介绍:
泡沫材料的挤出基本是指混合着化学发泡剂的聚合物的挤出。热量的产生融化了聚合物,也使得发泡剂受热分解出气体。气体分布于熔融的聚合物中并且不断扩散到模具上。
泡沫材料的挤出基本是指混合着化学发泡剂的聚合物的挤出。热量的产生融化了聚合物,也使得发泡剂受热分解出气体。气体分布于熔融的聚合物中并且不断扩散到模具上。
一般的挤出机只要满足以下要求,就都能够用于聚合物的发泡:
熔融温度必须保证能使发泡剂完全分解;
熔融压力必须保证使发泡剂产生的气体充满熔融聚合物中直到溢出到模具上。
如果温度达不到足够高,会造发泡剂不能充分分解从而造成浪费。而且没有分解的部分会凝固,它会阻碍融化或者会使产品形成孔洞、不良的微孔结构和表面。
压力的不足会导致“提前发泡”,即使随后增大压力,气体也不能“再融入”,这会造成微孔的破坏和瓦解,形成大量不规则的结构。
当轮廓和薄片为粗糙的表面时(鲨鱼皮),这种粗糙的发泡会使平滑的薄膜上形成孔。如果是薄膜吹制成型,吹制的薄膜管会崩坏。
运用“排气”或者排气挤出机(用于PS和PMMA的挤出)是比较合适的方法,但要遵循以下几点建议:
出口处需要堵住或者密封住,以防发泡剂产生的气体泄漏;
使用轴段没有被深切的三段式螺杆或者排气式螺杆,而且在排气区域螺纹不能太高。在挥发区,有一个高度自由的空间,这会降低轻微的压力,有可能引起提前发泡。对于较厚的螺旋轴,压力的下降可以通过提高螺杆速度或者增大模具中的压力来补偿。
发泡剂
福马索发泡剂是由卑尔根国际公司开发的,它的配方合理,如果使用得当,可在规定的温度范围内时确保分解完全且形成极其一致和精细的泡沫结构。
表1 福马索发泡剂产品及其分解温度
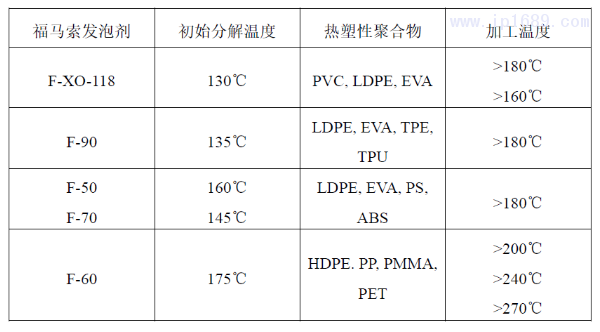
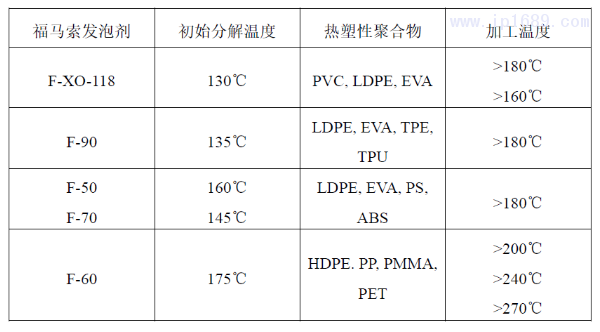
通常会使用两种形式的发泡剂,有粉末和浓缩物合或者颗粒状的母料。虽然看起来使用粉末状的发泡剂更经济,其实际上难以计量。当缺少合适的粉末计量系统时,通常会通过干混将粉末和聚合物混合起来。为了实现良好的混合,通常混合前,要使用合适的混合器在聚合物上涂上一层液体材料(涂料)。合适的涂料有低粘度的石蜡油或其他液体添加剂,如增塑剂、润滑剂或抗静电剂。一般涂层使用量不大,约为0.5%到1%,如果大量的使用,会引起熔融滑移或者过度润滑的危害,这会导致挤出机进料时出现问题。
