* 刘成娟1,刘成刚2,李延平3
( 1.福州职业技术学院,福建 福州 350108; 2.中国石油吉林石化公司研究院,吉林 吉林 132021; 3,集美大学机械与能源工程学院,福建 厦门 361021)
摘要: 综述了国内外几种注塑成型新方法和趋势。包括注塑成型计算机辅助工程 ( CAE) 、气辅注塑成型、快速 热循环注塑成型和微孔发泡注塑成型等技术的特点、研究现状和应用领域,并对发展方向进行了展望。
关键词: 注塑成型技术; 研究现状; 应用进展
注塑产品在成型时,常出现气泡、翘曲、熔接痕和浮纤等问题,这将直接影响产品的质量,使形状和尺寸达不到设计的要求,影响零件装配[1]。人们对注塑产品更高质量的追求,使得一些新的注塑成型方法应运而生。本文对注塑成型 CAE、气辅注塑成型、快速热循环注塑成型和微孔发泡注塑成型等技术进行研究,对推动注塑成型方法的研究和企业生产发展提供可靠依据,具有积极意义。
1 注塑成型 CAE 技术及特点
注塑成型 CAE 技术[2]是使用有限元、有限差分和边界元等方法,动态仿真模具型腔内塑料熔体的填充、保压、冷却和翘曲变形等,预测潜在的充填不足、熔痕和翘曲等缺陷,进而优化产品、模具结构和成型工艺参数得到优质产品的一门应用科学技术。 Moldflow 软件仿真流程,如图 1 所示。其基本优势如下: 1) “未 注 先 知”,针对所研究的 产 品,利 用Moldflow 软件仿真出产品潜在的短射、熔接痕、翘曲、气泡、水波纹和飞边等问题。
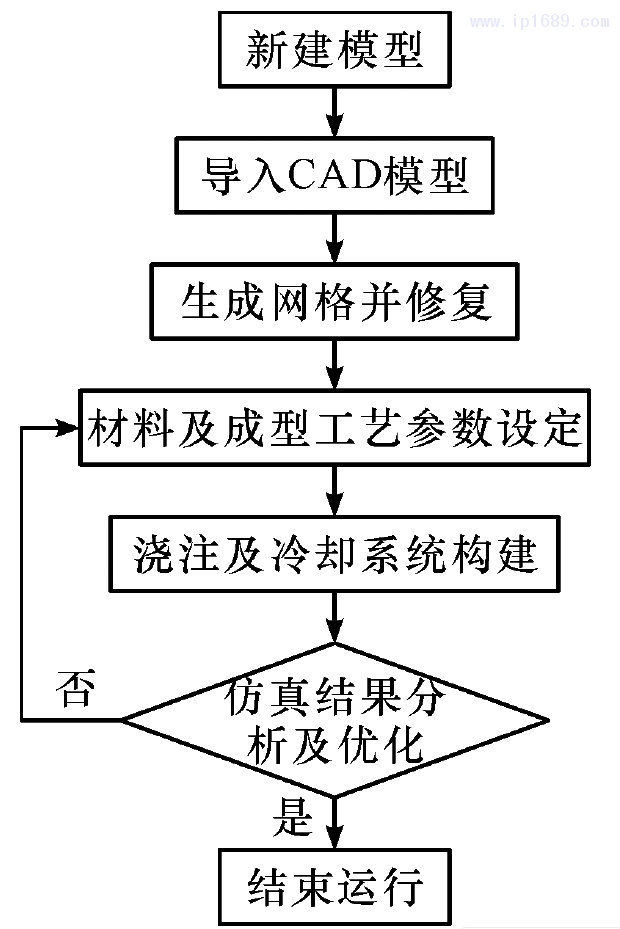
2) “未注先优”,在数值模拟仿真的基础上,对结果进行科学系统分析,设置合理优化方法,从产品结构,仿真模型和工艺参数等方面进行针对性的改进优化,从而获得最佳方案。
3) “未注先省”,通过 Moldflow 软件仿真和优化,可减少企业试修模次数,缩短研发和生产周期, 降低成本,获得优质产品。
2 注塑成型 CAE 技术在特殊产品中的应用
特殊产品与传统意义上产品相比,这类产品的形 状不规则、尺寸大、结构复杂、精度要求高和注塑成型加工难度大,生产周期长,注塑成型 CAE 方法对优化这类产品质量起着积极作用。
李晓芳等[3]以形状结构复杂、大型薄壁和精密三种塑料产品为研究对象,研究了在注塑成型过程中的技术难点。其中,形状复杂零件常具有壁厚不均、 孔种类和大小多样、凹槽和深腔等不规则结构。在数值模拟分析前处理过程中,对产品的三维模型进行网格划分需要大量的技巧和时间才能达到网格匹配率要求; 大型薄壁塑料产品造成其注塑时熔体流经路线长,易出现熔体充填不足及冷却固化时温度不均的问题; 强度比普通壁厚的产品稍差,长径比大,开模时易出现翘曲形变的缺陷; 精密产品尺寸误差要求较高,注塑成型过程要求更高。利用注塑成型 CAE 技术,确定最佳浇注和冷却系统,用此设计的每一步骤,都有相应的模拟结果,提前发现并优化充填不足、飞边、气穴、熔接痕、凹陷、翘曲变形等缺陷,达到 “未注先知”; 可以及时优化注塑过程,运用正 交试验法确定最佳成型工艺参数,达 到“未 注 先 优”; 降低注塑难度,简少大量的试模和修模过程,缩短生产周期,降低生产成本,为实际注塑生产提供有力的指导,达到 “未注先省”。
