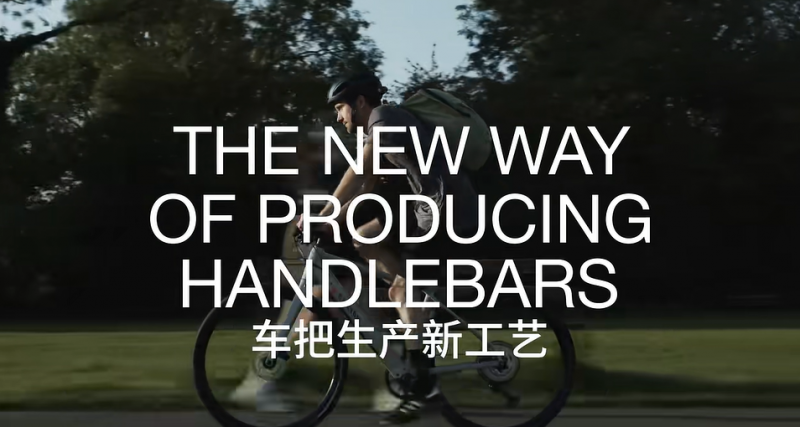
一体式车把新标准
传统铝制产品虽满足性能要求,但存在自重较大且制造工序复杂的局限性。通过与CANYON、Artefakt Design、DOMO Chemicals、Plastic Innovation及Simoldes的合作,我们成功研发出全塑集成车把,在设计理念、功能实现和生产工艺方面均实现创新突破。该中空结构的高性能组件在保持优异抗扭刚度和弯曲强度的同时,实现了轻量化设计,生产周期约为一分钟。通过流体熔融技术与碳纤维带材定向增强工艺的协同应用,使车把兼具轻量、坚固与功能性。
ENGEL fluidmelt技术
与碳纤维带材创新工艺组合
ENGEL在此创新项目中发挥核心作用,重点参与工艺开发与系统集成工作,涵盖从fluidmelt注塑成型到无拉杆式victory 1560/180注塑机及自动化方案的实施。该工艺通过模内注入水或氮气的技术原理,将熔融芯层转移至溢流腔或塑化单元,形成中空塑料构件。该技术可实现约25%材料的循环利用,显著降低部件重量。通过连续纤维增强技术进一步提升机械性能:基体采用玻璃纤维增强PA6材料保证结构刚度,同时在成型过程中植入四组单向碳纤维带材,针对关键承力区域进行定向增强。这种复合结构设计方案,使薄壁中空构件在高负荷条件下仍保持优异的结构稳定性。
新型车把的生产流程采用全自动化设计。冷却阶段完成后,中空结构组件可直接脱模使用,无需任何后处理工序。
相较于传统铝制工艺,该制造方案不仅显著提升量产效率,更在可持续性方面取得重要进展,通过精简生产步骤与减少加工能耗,实现资源利用率优化。
新设计与可持续性能结合
注塑成型工艺赋予的结构设计自由度,使多功能集成成为可能。电缆可以穿过车把内部的中空结构,照明单元亦可直接嵌入组件本体。由此打造出兼具轻量化、高性能与美学完整性的功能化部件。该方案在可持续性方面具有显著优势:基于材料重量差异与生产排放数据,热塑性工程塑料方案较传统铝材可降低约70%的碳足迹。组件本身具备耐久性特征,在闭环回收体系支持下可实现材料再生利用。全自动生产工艺使欧洲本土化生产具备可行性,通过就近供应模式有效降低运输环节的碳排放。
该项目已进入工程验证阶段,首批原型件于2024年10月完成试制,当前正在进行性能测试。
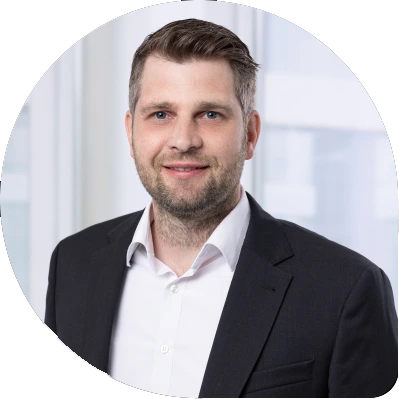
Christian Wolfsberger
汽车事业部业务发展经理
通过验证后,该部件将率先应用于CANYON品牌自行车产品体系。根据开发计划,量产产品预计于2025年秋季面市。此项生产工艺展现出显著的应用潜力,除车把部件外,研发团队已确认可将该技术延伸至其他自行车部件的制造领域,特别是当前由多零件组装的框架结构系统。