单螺杆挤出机主要用于挤出软、硬聚氯乙烯、聚乙烯等热塑性塑料,可加工多种塑料制品,如吹膜、挤管、压板、拔丝带等,亦可用于熔融造粒。双螺杆挤出机用于型材挤出的双螺杆具有相互啮合的螺棱、螺槽,并在较低的转速下操作,约为10/min以内。与单螺杆相比,双螺杆挤出机的进料和输送性能优越得多,尤其是那些难于喂入和容易打滑的,如纤维状、粉状和油脂类物料。物料滞留时间短且比较均一,较好的混合和较大的传热面积,使料温控制良好,这对热敏性材料的加工尤为重要。
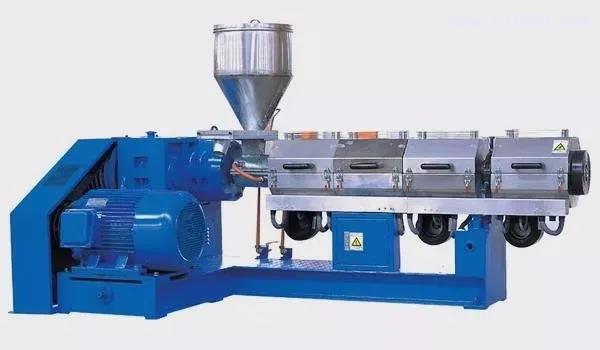
挤出机产能受限的因素
企业在日常生产过程中,一台挤出机产能受限的因素有很多,其中包括扭距、自由容积、排气、温度、建压、停留时间、热交换等等。这些因素最终都是和产品质量挂钩的。
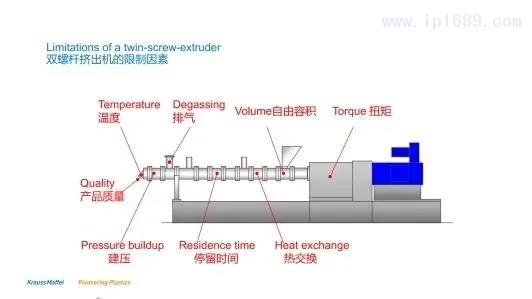
在这些影响的因素中,自由容积和扭距通常是最为直接也是大家最为关注的两个因素,但是这两个因素通常是在一台设备的设计和出厂的时候就已经决定了,一般如果不通过大型的整改或更换设备无法对这两个因素进行更改。
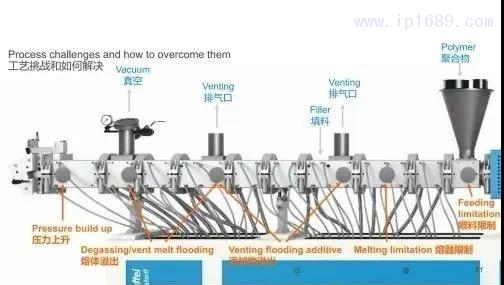
自由容积如何改进
在不改变设备的前提下,首先当我们如果遇到喂料限制的时候,我们可以通过更换螺纹元件的设计,使用一些深槽的螺纹元件。来得到更大的一个自由容积来提升整个挤出机的输送能力来解决这个喂料限制的难题。
其次在熔融塑化这一块,在改性的过程中,我们通常会在聚合物中加入一些有机或者无机的一些物质来达到改变聚合物物理或者化学性质的目的。在这个过程中,我们通常需要将两种或者多种不同的物质充分混合在一块,而且由于各种物质的表面应力或者它的界面应力不一样,所以我们需要首先保证聚合物处在一个百分之百熔融状态,这样可以对这些添加物进行更好的一个浸润、包覆的作用,例如像我们添加滑石、玻纤之类添加物。
如何获得比较好的熔融效果
决定因素或者说相关因素也是比较多的,其中包括螺杆的设计、螺杆的转速、物料的填充度、机筒的温度和扭距密度等等。首先,不同的聚合物对塑化能量的需求是不一样的,针对不同的聚合物,我们要相应的对螺杆进行设计。其次,在机筒温度方面,通常塑化段的机筒加工温度应该比聚合物熔点高30℃或者更高一些。再者,我们可以通过调整螺杆转速来调节物料在螺槽中的填充度,当几个方法同时相互作用的时候,我们可以得到一个比较好的熔融效果,甚至百分之百的熔融效果,对最终产品的均匀度和质量都有一个好的保证。
