罗江红,张艳彬
(新疆交通职业技术学院机电工程学院,新疆乌鲁木齐831401)
摘要:在某汽车车门内板拉延成形工序中引入了刺破工艺。基于数值模拟结果,采用响应面法对刺破刀具结构参数进行了优化,获得了最优刀具结构参数为:刺破刀轮廓长度100mm,宽度95mm,圆角半径65mm,刺破刀距离车窗区域A左侧壁和上侧壁的距离分别为45、50mm。研究了刺破工艺对板料局部应力的影响和零件拉延成形性的影响。结果表明:刺破工艺可以显著降低板料易拉裂位置的局部应力,还可以为零件刺破位置附近的易拉裂区域提供额外的板料流入量,从而降低其减薄率和拉裂风险。依据带刺破工艺的拉延成形方案制造了该车门内板拉延模具并进行了零件试生产,发现试验结果与模拟结果一致,得到了表面质量好、无拉裂缺陷的汽车车门内板零件。
关键词:车门内板;刺破工艺;结构优化;局部应力释放;成形性;
目前冲压成形技术已被广泛应用于汽车覆盖件生产,在冲压成形过程中,影响汽车覆盖件质量的主要缺陷有起皱、折叠、缩颈、破裂等[1-2]。对于该类问题,可基于数值模拟结果,使用三维造型软件对模具型面如凸凹、模圆角大小、拉延筋深度、宽度等进行修改和调整[3-4],或基于正交试验、响应面法、BP网络神经算法、多目标粒子群算法等对成形工艺参数如虚拟拉延筋系数、压边力大小、润滑系数等进行优化[5-6],从而解决起皱、拉裂等缺陷。然而,某些如四门两盖、地板等汽车的车身零件通常具有尺寸大、料薄、型面结构复杂等特点,在零件中间区、复杂型面区以及高筋侧壁等位置,板料流入量有限,易出现板料局部应力集中、板料减薄率高、局部拉裂等情况[7-8]。在零件型面相对确定的情况下,仅通过修改模具型面或优化工艺参数等方法,难以完全解决该问题。因此,本文以某汽车车门内板为研究对象,设计并建立了该零件的有限元模型,通过在拉延成形工序中增加刺破工艺[9],并采用中心复合试验和响应面法对刺破工艺刀具结构参数进行了优化,研究了刺破工艺对该车门内板易开裂位置的局部应力和拉延成形性的影响;最后通过数值模拟和生产试制,验证了该局部应力释放的方法可以有效解决车门内板高筋侧壁处出现的拉裂缺陷。
