摘要:提出一种基于吹塑成型工艺的塑料件结构强度分析方法,以更合理精确地分析计算吹塑件的结构强度。此方法将吹塑成型与结构分析顺序耦合应用Abaqus/Explicit对塑料圆管进行吹塑成型模拟,获得吹塑件的形状和非均匀厚度以及残余应力,然后将吹塑成型件导入到Abaqus/Standard中,并将非均匀厚度场和残余应力场映射到该吹塑件分析模型上,进行强度分析,评估其结构强度性能。以聚对苯二甲酸乙二醇酯PET塑料瓶为例,应用上述方法对吹塑成型的塑料瓶进行精确结构强度分析,能够指导塑料瓶的结构设计和成型工艺参数设置。
当前塑料行业发展迅速,应用领域涵盖了饮料、饮用水、药品、食品、化学品和汽车行业等[1]。一般情况下,制造商需要在有限的时间和成本里,设计并生产新型塑料产品。然而,有限的时间及成本往往限制了设计师的思路,难有创新。但随着计算机技术的发展,有限元仿真技术的应用可使设计时间和生产成本大大减少[2-3]。
在塑料件的生产中,吹塑成型是最常见的成型方法之一,其非常适用于生产热塑性中空塑料制品,比如矿泉水瓶、饮料瓶和油箱等吹塑成型模具只需凹模,因而设备造价低,适应性强等,在饮用水行业中应用十分广泛[4]。随着消费者的喜好变化,吹塑制品形状愈加复杂,越来越难保证其壁厚的均匀性,同时,吹塑成型导致的塑件残余应力,也影响着塑件的结构强度[5-6]。
图1所示的PET材料塑料瓶,需采用有限元方法分析其在正常使用、运输、跌落和挤压过程的安全性,以保证吹塑制品不会发生破裂。传统的有限元方法是将图1水瓶塑件作等厚件建模分析,忽略了厚度的非均匀性,特别是薄弱区域,导致分析结果并不能找出破裂风险区域。