刘 光1*,文 桦2,徐启杰3
1.驻马店职业技术学院机电工程系,驻马店 463000;2.黄淮学院信息工程学院,驻马店 463000;3.黄淮学院 化学工程学院,驻马店 463000
摘要:针对传统的ABS塑料电镀生产线自动化程度偏低、适用性差、生产成本较高和维护管理难度大等问题,设计开发了以S7-1200PLC和博途TIA Portal为核心的ABS塑料电镀生产全自动控制系统。利用S7-1200PLC设计主、从站控制系统,通过主站监控和管理电镀生产过程,以及从站输出控制电镀设备。在博途TIA Portal平台上设计上位机操作面板和PLC控制程序,既满足不同形状规格、牌号和用途的ABS塑料制件的电镀生产需求,又为工艺人员提供易于操作、维护和管理的应用功能。实际调试表明,所设计的系统能按照电镀工艺设定输出控制信号、反馈生产数据,实现了对电镀生产流程和工艺条件的高效监控。
关键词:ABS塑料;电镀;PLC;TIA Portal;控制系统
ABS塑料易于加工成型,其制品具有质量轻、强度高、表面光洁、抗蠕变能力强等诸多优点,经适当的电镀处理能大幅改善ABS塑料制品的硬度和耐磨性,特别适用于汽车、仪器仪表、电子电器等领域配件的装饰性与功能性需求。由于电镀工业化特征显著,以人工操作为主的传统电镀生产线自动化程度较低,电镀产品的质量容易受到工艺人员技术水平等因素影响。针对特定的工艺条件和生产流程,部分生产线利用成本低、操作简单和运行可靠的PLC系统对电镀生产过程进行自动化升级改造,通过PLC和触摸屏精确控制镀液配方与工艺参数,从而提高产品质量和经济效益[1-4]。然而,对于ABS塑料电镀生产,自动控制系统的实现及其应用性能不仅与电镀工艺条件和生产流程有关,还受电镀设备、辅助机电设施和现场环境等因素影响[5-6]。若电镀生产线按非标设备定制,成套系统交付周期长、投入成本高,真正投入电镀生产前还需要经过长时间反复论证和调试,企业承担很大的资金回收风险,因此需要设计通用性、模块化、可移植扩展能力强的电镀生产线自动控制系统。