1工艺分析及有限元模型
1.1 车门内板工艺分析
本文研究对象为某汽车车门内板,其三维模型如图1所示。该零件尺寸为1330mm×900mm,属于大型汽车车身覆盖件;区域A属大平面切边区域,在拉延成形工序中,该区域的成形性可不做考虑;车窗区域A上下边界处存在高筋区,区域A上下侧壁高度约为25mm,可能存在拉裂风险;区域B属车门内板功能结构区,空间结构复杂,型面变化较多,导致该区域板料流动困难,成形过程易出现板料过度减薄、拉裂等缺陷。此外,区域A与B之间存在一条长且细的高筋区,由于该高筋区位于零件中心部位,左侧为型面复杂的区域B,且顶部端面与右侧区域A的高度差约为35mm,故在成形该高筋区的过程中,板料流动阻力大,板料流入量非常有限,在不断的拉延过程中,区域A上下和左侧侧壁以及圆角部位发生开裂的风险较高。因此,解决该零件区域A上下和左侧侧壁以及圆角区域的开裂问题是该车门内板拉延工序的关键。
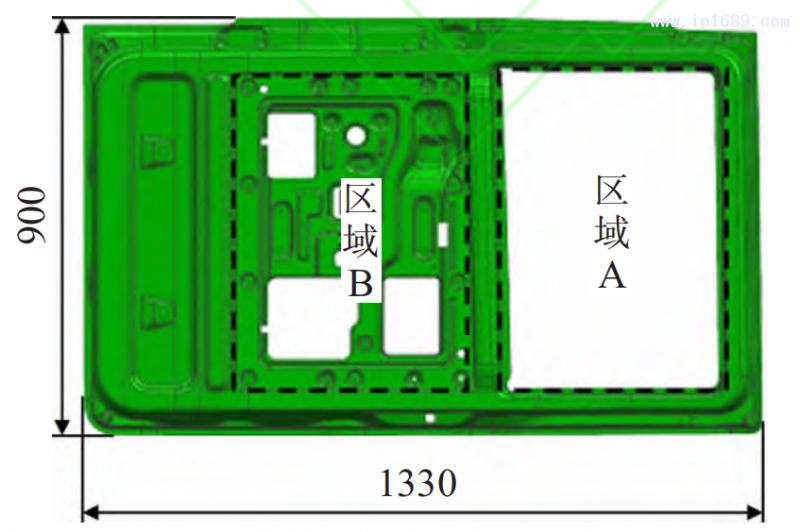
1.2 拉延成形方案设计
使用三维造型软件和Autoform设计并建立拉延成形方案1,即在拉延成形过程中使用常见的“上模-压边圈-下模”拉延成形方案,其有限元模型如图2所示。零件材料为超深冲用DC-06钢,板料尺寸为1600mm×1100mm,料厚0.7mm;根据实际生产经验,采用油润滑,选择摩擦系数为0.15,冲压速度50mm/s;使用中心复合试验和响应面法,获得最优压边力为427kN,取整为430kN。图3为方案1的车门内板零件减薄率云图和成形性云图。模拟结果显示,在区域A上侧和左侧侧壁出现严重的过度减薄现象,拉裂风险较高,且在上述区域位置零件的减薄率均超过25%。该位置出现拉裂缺陷的原因是因为该车门内板尺寸大、型面复杂,加之区域A上侧的侧壁垂直高度达25mm,左侧侧壁垂直高度达35mm,导致该处板料流动困难,板料在拉延过程中减薄严重,故而出现拉裂的缺陷。即使在对工艺参数进行优化后,零件区域A上下侧壁和左侧侧壁依然存在较高的拉裂风险。
