ISO/ASTM 52900 标准对增量制造(3D 打印)的定义是:用 3D 模型数据来连接材料使其成为制品的过程,通常是叠层成形。增量制造过程使用塑料、金属、陶瓷、玻璃或复合材料来制造物理模型、原型、样板、模具构件和批量生产器件。3D 打印包括 7 种不同的工艺。制件通过挤出、喷射、光固化、层合或熔结的方式制成。
3D 打印作为一种数字制造方式,每年的市场规模和发展速度都在成倍数地增长,它涉及到计算机、机械,其中重要的影响因素是先进的材料科学,尤其是复合材料对增材制造自动化的影响。数据表明,到 2026 年全球用于 3D打印的复合材料收入将超过 5 亿美元,未来十年内复合材料将成为 3D 打印主要的市场机遇。
3D 打印被业内视为一种将生产流程简化和自动化的方法,它保全了纤维复合材料在重量优化和强度方面的优势,对聚合物 3D 打印行业而言,3D打印的复合材料部件代表了一种更直接指向工业终端部件生产的途径,包括用于轻量化飞机和汽车的大型复杂几何部件。
目前,能使用复合材料的 3D 打印技术主要有 2 种,分别是熔融沉积(FDM)和粉床熔融(PBF),而后者主要指选择性激光烧结(SLS)。
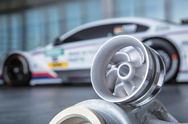
3D 打印材料:与金属的较量
复合材料通常被预示为未来的材料。它们的强度、性能比任何其他材料都具有令人难以置信的优势。伴随着波音 787、空中客车 A350 和宝马 i 系列的闪亮登场,复合材料正在成为一种主流制造的方式。然而,金属工业仍然是复合材料行业持续成功和增长的巨大威胁。美铝公司(Alcoa)的第三代铝 -锂合金已经令许多公司舍弃了复合材料,这些合金被用于各种新的航空航天项目。考虑到仅在过去几年中,复合材料大规模生产线已成为可能,这些金属的向前飞跃可能对复合材料不断增长的市场渗透率构成威胁。
3D 打印是金属与复合材料竞争的另一个领域。金属 3D 打印已经运作得相当好,适用于各种合金;但目前几乎没有复合材料 3D 打印技术的任何指标,复合材料在性能上还无法与最好的金属材料所提供的性能相媲美,更不用说类似于带状铺叠的东西。在过去的十年中,金属 3D 打印的研究一直在进行,这也令其在航空航天及其他领域,如高性能汽车等行业的应用获得诸多进展。当使用固体棒为原料时,目前钛 3D 打印机可以实现与机加工钛相当的性能,尽管这些部件需要一定程度的后加工,但是它们对于加工复杂的高强度部件来说是有效的。选择性激光烧结(SLS)打印机使用粉状原料,消除了这一加工步骤,使它们能够提供足够精确的元件,如 CFM 的 LEAP 发动机的燃料喷嘴,但是这种粉末工艺又有诸如孔隙率的其他缺点。
一台完全功能的碳纤维 3D 打印机应该能够生产复杂、详细和强大的部件,大大超过了加工铝和 3D 打印金属的能力,其成本在两者之间,同时允许用户使用全新的 CFRP(碳纤维增强聚合物)结构来定制其性能。复合原料比一些金属 3D 打印机所使用的精确粉末合金便宜,并且加热热塑性或反应性聚合物所需的能量远低于熔化金属所需的能量。由于在这一领域有限的投资和工程上的挑战,而非任何固有的物理限制,复合材料的这种潜力尚未实现。
金属是各向同性的,这意味着它们在所有方向上的性质是一致的,完全表征它们的弹性状态可以通过两个特性:杨氏模量和泊松比。另一方面,复合材料是各向异性的,并且需要更多数量的常数来描述它们的弹性行为。如果有人认为,在一个共同的基准下,当一种3D 打印材料勉强在单向拉伸试验中挤掉了一些特殊的铝合金,就认为它“比金属强”,这种比较变得更加有问题。金属具有相似的抗压强度和拉伸强度,而复合材料的抗压强度远低于其抗拉强度。复合材料的各向异性也与拉伸、压缩和剪切载荷的组合等各种其它静态强度性能相关。可以说,在 3D 打印领域,这两种材料各有所长。
