随着制造商寻求降低复合材料部件的成本,设计人员努力尽可能高效地使用构成材料,同时实现自动化生产和多种功能的集成。对于汽车应用而言,由于需要短循环时间,因此这一挑战更加严峻。
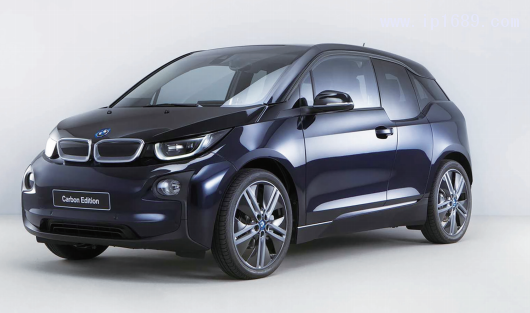
碳纤维车身的加工
宝马 i3 上科技含量最高的要数碳纤维增强复合材料 (CFRP)车身,这种材料是由宝马公司和西格里公司(SGL) 联合开发的,以基于聚丙烯腈的热塑性纺织纤维为原材料, 在一定的压力和温度下,转化成极其细长的碳纤维丝线,其中每条碳纤维的直径仅有 0.007 毫米,最后再经过相应的氧化和碳化处理,形成车身材料。
最初加工出的碳纤维细丝是以线束的形式呈现的,而每条线束都含有上万条丝,所以还需要对它们进行缠绕在线轴上的后续处理,为之后的装运工作做好一切准备。值得一提的是,西格里工厂生产碳纤维的整个过程非常环保,因为他们所消耗的电能全部来自哥伦比亚河的水利发电能量。
碳纤维材料被运往宝马在德国瓦尔斯多夫的零部件加工厂,然后根据需要纺织成各种各样的结构和样式;再接着工作人员把这些半成品送往莱比锡和兰茨胡特的碳纤维增强复 合材料冲压车间,完成碳纤维软性板材(类似坐垫、地毯) 的制造。通过各种加工机械,碳纤维板材被切割成各种不同的大小和形状,然后再利用热处理或塑料粉末高压粘合技术, 把这些板件加工出立体构型。加工成型阶段,每一次三个形状完全相同的碳纤维板件要重叠在一起,这样可以有效地降低在最终的树脂传递成型过程中材料发生撕裂的可能性。
树脂传递成型则是把高温高压的复合树脂注射入模腔, 浸透增强纤维材料、固化、脱模成型的技术,比传统高耗时的烘箱固化技术要先进很多。
在过去的十多年时间里,宝马公司一直致力于碳纤维增强复合材料产品和创新技术的研发,工程师们已经把产品的生产周期降低了一半以上,制造和原材料成本也减少了 30%—40%。工程师又有了进一步缩减碳纤维增强复合材料生产制造周期的新想法,但在 i3 的实际生产过程中也碰到了不少难题,可工程师没有为之担心,因为他们知道这是最终的成功所必须经历的经验积累阶段。
宝马的树脂传递成型技术允许加工那些尺寸较小的部件, 比如说车身侧围,再把它们粘结成一个更大的组分,最终在 模具中结合成整体车身;这种技术把零部件的总数降低到传统钢制车身使用总量的三分之一。
在树脂传递成型阶段之后,利用水激光切割技术完成碳纤维增强复合材料部件上的嵌入空和边缘剪裁加工;接着在最新的全自动化车身车间中,所有部件进行过表面磨砂处理, 增加粘附性后,结合为一个稳固整体。
除了车顶使用了可回收再利用的碳纤维增强复合材料, i3 外围全部采用树脂塑料,这也是宝马运用这种材料的首款 汽车。相同体积大小下,塑料板材的重量只有钢板的一般, 而且四分之一的树脂材料还是可再生或可循环使用的。因为加工设备存在一定的差异,车身外围塑料板材由三种不同的热塑性注射成型加工工艺完成,其中最先进的是外围塑料结构和基底结构同时注射成型和结合成整体的工艺。
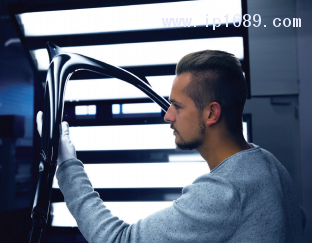
二次成型的骨架设计