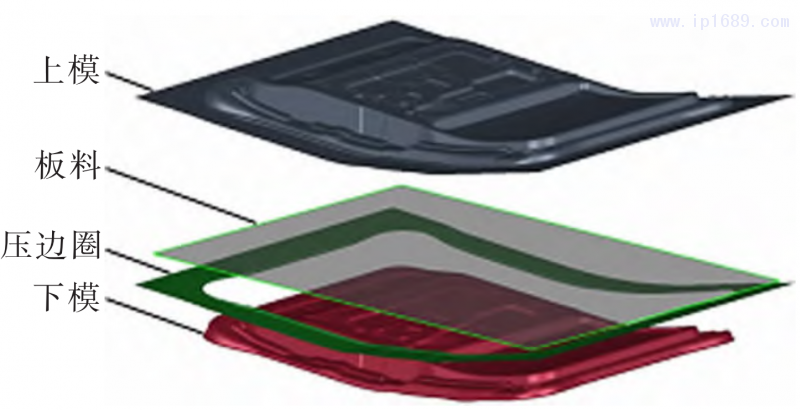
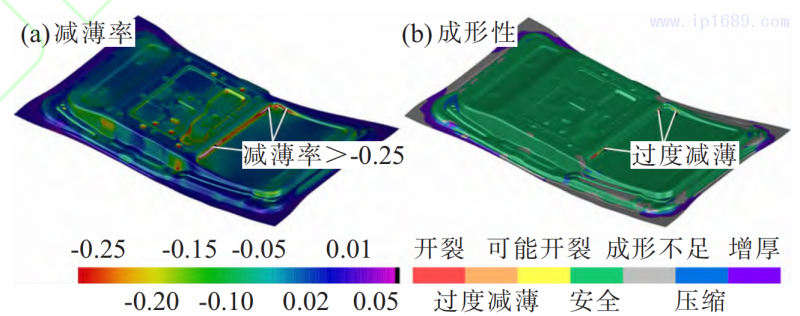
为了解决该车门内板拉裂缺陷,在方案1的基础上设计了方案2,即增加了刺破工艺:在下模增加一组刺破刀,由于零件区域A在后续工序中会被切除,故在该位置增加刺破刀不会影响零件最终的成形质量。图4为刺破工艺示意图。
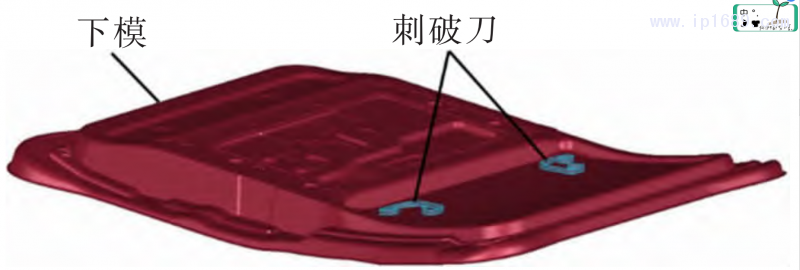
1.3 试验设计及方法
本文针对方案2的刺破工艺,研究了刺破工艺刀具位置和形状对车门内板拉延成形性的影响。以刺破刀轮廓长度H1、宽度H2和圆角R以及刺破刀距离车窗区域A左侧壁的距离X1、上侧壁距离X2作为优化因素,如图5所示。并在试验初期基于单因素变化的数值模拟试验结果确定了如表1所示的优化因素取值水平。
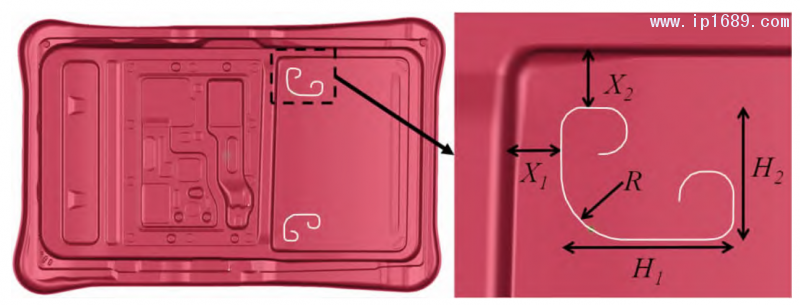
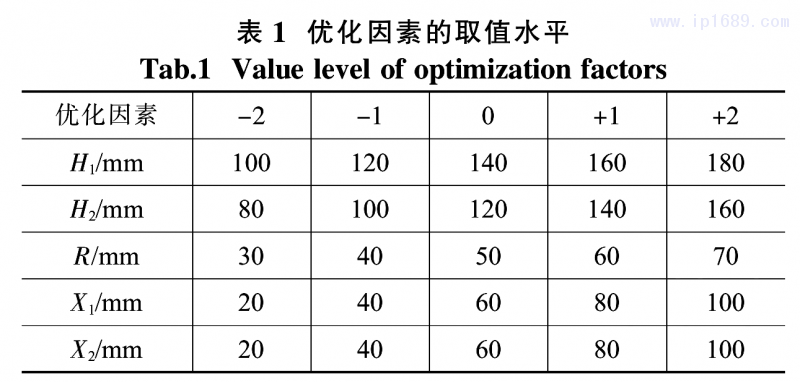
为了消除车门窗区域A上下和左侧侧壁存在的拉裂缺陷,以零件成形结束瞬时状态下的最大减函数Y1(式(1))和区域A上下和左侧侧壁以及圆角区域内的局部最大等效应力Y2(式(2))作为评价零件开裂的目标函数。
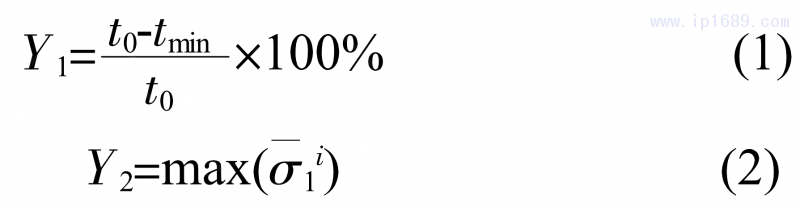
式中:t0为板料初始厚度;tmin为拉延成形结束后板料的最小厚度;σ1为板料单元格节点的等效应力。
确定评价函数后,利用Design-Expert软件以刺破刀的长度H1、宽度H2和刺破刀圆角R以及刺破刀距离车窗区域A左侧壁距离X1、上侧壁距离X2作为变量因素,以零件最大减薄函数Y1和区域A上下侧壁及圆角区域的最大等效应力Y2为响应函数,设计中心复合试验并通过数值模拟的方法获得试验结果,如表2所示。