在工业控制领域,相对于传统的PLC系统,博途TIA Portal和S7-1200PLC集成了通用的编程语言和网络通讯接口,模块化S7-1200PLC和分布式I/O配置几乎满足所有自动化控制系统要求,具有成本低、配置灵活可靠、维护简单、安装和扩展方便等优点。因此,在S7-1200PLC硬件和博途TIA Portal软件基础上,联合开发满足不同ABS塑料制件电镀生产需求的全自动化控制系统。建立S7-1200PLC主、从站系统,由主站监控管理电镀生产过程,从站输出控制电镀设备。设计易于操作、监控、维护和高效管理的上位机操作面板与S7-1200PLC自动化控制软件,方便工艺人员根据ABS塑料制件电镀需求在线设置工艺参数,并实现对电镀生产过程和工艺条件的全程自动化监控和管理。
1 ABS塑料电镀生产线总体构成
不同形状规格、牌号和用途的ABS塑料制件所需的电镀工艺不同,对应的工艺条件和生产流程差异也较大。通常,ABS塑料电镀工艺包括塑料表面金属化前处理和电镀两部分,先对塑料基体进行表面除油、粗化等处理,再利用胶体钯活化使基体表面均匀吸附钯液,通过解胶去除表层钯液吸附的锡(II)离子,然后以钯核为活化中心,进行化学镀镍,最后再根据塑料制件的使用要求进行装饰性或功能性电镀。ABS 塑料电镀生产线包括超声波清洗机、工位槽、行车、电控、管道、通风等设备,如图1所示。根据ABS塑料电镀的自动控制要求,工位槽按生产流程进行双排布置,工艺分为 S1~S20、Y1(清洗)等模块控制位,各工位槽间塑料制件输送和停靠时间控制由行车S20负责,工位槽自动加液、槽内工件位置检测、温度、pH和电流密度等调节则由对应的控制位S1~S19实现。
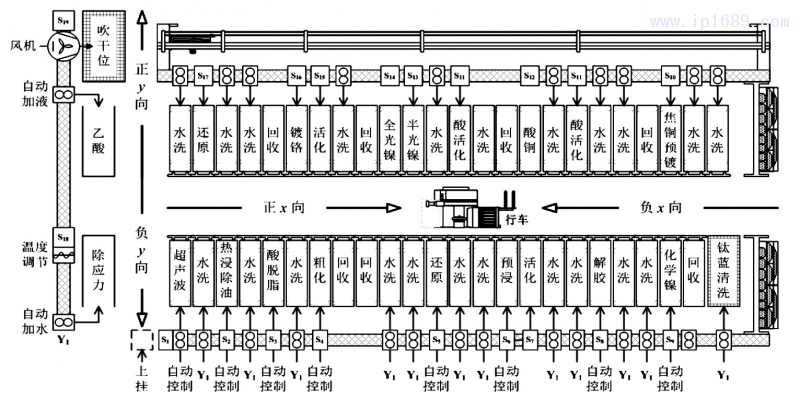
图1 ABS塑料电镀生产线总体构成
行车S20采用模块化结构设计,主要用于塑料制件的横移行走(x 和 y 向,M3电机)、升降(z 向,M2电机)和回转(M1电机)控制,如图2所示。行车吊钩具有防脱落触突结构,避免挂具在生产过程中脱落;吊钩能随横梁在M1电机作用下回转,以适应双排工位槽的电镀生产要求;吊钩下方配备接水盘,避免塑料制件带出的电镀液对车间地面腐蚀和污染;各工位槽电镀停靠时间由M2电机控制吊钩升降实现。行车S20起始位为上挂具点(图1),先沿y向横移完成残余应力消除,然后按正x向横移实现塑料表面金属化前处理,再通过横梁回转,沿负x向横移实现光亮镍、镀铬等电镀加工,最后经清洗、吹干后完成对塑料制件的自动化电镀控制。