二次成型或者说是包覆模压成型工艺,即在连续纤维预制件顶部注塑成型热塑性复合材料,多年来一直被认为是一种可能的解决方案。“这种方法已经达到了新的水平,现在实现了热塑性复合材料 BIW 白车身结构的全自动生产。”西格里 SGL Carbon 公司轻量化应用中心负责人 Christoph Ebel 博士解释道。
这一进步得益于“骨架”设计方法,该方法已经开发了好几年。正如 MAI Skelett 项目首次展示的那样,该工艺涉及使用单向(UD)碳纤维热塑性塑料,通过两步法 75 秒工艺进行热成型和包覆模压,从而生产出超过以往所有版本要求的结构屋顶构件。它还集成了附件夹子,并改变了从脆性到延性失效模式的碰撞行为,以提高 BIW 剩余强度。
为期 17 个月的 MAI Skelett 项目得到了德国联邦教育和研究部(BMBF)的支持,并由碳纤维复合材料联盟(Carbon Composites e.V.)的区域部门 MAI Carbon 完成。
在宝马公司的领导下,项目的重点是实现一个特定的演示:挡风玻璃框架,位于玻璃挡风玻璃上方的两根 A 柱之间。 其设计基于目前宝马 i3 的结构,包括所有的功能和空间要求。 挡风玻璃框架不仅作为屋顶的横向结构构件,还提供其他功能:刚度,同时降低噪音、振动和粗糙度(NVH);强度(屋顶压力测试),有助于满足碰撞要求;一种用于内部部件的固定装置(例如,遮阳板、内饰,用于照明的灯线束等), 以及与挡风玻璃、天窗和外部屋顶板连接的支架。
骨架设计的挡风玻璃框架在零件的角落处包含四个 UD 纤维增强拉挤杆,封装在包覆成型的框架中,以提供扭转刚度和复杂形状的功能附件。拉挤型材不是全部在一个平面上, 而是排列在不同的高度:两个靠近 60 毫米高的部分的底部, 两个靠近顶部。
对于 MAI Skelett 挡风玻璃框架,最终确定了 10×10 毫 米见方的横截面。目标是使用较便宜、较粗的碳纤维束。然而, 所选择的 50K 丝束纤维具有无数长丝的紧密堆积,这使得树 脂浸渍更加困难。SGL 热塑性塑料产品经理 Veronika Bühler 说:“总的来说,这一挑战可以通过优化的纤维引导和扩散来克服,以达到最佳浸渍和高达 50%体积的纤维体积含量。” 西格里 SGL 已经掌握了这项技术,现在提供拉挤成型作为其热塑性工具箱的一部分。“我们已经对半成品有广泛的了解, 因为我们的热塑性胶带也是基于拉挤成型的。因此,我们能够快速调整我们目前使用的拉挤成型技术,以创建我们自己的型材。该工艺包括纤维体积、孔隙率和尺寸精度的质量测试。 由于自动化和机器人处理,后者非常重要。例如,由于拉挤型材中的残余应力,不会出现曲率。”
除拉挤增强材料外,还在 MAI Skelett 项目中研究了热塑 性树脂。测试各种类型的聚酰胺 6(PA6 或尼龙 6)以确定所需的粘度和流变性,以优化拉挤成型质量和速度。SGL 通过其热塑性工具箱为该项目提供了一系列材料,其中包括 UD 带、有机片、短纤维和长纤维增强复合材料的短切纤维,以 及现在的 UD 增强拉挤成型,均基于 SIGRAFIL 50K 碳纤维, 适用于上浆聚丙烯(PP)和聚酰胺基质,包括 PA6 或原位 PA6。为了实现复合材料结构的最佳性能,必须协调纤维、 施胶和基质。