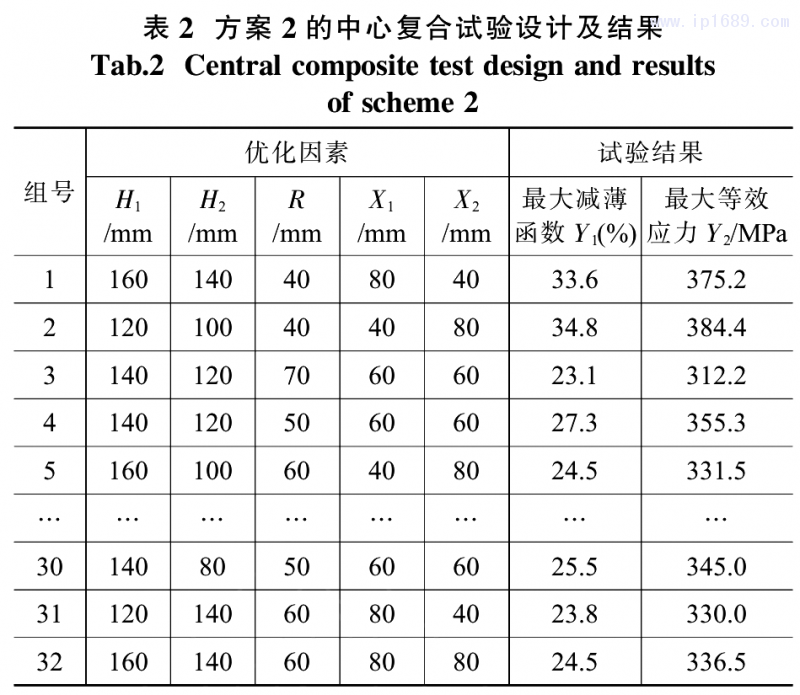
根据表2试验结果与5个优化因素之间的关系,建立二阶多项式,得到试验因素与评价函数之间的关系为:

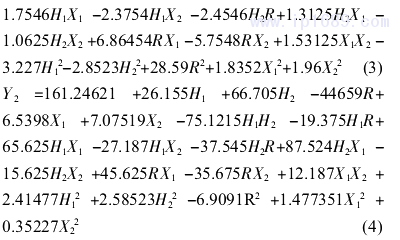
为了检验所建模型的可靠性,对其进行方差分析,分析结果如表3所示。从表中可以看出,两个评价函数最大减薄函数Y1和最大等效应力Y2的响应模型“P>F”概率均小于0.0001,结果显著;此外,两个响应模型的决定系数和修正系数均大于0.8,二者差值小于0.15;综上结果可以判断,所建立的响应模型具有较高的可靠性, 能够较好的反映优化因素与评价函数之间的关系,预测精度较高。
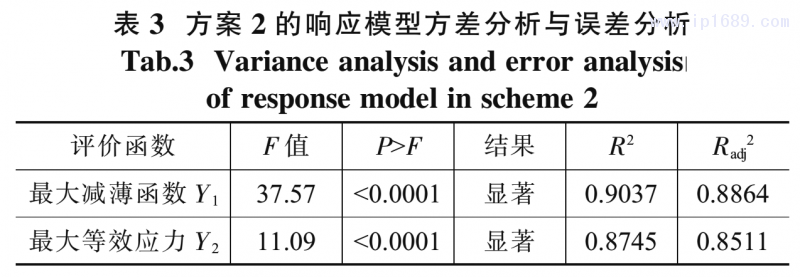
2试验结果与分析
2.1 多目标优化与验证
基于已建立的最大减薄函数Y1与最大等效应力Y2响应模型,对刺破工艺刀具结构参数进行优化。为避免零件车窗区域A上下侧壁和左侧侧壁以及圆角区域出现开裂,要求最大减薄率小于25%,即Y1<25%;同时要求最大等效应力Y2取得最小值。基于上述优化目标,对相应函数进行求解,获得刺破工艺刀具结构最优参数(取整)为:H1=100mm,H2=95mm,R=65mm,X1=45mm,X2=50mm,此时预测最大减薄函Y1=21.4%,最大等效应力Y2=295.5MPa。
利用Autoform软件,以优化后的刺破工艺刀具结构参数进行数值模拟,对多目标优化结果进行验证。图6为优化后该车门零件减薄率云图和等效应力分布云图。从图可以看出,零件最大减薄率为23.1%,小于25%,与响应模型预测值的相对误差为7.94%,零件开裂风险低;最大主等效应力为308.4MPa,与响应模型预测值的相对误差4.37%,零件危险位置卸载前的等效应力得到了有效降低。