近代注塑机的设计日趋完善成熟,为各项注塑工艺参数的调整提供十分方便的条件。尽管不同的注塑机调节方式各有所异,但是对于工艺参数的设定和调整项目基本是相同的。
在注塑机上的注射压力、保压压力都是通过调节注射系统的液压油路系统来实现的。因此, 在注射充模阶段或保压阶段,任何影响油路系统压力稳定的因素都会引起注射压力和保压压力的波动,都将影响最终充模压力曲线和注塑产品的质量。
注塑机在注塑周期中各阶段所消耗的能量是大不相同的,如图 1 所示看见,注塑工艺过程中的大部分功率消耗在注射充模、保压补缩和塑化阶段,其中以注射功率消耗为最大。注射功率和驱动油泵电机功率之间关系式 ( 1) 所示:
Ni = ηHKoNm ( 1)
式中:
Ni─ 注射功率,KW ;
ηH─系统效率;
Ko─电机超载系数;
Nm─电机功率,KW;
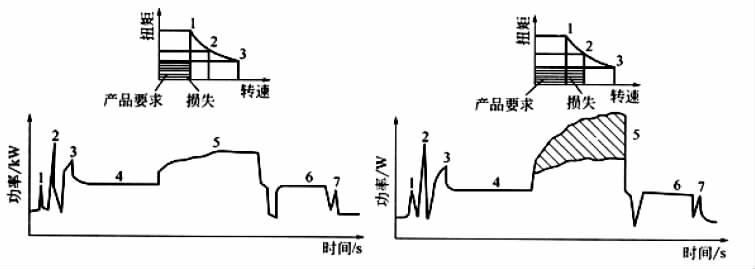
图1、注射成型周期中功率消耗曲线
注:1-模具闭合时的功率消耗;2-注射座整体前进喷嘴和模具接触时的功率消耗;3-注射时功率消耗; 4-保压阶段的功率消耗; 5 -塑化时的功率消耗; 6-注射座后退时的功率消耗;7-启模时的功率消耗;
注塑过程的功率消耗见表 1。
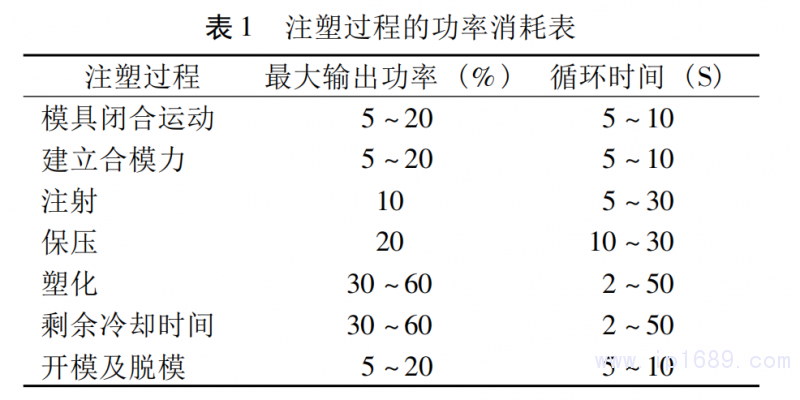
注射功率由注塑速率和注射压力所决定,如式 ( 2) 所 示 :
Ni = Qi Pi ( 2)
式中:
Qi ─注射速率;
Pi ─注射压力。
在工艺操作中注射压力和注射速率尽量与熔体在指定的工艺技术条件要求所消耗的注射功率相接近。
注塑机整体能耗最主要的两大部分为驱动动力部分的液压系统和注塑机筒外的加热系统。文章针对液压系统为节能改造的对象,对传统液压驱动式注塑机的液压系统能耗进行分析,并对定量泵电机组动力系统的节能特点进行分析,得出电液伺服系统的节能解决方案。
2.定量泵式注塑机节能特点及能耗分析
采用伺服电机驱动定量泵式系统的注塑机最主要的节能有点有以下几个方面:
( 1)节能效果明显示。相比传统的注塑机具有极佳的节能效果,节能率最高可达 40% - 80% , 如图2所示,特别是在保压和冷却阶段,效果尤其明显。实际上节能改造最终的效果节能量直接 取决于设备的负载大小,以及功率消耗中保压和冷却工序所占整体功耗的比例大小。
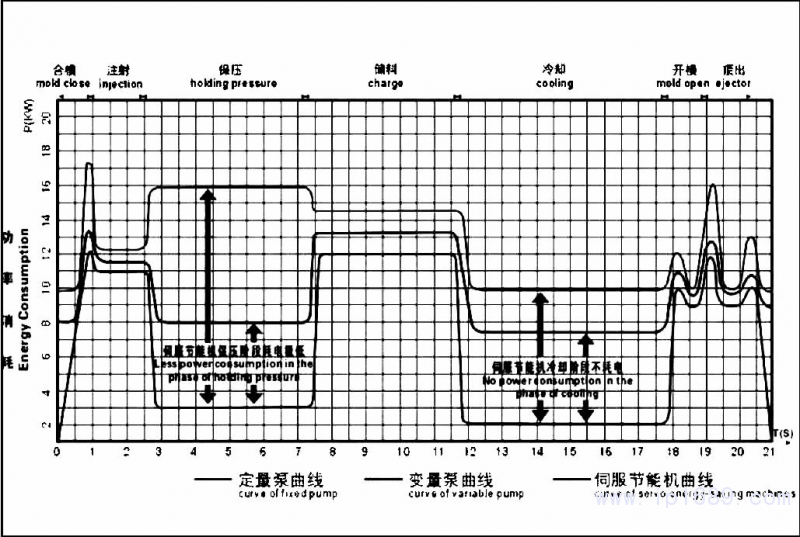
图2、功率消耗对比示意图
( 2)响应速度快。响应迅速高效,借助于高性能伺服电机,启动快速,减少动作切换时间,加快动作节拍,可提高生产效率 10%-15% ,见图3。
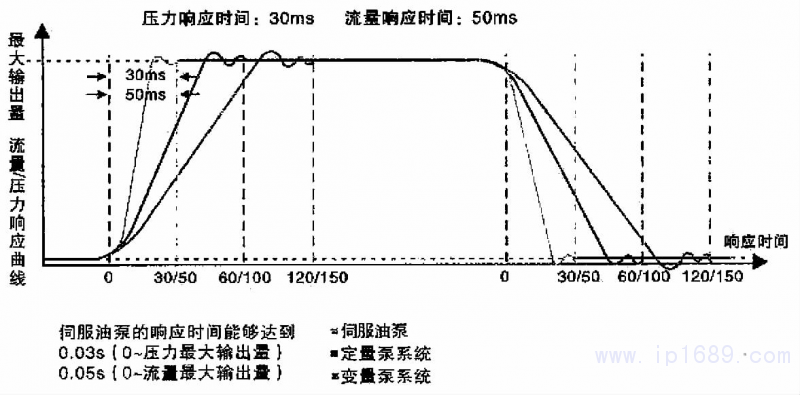
图3、系统响应对比示意图
( 3) 重复精度高。低速稳定,制品重复精度高,采用伺服电机系统,对射胶压力及系统流量进行闭环控制,相比传统液压动力控制系统稳定性及重复精度更高,提高产品成型质量。重复精度误差一般保持在 0. 3% 以内,有效降低了产品的废品率,有助于企业控制生产成本,见图 4。
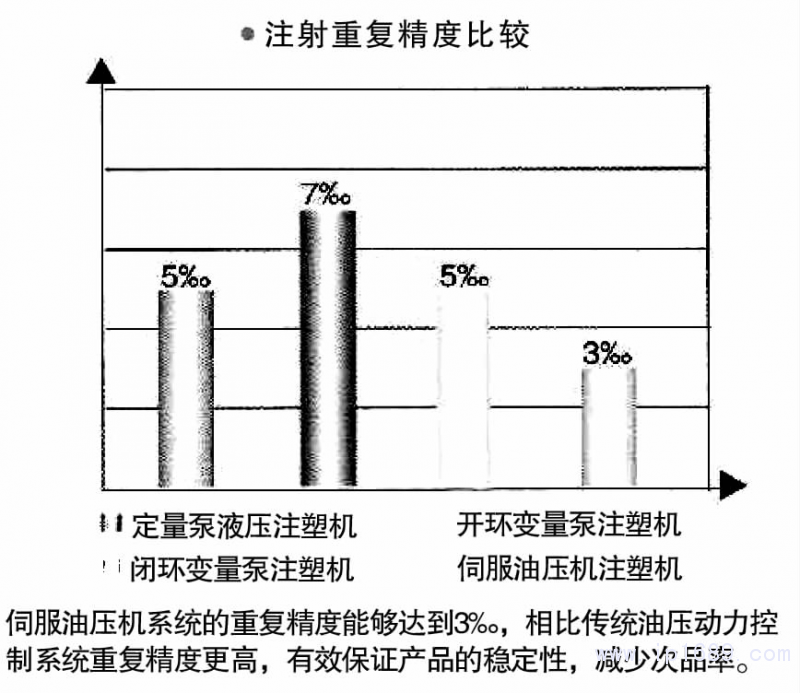
图4、注射重复精度比较示意图
( 4)延长液压系统寿命。伺服系统能量损耗较低,降低设备运行噪音和故障率。延长液压系统元件以及液压泵使用寿命,综合降低了设备的运行使用成本。
( 5)有效控制油温。伺服电液改造后大大减少了系统产生的热量,有效控制了油温,见表 2。
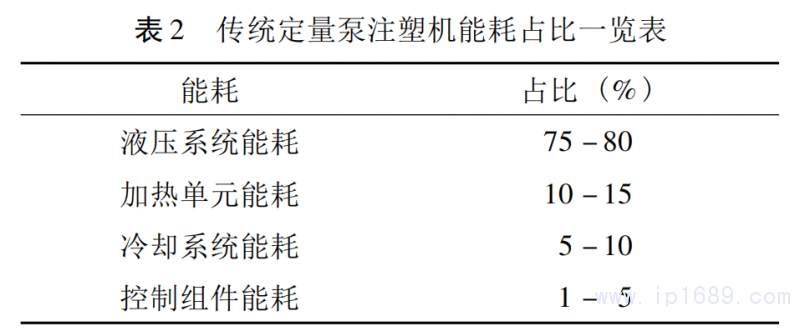
其中最大能耗部分: 液压系统用电量占注塑机的 75% 以上。经分析发现,在保压补料的冷却阶段,对于传统的定量泵系统配置注塑机来说该阶段无用功能耗将非常巨大。在该阶段液压动力系统不仅需要保持注射压力足够和保压冷却补料的需求,还应保证下一周期中正在塑化中的原料的性能与压力稳定。传统的液压泵系统受溢流阀开关的控制,很难保证执行系统中压力的波动范围及熔腔内保压过程的稳定。
3.注塑机电液伺服控制系统的结构设计
