马秀清,翟文斌,王治鹏,程 琨
( 北京化工大学,机电工程学院,北京100029)
摘要:三层共挤吹塑薄膜可将产品的多种特性在挤出过程中进行复合,并能大幅度地降低成本,因而其应用越来越广泛。以LDPE/HDPE/LDPE 三层共挤出薄膜为例,确定了三层共挤吹膜机头的流道结构,使用ICEMCFD对机头流道划分全六面体网格,采用POLYFLOW对机头流道内等温流动过程进行求解并分析了压力场、速度场和剪切速率场。机头流道流场的研究结果表明,层分配流道压力降较高,共挤出流道压力降较低; 层分配流道存在滞留区,熔体汇入共挤出流道后,相邻层熔体的速度分布向该层速度分布方式不断变化; 层分配流道中,沿螺旋槽轴线方向,剪切速率逐渐降低,随着层数的增加,共挤出流道壁面上的剪切速率减小。
关键词:多层共挤吹塑薄膜;数值模拟;压力场;速度场;剪切速率场
0 引言
随着市场对聚合物挤出包装材料性能要求的不断提高,单层包装材料已无法满足人们对包装薄膜(片材)产品的特殊要求[1],而多层复合包装由各单层薄膜(片材)各自承担一部分功能,可以满足这些要求。目前,多层复合薄膜的成型方法主要有湿法复合、干法复合、挤出涂覆及共挤出复合等[2]。与其他工艺相比,共挤出复合生产的薄膜层厚可以更薄,降低成本,成为多层复合薄膜的主要生产方法之一,应用较为广泛。
国内外对于共挤出复合法已有很多相关的研究。武停啟[3]通过复合共挤的一维计算发现,共挤出中界面处速度和剪切应力连续。Yu等[4 - 8]在复合共挤出一维计算方面进行了深入研究,阐述了界面处速度和剪切应力连续等规律。Perdikoulias[9]用4种不同分子量分布(MWD)的低密度聚乙烯(LDPE)在双层共挤环形机头中进行实验,指出了宽分布的材料更倾向于出现界面不稳定。Ahmed[10]对2种高密度聚乙烯(HDPE)和1种LDPE的平面收缩狭缝流动进行了实验观察,并与采用Wagner本构方程的模拟结果进行了比较。Anderson[11]研究了矩形流道中聚苯乙烯(PS)的共挤流动,指出由第二法向应力差引起的弹性重排可以形成十 分复杂的界面形状。Michaeli[12]采用电子工程的网络理论( network theory)计算了平面螺旋吹膜机头流道的流场。尹华涛[13]等采用双节点有限元法和曲面坐标法求解了衣架机头内复合共挤出的界面位置,分析了物料特性和进口流率对机头出口处界面位置分布的影响。邓小珍[14]以异型材为对象,对上下分层和芯壳分层的气辅共挤成型过程进行了实验和模拟。解挺等[15]介绍了共挤出物料的黏度比、机头温度和流道几何形状等因素对共挤出流动的影响Huang[16]分析了螺旋芯棒机头二维流道几何参数和流动均匀性的关系。吴卫平[17]用计算机设计优化了管材螺旋机头的几何尺寸和加工工艺,并用MDPE和HDPE进行了实验验证。张敏[18]对非牛顿流体共挤出流动过程的有限元模拟技术进行了研究,得出了有限元方法求解的技术路线。
共挤出技术可使产品具有特殊性能并降低成本,多层共挤薄膜消费市场巨大,发展前景广阔,在复合包装材料的加工过程中,共挤机头是核心部件。因此设计1个结构合理、流道设计巧妙的共挤机头十分关键[19 - 20]。然而,迄今为止,国内对复合共挤出技术的理论研究还不完善。文章在前人研究的基础上,采用某公司实际使用的1种多层共挤吹膜机头结构作为参考,对三层共挤吹塑薄膜平面叠加螺旋机头进行流道的结构设计。每层熔体的层分配流道结构较为相似,各层熔体按复合顺序依次汇入共挤出流道,完成复合。
1 三层共挤吹膜机头的主要参数
