经过长达七年的精心筹备与建设,国家重大工程——深中通道于6月30日正式启动通车试运营。此次通车标志着从深圳至中山的行程时间将大幅缩减,由原先的两小时缩短至仅需三十分钟,极大地提升了区域交通的便捷性与效率。
据悉,深中通道集“桥、岛、隧、水下互通”为一体,其中隧道部分长6.8公里,最深处达水下39米,是目前全世界最宽最长的钢壳沉管隧道,隧道体需要承受巨大的海水压力。作为沉管结构最为重要的“钢铁外衣”,每节钢壳长165米,宽46米,高10.6米,全部焊缝长度加起来达到38万米,断面相当于1.2个篮球场。如何精准高效地制造这样一个个庞然大物呢?新松工业机器人在其中扮演着关键角色!
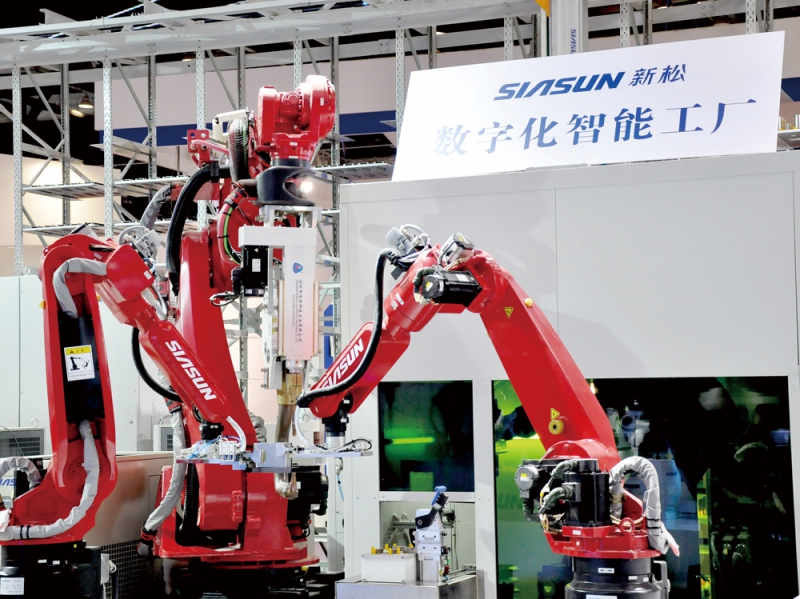
机器人可自适应和规划不同工件的焊接需求
在钢壳智能制造车间,少数工程师与红色新松工业机器人协同工作。这些机器人使用新松焊接系统,模拟人类焊接手法,自主完成复杂焊接任务。由于焊接对象体积大、重量高、结构复杂,机器人的智能分析与轨迹修正能力尤为重要。此外,由于焊板较厚,需多层多道焊接,工艺复杂度较高。
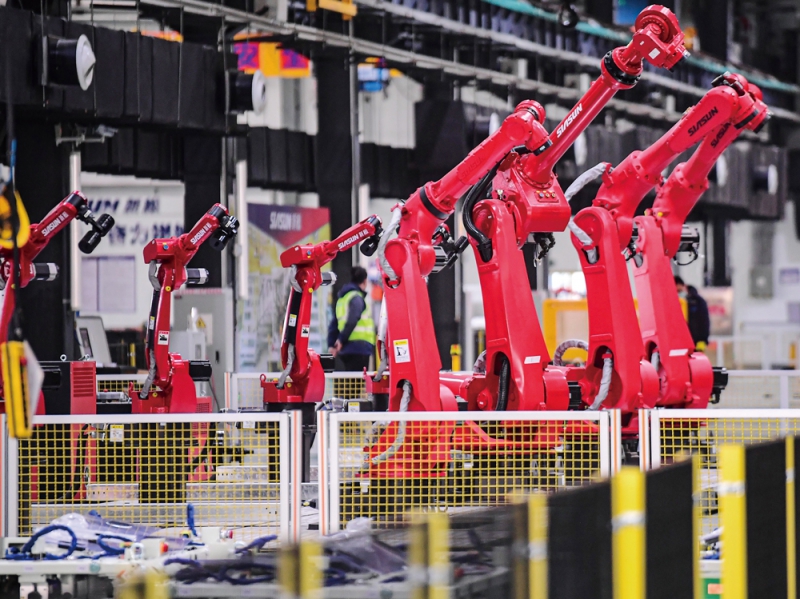
作为国内最早攻克工业机器人中厚板焊接技术的企业,新松采用柔性制造的设计理念,创新性的将3D视觉、点激光寻位、激光焊缝跟踪、机器人在线控制、机器人智能焊接等先进技术融入到机器人焊接工作站中,机器人可自适应和规划不同工件的焊接需求,自动调整焊接姿态,极大程度地减轻了传统工业机器人对于编程示教的依赖,有效解决了钢壳焊接过程中工件种类多,作业流程频繁更换等难题,相关技术已经达到了国际领先水平,实现了国家重大工程由国产机器人来造的愿景!
从深度参与国家重大工程,到实现国产机器人汽车点焊高端应用突破,再到央视龙年春晚的完美演出……近年来,新松工业机器人以其高精度、高效率、高可靠性、高耐久性、高智能性等诸多优势广受青睐。
未来,新松工业机器人还将全面推进在搬运码垛、磨抛、装配、喷涂等工艺环节以及汽车及零部件、新能源、3C电子等领域的应用,推动各行业高端化、智能化、绿色化升级,为国家培育发展新质生产力,推进新型工业化添薪助力!