一般来说,最好用颗粒状母料形式的发泡剂,这类似于使用其他添加剂或者色母料。许多类型的进料器、搅拌器和计量装置可以计量母料的重量或体积。然而,使用母料时,载体聚合物可能会影响发泡过程。
发泡剂和母料混合形成发泡剂母料,选择与聚合物相容的发泡剂母料时非常重要的,因此卑尔根公司的发泡剂能以不同的浓度用在不同的树脂母料中。
卑尔根公司还提供了全系列的产品,它们有放热发泡剂和放热/吸热混合材料。这种材料适用于粉末状和颗粒状母料。
机械参数
挤出机
大多数单螺杆挤出机都适用于发泡挤出,螺杆的长径比至少为24:1,常用的长径比为30:1。进料区的温度应低于发泡剂开始分解的临界温度,以防止其过早地分解。
使用有槽的管道能让挤出机内的相对压力快速增加(见图1、3),这对于低熔融温度环境中的发泡剂是有利的。当发泡剂在较早阶段就融化了并且开始分解,由于管道前段的高压作用,分解的气体能融入熔融物中且在短时间内有很好的分布状况。
当使用光滑的管道时,要到达熔融压力的时间较长(见图2、3),低熔点的发泡剂母粒会在管中过早地融化,这会导致气体或多或少地从料斗中溢出。这种情况下就需要把进料区的温度调低,以防发泡剂过早分解。
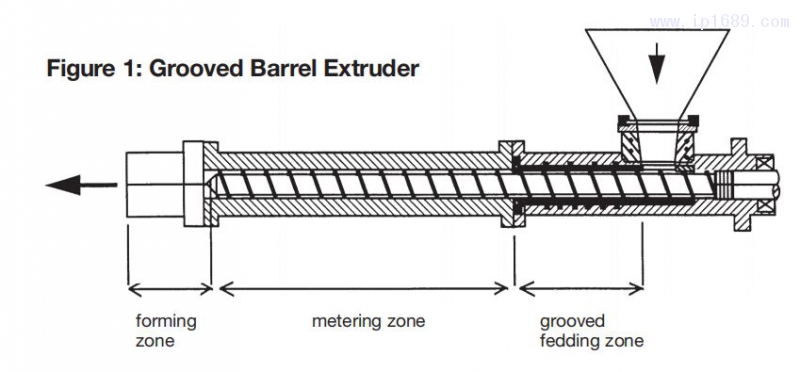
图1 槽管式挤出机
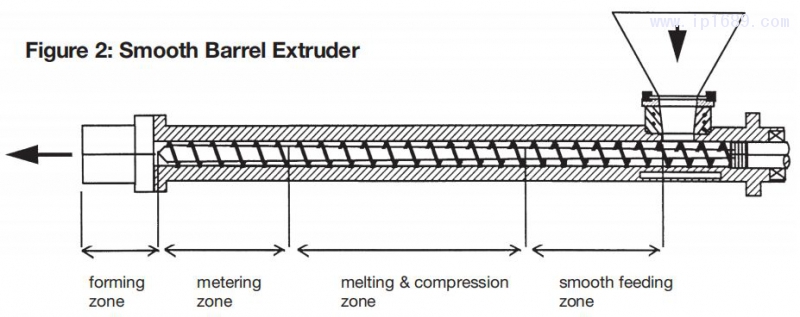
图2 光滑管式挤出机
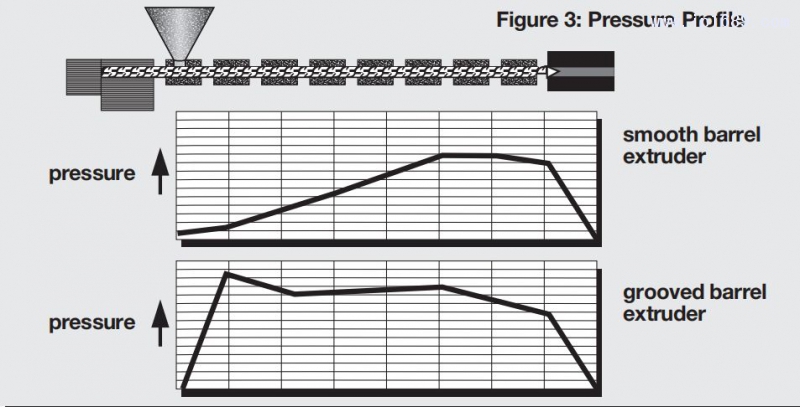
图3 压力简况
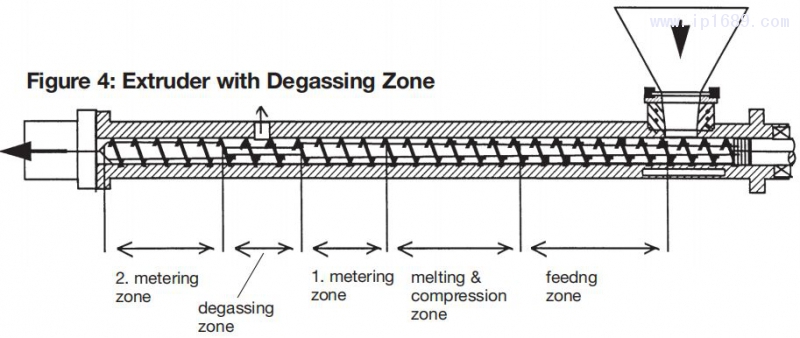
图4 有排气区的挤出机
螺杆结构
只要单段式的螺杆中没有大幅度的压降,普通的螺杆基本都能用于发泡挤出,大幅度的压降会导致熔体中不必要的提前发泡。为了工艺而制作的螺杆为三段式的(进料-压缩-计量/混合)。如果你留意了这篇报告开头所提及的内容,就会发现使用排气式螺杆也能达到良好的结果(见图4)。
随着屏障型螺杆的引入会导致一些新问题。其中一个就是由于屏障型螺纹和流动的树脂之间高压的降低,会导致提前发泡的几率增大。当使用较短的屏障分段,下降的压力就会从螺杆高速旋转中获得补偿。
一般在发泡挤出中不需要使用细筛网和换网器,因为泡沫的结构、杂质、黏胶或者添加剂通常不可见也不影响产品。
如果使用了熔体过滤器,那么细筛网的使用是很重要的,这能防止筛网后的压降,否则会造成提前发泡。