胡培成[4]以包装塑料产品、大型塑料产品和薄壁塑料产品为研究对象,研究了其生产工艺和关注的不同重点。包装塑料产品将知识工程与计算机辅助技术 ( AutoCAD、pro-E、SolidWorks、UG、Moldflow 和 Photo-shop) 相结合,可实现更高级和强大的包装设 计程序。大型塑料产品模具需考虑刚度、可靠性等问题,流道系统的平衡和冷却系统的设计要求高。薄壁塑料产品,熔体的收缩易造成翘曲变形。采用模具计算机辅助设计/计算机辅助工程/计算机辅助制造技术( CAD/CAE /CAM) ,能够优化模具结构,控制塑料产品的收缩率,提高产品合格率。
另外,注塑成型 CAE 技术在气辅注塑成型、快速热循环注塑成型和微孔发泡注塑成型等技术中得到广泛应用,并起到积极作用。
3 气体辅助注塑成型技术
气体辅助注塑成型技术是起源于 20 世纪 70 年代中期,80 年代中期开发成功,90 年代初实现工程化应用的新技术[5]。此工艺能极大程度地减少传统注塑成型和结构发泡成型所出现的产品缩痕、内应力和 翘曲等问题,是往复式螺杆发明之后,注塑领域第二 次创新型的发明[6]。
气体辅助注塑成型技术与传统注塑成型技术对比,在流动模型理论、工艺原理、设备和产品质量等方面都存在很大区别。
张响等[7]和王利霞等[8]研究了气辅注塑成型技 术的理论模型和数值模拟的理论,运用混合有限元/控制体积方法等,计算填充过程的压力场,预测填充过程气体充入、熔体前沿及外层聚合物的厚度因子和壁厚情况,并对模型进行可行性验证。研究了不同工艺参数 ( 如熔体温度、气体压力、延迟时间等) 对产品质量的影响,对生产实际具有指导意义。
气体辅助成型工艺过程包括熔体注塑、气体注塑、保压、排气和顶出产品五个阶段,与传统注塑成型相比多一个气体注塑阶段,成型系统单元需要专用的气辅设备,( 气体发生装置和气体辅助注塑成型控制系统) ; 模具依然采用恒温,对于流道截面突变等难成型区域,采用不同的调节温度; 通常采用单浇口,浇口与气体入口位置分开时,浇口应使最后填充点在气道终点附近[9]。
马玉录等[10]研究了气体辅助注塑成型工艺根据气体进口位置,分为喷嘴注塑气体法和模具注塑气体法; 根据产生气体压力的方法,分为不连续产生压力法和连续产生压力法,并叙述了其优点和区别。
气体辅助注塑成型工艺的局限性主要有排气孔问题、表面褪色和局部隆起问题。同时熔体最佳注塑量、模具和熔体温度、气体压力和延迟时间等成型工艺参数成倍增加对产品质量影响会更复杂[11-13]。
郑子军[14]阐述了基于神经网络的气体辅助注塑 工艺智能加工方法,提高了工艺参数的优化效率。
气体辅助注塑成型的 CAE 技术,可预测熔体、气体的流动成型情况,对新产品和模具结构研发,成型参数优化起到积极作用。
广泛应用在汽车配件、室内室外设施、卫星反射器、办公设施、日用品以及玩具等领域,具有节省材料、提高质量和降低成本等优点。
此外,液辅注塑成型技术,局部气体辅助注塑,振动气体辅助注塑等新的方法不断出现。同时,结合计算机辅助模拟和其他形式的注塑技术,对获得高质量产品和社会效益起到积极作用[15]。
4 快速热循环注塑成型技术
Bolstad 和 Lemelson 在 20 世纪 60 年代初,发明了一种模具快速加热和冷却的装置。Giboz 等[16]和 Yao 等[17]对材料在注塑成型过程中出现的气孔、流痕、熔痕和浮纤等质量问题,提出采用快速热循环注塑技术,即动态模温的方法来控制注塑成型,此方法得到广泛关注。
通用电气塑料日本有限公司、富士精工、三菱和韩国的三星公司于 2004 年开始,不断研发,生产了电子、家用电器和电视机外壳等产品。从 2006 年起,国内的山东大学与海信集团联合开发了快速热循环注塑系统,建成了模具、产品质量等成套技术与控制装备,并运用在多系列大尺寸液晶电视机面板的实际生产中。重庆大学、苏州大学和南昌大学等学校,TCL和海尔等电器公司也先后对变模温注塑技术进行了理论及应用研究。到 20 世纪 90 年代后此技术得到快速发展。
