李 洁
泸州职业技术学院 机械工程系,四川 泸州 646000
●摘 要: 根据需要完成的任务,实现特定的功能,依据现有的参数,设计一款往复螺杆注射系统。该系统由三部分组成,第一部分:驱动装置以及传动装置,选择三相异步电机作为驱动装置,然后通过单级齿轮减速器来把电机的转速传递到运动部件;第二部分:塑化装置,该装置利用螺杆和料筒实现对融化塑料的塑化;第三部分:注射装置,利用液压缸推动螺杆实现注射,并且可以在下一个循环之前实现螺杆的退回。该注射系统具有结构简单、制造成本低、加工制造容易的特点。
●关键词: 注射机;驱动装置;传动装置;塑化装置;注塑装置;往复螺杆
随着国家各项政策的颁布,对于当下注射机的发展要求要做到质量轻便、节约资源、能源损耗少、 效率高、成本小。传统的注射机质量体积庞大、工作效率低,而本文设计的往复式注射机完善了传统注射机的这些缺点。往复螺杆式注射机在实际工作时,在锁模力只有传统技术三分之一时,仍然可以保证产品成型的质量要求,即大大提高了工作效率,也极大地保证了产品的精度要求,对于资源节约、能源节约和成本控制都有着极大的意义合理的注塑系统对注射机来讲至关重要,注射机要完成塑料的塑化以及加压均需靠注塑系统。
按照生产塑料产品的流程来说,注塑系统首先要保证可以融化、塑化一定量的塑料,然后把这些塑料在一定的压力、速度下注射到模具中;保压一段时间防止融化的塑料反向流动,考虑到材料热胀冷缩的属性,所以为了防止产品的收缩,需要往模具中多加入一些材料【1-6】。市面上的注射机的注塑系统 大多采用往复螺杆式,其次是柱塞式。
本次设计要求从经济性、安全性、合理性几个方面考虑。本次的设计对象是往复式螺杆注射机,通过资料查询的基本数据,以螺杆直径为设计出发点,使用类比设计的思想对料筒、喷嘴和减速器进行参数计算和材料选择。本次设计的往复式螺杆注射机的要求是机构简单、制造性好、性能质量可靠。本次设计主要围绕以下内容展开:传动装置设计、塑化装置设计、注射装置设计,并对其结构进行必要的强度设计。
1 总体方案设计
1.1 柱塞式注射装置
柱塞式注射装置由定量加料装置、塑化部件、注射液压缸、注射座移动液压缸等组成。柱塞式注射装置主要根据其自身结构的原因,导致其具有以下缺点:塑料受热不均匀,限制了料筒的塑化能力。塑料的热传导属性差,在加热的时候会导致料筒中间的部分塑料还未融化,而料筒边缘的塑料已经融化,严重的会出现料筒中间塑料未塑化,而料筒边缘塑料已经分解的情况;压力损失大,分流梭与料筒内壁的狭缝导致了很大的压力损失[7],工艺条件的稳定性不易提高。注射压力需要作用在未融化的塑料上才可以传递到熔料,这会导致柱塞等速的移动中,熔料的冲模速度不均匀,而且不能保证每 次注射的熔料的量一致[8]。
1.2 螺杆预塑式注射装置