熔体泵的使用能让压缩过程有以下几个优点:
流量稳定;
管道中压力会上升;
较少的密集材料会在管道里流动。
在发泡挤出中,在熔体进入熔体泵的位置放一个压力表是非常重要的,这个压力表的读数可以用来控制螺杆速度,以确保在挤出机末端有一个稳定的熔体输出。
如果压力设定过低,可能会出现提前发泡,因此增大压力是很有必要的。
实验表明,以下的压力可以作为生产可用的发泡产品的最低标准:
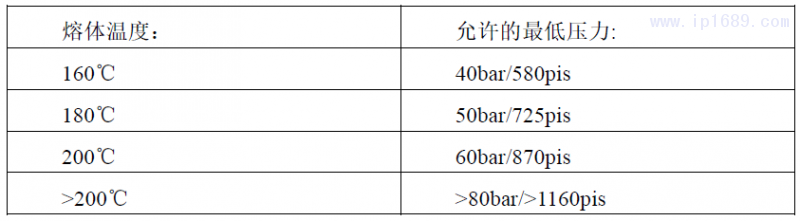
挤出工艺模具
槽模
槽模用于制作薄膜(通过冷却辊堆积起来),或者像薄片的薄膜(堆积)。当使用带有节流杆的槽模时(节流杆是为了更好的分散熔体),杆不应该闭合得太紧,否则在熔体经过节流杆后会产生压降,从而导致提前发泡。
最好是能检测熔体中的一个微小区域,只要退出模具,就会释放出自由气体。在这之后,能看到气体的膨胀,这被称为“光晕”。当你看到一个光晕时,就能确定在模具和设备里没有发生发泡和膨胀。
在发泡熔体冷却过程中通常会出现以下问题:
泡沫形成的时间不够—模具和冷却辊之间的距离太短;
泡沫结构被破坏—各冷却辊间的距离太短;
当生产较薄的薄膜时,气泡会被严重拉伸,从而导致泡沫膜的密度会增大—退去速度过快。然而,对于某些工艺,这种拉伸或者定向时必须的,例如装饰性缎带和包装带。
当调整槽模开口距离时,必须考虑重量的减少。如果减少了30%重量,开口应该比相同厚度的膜小30%(以补偿发泡的补偿)。
型材模具、管状喷嘴
与草木槽模的横截面相比,型材模具的截面一般不能改变或调整。在设计和加工模具时,要考虑其是否能生产出需要的泡沫产品。一般情况下,模具的成型段长度要较短,以保证直到模唇时都保持着高熔体压力,这也适用于泡沫吹膜成型。还需要注意的是,模具的压力特性可能会受到许多因素的影响,如树脂种类、树脂粘度、温度、期望降低的密度值、输出速率和实际产品的截面。
混合挤出成型
许多的混合挤出成型都用来制作泡沫的内层、固体层、外层。在这种情况下选择合适的材料是非常重要的。对于外层,建议使用“更软”的材料;对于内层,建议使用更硬的材料。推荐这种结构是因为,与同一树脂的一般熔体相比,发泡的熔体有更好的流动性(更低的表观粘度)。如果层间的粘度不同,会导致泡沫结构的劣化或破坏。
实验表明,固体层可以使用比泡沫层熔点高2-3倍的树脂,可以形成良好的泡沫结构。(文章来源于网络)