图1、2分别为三层共挤吹塑薄膜平面叠加螺旋机头流道几何模型及螺旋分配系统主要结构。文章采用的机头使用两台或三台挤出机生产ABA型三层共挤吹塑薄膜,物料组合结构形式为LDPE/HDPE/LDPE。模型具有周期对称的特点,为了减小计算规模,提高计算精度,文章使用周期性边界对1/8的流道进行模拟,周期性边界入口所在平面为XY平面绕Y轴旋转-22.5°后形成的面,周期性出口所在平面为XY平面绕Y轴旋转-67.5°后形成的面。
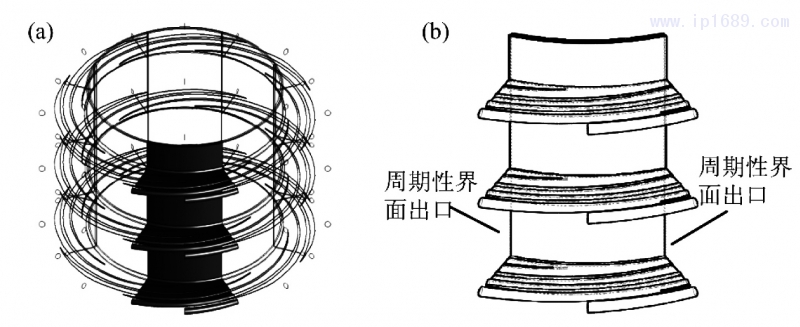
图 1 流道几何模型
(a)轴测图 (b)周期边界
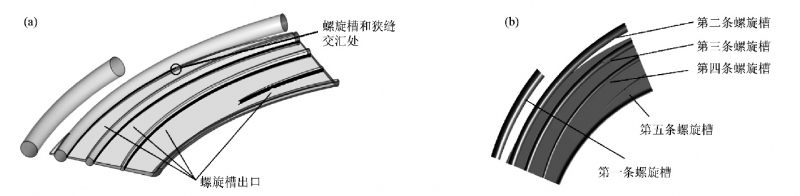
图 2 与螺旋分配系统相关的名称
(a)螺旋槽和狭缝交汇处及螺旋槽出口 (b)螺旋槽编号
2 模型的建立和边界条件设置
2. 1 数学模型
聚合物共挤出过程中,由于流道结构和聚合物流变行为的复杂性,为了便于计算且符合实际加工条件,数值模拟的简化和假设为:聚合物熔体为不可压缩流体,熔体进行等温和稳定层流流动;熔体之间互不相容且无滑移,不计界面张力,忽略体积力、惯性力,流道壁面无滑移。
连续性方程如式(1)所示。

式中:V 为速度矢量,m/s;ρ 为熔体密度,kg/m3;t 为时间,s。
动量方程如式(2)所示。

式中: P为静水压力,Pa;τ为应力张量,Pa;g为重力加速度,m/s2。
广义牛顿流体的本构方程如式(3)所示。

式中:η(·γ)为非牛顿黏度(表观黏度),Pa·s; γ·为剪切速率张量,1/s
2.2 有限元模型
将 SOLIDWORKS 中建立的流道模型导入ICEMCFD中进行离散,划分有限元网格,使用周期性边界对1/8的流道进行模拟。采用笛卡尔直角坐标系,Y正方向为挤出方向,以XY 平面为基准,Y 正方向为旋转轴,旋转-22. 5°为周期性入口所在平面,旋转-67. 5°为周期性出口所在平面。利用ICEMCFD特有的多块结构化网格划分方式对整个机头流道全部采用填充性更佳的八节点六面体网格离散。
2. 3 物性参数
模拟分析所用物料为低密度聚乙烯(LDPE)和高密度聚乙烯(HDPE)。LDPE 的拟合流变参数和HDPE的流变参数如表 1所示。

表 1 材料的物性参数
2.4 边界条件
(1)入口边界:由于模型的周期对称性,体积流率按1/8模型计算,第一层LDPE入口边界的体积流率为2. 64×10-7m3/s,第一、二、三层体积流率之比为Q1∶Q2∶Q3 =1 5∶1. 5∶ 1。
(2)流道壁面边界:模拟分析采用无滑移边界条件,且采用Navier滑移定律,降低了计算收敛难度,如式(4)所示。

式中:f(v) 为剪切应力,Pa;vs为壁面上熔体的切向速度,m/s;vwall为壁面切向速度,m/s;k为滑移系数,Pa·s/m;e为控制方程线性关系。k和e均是与材料相关的参数。文章取vwall = 0,k =108,e = 1。
(3)周期性边界:模型以Y轴正方向为中心,呈-45°周期对称,设置周期性入口边界和周期性出口边界,组成周期性边界。
(4)分界面边界:界面上的速度连续,熔体不能穿越界面,即vn = 0;界面两侧的切应力和法向应力连续。
(5)出口边界:忽略膜泡所受牵伸和吹胀的影响,fn = 0,fs= 0。
3 数值模拟结果及讨论
3.1 压力场结果分析
模型流道的压力场及周期对称模型形成机头整体压力场,如图3所示。从图3中可以看出,流道内压力沿熔体流动方向逐渐减小。第一层压力最大,结合模拟所用的LDPE,最大值约
为32. 32 MPa,第二层和第三层压力较小,机头压力降较大。这和螺旋芯棒机头压力降较大的特点相一致.