快速热循环注塑成型与常规注塑成型过程,主要差别点是,前者不同成型工艺阶段可以采用不同的模具温度,并且能直接进行整机产品生产并装配。减少了后续喷涂和抛光等工序,可获得表面高光并且无熔接痕的高质量产品,可成型超薄并带有微特征的产品,是一种节能、环保、应用前景广阔的先进注塑成型技术。
史展林等[18]系统分析了国内外学者关于模具快速加热、冷 却 方 法,随 形 管 道 加 热、冷 却 的 研究现状。边智等[19]总结了一系列模具型腔快速加热冷却技术,包括电阻加热、对流加热、辐射加热,模内水介质电加热和表面覆膜加热等; 模具冷却技术研究较少,有采用较低的冷却液温度,随形或热管冷却等,以此获得较高的冷却速率,缩短时间。这些技术为模具快速加热和冷却提供了多种选择; 模具结构加工技术包括,3D 技术打印任意复杂结构 “随形”管道模具,具有随形介质通道的车载高光蓝牙模具,具有分层结构蒸汽加热式模具,制造表面粗糙度 0. 025 μm 以下的高精度抛光 “部分冷间隙”模具新结构,与气体辅助注塑成型工艺相结合,提出板凳形式的螺柱新结构,解决带筋和柱结构塑料产品易出现的缩痕等缺陷。同时,很多学者利用注塑成型 CAE 技术,进行了模具充模成型技术、快速加热和冷却技术、产品成型质量和缺陷等研究。
此成型方法,仍存在许多问题亟待解决。比如:
1)模具温度控制技术不成熟,模具加热、冷却时间对型腔最髙和最低温度影响的研究较少
[20],缺少模 具实际试验方面的研究成果[21],影响了产品大批量工业化生产; 2) 复杂的模具型腔结构,对加热冷却管路的优化布局、动模与静模的精确对中、分型面的良好排气等均提出特殊要求; 3) 工艺参数研究不系统,不同高分子材料 ( 结晶和非结晶型) 对产品质量的影响规律也不尽相同,缺乏生产实践应用情况的研究[22]。
5 微孔发泡注塑成型技术
21 世纪的新型材料———微孔发泡塑料[23]由美国麻省理工学院的 Suh 等学者研制成功,随后由 Mar- tinim、Suh 等学者研究出微孔发泡成型技术,并在1984 年取得美国专利[24-25]。
此塑料定义为泡孔大小在 0. 1~100 μm 之间,密 度大于 109个/cm3 的发泡聚合物; 微孔发泡聚合物比未发泡聚合物具有冲击强度高、隔热隔音性能高、疲劳寿命长、热稳定性好、成本低、质量轻等优点; 在航空航天、汽车、日用品、生物医疗、电器和组织工程支架等行业领域有着良好的应用前景[26-28]。
近几年,我国对此技术的应用研究越来越重视。围绕着成型理论、优化工艺参数、改进设备、运用注塑成型 CAE 技术提高产品质量等进行研究。
陈建平[29]阐述了微孔发泡注塑成型技术原理, 分析了微泡成核、长大和冷却等工艺过程,用连续性、能量和动量三个方程描述充模过程,并建立数学模型,详细研究了求解微孔生长方程、温度场、压力场的方法和步骤,并用于泡孔大小和分布的预测。
王飞[30]研究了不同填充时间、注塑压力、气体 含量、初始泡孔半径及泡核含量、流动前沿温度等参数对产品质量的影响规律,并使用软件仿真寻找最优解,创新研发出电气控制的超临界气体注入系统,多头螺纹专用螺杆。
胡瑞生等[31]和王恒等[32]学者研究了近年来国内外注塑微发泡产品表面质量的研究概况。增加气体反压力抑制充模时泡孔成核,利用绝缘膜提高模具温度,共混聚合物改变性能等提高产品表面质量,并对以后发展方向进行了展望。
