黄永程,杨 斌(1),伍先明(2),杨晶晶,王鹏程,李 俏,黎志勇,刘顺彭,孙庆辉
广东理工学院,广东 肇庆 526100
摘 要:
基于Moldflflow 2018软件对薄壁塑件进行注塑成型和注塑压缩成型模拟,分别从V/P切换时的压力、填充末端压力、流动前沿温度、平均体积收缩率、气穴、熔接线和翘曲变形等方面进行对比分析。结果表明:采用注塑压缩成型工艺加工的薄壁塑件质量优于由注塑成型工艺得到的薄壁塑件,该对比分析结果对薄壁塑件的实际加工具有一定的指导意义。
关键词: 薄壁塑件;注塑成型;注塑压缩成型;翘曲变形
随着社会的飞速发展,塑料制件在家电、汽车、 高铁、航空航天等领域得到广泛应用。其中薄壁塑件因自身刚度较差,易出现较严重的翘曲变形,致使塑件的形状和尺寸偏离原始设计要求,进而导致外观质量变差、装配性能下降。采用传统加工方法很难得到高质量的薄壁塑件,为此诸多研究者对注塑成型工艺进行了大量的数值模拟和实验对比分析。例如,肖民等[1]模拟分析了保压工艺对薄壁塑件成型的影响,并通过注塑实验进行了验证,结果表明,保压工艺对塑件翘曲变形具有显著影响。殷筱依[2]采用正交试验法分析了工艺参数和模具结构对薄壁塑件翘曲变形的影响,从而确定了影响塑件翘曲的主要因素,同时优化了模具结构,最终得到一组最优成型工艺参数(该工艺条件下得到的塑件翘曲变形量最小)。江青松等[3]采用耦合有限元分析方法对薄壁塑件应力分布和翘曲变形进行分析。结果表明,随着翘曲变形的产生,塑件内的残余应力相应减小;壁厚是影响翘曲变形的主要因素,而工艺参数的影响相对较小。