螺杆预塑式注射装置是由两个料筒组成的,一个是螺杆预塑式料筒,另一个是注射料筒,两个料筒的连接处有单向阀。与柱塞式注射装置不同的是,螺杆预塑式注射装置使用单向阀把两个料筒连接在一起。熔料先在螺杆的不断搅拌下,在预塑式料筒塑化,然后注射柱塞把熔料注射到模腔中。这极大地提高了塑化质量和塑化效果,加上取消了分流梭,所以注射压力损失不大,注射速率也得到提高,因此适用于连续注射或注射量大的注射机。考虑到需要增加一个料筒以及单向阀等部件,整个装置变得复杂、庞大,如果单向阀与两个料筒有间隙,还会导致熔料的泄露,基于上述问题,在此基础上又改进了往复式螺杆注射装置。
1.3 往复螺杆式注射装置
往复螺杆注射装置也叫螺杆一线式(简称螺杆 式)注射装置,主要由塑化部分、料斗、螺杆、传动装置 、注射座、注射座移动液压缸、注射液压缸等组 成。往复螺杆注射装置按照不同的分类方法有不同的分类形式。往复螺杆注射装置还有采用液压马达直接驱动型,可根据注射液压缸数目分为单缸式和双缸式两类结构。对于双缸式液压马达随动式注射装置,螺杆和液压马达直接连接传递运动。双注射油缸放置在料筒两侧平行排列,注射时,液压马达随螺杆一起作轴向移动,故称随动式。这种形式的注射装置结构紧凑,能耗低,它是恒定力矩驱动装置,当螺杆出现过载时,液压马达无法驱动,起到对螺杆的保护作用,而电动机驱动装置为恒定功率驱动装置,当螺杆过载时容易扭断螺杆[9]。
1.4 方案的选定
通过上面对比可以发现往复螺杆式注射装置
具有以下优点:
(1)螺杆式注射装置塑化时可以使塑料受热均匀,以及螺杆的旋转运动也可以更好地对塑料进行塑化,所以塑料的塑化质量以及塑化效果得到了显著的提升。
(2)注射压力损失减小。
(3)生产效率高。料筒内表面的残余废料,可以通过螺杆的转动起到自清洁的效果,节省了清洗料筒的时间。
(4)螺杆式注射装置可以对塑料进行染色加工,而且料筒清洗比较方便。螺杆式注射装置机构上相比柱塞式注射装置较复杂,会导致注射机制造成本的增加,但是因为其优点很好地解决了生产方面的困难,市场应用比较广泛,所以本研究最终选择往复螺杆式注射装置。
2 主要零部件设计
2.1 螺杆设计
注射机螺杆分为渐变型螺杆、突变型螺杆、通用型螺杆。
渐变型螺杆:螺槽深度逐渐过渡,适用于软化温度变化范围大的熔料。
突变型螺杆:指螺杆槽深度由深变浅的过程,适用于具有稳定熔点的塑料。
通用型螺杆:压缩段长度在突变型螺杆和渐变型螺杆之间。螺杆常见压缩比见表1。
▲ 表1 常见注射螺杆的压缩比
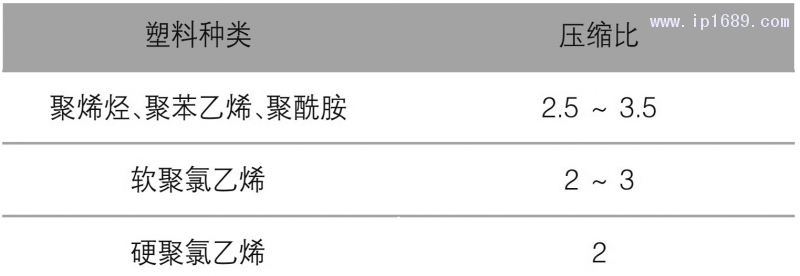
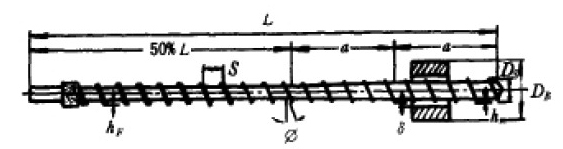
为了避免注射时出现熔料堆积以及熔料的回流,所以螺杆的头部一般选择锥形尖头,如图2所示。

2.2 螺杆的尺寸
(1)长度L的确定
螺杆直径Ds=40 mm。查阅资料得知螺杆长度与螺杆直径的比值(L/D)在18~22之间,常选择20:1。所以螺杆的长度为L=40×20=800 mm。而通用螺杆不同段占的比例不一样,加料段、压缩段、均化段占的比例分别为50%、25%、25%,所以加料段、压缩段、均化段的长度分别为400、200和200 mm。
(2)确定均化段螺槽深度h3和压缩比i
螺槽深度(h3)越小,那么螺杆旋转产生的剪切热越大,此时消耗螺杆的功率也就越大。按照经验公式来算:一般h3=(0.04~0.07)Ds。此处取h3=0.065Ds=2.6 mm。
