分厂承接家用空调、商用空调、大松生活电器、晶弘冰箱、厨房三件套、手机、洗衣机等所有基地批量投产前试制工作及总部注塑件配套工作,对接公司注塑领域新产品、新材料、新工艺的开发和试制工作。
2012年,分厂全面推进自动化的创新改善工作,从生产排产自动化、厂房布局规划、设备模具自动化、现场自动化、物流自动化方面进行了大规模整改。
工作开展之初,分厂必须明确现存的问题及未来注塑自动化开展方向。譬如,面对消费者更多的个性化要求,面对市场多款式、小批量的供给需求,分厂如何快速反应?面对日益严峻的劳动力短缺,分厂能否实现车间的少人化,甚至无人化?一系列考量之后,分厂将自身定位为高自动化,集注塑生产、二次加工、零部件装配于一体的配套加工产业链式的加工工厂,从劳动密集型企业向技术密集型企业转型。
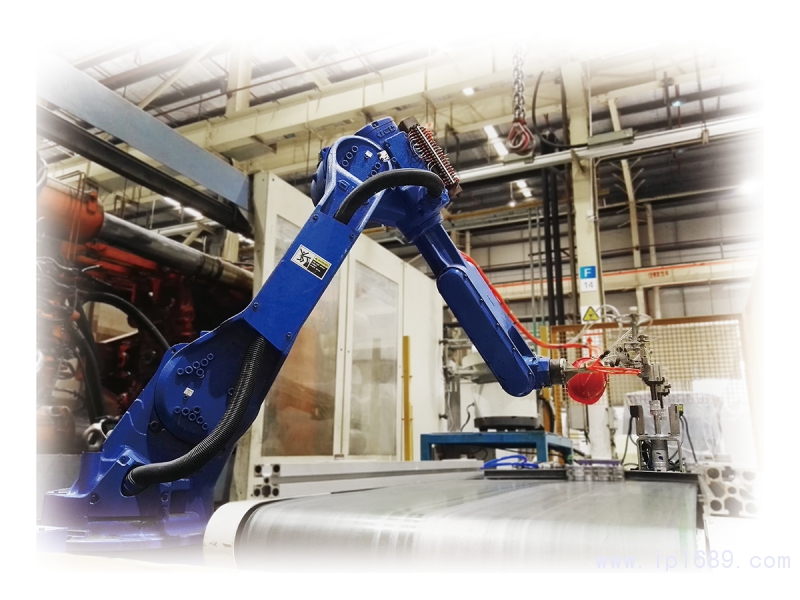
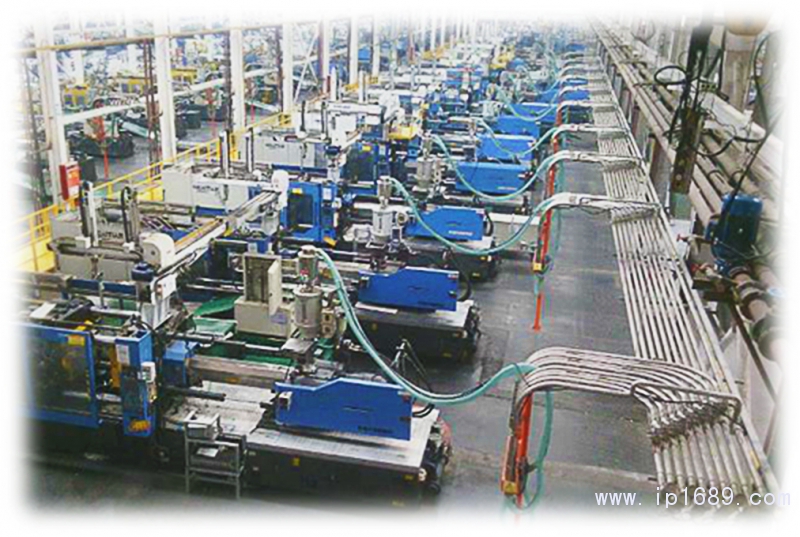
格力车间局部
2012-2017年间,分厂注塑从设备自动化、物流自动化、全流程信息化三个方面开展,取得了一定的成绩。以注塑工序、岗位为例进行分析,材料供应自动化、模具切换自动化、二次加工自动化、检测自动化、包装自动化、取件自动化、预装自动化、物流自动化提高了注塑工序自动化率,工作人员从1400多人下降到800多人,注塑工序自动化率从45%提升到65%。
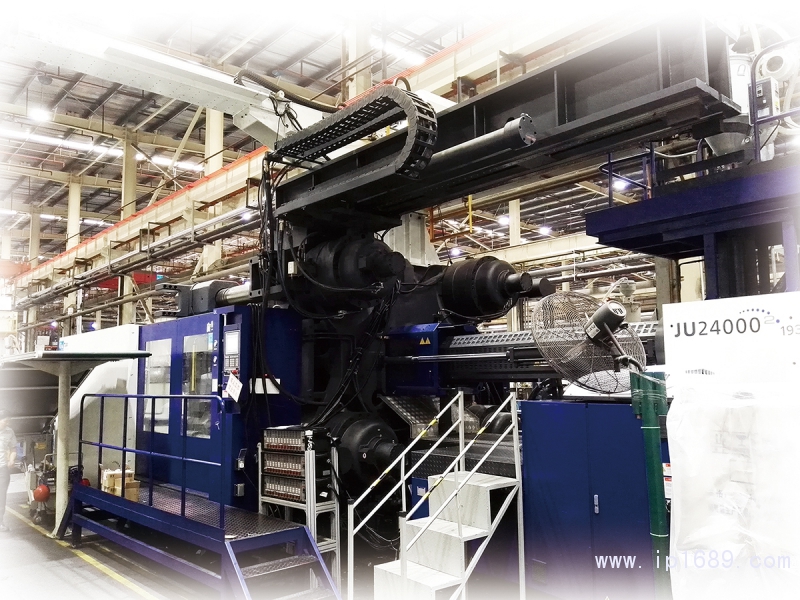
格力生产设备
分厂负责人认为,未来注塑工厂的总体布局要注重工厂硬件及技术细节方案设计,在对自动化设备等“硬件” 投入的同时也要加强基础工程、体系、人才队伍等“软件”的建设;要重点解决影响自动化生产源头问题(生产排产、模具、标准化、包装物流);要加快信息化建设,完成生产、物料、人员、设备等各方面数据采集及监控,为员工创造舒适的工作环境。