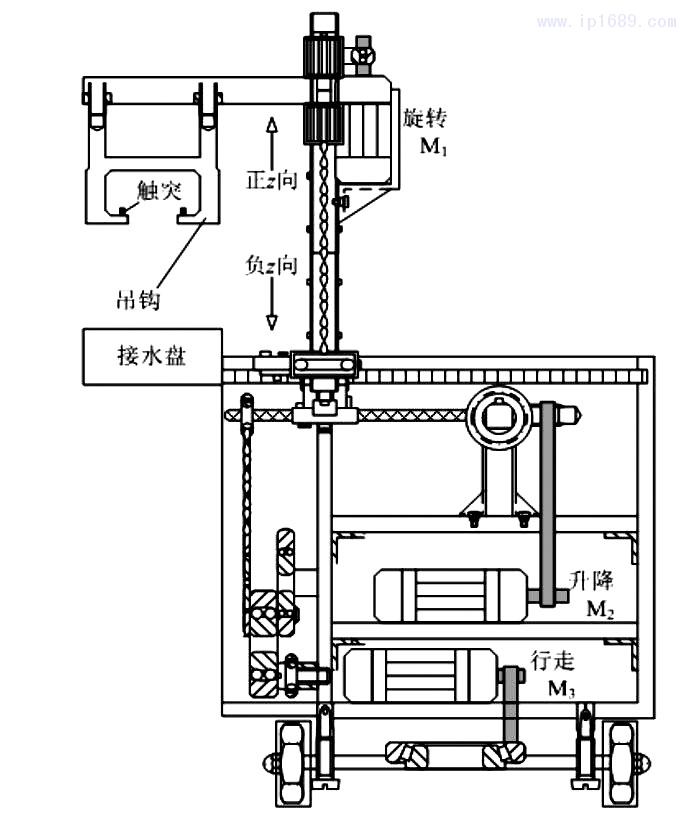
图2 电镀行车基本结构
2 硬件设计
2.1 PLC系统设计
控制位S1~S20、Y1分别对应于ABS塑料电镀生产线不同的工艺环节:首先根据I/O数量以及工位槽对加液、槽内工件位置检测、温度、pH和阴极电流密度等不同控制要求,将S1~S20、Y1各工艺环节分属于不同的PLC分布式I/O从站,再通过高性能的以太网通讯将控制信号上传到PLC主站和上位机,然后根据ABS塑料制件的形状规格、牌号和用途,设置各控制位的工艺参数,再由PLC主站执行,实现ABS塑料电镀生产线的自动化控制。
主、从站S7-1200PLC控制系统结构如图3所示,PLC以CP-U1214C为核心开发,利用集成的Profinet工业以太网接口实现Profibus、RS232/RS485等通讯服务,兼容电镀生产线超声波清洗、工位槽温度控制、行车、铬雾通风回收、电镀(半光镍、全光镍和镀铬)电源等机电设备的在线监控接口。主站S7-1200PLC板载14/10点数字量输入/输出、2点模拟量输入,本地扩展16/16点SM1223数字量输入/ 输出,用于本地操作台上电、急停、复位、自动/手动控制、S1~S20各控制位调试按钮等数字信号输入,故障和运行状态指示灯等数字信号输出。
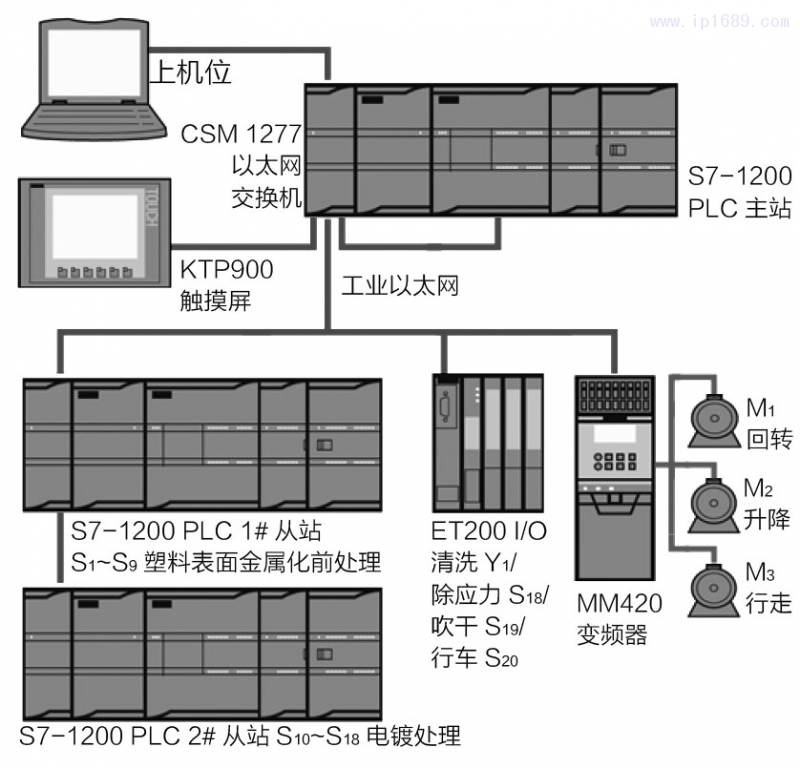
图3 控制系统总体结构
主站S7-1200PLC通过2台以太网交换机CSM1277与上位机、KTP900触摸屏、S7-1200PLC#1和#2从站、分布式I/O单元ET-200SP、行车控制变频器MM420等设备建立工业控制网络,接受上位机或触摸屏对各控制位电镀工艺参数的在线设置,通过主站S7-1200PLC调度从站PLC、分布式I/O和变频器等机电设备,从而满足不同ABS塑料制件的电镀生产和工艺条件需求。
2.2 工位槽控制系统设计