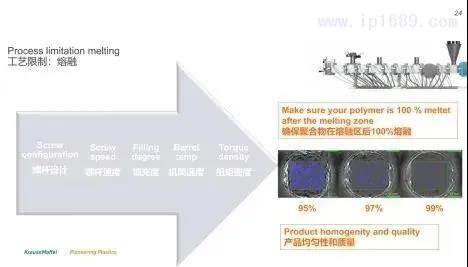
填料溢出的解决方法
当我们遇到这种到溢出的现象一般主要是两个原因,一种是树脂或者是聚合物对这个添加物的浸润不够充分。第二种是由于螺槽中的自由容积不够导致填料的溢出。针对这种现象,首先我们可以通过调整螺杆设计来增强或者加大树脂对填料的浸润包覆。其次,通过螺杆设计协同螺杆速度的一个改变,我们可以改变物料在螺槽中的一个填充度,来解决这个填料溢出的问题,那在这个方面螺杆设计将会是一个成功的一个关键因素。
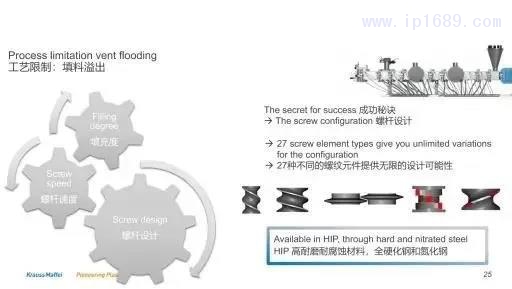
在这个生产过程中,我们经常也会遇到熔体从排气口或者真空口溢出的一个现象,针对不同的熔体解决办法是怎样的呢?
比如PET类是一个低粘度、附壁的熔体,我们通常选用一个大开口敞开式的排气插件来使用。比如PP类是一个中高黏度、附壁熔体,我们采用这种半开口式的一个排气插件,而对于像一些HDPE之类的这个高粘度的但不附壁的熔体,我们会采用这种小开口几乎全覆盖的一个排气插件来使用。那其实很多人想问,我为什么要用这么多的排气插件,我全部用C型这种小开口的就好了,我不需要去准备这么多的类型的插件。其实不然,特别是针对气味和VOCs这块!当我们如果全部使用这种小开口的这种排气插件,他对脱挥的效果会大大打折扣。所以综合考虑到脱挥的效果等等,我们还是要选择相对应的合适的一个排气插件。
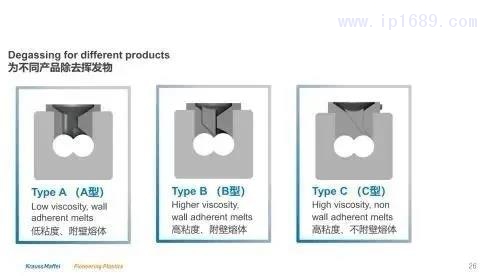
随着大众或者大家对健康越来越高的要求,大家对塑料部件的气味和VOCs的要求也是日益的提高,特别是在汽车行业,我相信大家都碰到过气味和VOCs的困扰。在这张图上大家可以看到左边是一个比较传统或者一个标准的真空装置,在右边我们可以看到这明显是一个加大的真空装置,我们可以通过增加它的一个脱挥面积来提高脱挥效果来以达到低VOCs或者低气味的产品。
最后在这个实际生产过程中,大家也经常会碰到由于机头压力的不稳定造成这个料条的波动,甚至料条断裂使整个生产的过程非常的不平顺。影响机头压力波动的因素熔体黏度、熔体的温度包括建压段所使用的螺纹元件的螺距都是有关系。我们可以通过调整机器的转数和机筒的加工温度来实现对熔体温度和粘度的调整,同时在辅配上不同螺距的螺纹元件的使用来调整他整个的压缩比,可以达到让机头压力稳定的一个作用,使得整个出条或者料条的出料比较稳定。
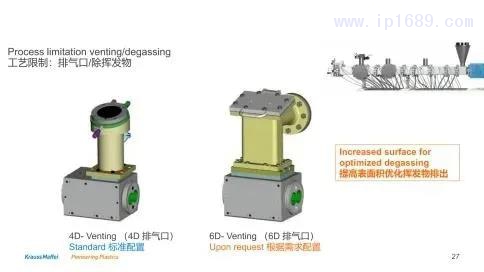