摘要:文章介绍了高速薄壁注塑在一次性餐盒成型中的应用,分析了聚丙烯高速薄壁专用注塑机的性能要求,在此基础上研究了注塑机的注射、合模、液压和控制系统,实现一次性聚丙烯餐盒的高速薄壁注塑,并在企业中成功应用。
引言
一次性餐盒在餐饮行业得到广泛应用,但由于制品缺陷、质量不可靠、无法有效降解、白色污染等问题,发泡和吸塑成型的一次性餐盒,逐步被市场淘汰[1]。采用注塑成型的餐盒逐渐成为同类市场的主力产品,注塑成型的餐盒采用食品级透明聚丙烯,具有极好的机械性能和耐热性能,制品能在100℃以上温度进行消毒灭菌,在不受外力的条件下,150℃也不变形,脆化温度为-35℃,能用微波炉进行加热,特别适合加热饭菜的包装应用,为此注塑餐盒得到了广泛应用[2]。
一次性塑料餐盒产量特大,要求薄壁,一般为0.4~0.5mm,以降低单个餐盒成本,高效率生产要求注塑机采用机械手全自动工作模式,产品生产周期短[3]。薄壁模具在通用注塑机上生产,产品无法成型,注塑周期长,采用德国、日本等进口设备价格高,高速薄壁专用注塑机国内也有企业在研制,但产品成型率低,注射周期较长效率不高,机器高速生产时工作不稳定,为此研究针对聚丙烯的高速薄壁专用注塑机对该产品的注塑技术发展具有重要意义。
聚丙烯产品的薄壁注塑的相关研究在国内外文献中时有报道,主要关注从薄壁注塑的原材料、薄壁注塑的模具结构等方面来实现薄壁注塑成品率的提升。
朱海旭等[4]以聚丙烯塑料餐盒盖为研究对象,对薄壁扁平结构的产品成型过程展开分析,通过Moldflow软件对浇口位置、模具的排气冷却方案等进行优化设计,实现大批量生产前提下的效率提升与成本降低。曾辉等[5]就薄壁塑件产品表面缩水问题进行了分析,探讨了模具与原料对产品缩水的影响,最终作者认为,设计与生产过程是导致产品缩水的关键原因,其中模具结构起主导作用。孙健华等[6]基于CAE与DOE技术对薄壁塑件的质量控制方法进行了分析,特别关注了薄壁塑件翘曲变形问题,研究了熔体温度、模具温度、保压压力与保压时间等对翘曲变形的影响,通过对工艺参数的优化,缩短生产周期的同时提高了产品质量。
张杨[7]采用单因素实验的方法分析注射速度、模具温度与熔体温度对不同厚度的六翅片薄壁微注塑制品的充填过程、形态结构以及纳米压痕力学性能的影响。薄壁微注塑制品充填过程的流动分析采用UG和MOLDFLOW对1.0mm,0.5mm与0.2mm3种厚度六翅片微注塑制品进行3D实体建模,并分析各个工艺参数充填过程的影响规律。结果表明:微制品充填过程中型腔内熔体的流动由于分流道效应存在流动不平衡的现象。注射速度对微制品注塑成型过程的熔体速度、剪切速率的影响比较大,而熔体温度与模具温度的影响较小。速度在型腔的中面最大靠近模壁最小,而剪切速率在型腔的模壁处最大中面最小;随着注射速度增大,剪切速率越来越大。