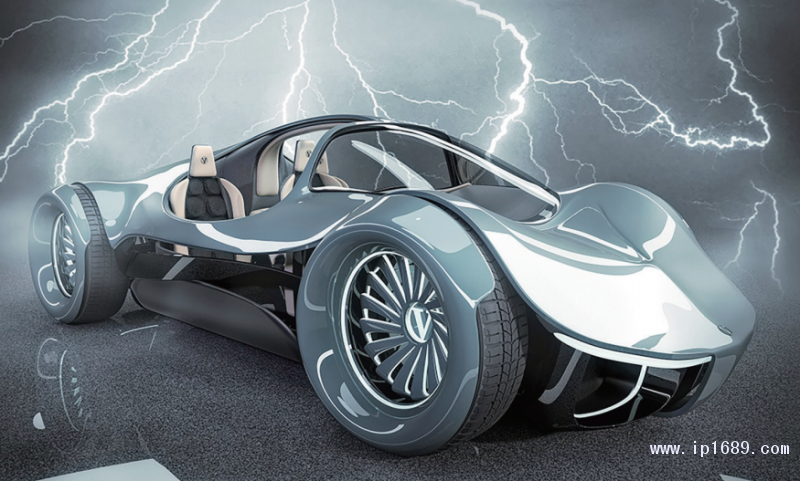
3D 打印技术:熔融沉积(FDM)和粉床熔融(PBF)
熔融沉积(FDM)
熔融沉积成形工艺(FDM)是普及最广的 3D 打印技术,主要使用 ABS、PLA 等材料,其工作原理是将 ABS、PIA 等材料通过加热熔化,再凝固成形。材料通过挤出机构被送进热熔喷头,在喷头内被加热熔化,喷头根据集成化电路系统,让喷头沿零件截面轮廓和填充轨迹运动,同时将半熔融状态的材料按软件分层数据控制的路径,挤出并沉积在指定的位置凝固成形,与周围的材料粘结,层层堆积成形。
粉床熔融(PBF)
粉床熔融(PBF,选择性激光烧结 SLS),选择性激光烧结(Selective Laser Sintering)技术由美国德克萨斯大学奥斯汀分校的 C.R. Dechard 发明,主要是利用粉末材料在红外激光照射下高温烧结的基本原理,通过计算机控制光源定位装置实现精确定位,然后逐层烧结堆积成型。先用铺粉滚轴铺一层粉末材料,通过打印设备里的恒温设施将其加热至恰好低于该粉末烧结点的某一温度,接着激光束在粉层上照射,使被照射的粉末温度升至熔化点之上,进行烧结并与下面已制作成形的部分实现黏结。当一个层面完成烧结之后,打印平台下降一个层厚的高度,铺粉系统为打印平台铺上新的粉末材料,然后控制激光束再次照射进行烧结,如此循环往复,层层叠加,直至完成整个三维物体的打印工作。
近些年,有一些公司在 3D 打印方面取得了独特的和突破性的发展。例如,美国辛辛那提公司与美国橡树岭国家实验室共创了“大面积增量制造”体系,打印速度达到 45-48kg/h。适用于复合材料的大规模制造。美国EnvisionTEC 公司研发中小型打印体系,能够打印玻璃纤维增强高强度塑料。美国 Markforged 公司推出了世界上第一
种商业化 3D 打印机,可用连续碳纤维、芳纶纤维或玻璃纤维打印制品。同样,美国 Arevo 公司研制了增量制造体系,能够打印连续纤维增强材料和热塑性基体的复合材料。
用于 3D 打印的复合材料
玻璃纤维复合材料供应商欧文斯科宁 Owens Corning 的 XSTRAND™ 系列材料可用于 FFF / FDM 3D 打印机,其强度和韧性高于碳纤维填充 ABS、纯PP 和标准 PA6。欧文斯科宁 3D 打印玻璃纤维复合材料主要包括 GF30-PP 和GF30-PA6 两种:GF30-PP 是一种增强聚丙烯丝材,其玻璃纤维含量为 30%,具有很高的硬度,并能抵抗温度变化、耐化学品腐蚀,耐紫外线老化。
GF30-PA6 是一种增强 PA6 尼龙丝材,玻璃纤维含量为 30%,特点是高强度和耐高温。由于耐磨性高,GF30-PA6 可以用来替代汽车生产线上使用的钢制夹具和固定装置。此外,GF30-PA6 适合应用的温度范围在 -20℃至120℃。
此外,增材制造技术领域的专家Stratasys 公司用于 FDM 3D 打印技术的尼龙 12CF 材料,含有多达 35% 的碳纤维,因此各种属性都非常优异,比如最终拉伸强度为 76 兆帕(MPA),拉伸模量为7529兆帕,抗弯强度为142兆帕,足以在许多应用中取代金属,非常适合汽车、航空航天等行业。这种碳纤维增强热塑性材料,用于生产
高性能原型,能够在设计验证过程中经受生产零件的严格测试满足生产环境的苛刻要求,并可应用于生产线上的夹具制造。
Stratasys 还与迈凯轮建立了合作伙伴关系。这一合作伙伴关系已经取得实质性的进展,包括迈凯伦的一级方程式赛车上已经安装了一些 3D 打印制造的部件。
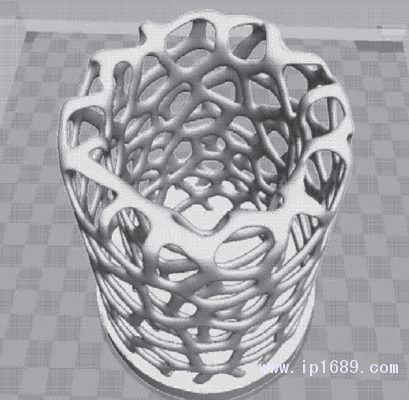