与其他设备相比,工位槽直接面向不同的电镀过程,对其控制系统设计更能体现S7-1200PLC的通用性、模块化和可移植扩展能力。对于图1所示的ABS塑料电镀生产线,各工位槽控制参数主要包括:①控制台S1~S20调试开关SB,工位槽和储液槽液位上限H、下限L位置开关SQ等数字量输入。②加液、过滤和水洗喷淋等泵组继电器KM,超声波、通风机、温度和电源控制等设备继电器KM,正常运行和异常报警指示灯HL等数字量输出。③电镀液温度和pH,焦铜、光亮镍和镀铬等过程电压和电流,加液泵流量等模拟量输入。
以焦铜S10工位槽为例,PLC硬件系统的接线原理如图4所示。分别在#2从站S7-1200PLC基础上扩展1块SM1222数字量输出和SM1231模拟量输入模块,实时监测焦铜S10工位槽的数字(开关SB和液位SQ 等)和模拟(温度、pH、电镀电源等IWI)信号,由#2从站按工艺条件在线处理监测信号,自动控制设备或泵组继电器KM、指示灯HL等状态。
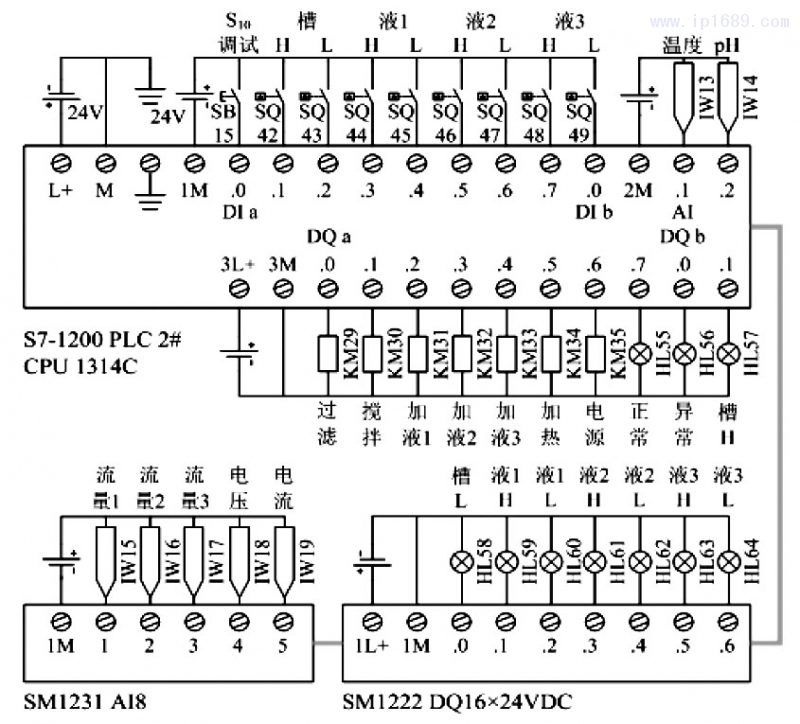
图4 PLC端子接线(焦铜S10工位槽)
2.3 行车控制系统设计
为避免挂具或工件掉落,在各工位槽间高效、平稳转移ABS塑料制件,电镀行车M1回转、M2升降和M3横移行走采用一台MM420变频器进行控制,如图5所示。
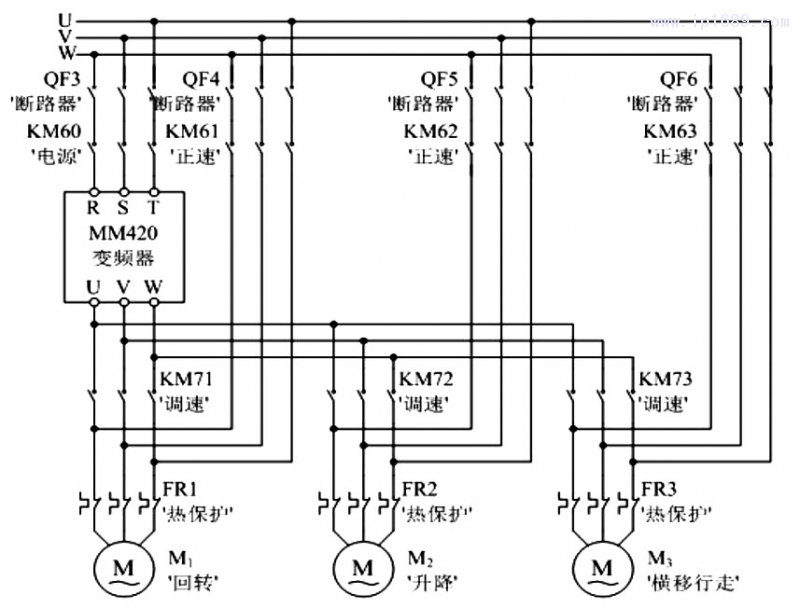
图5 电镀行车控制电路
当行车上挂后,本地操作台或操作面板选择自动运行 ,MM420变频器和调速继电器组KM71~KM73控制行车动作,根据限位开关的位置输入,利用开环直接控制ABS塑料制件在工位槽的位置和停靠时间。同时,#1、#2 从站也对槽内有无工件进行检测,利用闭环反馈间接验证行车位置和ABS塑料制件停靠时间是否满足工艺条件和生产流程的参数设定。当选择手动运行,按工艺条件和生产流程控制正速继电器组KM61~KM63,分别实现行车的M1回转、M2升降和M3横移行走控制。
3 软件设计
3.1 上位机操作面板
由于S7-1200PLC主、从站系统采用工业以太网通信,而超声波清洗、铬雾通风回收和电镀电源等设备采用串口通信(RS232/RS485),为了能在同一控制平台上实现ABS塑料电镀生产线的集中监控和高效管理,缩短开发周期、降低设计成本,电镀线操作面板和自动化控制软件分别在博途TIA Portal集成平台上利用WinCC和STEP7编程软件开发。