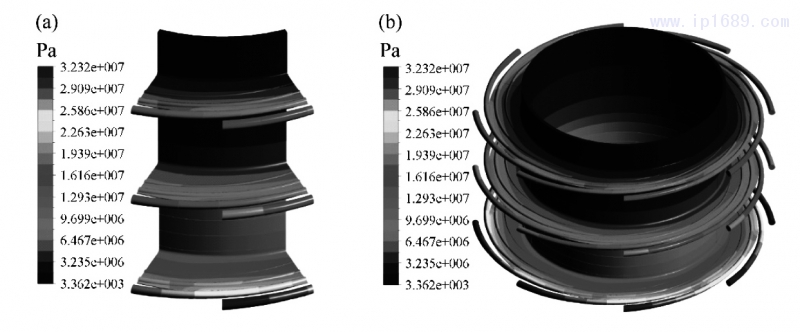
(a)计算域的压力分布云图 (b)整个流道的压力分布云图
图 3 压力分布云图
图 3 压力分布云图
第一层层分配流道的压力等压线如图4所示。在第一条螺旋槽和第二条螺旋槽前段部分,等压线垂直于螺旋槽轴线;在狭缝中,等压线是以Y轴为中心的带有“Z”形弯折的一簇类同心圆,“Z”形弯折均发生在螺旋槽区域中,弯折点位于螺旋槽和狭缝的相贯线附近。在螺旋槽和狭缝交汇处,等压线开始变成类同心圆形状,且该处等压线十分密集,压力梯度较大;沿狭缝流动方向,压力梯度越来越小。图5为各条螺旋槽出口在层分配流道对称平面上的压力降,这是模型周期对称后一条完整螺旋槽的出口在层分配流道对称平面上的压力降。从图5中可以看出,螺旋槽沿程,压力梯度整体上不断减小,在第五条螺旋槽末尾段趋于零,在螺旋槽与狭缝交汇处所对应的角度上,压力出现一小段局部的升高。
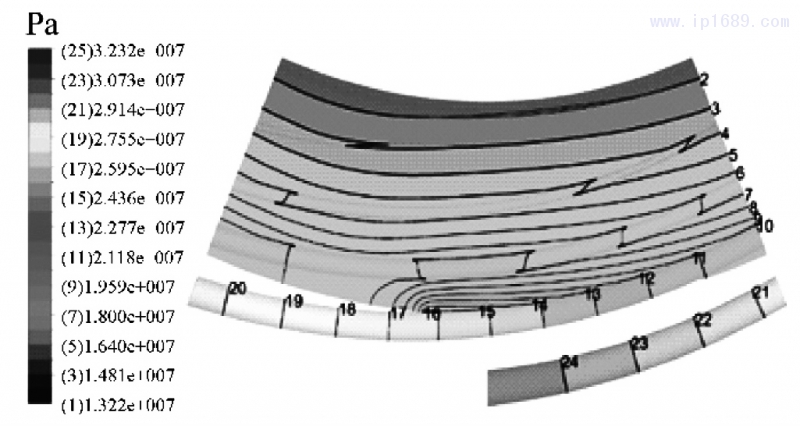
图 4 第一层层分配流道等压线
3.2 速度场结果分析
图6a为整体速度分布云图,图6b为XY平面绕Y轴旋转-45°截面上的速度分布云图。由图可知,共挤出流道壁面上的速度几乎为0(10 -5~10-4m/s),较好地接近壁面无滑移假设。
图7为第一层熔体层分配流道对称平面上的速度分布云图。熔体受到壁面的粘附作用,沿螺旋槽径向速度降低;随着螺旋槽径向尺寸不断减小,流动截面逐渐变小,沿螺旋槽轴线方向,
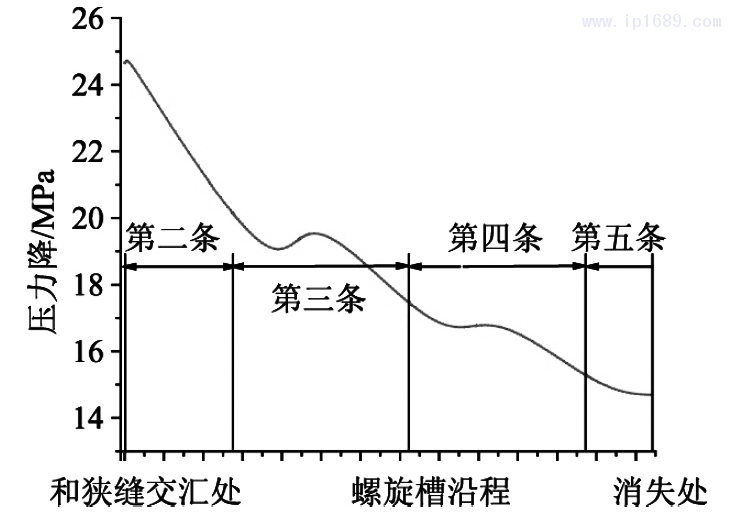
图 5 螺旋槽出口在对称平面上的压力降
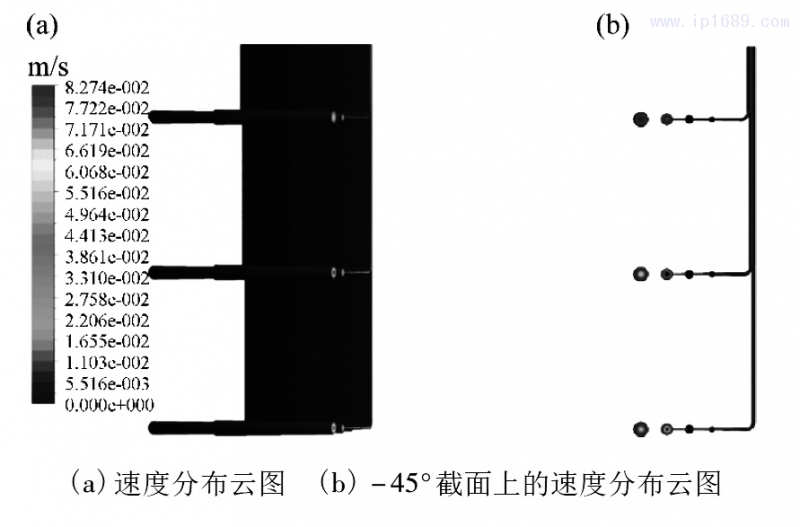
图 6 速度分布云图
速度先增大后减小,极大值出现在螺旋槽和狭缝交汇处及其上游。图8为各条螺旋槽出口在层分配流道对称平面上的速度分布。由图8可知,螺旋槽和狭缝交汇处的漏流最大,接着,迅速减小,在螺旋槽沿程方向上,运行至螺旋槽和狭缝交汇处所对应的角度,螺旋槽中的流量受到螺旋槽和狭缝交汇处漏流的补充而增大,漏流逐渐增大,但随着狭缝高度的增大,流动截面增大,所以幅度不断减小。运行至滞留区所对应的角度,均会再次出现低点.
4.3 剪切速率场结果分析
图9为第一层层分配流道的剪切速率场。图中的最高剪切速率控制为1500 s- 1,实际深色区域最高值为4363s-1,出现在螺旋槽和狭缝交汇处的狭缝壁面上。从图9中可以看出,沿螺旋槽轴线方向,剪切速率逐渐降低;沿狭缝流动方向,剪切速率逐渐减低,螺旋槽区域出现局部的低值;在滞留区,剪切速率出现最低值,在螺旋槽和狭缝交汇处出现最高值。这和速度场的分布规律较为一致。
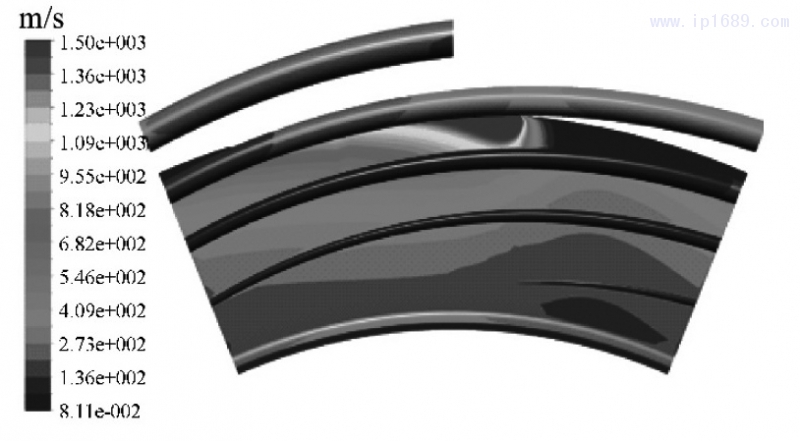
图 9 层分配流道剪切速率分布云图