电液伺服系统中的控制系统可采用单片机或者运放为主的电子线路系统,两种方式均能够很好的完成注塑工艺中各个阶段对于驱动系统的实时控制任务。改造前的注塑机液压系统如果是传统电磁方向阀和压力阀控制系统,注塑机主控制器向控制阀输出的是电流信号,如果是比例阀控系统则注塑机主控制器或可编程控制器向比例压力阀和比例流量阀输出的控制信号可以是可变脉冲宽度调节信号,通常是24V频率1KHz,电流值一般为0.1-1A,底电流是为了克服电磁阀开启动作死区。在改造过程中注塑机原始液压系统油路结构不需要进行特殊改动,普通异步电机和定量泵需更换成为伺服电机以及高速高压泵,在油泵出口法兰盘处外接压力传感器。从注塑机控制板输出的原始信号若是电流信号,则需要配置信号转换板,将其转换成电压信号,并且可以实现调整液压系统底压底流大小的作用,具体系统结构图如图 5 所示。
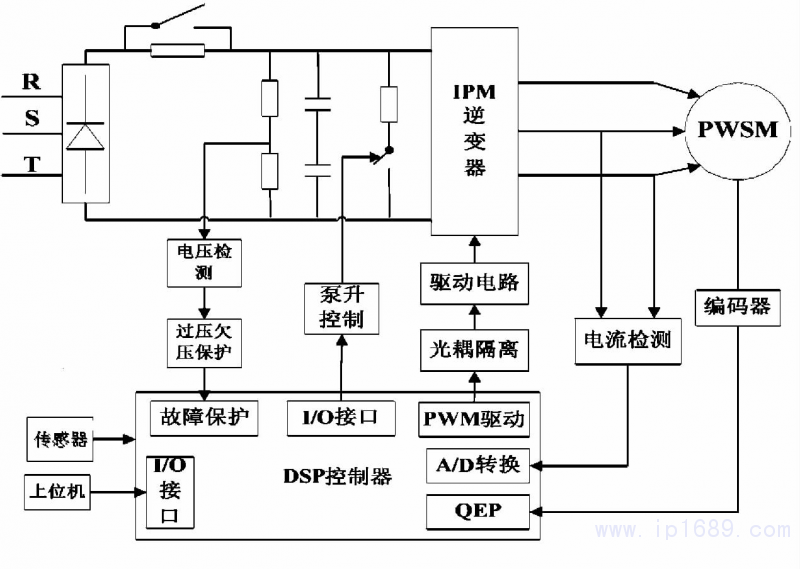
图5、伺服驱动器控制系统结构图
改造后,注塑机主控制电路板向比例压力阀和流量阀输出的控制信号,通过信号转换板输入到伺服驱动器中,再通过伺服驱动器来控制伺服电机带动定量泵以达到直接控制系统压力与流量的目的,其本质就是将原来液压系统回路的阀控系统改为了泵控系统。伺服驱动器采用 PI 方式对接入的压力和流量信号进行调节,通过调节伺服电机的输出转矩和转速,从而调整油泵电机的输出流量和压力。同时采用电机上的旋转编码器和油路中的压力传感器进行反馈,形成高精度的双闭环控制,不仅可以满足注塑机在各个工序中所需的油压大小和流量速度,而且在此基础上大大提高了控制精度,从而得以提高生产效率。并使设备在达到工艺技术要求的基础上更改动力系统工况从而最终达到节能效果。具体控制方框图如图6所示。
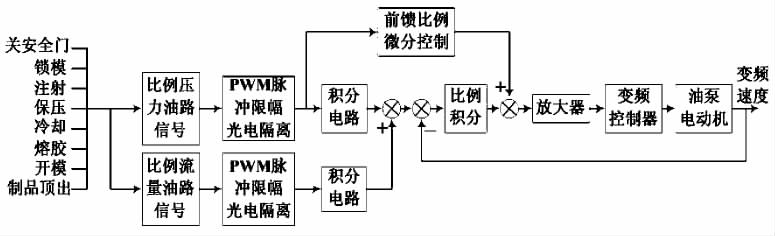
图6、电液伺服系统控制方框图
可见,改造后的电液伺服系统是一套采用前馈PD控制结构的典型伺服电机电液控制系统。该控制系统中伺服跟随控制器信号,来自于注塑机主控制板对原始比例压力与流量阀的压力及流量控制输出信号。经过光电隔离和脉宽调制电路后整形为满足工艺操作要求的序列脉冲随动信号,这里增加了前馈PD控制和PI 控制模块用来克服伺服控制跟随信号给伺服电机造成的纯滞后时间,而前馈PD控制模块的作用则是为了加快变频速度的响应以提高系统的动态响应指标,PI模块则是用来改善系统静态误差。采用这种控制电路时可使得原注塑制品工艺周期平均缩短1S左右,因而可以提高生产效率。