成晨[8]应用DOE实验方法对影响电钻外壳注塑成型质量的因素进行研究。余蔚荔[9]对薄壁塑料制品注塑成型技术及其亟待解决的问题进行分析,提出采用基于Moldflow软件的薄壁注塑制品成型技术进行数值分析,并引入计算机辅助工程技术(CAE)模拟成型过程。采用正交实验法对注射压力、注射速度、熔料温度等工艺参数进行优化。结果表明,在注射压力143MPa、注射速度13cm3/s、熔料温度272℃的条件下,获得最小凹缩值和翘曲变形值,分别为4.324%,0.1546mm。
石则满[10]通过对薄壁产品特点的分析,找出生产薄壁产品的设备应该具有的性能特点,再通过试验来验证这种分析的科学性及有效性,指出生产薄壁注塑产品需要采用高速高压注塑机才能实现,国内尚无相关产品应用于生产实践中。
同时,北海炼化与中国石化的聚丙烯产品取代国外进口材料,进入聚丙烯注塑饭盒生产领域,也被广泛报道。从材料的角度给出了薄壁注塑一次性饭盒生产的关键影响因素:原材料问题已得到有效解决。
综上所述,原材料与模具结构等都得到了合理、可靠的解决,但在薄壁注塑产品的生产装备上,并未得到充分的分析探讨与研究。本文将从高速注塑机的设计与方案实现的角度,为聚丙烯薄壁注塑生产一次性餐盒提供有效的装备方案支撑。
1聚丙烯高速薄壁专用注塑机性能要求
注塑机要实现聚丙烯高速薄壁注塑,需满足以下要求:(1)薄壁注塑。注射速度要高,液压系统回油要快。(2)高速注塑机。缩短注塑成型周期,缩短注射部件的注射时间和预塑时间,缩短合模部件的开合模时间和顶出时间。(3)提高高速注塑机的注射压力。合模力增加,注塑机的刚性要好,在保证高速运行的同时,实现工作平稳可靠。(4)注塑机高速运行时磨损加剧,要提高机器耐用度,改进油箱设计,实现液压系统的温度稳定。此次设计中的主要参数如表1所示。
表1 技术参数
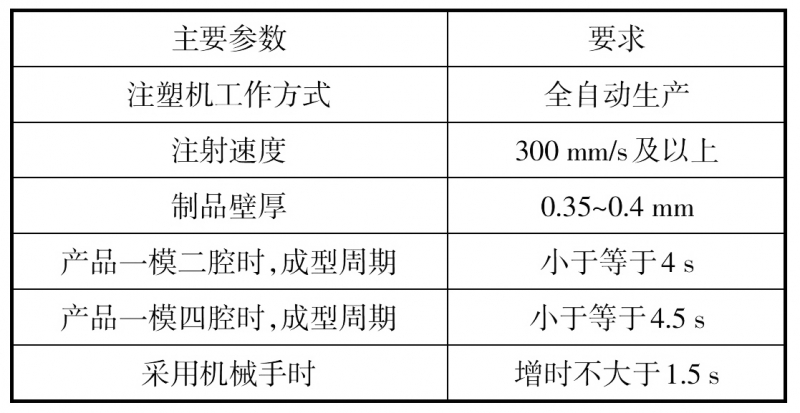
2高速薄壁注塑机的设计
2.1优化注射部件结构,提高塑化能力和注射速度
熔体填充模腔时,遇冷的模壁形成固化层,流动通道变窄,在薄壁注塑时,模壁小于0.5mm,流动通道因固化层消失形成短射,因此要求注塑机高速注射,在固化层不太厚时填满模腔。通用注塑机的注射速度在100mm/s左右,不能应对薄壁注塑,应增加油泵功率提高注射速度或采用双泵注射进一步提高速度,由于薄壁件的注射量不大,也可设计小直径螺杆和小直径注射油缸,使注射速度提高到300mm/s及以上。
要实现塑化均匀和高的塑化能力,最重要的是螺杆结构,选择专用聚丙烯螺杆以提高其剪切力得到高的熔融速度,具有低温塑化能力,得到高的混炼温度,在低背压情况下提高螺杆塑化能力,实现塑化均匀。塑化能力与螺杆转速、螺杆均化段螺纹深度、螺杆直径有关,在螺杆直径确定情况下,螺杆均化段螺纹深度变化不大,此时应选择转速较高的预塑液压马达以提高塑化能力。设计专用加长喷嘴、螺杆头和爪型止逆环,实现启闭灵活,升压快,注射时熔料回泄量降至最低,止逆环区域内发热量保持最低,提高注射部件使用寿命。