此外,为提高薄 壁塑件的质量,还可采用特殊的成型方法,如注塑压缩成型。注塑压缩成型是一种注塑和压缩模塑的组合成型技术,其是将塑料熔体注入稍微开启的模具内,待注塑完毕,在熔体固化前通过外力进行二次合模,从而使塑件均匀受力以减少残余应力、提高塑件性能。诸多研究表明,与传统注塑成型相比,注塑压缩成型工艺具有很大的优越性。例如,J Y Ho等[4]采用有限元法对厚1.5 mm、半径70 mm的圆盘注塑压缩成型进行了仿真和实验,并对比分析了模拟及实验数据,研究发现,与注塑成型相比,注塑压缩成型的剪切速率更低,剪切应力分布更均匀。本研究对薄壁塑件的注塑成型和注塑压缩成型工艺进行了对比分析,为薄壁塑件的实际生产提供参考。
1 薄壁塑件前处理
1.模型建立
薄壁塑件是指流长厚度比,即熔体从进入模具到型腔最远点的流动长度与塑件平均壁厚之比在 100或150以上的塑件(或厚度小于1 mm,同时投影面积在50 cm2 以上的塑件)。本研究以某品牌笔记本电脑显示器外壳作为分析模型(如图1所示),其外尺寸为340 mm×230 mm×1.5 mm,内尺寸为310 mm×175 mm×1.5 mm,属于薄壁塑件。在Pro/E 中建立该显示器外壳三维模型(图1(a)),然后导入CAD Doctor对其进行修复,再把修复后的模型导入Moldflflow中进行3D网格划分(图1(b))。该模型的四面体数为57 628,节点数为10 752,最大纵横比为28.26%,在允许范围内。
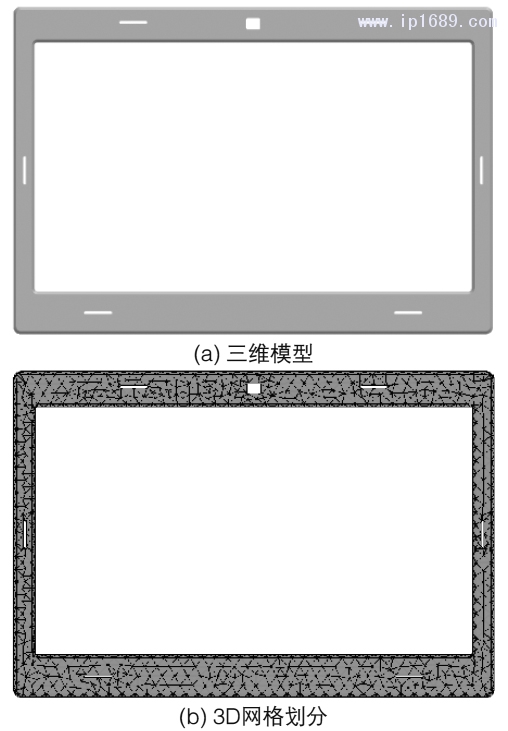