对于上位机操作面板,一方面需要提供直观、准确和实时的电镀工艺参数与故障信息,另一方面具有良好的可操作性,方便工艺人员在线设置工艺参数和高效管理电镀生产流程。考虑ABS塑料电镀生产的实际需求,上位机操作面板如图6所示,操作菜单包含主界面、电镀工艺进程、I/O状态、数据记录、报警记录、工艺选择和系统设置等选项。
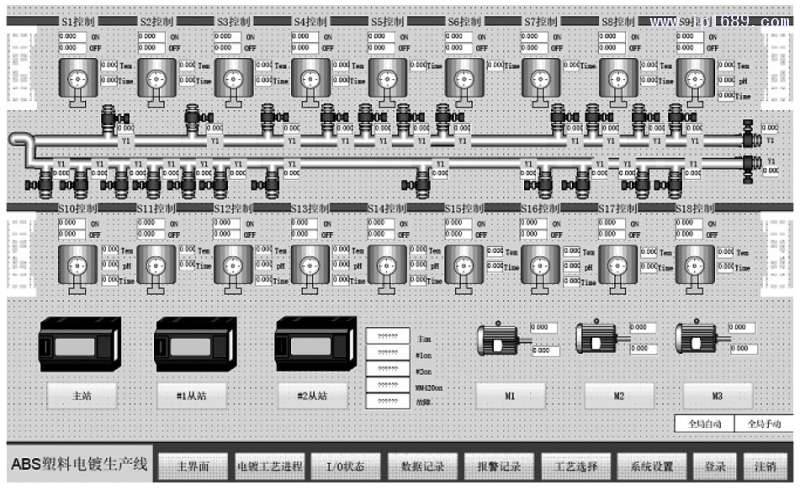
图6 上位机操作面板
主界面可通过WinCC直接创建,利用内部多种功能控件和定义的关联变量提供现场电镀设备直观的电镀工艺流程和控制位信息,实时显示各工位槽、行车和控制阀组等设备的状态参数。电镀工艺进程用于在线记录S7-1200PLC主、从站设备的I/O状态,实时监视生产数据和系统故障,为定量和定性分析工艺条件和生产流程对电镀质量的影响提供数据支持。工艺选择可用于在线设置和存储不同形状规格、牌号和用途的ABS塑料制件电镀参数,并允许工艺人员选用已存储的工艺数据,从而避免遗漏或误设置电镀参数。系统设置主要实现对电镀生产数据的后续管理与应用,支持生产数据的在线查询、编辑、导出和打印等。
3.2 电镀线自动控制软件
ABS塑料电镀线S1~S20、Y1等控制位具有典型的时间序列特性,所需的梯形图程序由STEP7开发,在主程序OB1中循环调用各控制位子程序,由中断负责子程序的调用时序,以满足不同形状规格、牌号和用途的ABS塑料制件电镀所需的工艺流程,如图7所示。
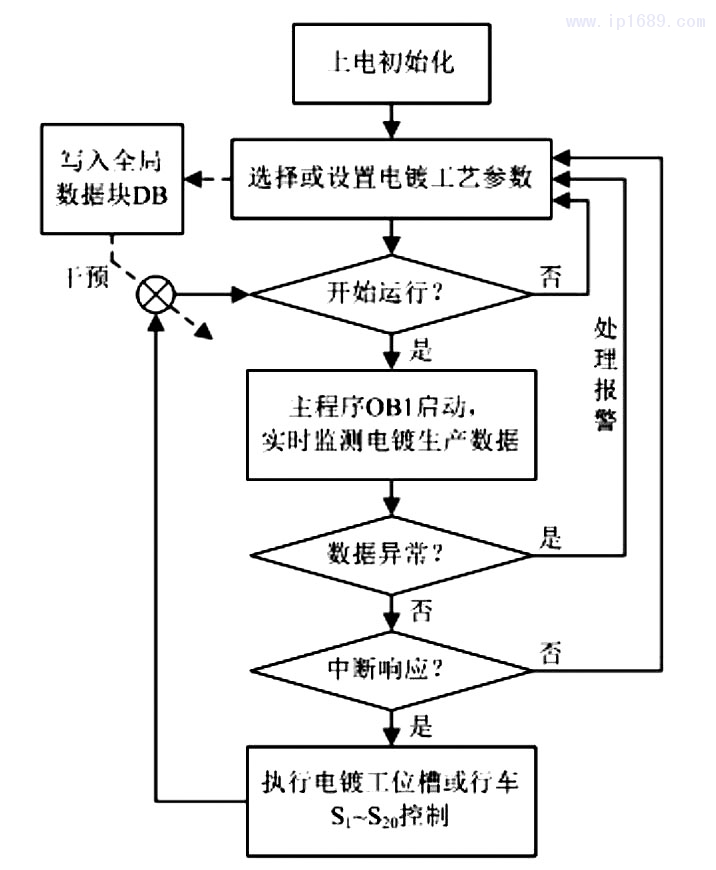
图7 ABS塑料电镀线自动控制流程
系统上电后,工艺人员通过上位机(或触摸屏)操作面板设置或选择电镀工艺参数。由于WinCC在开发操作面板时已经将电镀线控制软件的内部变量与操作面板变量相关联,设置或选择的工艺参数将自动写入梯形图程序的全局数据块DB1。选择运行后,主程序OB1启动将调用电镀线S1~S20、Y1等控制位子程序,实时采样、显示和处理电镀线生产数据。为确保OB1内对子程序的调用满足不同工艺条件和电镀流程需求,根据设置的电镀时间等参数,中断程序按工艺流程循环控制子程序的调用顺序,在线响应DB1数据块中设置的工艺参数。