图7为刺破工艺刀具结构优化后,该车门内板零件的成形性图。从图中可以看到,零件区域A上下侧壁和左侧侧壁以及圆角处的成形性为安全,零件其它有效型面区域的成形性同样为安全,不存在开裂风险。由此可推断,其一,通过在车门内板车窗区域A内加入刺破工艺,并对刺破工艺刀具结构参数进行优化,可以有效解决区域A上下侧壁和左侧侧壁以及圆角处的开裂问题;其二,由数值模拟结果验证了基于中心复合试验和多目标优化方法的可靠性和有效性。
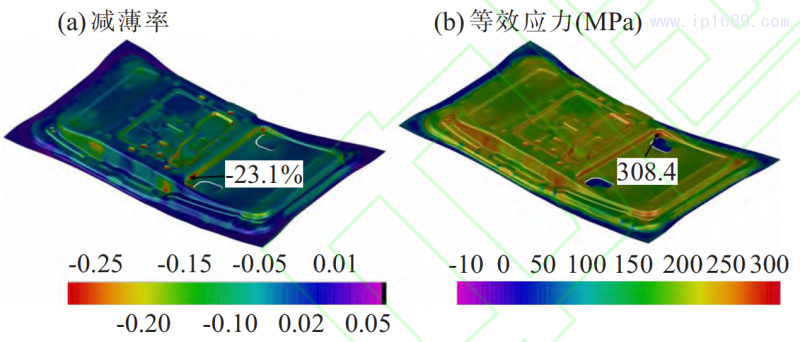
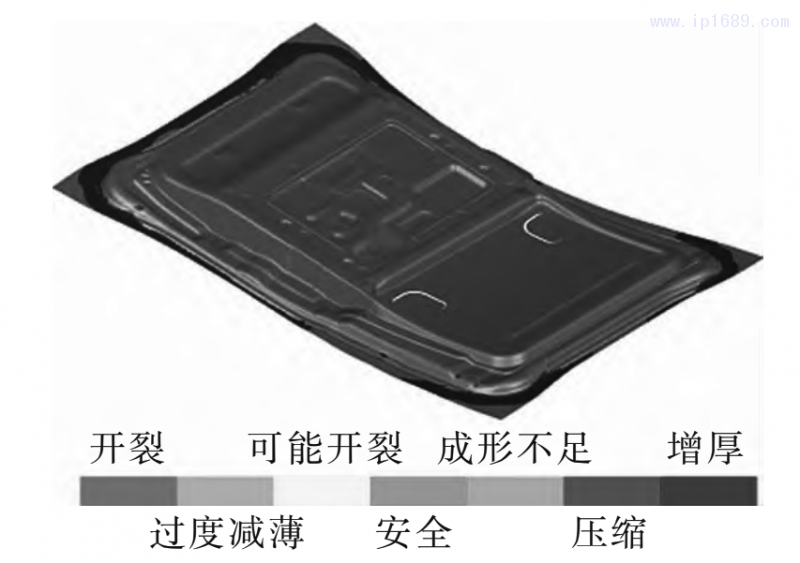
2.2 刺破工艺对零件局部应力的影响
为了验证刺破工艺对零件易拉裂位置的局部应力的影响,在零件易开裂区域取点1~10号(图 8),其中1~4、7~10为等距点,4~7为等距点,且距离为其它距离的2倍。对比取点位置在无刺破工艺条 件下零件成形结束瞬时的等效应力和有刺破工艺条件下零件成形结束瞬时的等效应力以及有刺破工艺条件下零件卸载后的等效应力,结果如图 9 所示。由图可知,增加了刺破后,在零件拉延成形结束瞬时,零件1~10号危险位置的等效应力由无刺破时的325.1~414.8 MPa下降至有刺破时的265.4~308.4MPa,1~10位置的局部等效应力降低了5.1%~28.1%。其中,2号位置和9号位置的等效应力降低最少,这是因为板料刺破后,2号和9号位置正好处于刺破区的圆角部位,板料需要上侧侧壁和左侧侧壁流动,使得该处减薄率较高,同时该圆角又处于板料应力释放的一个盲区,故板料成形结束瞬时的等效应力较其它位置偏高。另外,零件1、3、8、10号位置,板料的等效应力降低最大。这是因为该处位于零件刺破中央位置,故应力释放效果最明显。 