故本文提出一种基于吹塑成型工艺的塑料件结构强度分析方法,其能够考虑吹塑成型后的不均匀厚度以及残余应力对塑件的结构强度的影响,即先用有限元软件Abaqus的Explicit模块对塑料管进行吹塑成型模拟,获得塑件的形状、非均匀厚度以及残余应力,再把此塑件导入到Abaqus/Standard中,并映射厚度场和应力场,精确合理地分析计算塑件结构强度。
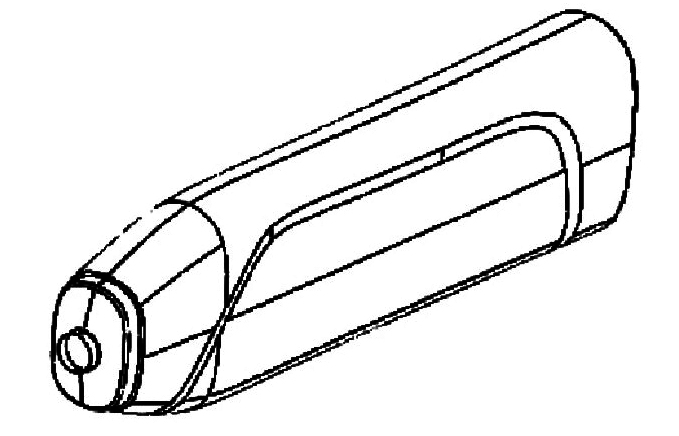
图1塑料瓶几何模型
1吹塑成型分析
1.1吹塑成型建模
本文吹塑成型方法采用Abaqus/Explicit显式算法进行求解。显式算法求解速度快且收敛性良好[7]。吹塑成型网格模型如图2所示,对模具凹模划分网格,并把采用壳单元的吹塑管装配于模具中间。
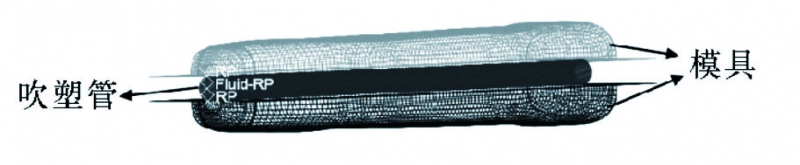
图2吹塑分析有限元模型RP表示参考点
1.2材料和边界
表1PET塑性参数
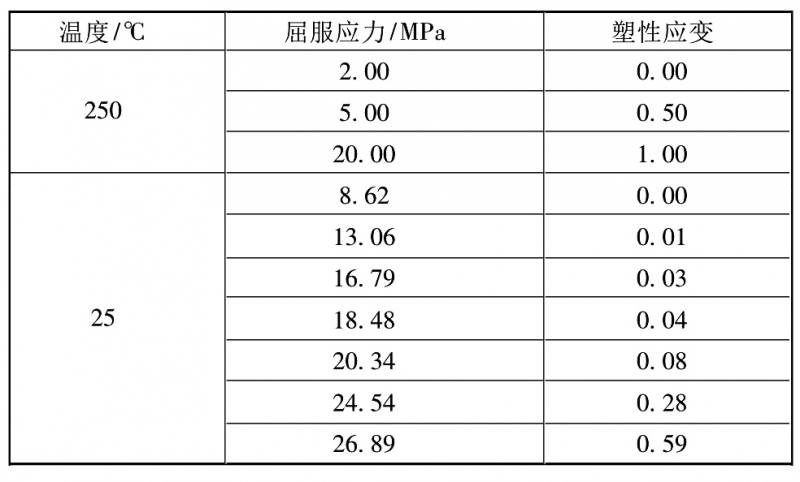
在高温250℃吹塑管弹性模量为10MPa,泊松比为0.3,密度为0.94g/cm3,并采用表1提供的250℃对应的PET塑性参数。
在吹塑模型中,模具均设置为离散刚体,仅吹塑管为变形体。设置两个分析步第一个分析步为对图2的上下凹模闭紧合模第二个分析步在约束吹塑管尾部的情况下进行吹塑成形。
在吹塑过程中,吹塑管与空气之间存在着热交换,参考文献[8]设置热交换系数为500W/mm2·℃。同时,设置模具与吹塑管的摩擦因数为0.4。
1.3 分析结果
1.3.1 动能/内能比