同样,图8给出了焦铜S10工位槽的梯形图程序:通过上位机操作面板设定焦铜S10控制位的时间PV为120s,输出的变频器MM420控制数据存储到DB1.DBW110中 ,若程序扫描电参数等于DB1.DBW110,则行车M2电机动作,提升工件进入下一电镀过程。
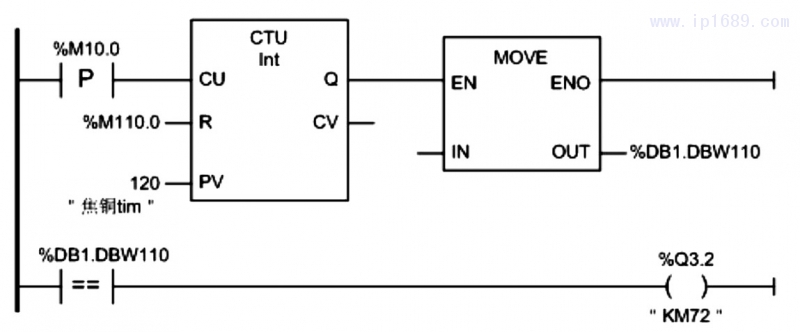
图8 梯形图程序(焦铜S10工位槽)
4 结语
在博途TIA Portal和S7-1200PLC控制平台基础上搭建适于不同形状规格、牌号和用途的ABS塑料制件电镀生产的全自动控制系统。与传统的PLC系统不同,所开发电镀控制系统具有良好的通用性、模块化、可移植扩展能力,兼容不同通信端口的电镀设备,并支持在统一的编程平台TIA Portal上灵活设计电镀生产需要的工艺流程和应用功能。由于工位槽、行车和控制阀组等设备可由电镀企业自行配置,整套系统的投入主要集中在PLC系统硬件、上位机操作面板和自动控制程序等部分,与非标定制相比,系统交付周期短(≤ 2月)、投入成本最大可节省70%。此外,对部分工位槽和上位机操作面板的调试表明,所开发控制系统运行稳定、故障率低,能根据工艺设定实现电镀生产流程和工艺条件的在线监控与高效管理。
参考文献
[1]李秀忠.基于S7-300PLC和ET200S的电镀生产线自动控制系统设计[J].制造业自动化,2015,37(7):134-138.
[2]杨文刚电镀生产工艺参数的可编程逻辑控制系统设计[J].电镀与精饰2017,39(2):30-34.
[3]徐竟天,张甜甜,程瑞洲,等.基于S7-300PLC 的电镀恒温控制系统设计[J].电镀与涂饰,2015,34(12):690-695.
[4] 李宁,卢子广,罗启平.镀铬槽液温度自动控制系统研究[J]电镀与精饰,2017,39(8):25-28.
[5] 郭伟荣,曾鑫.ABS 塑料电镀自动线生产工艺[C]// 2014 (重庆)国际表面工程论坛暨第十二届全国表面工程·电镀与精饰年会论文集.重庆,2014:337-343.
[6]刘海涛.ABS 全自动塑料电镀生产线三维设计及关键结构优化研究[D].无锡:江南大学,2009.