压缩比(i):加料段螺杆的螺槽深度h1与均化段螺槽深度h3的比值,即i=h1/h3。取i=2.1,则h1=i·h3=2.1×2.6=5.4 mm。
(3)螺杆材料的选用
考虑到注射机螺杆的工作环境,不仅要承受很大的作用力,而且要不断地做往复运动。所以在选择螺杆材料的时候要保证高强度、耐磨损及耐腐蚀,然后为了保证工作过程中的平稳,螺杆的表面粗糙度一定不高于0.4 μm。所以材料一般选择40Cr,为提高螺杆的耐磨性和耐腐蚀性,螺杆的表面要经过喷涂处理。
2.3 螺杆的强度校核
当注射机压力为30 MPa时,强度校核计算公式为:
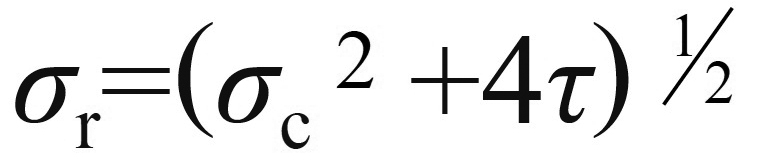
经计算,螺杆强度满足要求。
3 传动装置的设计
3.1 电动机的选择
(1)类型和结构构型式
考虑到在注射机启动瞬间容易出现超载的情况,所以电动机的功率选择要略大于螺杆工作功率,因此选择Y系列三相异步电动机。
(2)电动机的功率
查得:η1—联轴器传动效率,0.99;η2—每对轴承传动效率,0.99;η3—圆柱齿轮的传动效率,0.97。
总传动效率:

电动机所需功率:
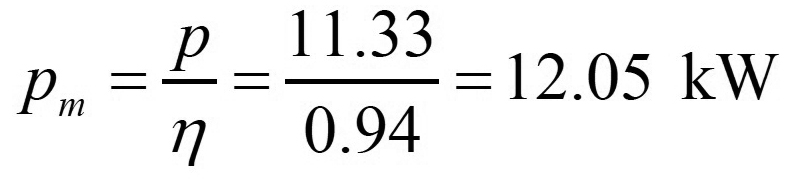
电动机转速:

3.2 减速器的设计计算
电动机型号为Y180L-6,满载转速为970 r/min,
所以传动比为:
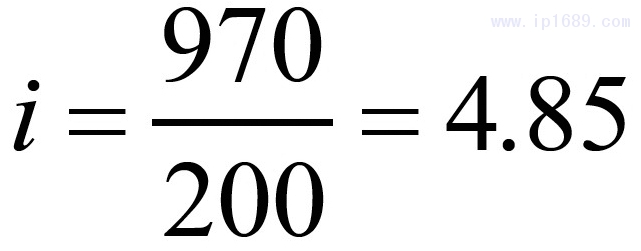
(1)各轴的转速
电动机轴 nm=970 r/min
Ⅰ轴 n1=nm=970 r/min
Ⅱ轴 n2=200 r/min
(2)各轴的输入功率
12:21ሆ!ڼ58ਝ!ڼ21DŽጺڼ441Dž
3齿轮传动设计图如图3所示。
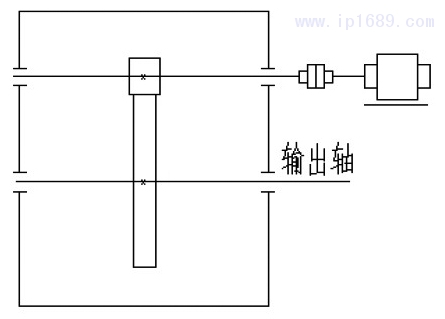
▲ 图3 齿轮传动简图
(3)齿轮类型、精度等级、材料及齿数的选择
齿轮类型:直齿圆柱齿轮。
考虑注射机的工作转速不高,所以齿轮的精度 等级为7级。
小齿轮材料:调质处理的40Cr,布氏硬度为280;
大齿轮材料:调质处理的45钢,布氏硬度240。
齿数:当小齿轮z1=24,则大齿z2=5×24=120。
(4)强度校核
按齿面接触强度设计,设计计算公式为:
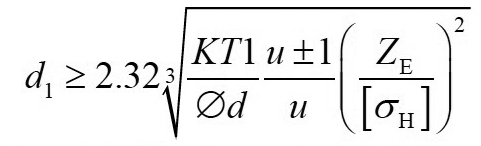
其中:K为载荷系数;T1为小齿轮传递转矩;ZE 为弹性影响系数;δH为接触疲劳强度。
按齿根弯曲强度设计,设计计算的公式为:
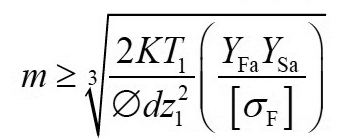
其中:K为载荷系数;T1为传递转矩;YFa为应力
校正系数;YSa为应力校正系数。
(5)齿轮零件图如图4所示
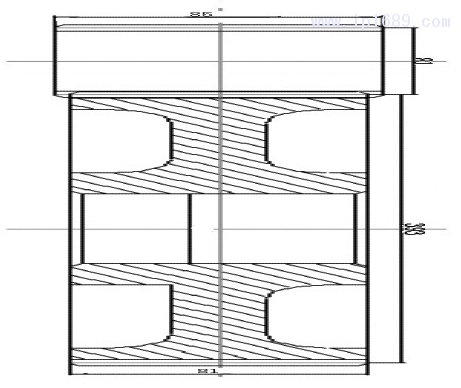
▲ 图4 齿轮零件图
4 注射装置的设计
4.1 喷嘴的设计
(1)尺寸的确定
查阅资料可知,喷嘴直径根据以下公式确定:
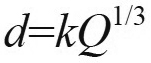
(2)材料的选用
在材料的选择上可以与料筒相同,即也选用45
钢[11]。
4.2 螺杆最大行程计算


4.3 液压油缸的直径计算

4.4 注射力计算
注射力根据以下公式确定:

其中:F为注射力;Ds 为螺杆直径;p为注射压力。
5 总结
本文根据给定的设计参数介绍了一种往复螺杆式注射系统的设计,所设计的注射系统包括传动装置、塑化装置、注射装置三大部分[12]。传动装置采用了单级齿轮减速器和三相异步电动机满足设计要求,电动机输出的转速经减速到要求转速后传递到螺杆上,带动螺杆转动。塑化装置采用三级变径螺杆与料筒结合完成对坯料的塑化,螺杆转动完成了坯料的疏松,同时起到剪切和混炼的作用,能提高塑化效率,改善熔融物的质量[13-14]。注射装置采用单向液压缸与往复螺杆结合,由液压缸活塞推动螺杆完成注射过程,并在下一循环的塑化过程中自动完成螺杆的退回,随着螺杆的转动,熔融塑料在料筒前端累积增多,在融料的压力下螺杆沿轴向后退,待回退到融料量满足需求时,螺杆停转,并在注射液压缸的推力下完成注射过程。所设计的装置具有结构简单、性能可靠、制造容易的特点。
参考文献:
[1] 赵银章. 旧型往复螺杆式注塑机的改造[J]. 现代塑料加工应 用, 1999(6): 2-10.
[2] 王卫卫. 金属与塑性成型设备[M]. 北京: 机械工业出版社, 1996.
[3] 项 钢. 高 效 精 密 注 塑 机 规 划 和 选 型[J]. 工 程 建 设 与 设 计,2010(3):12-16.
[4] 马海舟,潘晓铭,潘道波. 塑料注塑机快速注射部分设计与应用
[J]. 液压与气动, 2007(2): 35-40.
[5] 雄戈. 智能化全电动注塑机[J]. 国外塑料, 2009, 27(4): 25-30.
[6] 陈仲成. 革新注塑机成型条件及调整方式探讨[J]. 现代商贸工业, 2009(13): 21-27.
[7] 向鹏,李绣峰,杜遥雪. 全电动注塑机的特点及应用领域[J]. 现代塑料加工应用, 2007, 19(1): 26-31.
[8] 吴红. 小型注塑机液压系统优化设计研究[J]. 南宁职业技术学院学报, 2009, 14(1): 42-45.
[9] 刘向东. 塑性成型设备[M]. 北京: 机械工业出版社, 2002.
[10] 吴宗泽. 机械设计课程设计手册[M]. 北京: 清华大学出版社,2004.
[11] 郭建松,包建东,朱建晓,等. 低压注塑机注射装置智能化温度控制研究[J]. 工业仪表与自动化装置, 2016(6): 12-17.
[12] 一种注塑机螺杆止逆环的密封性检测方法[J]. 橡塑技术与装备, 2017, 43(8):15-16.
[13] 邹志恒. 注塑机拉杆断裂的原因及改进措施[J]. 橡塑技术与装备, 2017, 43(10): 2-5.
[14] 容晓. 注塑机故障模拟系统设计方案[J]. 产业与科技论坛,2017(10): 11-21.