2.2适当提高系统压力,实现多级注射控制
小直径螺杆和小直径注射油缸可以提高注射压力。为提高制品质量,改善注塑缺陷,适合薄壁制品的长流程,在注射过程中,设计多级注射控制,当螺杆向模腔内推进熔体时,在不同位置的注射压力和注射速率均可控。塑化热能主要来自料筒加热和螺杆剪切,料筒加热圈采用陶瓷绝缘材料,实现熔融物料温度波动小,料筒温度分布合理并控制准确,陶瓷加热圈如图1所示。射台采用线性导轨导向,底座采用桥式焊接结构,高速注射时工作平稳(见图1)。
图1 陶瓷料筒加热圈
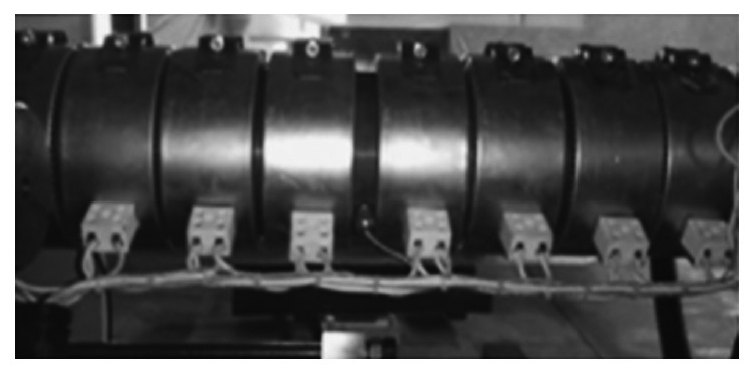
2.3优化合模机构,实现注塑机工作的可靠性
注射压力提高后,模腔压力增加,模板反弹力大,所需的合模力大,液压直压合模机构比曲肘连杆合模机构的模板变形要小,但考虑卧式注塑机的发展趋势,仍采用曲肘连杆合模机构,此时要求模板有较好的刚性,减少模板变形,合模力分布均匀,合模平行度好,实现开闭高速。在设计模板和拉杆时应选择刚性好的材料,通过布置加强筋,适当增加模板厚度,采用紧凑型的顶出和注射油缸,以减小模板中心孔位的变形,实现模板的高刚性,使模具在高压锁紧时产生的变形小,提高制品精度。采用比普通注塑机更高的机械加工精度和选择合理的热处理,在摩擦副间加装石墨铜套,在机器高速开合模时,减少摩擦系数,提高耐磨性,延长机器使用寿命。通过软件对合模部件进行运动分析,确定最佳的响应。餐盒产品高度不高,缩短合模部件的开模行程,缩短开合模时间,缩短顶出距离,减少顶出时间,以提高注塑机效率。
2.4优化的液压系统,实现高速注射
注射速度快,传统的注射油缸来不及回油,重新设计液压缸结构,通过增加后活塞杆实现液压系统的快速回油;采用双注射油缸,使注射动作更加平衡;采用双动力液压系统,实现预塑、开模的复合动作,以提高其效率,又可合并动力,注射速度大幅度提高,注射部件示意图如图2所示。液压系统油路采用硬管提高油路的刚性,采用伺服控制,使系统的输出量(如位移、速度和力等)能自动、快速、准确地跟随输入量的变化而变化,与此同时,输出功率被大幅度地放大,实现高速控制,同时能节能。考虑到薄壁制品生产周期短,开合模频率高,注塑机为连续工作,液压油温度会升高,选用大油箱,进行热平衡设计,选择与之匹配的冷却系统,必要时考虑温度控制和报警功能,提高液压系统的稳定性。
1-双出杆防护罩; 2-双出杆活塞杆; 3-防尘圈压盖; 4-注射前缸盖; 5-注射活塞; 6-注射油缸; 7-弹簧挡圈; 8-密封圈; 9-注射后缸盖; 10-注射活塞杆螺母; 11-注射活塞杆压板; 12-导杆支座; 13-导杆; 14-注射防护罩; 15-预塑马达; 16-射台后板; 17-防尘圈; 18-铜套; 19-射台前板; 20-D-A-S 活塞封; 21-铜套; 22-密封圈; 23-防尘圈; 24-螺杆料筒组件; 25-前模板