图10为共挤出流道的剪切速率场,图11为界面上的剪切速率场。从图10、11中可以看出,在各层熔体汇入共挤出流道处,界面上的剪切速率最大,随着层数的增加,共挤出流道壁面上的剪切速率减小。以第一层为例,当第二层汇入共挤出流道后,第一层脱离了第一、二层间共挤出流道壁面的影响,速度梯度随着层数的增加而降低,剪切速率减小。
4 结论
(1)压力场:层分配流道中,螺旋槽沿程方向的压力不断降低,在螺旋槽和狭缝交汇处的对应角度上出现局部高点;沿着某一挤出径向的径向位置减小方向,压力不断降低,在螺旋槽区域出现平台。
(2)速度场:层分配流道中,螺旋槽出口中心线上的速度不断降低,在螺旋槽和狭缝交汇处的对应角度上出现局部高点。层分配流道存在滞留区,层分配流道出口速度呈类正弦曲线的分布,螺旋槽和狭缝交汇处对应的角度附近为高点,滞留区对应的角度附近为低点。
(3)剪切速率场:层分配流道中,沿螺旋槽轴线方向,剪切速率逐渐降低,在螺旋槽区域出现局部的低值。共挤出流道中,界面1、2上的剪切速率分别在第二、三层熔体汇入共挤出流道处最佳。随着层数的增加,共挤出流道壁面上的剪切速率明显减小。
参考文献:
[1]贾明印,薛平,朱复华,等.共挤出技术在聚合物成型加工中的应用及其设备的最展[J].工程塑料应用,2006,34 (1):66-69.
[2]苗立荣,张玉霞,薛平.多层共挤出塑料薄膜机头的结构改进与发展[J].中国塑料,2010,24(2):11-20.
[3]武停啟.聚合物共挤出复合流动机理及数值模拟研究[D].北京:北京化工大学,2006.
[4]YUTC,HANCD.Stratified two-phase flow of molten polymers[J].Journal of Applied Polymer Science,1973,17(4):1203-1225.
[5]HAN C D.Multiphase flow in polymer processing[M].New York:Academic Press,1981:341-342.
[6]HANCD,CHINHB.A study of coextrusion in a circular die[J].Journal of Applied Polymer Science.1975,19: 1875-1883.
[7]HANCD,SHETTYR.Studies on multilayer film coextrusion I. therheology of flat film coextrusion[J].Polymer Engineering andScience,1976,16(10):697-705.
[8] HANCD,CHINHB.Theoretical prediction of the pressure gradientsin coextrusion of non-newtonian fluids[J].Polymer Engineering and
Science,1979,19(16):1156-1162.