4.注塑机电液伺服控制系统的特点
注塑机上的电液伺服闭环控制的核心在于完全根据系统的需要,随动提供流量和压力,将原来开放式阀控液压传动调节的系统方式更改为反馈控制的泵控驱动动力直接调控方式,从而实现按需供油节省了原来开放式的液压系统中的大量溢流损耗。完全满足工艺技术对注塑设备的要求,并同时达到塑料成型快速、精确和节能的效果,而该液压系统控制策略的核心本质就是带压力补偿的流量控制方式控制液压系统动力驱动单元,并用泵出口的压力反馈闭环来消除对系统流量估算的控制精度。
在系统中伺服电机的转速控制着液压系统动力单元的输出流量,当系统中的流量建立了压力之后,则由伺服驱动器的PID系统控制伺服电机转速稳定油压。液压系统中的流量压力实际上均由伺服驱动器对伺服电机的转速控制,最终达到对液压系统动力输出单元的实际控制效果,在系统油压还没有得到完全建立的时候,液压回路中的管路尚有部分实际空间,此时用液压系统中的流量正比与伺服电机连带柱塞泵同轴转速的估算方式来控制运转油泵伺服电机组的转速。待管路很快充油完毕后,液压油会受到管路的限制从而使系统很快建立油压。当油压建立起来之后,利用伺服驱动器 PID 调整油泵伺服电机转速来最终将系统压力控制在注塑机控制板中输入的系统给定值。
5.总结
节能改造系统实际可总结为两点: ①系统压力未到时,伺服油泵电机组转速由流量指令控制;②系统压力到达后,伺服油泵电机组转速由压力指令和压力反馈的差值控制。
液压系统最终的控制对象就是压力和流量,几乎所有的液压控制系统都是围绕这两个物理参量为核心来寻找更新、更好、更精确的控制方法,采用该电液伺服系统可以对注塑机液压系统的压力和流量完成双闭环反馈控制,从而达到尽可能的保证了注射工艺对设备的压力和流量要求,补偿系统高压时液压泵的泄漏所产生的流量误差,使得流量控制更加准确,并实现了按需供油节省了大量溢流损耗。