1.2 材料选取
考虑到笔记本电脑显示器外壳对机械强度、散热效果、质量和光泽度等的要求,选用工程塑料 PC+ABS(聚碳酸酯与丙烯腈-丁二烯-苯乙烯共聚物的共混物),由该材料制备的显示器外壳具有壁薄、质轻、强度高、散热快、屏蔽好等突出优点[5]。本实验选用牌号为Baybtend FR3001的PC+ABS材料,该材料的推荐模具表面温度为70℃、熔体温度为260℃,材料流动性较好,其黏度曲线如图2所示。
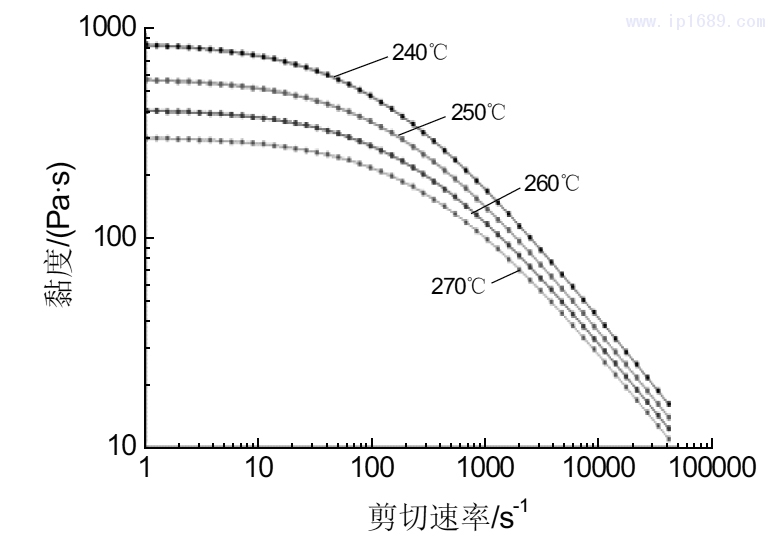
1.3 流道及冷却系统设计
显示器外壳塑件较薄且面积较大,故采用一 模一腔,4个浇口进料。通过Moldflflow 2018软件进行分析,最终确定的最佳浇口位置为N392、N293、N1096、N1157,如图3所示。
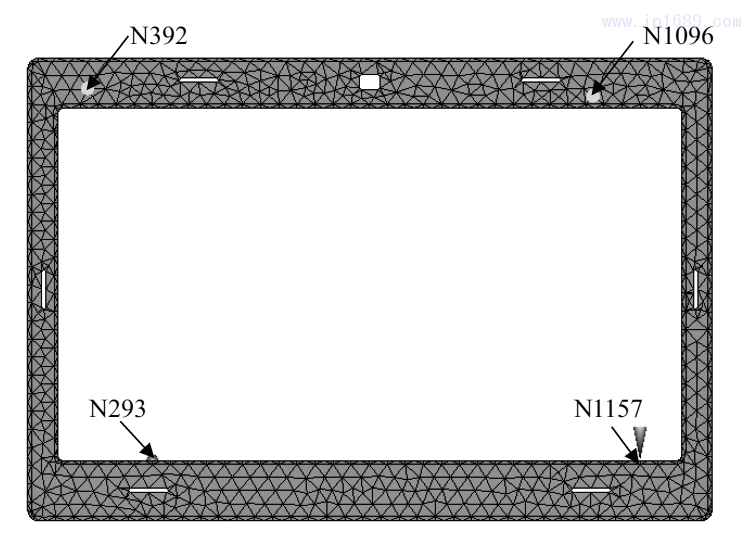
此外,为不影响塑件外观,采用潜伏式浇口,进胶点位于壳体背面。浇口始端直径为1.2 mm,末端直径为6 mm;分流道直径为6 mm;主流道始端直径为8 mm,末端直径为6 mm;冷却水道直径为8 mm,水道中心距为30 mm。整个系统如图4所示。
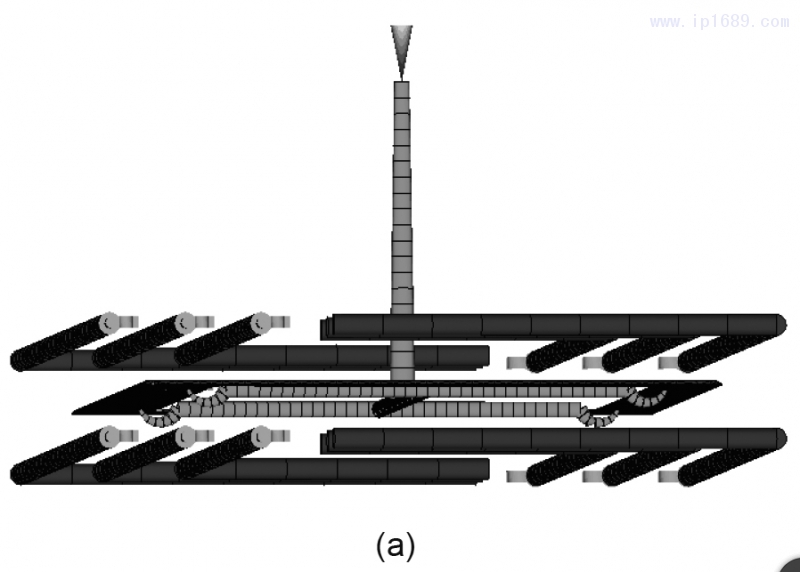
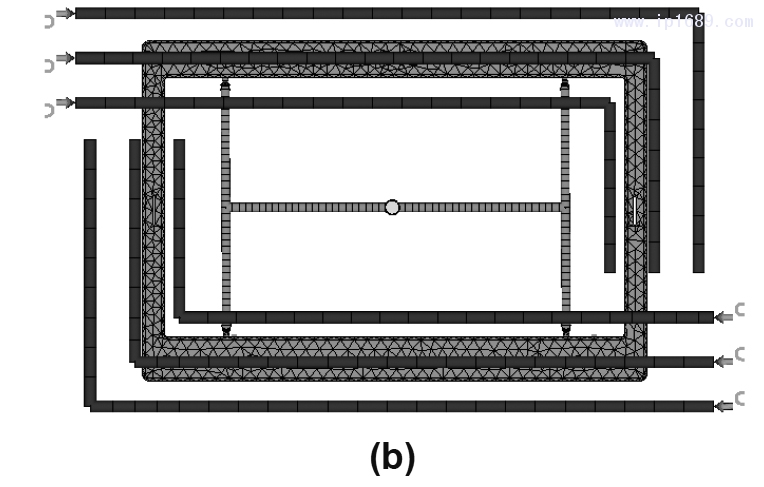
2 工艺分析