阮剑波等[33]总结了现阶段发泡注塑成型的优缺点,提出了一种二板式注塑机新技术。其具有独立的微开精度控制系统,可以精确控制产品壁厚,主要用于生产汽车零件,此项技术具有很好的发展潜力。
韩云等[34]利用 Moldflow 软件对填充、流动和冷 却等过程进行数值模拟分析。分析了注射速率、冷却时间、剪切应力、摩擦能等对气泡成核的影响,得到工艺参数优化方案,缩短生产周期。
李树松等[35]研究了通过改变模具温度对产品的泡孔结构、力学性能、减重比以及表面质量的影响,并利用软件仿真验证模具温度变化时,产品减重比和泡孔尺寸的变化规律。
此外,随着此技术的深入研究和广泛应用,出现新形式的注塑方法。例如,Xiao 等[36]把微孔发泡注塑技术和快速热循环成型技术结合,开发出一种电加热和水冷却快速热循环成型的模具; 王小新等[37]将气辅成型技术和快速热循环成型技术结合,分析了减少表面缩痕问题的方法等。
6 总结及展望
随着航空航天、汽车、电器等工业的快速发展,对塑料产品的品质要求也不断提高。对注塑成型技术的系统且深入研究,使得结构复杂,高质量产品能够加工出来,推动了计算机数值模拟仿真技术发展,同时,促进了新型注塑成型方法进一步研究、技术革新、融合、创新和应用。
参考文献
[1] 师中华,胥光申. 基于笔记本上边框的 Moldflow 分析与 应用 [J]. 西安工程大学学报,2014,28 ( 3) : 306- 310.
[2] 李德群. 现代塑料注射成型的原理、方法与应用 [M]. 上海: 上海交通大学出版社,2005: 118-119.
[3] 李晓芳,谢光前,李春光. 计算机模拟技术在注塑成型中的 应用研究 [J]. 塑料工业,2018,46 ( 11) : 72-75.
[4] 胡培成. 计算机辅助设计塑料产品的应用研究 [J]. 塑 料工业,2018,46 ( 6) : 65-68.
[5]耿铁,闫丽群,张艳云. 气辅注塑成型过程中气体穿透 长度的 MPI 三维数值模拟及实验研究 [J]. 科学技术与 工程,2013,13 ( 16) : 4727-4731.
[6] 余玲. 杂物盒的气体辅助注射成型模拟及工艺优化 [D]. 成都: 西华大学,2006.
[7]张响,董斌斌,王利霞,等. 基于数值模拟的气体辅助 注射成型工艺控制研究 [J]. 工程塑料应用,2004,32 ( 6) : 30-33.
[8] 王利霞,申长雨,李倩,等. 气体辅助注射成型工艺及 充模过程 CAE 分析 [J]. 高分子材料科学与工程, 2003,19 ( 3) : 160-167.
[9]张艳云,耿铁,任清海. 气体辅助注射成型技术研究综 述 [J]. 机械设计与制造,2011 ( 2) : 246-248.
[10] 马玉录,茅晓东,何曼君. 气辅注射模塑———一种新型 塑料成型工艺 [J]. 高分子材料科学与工程,1994 ( 6) : 120-125.
[11] RUSCH K C. Gas-assisted injection molding-a new technol- ogy is commercialized [J]. Soc Plast Eng,1989 ( 45) : 35-38.
[12] FALLON M. Why they are talking about gas injection molding [J]. Plast Technol,1989 ( 6) : 70-75.