卸载后,零件1~10号危险位置的等效应力由拉延成形结束瞬时的265.4~308.4MPa降低到了卸载后的 13.2~72.8MPa,其中1、4、8、10位置残余应力较高,这是因为该处处于零件刺破中央位置,刺破后,该位置的应力的得到释放,减薄率降低,但也导致该位置板料塑性变形量减少或塑性变形不充分,故卸载后残余应力较大。但综合零件拉裂位置的等效应力变化结果可以清楚地看到,刺破工艺可有效降低板料易开裂位置的等效应力。
表4为在刺破条件下零件拉延成形结束瞬时,零件刺破边缘a~j号位置(图10)的板料流入量。从表中可以看到,方案2带刺破工艺的板料成形结束瞬时,零件区域A上侧壁板料流入量增量较小,平均为1.43mm;左侧壁的板料流入量增量较大,平均为5.9mm。这是因为零件局部刺破后,刺破位置板料由原来的受拉状态转变为可有限流动的状态,使得刺破边缘的板料可向区域A上侧和左侧侧壁流动,为其提供额外的板料流入量。
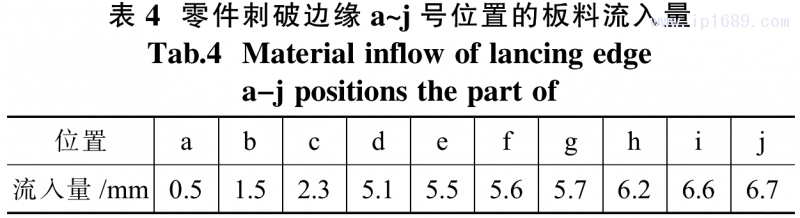
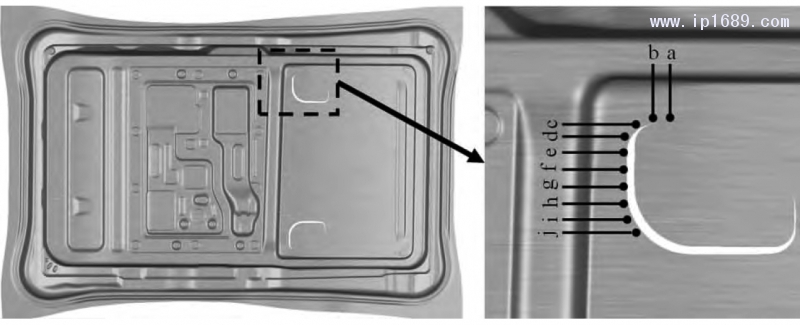
综合上述试验结果可以看到,在该车门内板拉延成形过程中,通过引入刺破工艺并对刀具结构参数进行优化,将区域A内的板料刺破,一方面使得零件危险区域板料所受应力得到释放,卸载后零件最大等效应力小于75MPa;另一方面使得模具对刺破位置板料的约束力减小,为区域A上侧和左侧侧壁提供了额外的板料流入量,有效降低了该位置的板料减薄率和拉裂风险。
3生产验证
根据方案2设计,在该车门内板拉延成形模具下模安装了刺破刀,如图11所示。并进行了试模生产,得到的试模零件如图12所示。从图12可以看到,刺破刀对应位置的零件已被刺破,零件区域A上侧和左侧侧壁处无拉裂缺陷。该试模结果证明,通过刺破工艺,可以释放零件易拉裂位置的局部应力,同时还可以为零件易拉裂处提供额外的板料流入量,从而降低零件局部位置的减薄率并消除零件的拉裂缺陷。

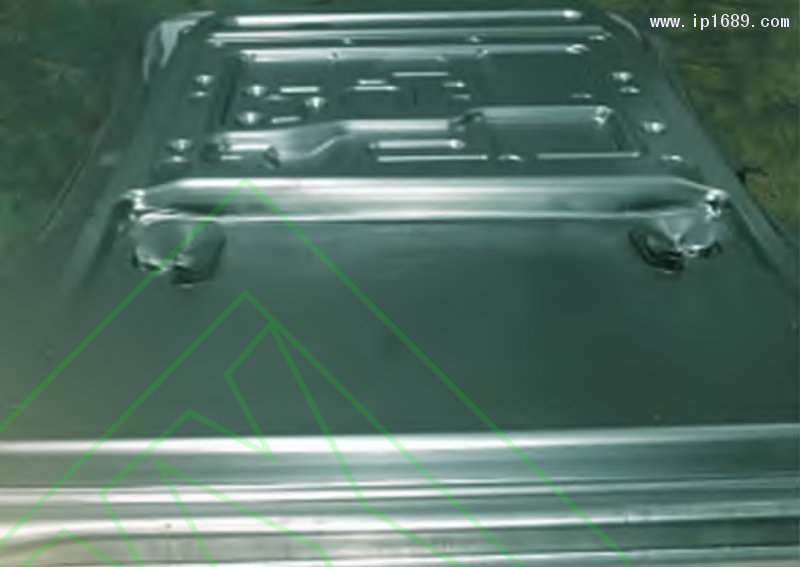
4结论