采用Moldflflow对塑件模型进行模流分析,结果显示,在塑件成型过程中能够实现充填平衡和均匀冷却,进而验证了所设计浇注系统和冷却系统的合理性和有效性。根据材料自动匹配成型条件,成型条件均采用默认值。
2.1 V/P切换时的压力和填充末端压力
V/P切换时的压力显示了从速度控制切换到压力控制时,模具内整个流动路径的压力分布,压力越大说明熔体流动阻力也越大。本实验的最大(V/P切换时)压力发生在熔体注射位置附近(如图5所示),其中注塑压缩成型的最大压力为23.45 MPa,而注塑成型的最大压力达到180 MPa,且出现短射现象。
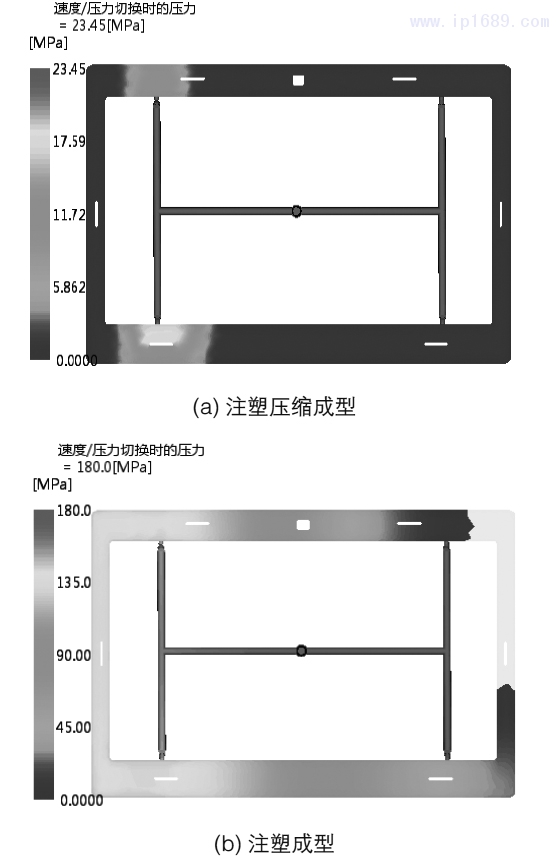
填充末端压力显示了在填充结束时压力在模具中沿熔体流动路径的分布情况。与普通注塑成
型相比,注塑压缩成型型腔可以自动调整,在注塑过程中所需压力较小。图6为上述两种成型工艺的填充末端压力模流分析结果。从图6可以看出,注塑压缩成型的填充末端压力最大值为23.02 MPa,其制品在低压状态下完成充填,而注塑成型的填充末端压力最高达到144 MPa。
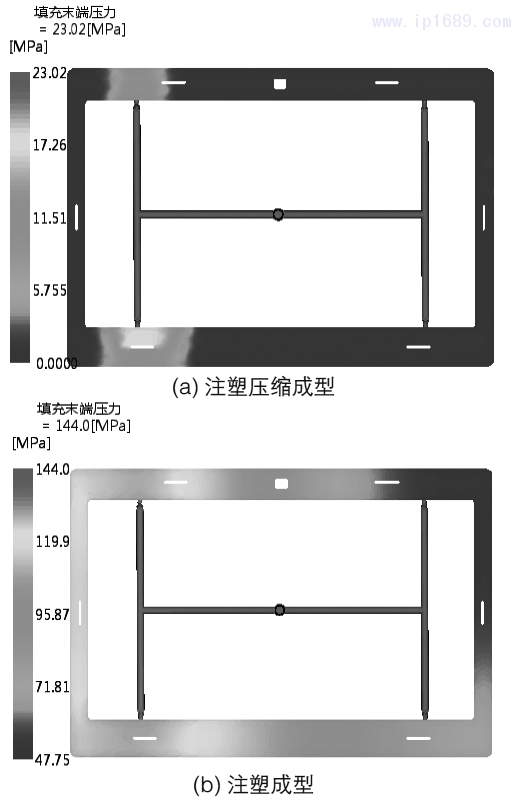
2.2 流动前沿温度
流动前沿温度是熔体充填一个节点的中间流温度,代表截面中心的温度。流动前沿温度过高会导致材料降解、制品产生表面缺陷,温度过低则会发生滞流或短射。图7为普通注塑成型与注塑压缩成型的流动前沿温度模流分析结果。由图7可知,注塑压缩成型的温度变化范围小于注塑成型,前者的温度变化比较均匀。
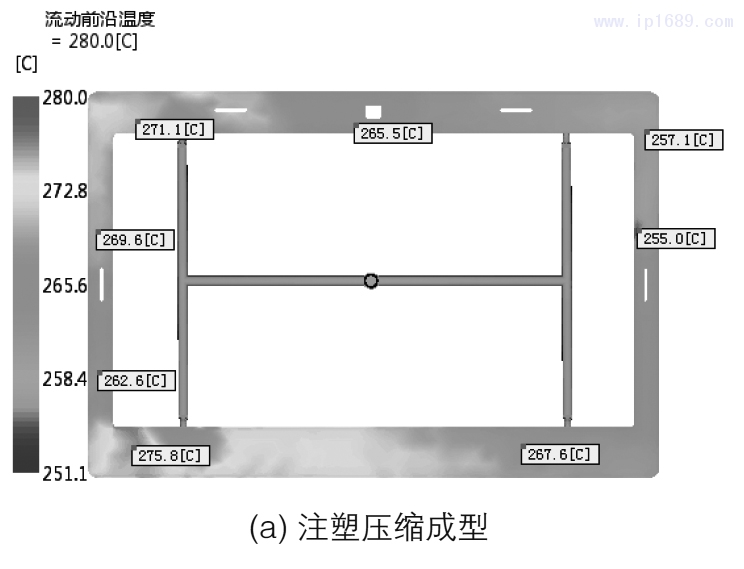