[13] SHAH S,HLAVATY D. Gas injection molding of an auto- motive structural part [J]. Plast Eng,1991,199 ( 10) : 21-25.
[14] 郑子军. 气体辅助注塑成型工艺参数优化设定方法研究 [D]. 杭州: 浙江工业大学,2005.
[15] 张晓黎,吴崇峰,屈春起. 气辅注射成型技术进展 [J]. 中国塑料,2002,16 ( 8) : 16-20.
[16] GIBOZ J, COPPonNEX T, MELE P. Microinjection molding of thermoplastic polymers: A review [J]. J Micro- mechanics Microengineering,2007,17 ( 6) : 96-109.
[17] YAO D G,CHEN S C,KIM B H. Rapid thermal cycling of injection molds: An overview on technical approaches and applications [J]. Adv Polym Technol,2008,27 ( 4) : 233-255.
[18] 史展林,张磊,侯俊吉,等. 快速热循环注塑成型技术 发展综述 [J]. 精密成型工程,2017,9 ( 5) : 1-18.
[19] 边智,谢鹏程,安瑛. 注射成型快变模温技术研究进展 [J]. 现代塑料加工应用,2016,22 ( 5) : 48-51.
[20] 邓丽霞. 快速热循环注塑技术的研究现状与前景 [J]. 塑料工业,2013,41 ( 6) : 10-13.
[21] 王小新. 快速热循环高光注塑模具加热冷却方法与产品 质量控制技术研究 [D]. 济南: 山东大学,2014. [22] 全东. 快速热循环注塑工艺实验及模拟研究 [D]. 济 南: 山东大学,2012.
[23] LEE Y H,PARK C B,WANG K H,et al. HDPE-clay nanocomposite foams blown with supercritical CO2 [J]. J Cell Plast,2005,41 ( 5) : 487-502.
[24] MARTINI J E. The production and analysis of microcellular foam [J]. Massachusetts Inst Technol,1982,28 ( 1) : 674-676.
[25] MARTINI-VVEDENSKY J E,SUH N P,WALDMAN F A. Microcellular closed cell foams and their method of manufac- ture: US4473665 [P]. 1984-09-25.
[26] YANG Q,ZHANG G,MA Z,et al. Effects of processing parameters and thermal history on microcellular foaming be- haviors Peek of using supercritical CO2 [J]. J Appl Polym Sci,2015,132 ( 39) : 42576.
[27] 李帅,赵国群,管延锦,等. 模具型腔气体压力对微发 泡注塑件表面质量的影响 [J]. 机械工程学报,2015, 51 ( 10) : 79-85.
[28] MI H Y,JING X,SALICK M R,et aL. Fabrication of themoplastic polyurethane tissue engineering scaffold by com- bining microcellular injection molding and particle leaching [J]. J Mater Res,2014,29 ( 8) : 911-922.
[29] 陈建平. 微孔塑料注射成型数值模拟 [D]. 郑州: 郑州 大学,2007.
[30] 王飞. 微孔发泡注塑成型工艺与关键设备的研究 [D]. 苏州: 苏州大学,2012.
[31] 胡瑞生,王毅,张翔,等. 注塑微发泡制品表面质量和发泡形貌的研究进展 [J]. 工程塑料应用,2016,44 ( 3) : 135-140.
[32] 王恒,张翔,曾祥补,等. 微孔注塑发泡制品表面质量的研究进展 [J]. 塑料工业,2017,45 ( 10) : 30-34.
[33] 阮剑波,俞诤,郑海伟,等. 二板式注塑机微开技术在 发泡注射成型中的应用 [J]. 塑料,2017,46 ( 3) : 89 -91.
[34] 韩云,林有希. 微孔注塑成型过程的 Moldflow 模拟仿真J]. 合成树脂及塑料,2017,34 ( 1) : 60-65.
[35] 李树松,闫宝瑞,安华亮. 基于 Moldex3D 分析模具温度对 PP 发泡注塑制品的影响 [J]. 中国塑料,2019, 33 ( 1) : 53-58.
[36] XIAO C L,HUANG H X,YANG X. Development and ap- plication of rapid thermal cycling molding with electric heating for improving surface quality of microcellular injection molded parts [J]. Appl Therm Eng,2016,100 ( 5) : 478-489.
[37] 王小新,张明磊,鲁韶磊,等. 外部气辅成型技术在高 光注射成型工艺中的应用研究 [J]. 模具工业,2014, 40 ( 5) : 40-43.