她还解释了原位 PA6:“这是当你与己内酰胺单体或单 个单体与催化剂和活化剂反应时,它们在复合材料部件成型过程中聚合(形成长长的聚合物链)。”换句话说,己内酰胺在原位聚合成聚酰胺。Buhler 指出,聚酰胺作为一个聚合 物基团包括 PA66 和 PA12,以及某些类型的 PPA 作为额外的 基质选择。
挡风玻璃框架制造的另一个重要方面,是热塑性半成品 在成型过程中和成型后的热成型能力。这关系到在包覆成型期间是否能够进一步实现形状的功能化以及熔合。两者都是 MAI Skelett 项目设计中的重要因素。
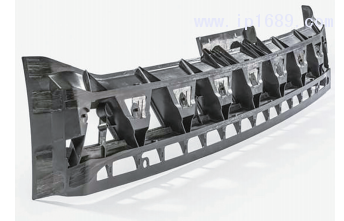
热成型和包覆成型
MAI Skelett 挡风玻璃框架的生产始于碳纤维 / PA6 拉挤型材。然后必须对它们进行修改,以适应组件的形状以及在不同点处的负载引入。选择热成型来做到这一点,首要关注的是碳纤维的高强度和刚度只能通过尽可能保持直线来实现。 当拉挤棒在基质流动方向上拉伸,然后在棒的末端变平并弯曲时,实现了这一点。
该方法的第二步是将热成型拉挤型材放置在红外加热器 下,使其在不到 50 秒内达到温度,然后使用为此目的开发的自动处理系统转移到注塑模具中。项目中的所有部件均在现有的注塑机上生产。
然后将纤维增强的化合物包覆成型到型材上和周围。在包覆成型期间,在模具和工艺中都需要精确度,以便将四个热成型拉挤棒保持在适当位置。
两步法,预成型拉挤成型的热成型和包覆成型的总循环时间约为 75 秒。由于热塑性基体在包覆成型之前会重新熔化, 因此可以在非常短的循环时间内将预制和热成型棒材成型并粘合到成品部件中。通常,热塑性塑料的可熔性也能够与均匀的金属部件连接。由于热塑性热成型和注塑成型工艺具有出色的再现性和工艺控制,这是大批量生产的关键因素。
延展性失效
评估了使用玻璃和碳纤维的相容模塑化合物的 PPA 和 PA6 型材,以探索该组件的更具延展性的失效模式。虽然更 具延展性的失效模式减少了挡风玻璃框架的承载能力,但从 整体上改善了 BIW 的结构完整性。
分析方法包括实体建模、钢筋建模(几何建模,其中拉 挤成型作为钢筋加强包覆成型)和使用壳单元建模,以及这 些的各种组合。软件包括 FE 解算器 ABAQUS(达索系统) 和由 Sandia National Laboratories 开发的 Dakota 参数求解器。 OptiStruct 用于拓扑优化。
虽然宝马没有在其最终项目报告中指定首选材料组合, 但它确实得出结论,最终模拟和测试结果表明骨架组件超出 了当前碳纤维增强塑料(CFRP)部件的所有要求,除了扭转 刚度,被确定不是挡风玻璃框架的关键设计驱动因素。与 当前的 CFRP 部件相比,骨架设计超过了碰撞载荷情况下 的载荷水平和能量吸收。它还成功地实现了更具延展性的 失效模式,这不仅进一步提高了复合材料结构的碰撞性能, 而且进一步提高了对碰撞性能的理解以及它与整个 BIW 结 构的关系。
未来的骨架设计应用
在 MAI Skelett 最终报告中,宝马指出,它已经确定了其 他六种车辆部件,这些零部件可以从使用骨架设计方法显著 降低制造、材料和工装成本中受益。SGL Carbon 建议在汽车 和航天座椅结构、仪表盘、机器人手臂、x 射线工作台等方 面进行应用。