陶氏杜邦公司在Formnext展会上,推出了新的玻璃和碳纤维增强 3D 打印耗材丝。原本处于竞争关系的陶氏化学和杜邦合并之后,在 3D 打印耗材行业中动作不断,发挥材料方面的优势抢占市场。杜邦 Zytel 3D 打印专用尼龙材料本身就是一种高性能、强度好的耗材,改性的新材料 Zytel 3D12G30FL BK309和 Zytel 3D10C20FL BK544 则进一步提升强度,可与现有的增强注塑相媲美。新的耗材丝是为了满足工业对更硬和更坚固材料的需求而开发的。
索尔维近期推了出 10% 碳纤填充的 KetaSpire® PEEK(聚醚醚酮)及纯Radel®PPSU(聚苯砜)材料,适用于e-Xstream engineering 公司最新发布的Digimat®-AM(增材制造)软件(2019.0)。索尔维在现有的纯KetaSpire® PEEK AM材料基础上,扩充了适用于 e-Xstream engineering 公司 Digimat®-AM 软件的线材产品种类。
近期部分应用案例
3D 打印的混凝土复合材料最新技术
美国陆军工程师研发出了一种新型复合材料,可用作混凝土 3D 打印。值得一提的是,利用这种材料可以打印出更坚固的结构,并且大大缩短了生产时间。
以前使用普通混凝土进行 3D 打印,但是由于含有沙子、沙砾和石块等材料,容易堵塞机器。为了解决这个问题,美国国防部下属的陆军工程兵团(USACE)创建了一种含有各种元素的粘合剂,使得 3D 打印建筑物更有效。
混凝土有两种主要组成部分:固体混合物和液体混合物。一层固体混合物由粘土、煤灰(煤粒)和硅灰组成,然后结合沙子、砾石、石头等材料与粘合剂混合形成完全固体混合物。粘合剂增加了流动时间并改善了混凝土凝固时间。液体混合物包括常用于混凝土中的化学品和液体,以改善其流量和粘度,达到实现快速泵送的目的,其中还包括干燥时减少开裂和尺寸收缩的化学制品,以及用于降低混合物糊化性的增塑剂。
由于有了这种新型粘合剂,混凝土拌合物不需要进行改造,就能具有更理想的性能。根据 USACE 的说法,它还可以提供很高的强度,十分适用于制造强度要求较高的网格层。
航空发动机将用上 3D 打印复合材料结构件
牛津性能材料公司 Oxford Performance Materials(OPM) 为 CST-100“星际客机”太空飞船(波音和NASA 合作研制的专门执行空间近地短途运输任务)供应 3D 打印零件,该零件为大型、复杂的复合材料承载结构件。在这之前,OPM 公司已经为波音 CST-100 空气新生系统制造了 3D 打印复合材料结构承载管道零件。
牛津性能材料开发了 OXFAB 3D系列打印材料:OXFAB-N 和 OXFABESD。由于其惰性特点,OXFAB 具有高度耐化学性和耐热性以及定制电性能的能力,同时抵抗火焰和辐射,这对于高性能的航空航天和工业零部件十分关键。通过镀镍工艺,牛津性能材料发现新材料可以达到介于钛合金与高性能航空铝的性能。经过范围广泛的机械试验数据证明,OXFAB 可以用于 3D 打印功能完整的、可直接使用的零部件。
制造过程中,OPM 公司利用具有抗热及支撑高机械载荷的能力高性能碳纤维短纤维增强的热塑性聚醚酮酮(PEKK),采用增材工艺制造的该零件。该零件是激光烧结 3D 打印成形,将短的碳纤维掺入到 PEKK 中,极大增强热塑性材料强度并使其具有传导性。公司下一步计划将该技术应用于民用飞机,最初应用目标是涡扇发动机上的推力转向叶栅和风扇出口导向叶片,这些零件为次承力结构件,相比传统手工铺放工艺可节省 50% 成本,且节省劳动力和某些加工步骤。
OPM 公司还希望通过回收增材工艺过程中未使用的粉末以减少成本。实际制造中,在每次运行中只使用了 10%到 12% 粉末,其他 85% 以上未曾使用的粉末可以进行回收,目前公司具有回收一次的能力,正在与其他公司研究开发回收三次乃至更多次的技术能力。(文章来源于网络)
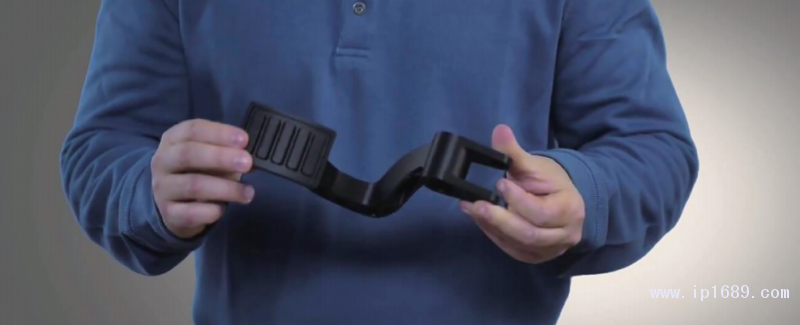