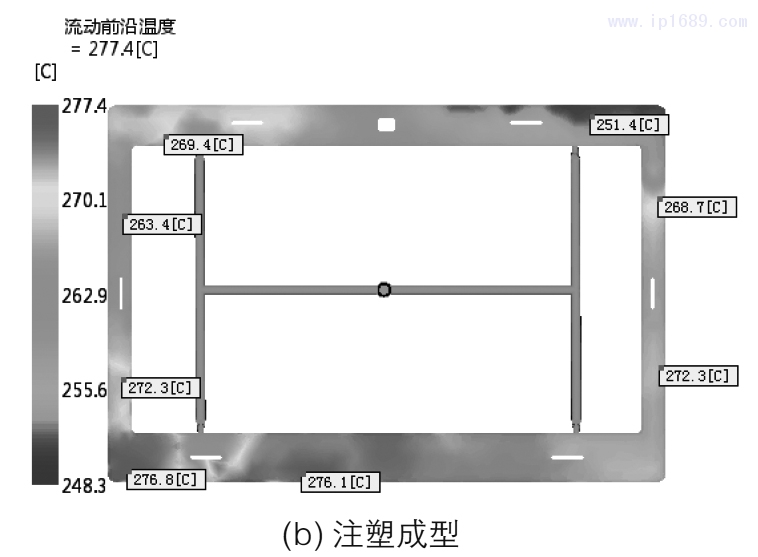
2.3 平均体积收缩率
体积收缩率显示了每个单元(在顶出时)相对于自身原始体积的收缩率,体积收缩必须均匀分布在整个塑件上才能减小翘曲变形。图8为普通注塑成型与注塑压缩成型的平均体积收缩率模流分析结果。从图8可以看出,注塑压缩成型工艺的平均体积收缩率变化较小,而注塑成型工艺的体积收缩率变化较大,且出现反向收缩。
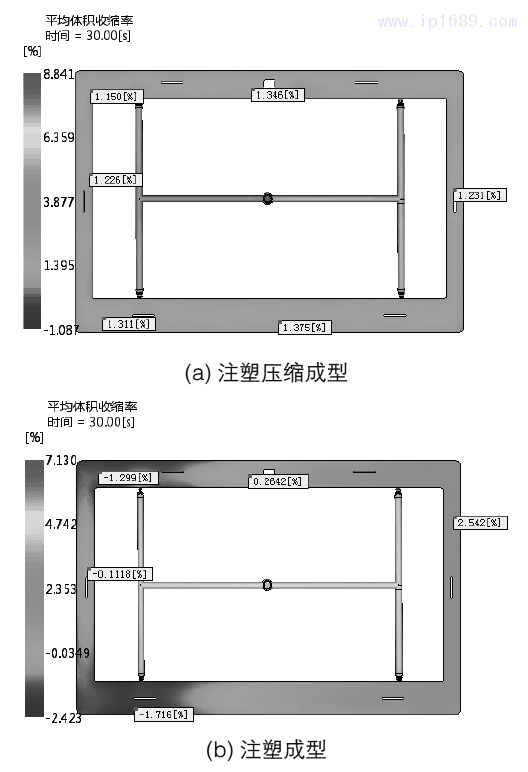
2.4 气穴
气穴通常出现在节点位置,当熔体从各个方向流向同一个节点时就会形成气穴,气穴过多会影响塑件的质量。由图9可以看出,注塑成型塑件产生了3处气穴。

2.5 熔接线
充模过程中,两股相向或平行的熔体前沿相遇,就会形成熔接线。通常两股汇合熔体前端的夹 角(汇合角)越小,产生的熔接线越明显。熔接线是 常见的塑件缺陷,其存在不仅影响制品外观质量,而且对制品的力学性能影响很大。从图10可以看出,注塑压缩成型产生的熔接线明显少于注塑成型。
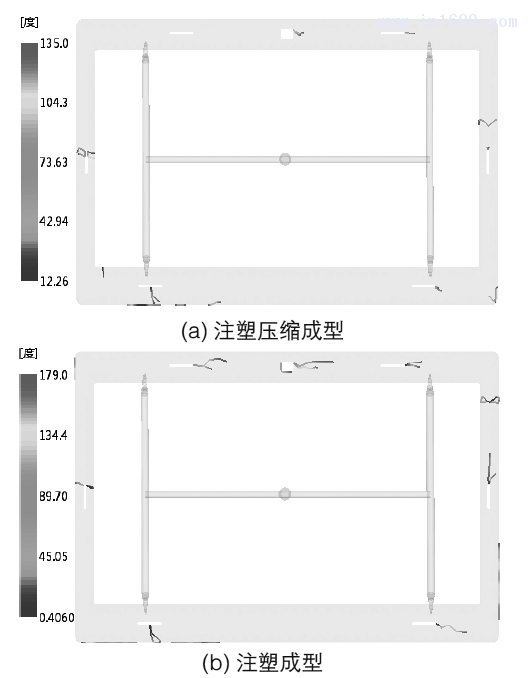
2.6 翘曲分析
翘曲变形是指塑件的形状偏离模具型腔的形状所规定的范围,是塑件常见的缺陷之一。对于薄壁塑件,其更易发生翘曲变形。从图11可以看出,注塑压缩成型的最大变形量为1.802 mm,注塑成型最大翘曲变形量为2.632 mm,注塑压缩成型产生的翘曲变形明显小于注塑成型。