然而,骨架设计方法得到了进一步的发展,扩展到后续 的 MAI Multiskelett 项目中的多轴受力构件。它研究了轴承部 件和拉挤型材相交的区域,也研究了高荷载引入区域,特别 是几个主要荷载路径相交的大型结构部件。与之前的 Skelett 项目一样,对组件设计和低成本的串行生产线进行了研究。
骨架设计如何进一步优化现有复合材料部件的一个例子是 2017 年 由 SGL 和汽车技术专家 Bertrandt(德国 Ehningen)开发的电动汽车碳载体前部内部。集成了所有主 要功能和装饰组件。在传统仪表板中,碳载体基于热成型有 机薄片作为承载“骨架”以增加刚度。
“碳载体”结合轻量级碳纤维复合材料和集成功能的“完 美的案例”用于“创新型材料混合的汽车行业”。在轻型结 构领域,碳纤维增强塑料(CFRP)扮演了重要的角色。整体 设计,是基于在 Bertrandt 创建的基础功能包的基础上开发模 型的前汽车内饰及可转换电力驱动车。模型包括所有主要功 能和装饰组件的传统仪器面板。结构组件也被重新设计,使 车内感觉更自由、光明和浮动的印象。
“既然设计碳载体,我们确保现在或在不久的将来其组 件,技术和组装概念可以用于大规模生产。尤其是电动车,减少体重意味着更大的行动范围。”Michael Hage CAE 开发 主管如是说。加工工艺的主要挑战是找到最优的配置矩阵和 纤维材料,纤维长度、层结构和过程技术,以满足更加广泛 的需求。整体设计是一种排他性的安装结构,SGL 集团不仅 共享其材料和过程的专业知识,同时也在提供了其在大组件 生产的经验。最优混合材料以及生产技术开发在单独的轻量 级和应用中心(LAC), 轻量级的解决方案都是设计用于大 规模生产。
“将来,这部件可以用包覆成型热塑性型材的设计取 代。”Ebel 说,“这将省略有机片的切割、铺设和修剪操作。 此外,横梁也将过时,因为我们将其整合为拉挤型材并包覆 它们以实现仪表板设计。这种包覆成型的部件还可以提供更 大的空间和灵活性,以容纳所需的附加元件以及用于连接这 些元件或电缆等的螺钉和夹子。”
由 SGL 和 Bertrandt 开发的电动汽车的碳载体前置内部。
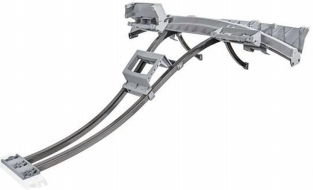
Ebel 承认这将是一项巨大的设计变更。“但它降低了成本并使整个组件更加高效。”他指出,设计一种几乎没有浪费的工艺是有可能的,因为型材完全按照所需的长度切割, 而且在这些步骤中或在过度成型前的热成型过程中不会损失碳纤维增强材料。座椅也是骨架设计的主要候选。“在复合材料中,它们通常由织物或带制成,并且仍然是片状结构。 但是我们可以通过整合底部的轮廓和增加刚度来减小平面区域的厚度。拉挤型材不是唯一可以构建的有效 UD 产品。
“我们正在轻量级应用中心吸引了很多公司。”Ebel 说, “骨架设计作为一个额外的创新概念引起了很多人的兴趣, 并且被我们的访客看作是非常有前景的。”该中心已经建立了自己的设计能力,可以帮助公司整合创新的想法,如骨架概念,为未来的材料高效组件开辟新的设计空间。
“在很多应用中,我们可以使用类似挡风玻璃框架的设 计。”布勒说,“对于碳纤维行业来说,从准各向同性铺层发展是很重要的,这使得碳纤维的强度和刚度有了很大的提高。相反,我们必须开发更有效的材料形式,把每一种材料只放在需要的地方。这是这个行业未来所需要的。”(文章来源于网络)