通过动能/内能比判断吹塑成型是否为准静态分析。模型的动能-内能曲线如图3所示,可以看出随着时间的增加,模型的内能总体成上升趋势,且在合模步骤完成后继续吹塑时上升幅度较大,动能在吹塑模拟过程中几乎为0。动能除以内能则绘制成图4所示的动能/内能比[9],可知随着动能/内能比趋于平稳,其值小于5%,由此可判断此吹塑成型分析结果符合准静态过程。
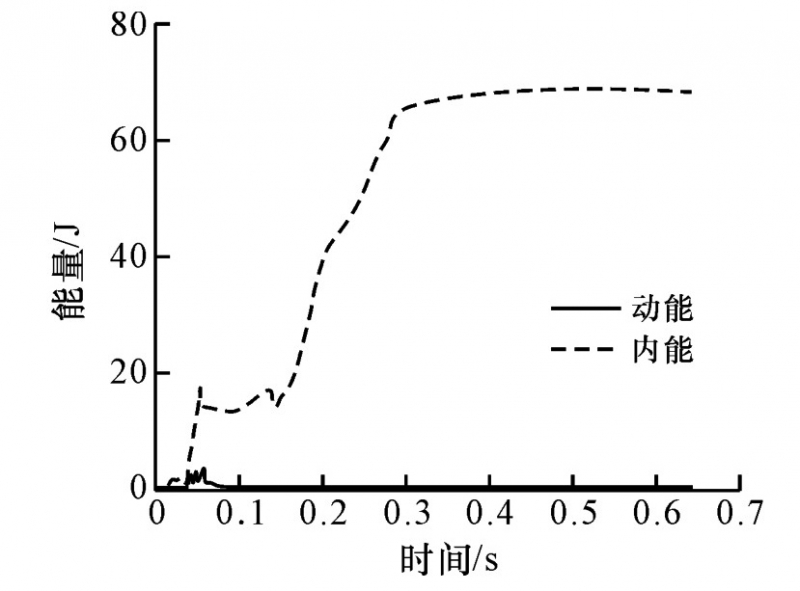
图3吹塑成型中动能与内能
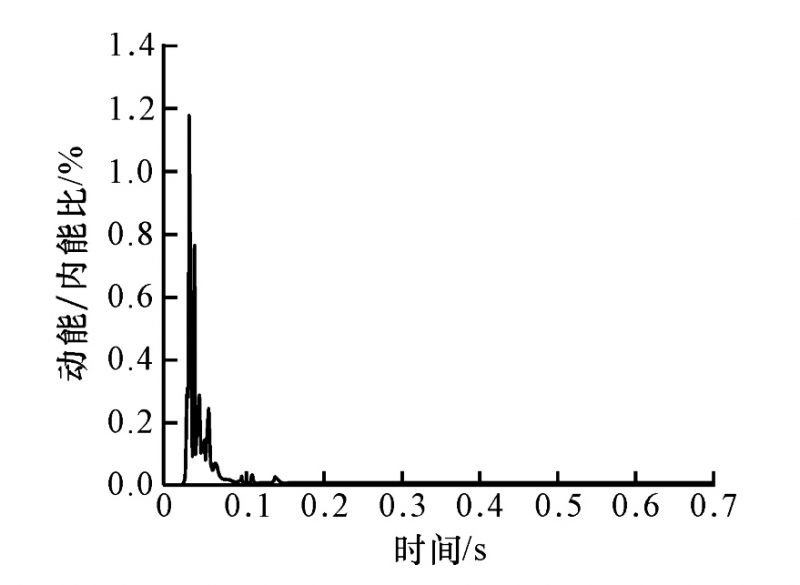
图4吹塑成型中的动能/内能比
1.3.2厚度分布
吹塑件厚度分布如图5所示。由图可知吹塑件并非等厚件,非均匀厚度分布范围约为0.5~9.5mm,瓶身的厚度相比瓶口较小,瓶身左右两侧的厚度较小,上下两侧厚度较大。把图5中每个节点对应的坐标和厚度值写出,用于后续联合仿真的厚度映射。
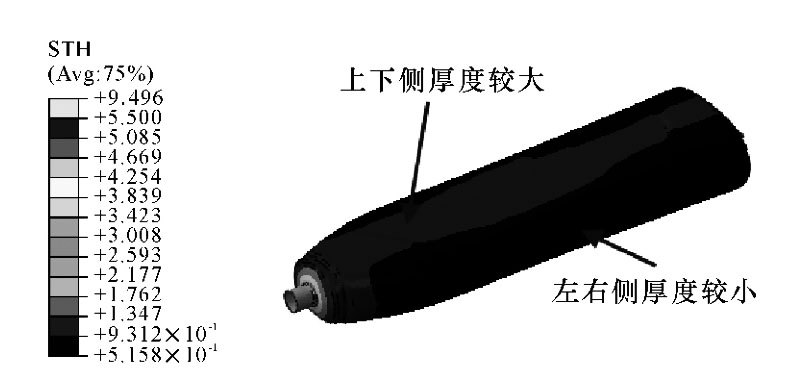
图5塑件厚度云图
2结构强度分析
2.1强度分析模型
因隐式算法求解非线性静力更为精确[7,9],故针对图6结构强度分析模型,采用Abaqus/Standard隐式求解。材料选用常温下的PET材料属性,即弹性模量为903MPa,塑性参数为表1中25℃对应的参数。在瓶口处固定约束的条件下,瓶身上下两侧用半球向中间挤压18mm,分析半球的反作用力,获得其力-位移曲线即为此塑料件强度标准。

图6结构分析模型
应用本文所提出的方法进行吹塑和结构联合分析,还需如图7示意将吹塑成型厚后的材料厚度和残余应力映射至壳单元的塑料瓶模型上。
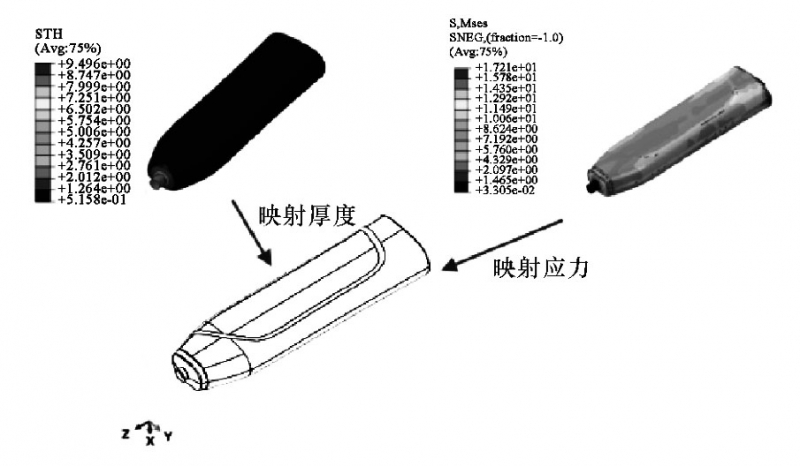