图2 注射部件示意
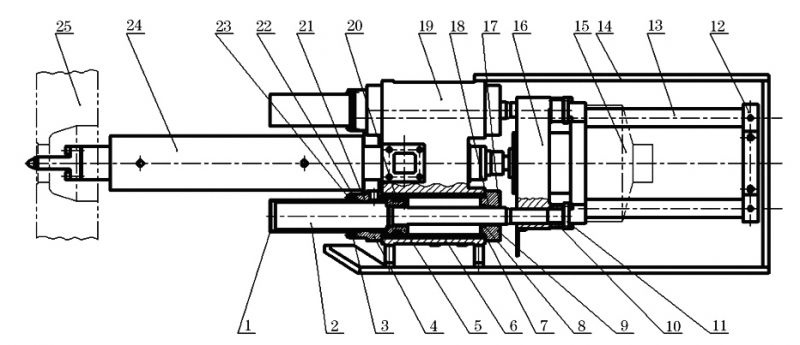
2.5优化控制系统,实现快速响应和友好用户界面
通过改变PLC控制为计算机控制,提高其高速响应,实现手动、半自动和全自动工作模式,通过输入变量实现注塑机注塑参数和温度的过程控制。采用计算机控制后存储量增大,还可以把常用物料的工艺参数输入计算机,实现常用塑料注塑工艺推荐值;实现一台主机通过网路同时控制多台注塑机,实现网络化管理。采用触摸屏操作,实现用户界面友好。
3 结语
本文以研究聚丙烯高速薄壁成型为应用背景,以注塑机为研究对象,提出了一种针对传统注塑机在不使用储能器的情况下实现高速薄壁成型的研究。通过优化注塑机的注射、合模、液压和控制系统,可以大大提高注塑机的塑化能力,提高注射速度和压力,提高回油能力,实现高速注射,优化注塑机的结构,提高机器可靠性,实现聚丙烯薄壁餐盒的高速生产,突破塑料薄壁成型和高速机寿命短可靠性低的技术瓶颈。
当然要得到高质量的薄壁制品,必须综合考虑模具、注塑机以及成型工艺的因素,以改善制品短射、翘曲变形和熔接线等缺陷。采用高速薄壁注塑机注塑CO-PP一次性250mL餐盒,实现注塑周期3.8s,制品壁厚0.45mm。
参考文献
[1]刘亚芳,王顺达,牟子平.两种一次性餐盒生命周期各阶段对环境的影响比较研究[J].黑龙江科技信息,2014(9):100-101.
[2]张帮伟.浅析无任何标识的一次性餐盒危害性[J].食品安全导刊,2017(30):76.
[3]何伟.快速薄壁注塑聚丙烯色粒超标产生原因分析[J].广州化工,2016(5):178-180.
[4]朱海旭,王金莲.基于CAE技术的餐盒盖叠层热流道注射模具设计[J].装备制造技术,2016(8):241-243,246.
[5]曾辉,张辉,林裕亮,等.薄壁塑件表面缩水的原因分析及解决方案探讨[J].日用电器,2017(7):69-73.
[6]孙健华,顾海,张捷.基于CAE和DOE技术的薄壁塑件翘曲变形分析及优化[J].计算机辅助工程,2017(3):40-44.
[7]张杨.等规聚丙烯微注塑制品的充填流动特性、形态结构与纳米压痕力学性能[D].郑州:郑州大学,2017.
[8]成晨.一种基于DOE注塑成型仿真实验的研究[J].好家长,2016(51):206.
[9]余蔚荔.薄壁注塑制品工艺参数优化研究[J].塑料工业,2016(7):64-66.
[10]石则满.薄壁件产品对注塑机性能要求的研究[J].橡塑技术与装备,2016(20):56-57,60.