[9]PERDIKOULIAS J,TZOGANAKIS C. Interfacial instability in coextrusion flows of low-density polyethylenes: experimentalstudies[J].Polymer Engineering and Science,2000,40(5):1056-1064.
[10]AHMEDR,LIANGRF,MACKLEY M R.The experimental observation and numerical prediction of planar entry flow and die swell for molten polyethylenes[J].Journal of Non-Newtonian Fluid Mechanics,1995,59(2 /3):129-153.
[11]ANDERSON P D,DOOLEY J,MEIJER H E H. Viscoelastic effects in multilayer polymer extrusion[J].Applied Rheology,2006,16 (4 ):198-205.
[12]MICHAELI W,BLMERP.Flat spiral dies-rheological design with network theory[J].Journal of Polymer Engineering,2004,24 (1 /2 /3):137-154.
[13]尹华涛,江波.共挤出机头中的聚合物熔体流动分析[J].现代塑料加工应用,2003,15(4):44-47.
[14 邓小珍.塑料异型材气体辅助共挤出成型的实验和理论研究[D].南昌:南昌大学,2014.
[15]解挺,朱元吉,尹延国,等.共挤出的影响因素[J]塑料科技,1996(5):30-33.
[16] HUANG C C. A systematic approach for the design of a spiral mandreldie[J]. Polymer Engineering and Science,1998,38(4):573-582.
[17]吴卫平.用于管材加工的螺旋机头[J].塑料工业,1991 ( 2 ):30-34.
[18]张敏.双组分聚合物异型材共挤出过程的数值模拟研究[D].济南:山东大学,2007.
[19]徐玉兴,李国胜.三层复合薄膜共挤机头流场仿真分析[J].CAD/CAM 与制造业信息化,2013(10):63 - 68.
[20]WHITE J L,UFFORDRC,DHAROD KR,et al.Experimental and theoretical study of the extrusion of two-phase molten polymer systems[J].Journal of Applied Polymer Science,1972,16(6):1313-1330CAD/CAM 与制造业信息化,2013(10):63-68.