(1)针对某汽车车门内板拉延成形时易出现拉裂缺陷的问题,设计了带刺破工艺的拉延成形方案,通过响应面法和数值模拟结合的方法,获得最优刺破工艺刀具结构参数H1=100mm,H2=95mm,R=65mm,X1=45mm,X2=50mm,并成功消除了零件的拉裂缺陷,证明了评价函数的有效性和响应模型的可靠性以及该优化方法的可行性。
(2)通过数值模拟分析了某车门内板拉延成形过程中成形板料易拉裂位置的局部应力变化,结果表明:刺破工艺不仅可有效降低成形板料易拉裂位置的应力,同时还可以提高刺破位置板料的流动性,为刺破位置附近易拉裂处提供额外的板料流入量,从而降低成形零件的减薄率和拉裂风险。
参考文献:
[1] 安治国,刘志禄,韦光珍.基于数值模拟技术的轿车零件成形工艺优化设计[J].热加工工艺,2008,37(23):58-60.
[2] 周均,王勇.基于Autoform软件的冲压成形工艺参数优化[J].兵器材料科学与工程,2017,40(1):79-82.
[3] 张玉平. 某车型左/右车门内板的成形分析及有限元模拟[J].兵器材料科学与工程,2013,36(3):96-98.
[4] 汤淑芳,覃柏英,林贤坤等.发动机隔热罩冲压成形的仿真与优化[J].热加工工艺,2016,45(1):121-124.
[5] 李萍,薛克敏,杨文江.瑞风商务车托架拉延成形数值模拟及工艺参数优化[J].机械工程学报,2008,44(7):176-180.
[6] 余世浩,赵锐敏,李佳琪等.基于多目标粒子群算法的冲压成形工艺优化[J].热加工工艺,2014,43(1):144-147.
[7] 刘晓晶,陈晓桐,张晓华等.铝合金车门内板成形工艺数模拟及模具设计 [J].哈尔滨理工大学学报,2018,23(4):118-121.
[8] 李骁,郑松林,张振华等.汽车门内板冲压成形起皱研究[J].热加工工艺,2014,43(7):154-158.
[9] 刘驰. 防止座盆拉延件开裂的工艺改进 [J].锻压技术,2014,39(3):20-24.