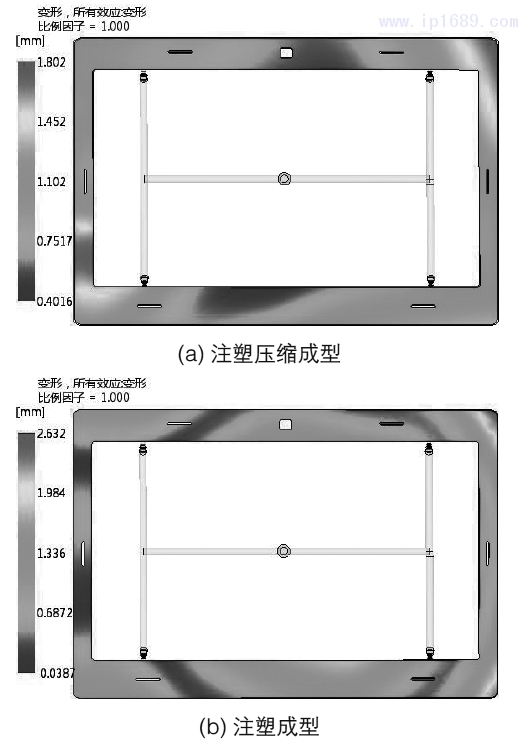
3 结论
(1)与普通注塑成型工艺相比,注塑压缩成型在V/P切换时的压力减小了87
.0%,填充末端压力减小了84.1%,制品翘曲变形量减小了31.5%。
(2)与注塑压缩成型工艺相比,普通注塑成型的流动前沿温度变化不均匀,平均体积收缩率变化较大,且出现反向收缩,同时产生较多的气穴和熔接线,严重影响了塑件的质量。
参考文献:
[1] 肖民,阮育煌,威巍. 薄壁注塑件保压工艺的CAE分析及优化 [J]. 机电工程技术, 2012, 41(11): 12-16.
[2] 殷筱依. 薄壁塑件注塑成型翘曲变形控制研究[D]. 重庆: 重庆交通大学, 2017.
[3] 江青松,柳和生,熊爱华,等. 纤维增强薄壁注塑件翘曲变形耦合有限元分析[J]. 北京化工大学学报: 自然科学版, 2017, 44(2): 103-107.
[4] J Y Ho, J M Park, T G Kang. Three-dimensional numerical analysis of injection-compression molding process[J]. Polymer Engineering and Science, 2012, 52(4): 901-911. [5] 丁清国. RHCM成型数值模拟分析及工艺参数优化[D]. 昆明: 昆明理工大学, 2013.
[6] 黄成,黄建峰,等. Moldflow 2018模流分析从入门到精通[M]. 北京: 机械工业出版社, 2018.