirner, SPE-ANTEC Tech. Papers, 57, (2011)