近日,在南沙模塑高峰论坛主办方的组织下,《塑胶工业》记者一行荣幸参观了广汽丰田汽车有限公司(本文简称“广汽丰田”)的总装车间。
据了解,广汽丰田成立于2004年9月1日,是由广州汽车集团股份有限公司和丰田汽车公司按50:50的股比共同投资建设和经营的企业,合资年限30年,注册资本84223万美元。公司位于广州南沙区,占地面积282万平方米,建筑面积74万平方米,目前共有10029名员工,生产车型包括CAMRY凯美瑞(含凯美瑞双擎)、HIGHLANDER汉兰达、YARiS L致炫、LEVIN雷凌(含雷凌双擎)、YARiS L致享系列轿车,现有三条生产线,整体产能达到每年50万台。其中,第一、第二生产线产能到达每年40万台,第三生产线初期产能达到每年10万台,未来可根据市场需求快速扩充至每年20万台,届时广汽丰田总产能可突破每年60万台。
广汽丰田自2004年成立以来,一直致力于社会贡献和公益活动的开展,工厂参观服务即为其中的一项重要内容。据悉,记者一行本次参观的总装车间,为汽车制造五大工艺 ( 冲压、焊装、涂装、成型、总装 ) 的最后一大工艺,主要负责零部件的装配。总装车间采用精细的零件分拣系统(SPS方式),把零件区及装配区分离,使生产线简洁化。同时导入先进的“安东系统”,实现“自动化”生产。
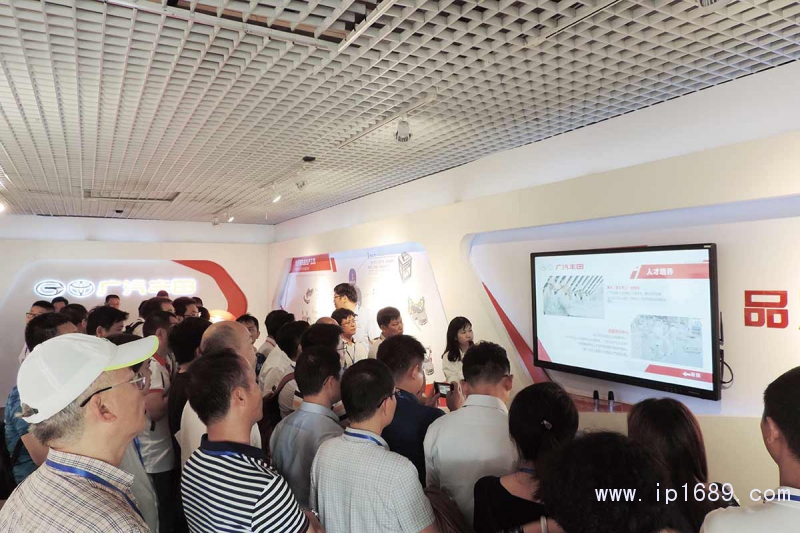
广汽丰田文化展览室
在广汽丰田工作人员的陪同下,记者一行从广汽丰田的文化展览室列队走进了总装车间。五十人的队列从逼仄的文化展览室内走出,来到一条约为两层楼高的室内参观桥上:抬头见到的不再是展览室低矮平淡的室内房顶,而是密密麻麻却排列得井然有序的钢架;四周也不再是展览室拥挤的四壁,而是开阔堪比足球场的生产车间。待完成的各式汽车正在机器托盘的运动下轮番前进、停留,再进入下一道工序;形形色色的机器人在转动、伸展、收缩、抬高、放低,自行负责着相应的工序;而身着统一制服的工人们都在各自的岗位上劳作,或站立加工,或弯身装配,或蹲伏检测,或驾驶运送……整个车间充满动感,这里的所有运动似乎都在传达着两条无形的信息:科技、效率。
据陪同参观的工作人员现场介绍,广汽丰田的总装车间有为数不少的特色。
其一是辅助运输装置的使用,这是为了降低工人的工作强度。工作人员表示,在零件安装过程中采用辅助运输装置,可协助搬运和防止重物掉落伤人,这就是尊重人的表现,让员工在安全的环境里轻松地作业;同时,也降低了员工的体能负荷,消除了疲劳作业带来的潜在品质不良可能。
其二是安东系统的采用,这是为了使品质问题可视化。工作人员谈道,位于我们上方的屏幕就是安东系统的显示屏,安东系统是一套监控系统,它对生产过程实施监控,生产过程出现的所有异常均会反馈到系统,以声响及图象的形式发出警报,使问题100%暴露,如车辆在到达下一工位前问题仍未得到解决,生产线就会停止。安东系统既有让员工直接手动报警的机制,即安东拉绳,一拉它系统就会报警并同时在屏幕上显示图像和工位,此外,也有通过监控设备自动报警的机制。
其三是防错装置的使用,这是为了降低错误率。据工作人员介绍,总装车间的零部件安装以人工作业为主,为避免人为偶然错漏所造成的拧紧不良,工厂也引入了“自动防错系统”,出错时设备会自动停止。举例来说:安东系统的自动报警指示灯有三种颜色的灯柱,当开始作业时,蓝灯点亮。只有在作业者将螺栓全部拧紧,绿灯才能点亮,该工位才能被通过。否则,安东系统就会自动报警,红灯将点亮,生产线停止,直至班长将问题解决,生产线才能再次开动。这样有效防止了漏拧紧的现象,是总装工序品质保证的重要一环。
等队列行进到总装车间的最后一道关卡——检测线,就意味着参观活动的行将结束。在检测线车间里,记者见证了一辆辆高质成品汽车的出产远远没有想象中的轻松——在交付给消费者之前,血统优异的汽车还要面临繁琐的检查,检查内容包括车辆灯光、四轮定位调整、车辆装箱角度检查和前大灯水平调整、转毂测试以及制动测试、尾气、淋雨房以及小型试车跑道试跑。据工作人员介绍,所有车辆在完成了全部零件的安装后都要经过这里,检查人员会对车辆进行目视、手测等认真仔细的检查。在这条检查线上会进行700多个项目的检查,全部检查合格的车辆就可以在厂房末端一侧的小型试车跑道上进行试跑检测,至此如果没有发生任何问题,车辆就会被确认为合格并由电脑自动打印合格证,然后才可出厂。
参观结束后,坐在返程大巴上的记者反复咀嚼着在广汽丰田工厂现场的视听感受——那是一种滋味复杂的震颤,里面交织着对人类技术的惊叹和某种对人类技术的微妙恐惧。此前仅仅在书本和电视中见识过工厂为何物的记者,愿把这次参观视为另外一种旅行,因为相较于大自然景观的鬼斧神工,记者在广汽丰田工厂的实地见闻真切地让记者领悟了另外一个成语,一个形容人类的成语——巧夺天工。