图7映射厚度和残余应力
2.2 强度分析结果
采用本文所述方法,通过映射厚度和残余应力至结构模型,强度分析结果的应力如图8。
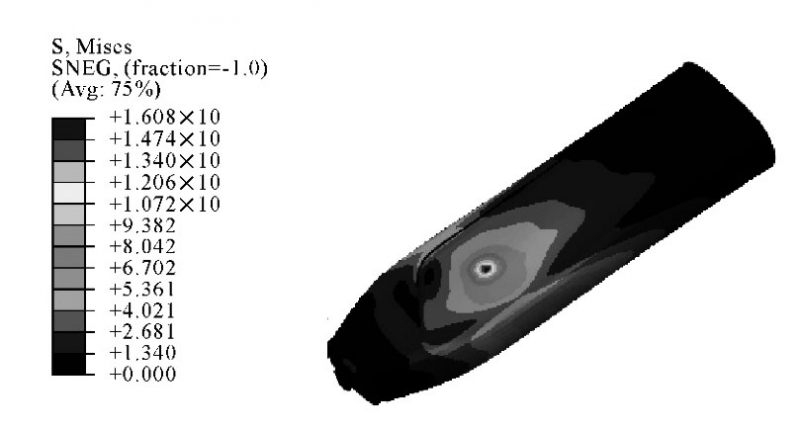
图8非均匀厚度塑料瓶的应力分布
3分析方法讨论
为对比本文方法的合理性,特针对图6的结构模型进行等厚分析,即塑料瓶不通过映射获取厚度,而是分别直接定义等厚度为0.5、0.8、1.0mm。其中均匀厚度0.5mm的塑料瓶应力分布如图9所示。与图8对比可知,图9中应力分布趋势基本相同,但应力数值有较大差别。
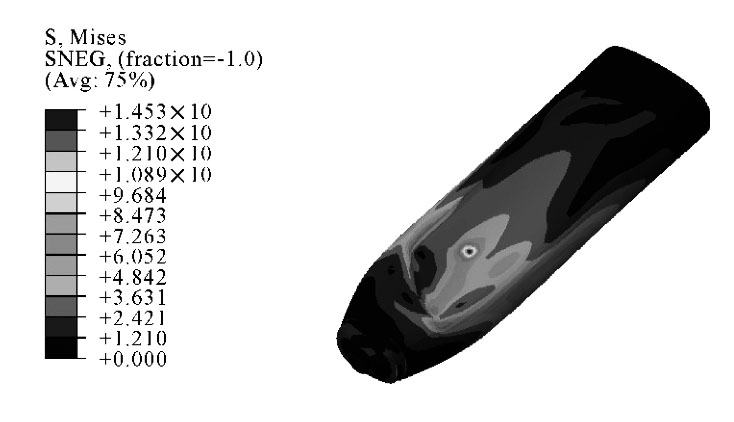
图9均匀厚度0.5mm塑料瓶的应力分布
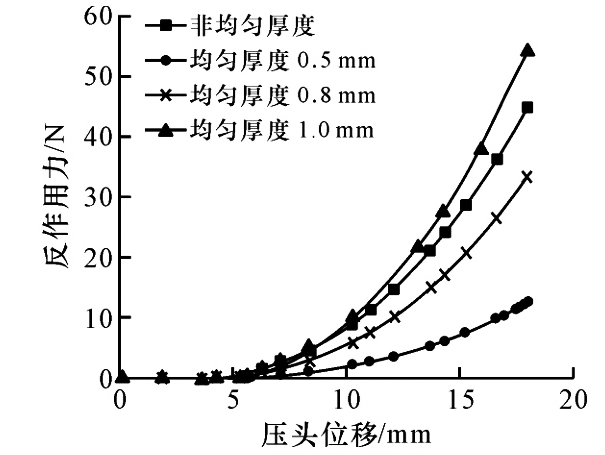
图10不同厚度塑料瓶的力-位移曲线
为对比明显,绘制出图10半球压头力-位移曲线。由图10可知,本文联合仿真方法所获得的非均匀厚度力-位移曲线分布于0.8、1.0mm均匀厚度的力-位移曲线之间,这也说明了无法通过定义均匀厚度的方法对吹塑件进行结构强度分析。
4结束语
1进行产品设计时,考虑产品制造工艺。将吹塑成型的吹塑工艺考虑到结构强度分析中,更为合理准确地对塑件强度进行分析。
2运用不同算法各自的优点,将显式分析的结果映射到隐式求解的结构分析中,能够将制造过程模拟与结构强度模拟联合到一起。
3考虑吹塑工艺的塑件强度分析结果表明,由于吹塑成型对材料的影响导致厚度分布不均匀,故在进行强度分析时,需考虑工艺的影响,才能使强度结果更接近实际。(文章来源于网络)